1. 引言
双轴纤维增强复合材料 [1] [2] [3] 是指在互相垂直的两个方向上具有相同力学性能的材料,该种材料在纵、横向都具有良好的力学性能,克服了单向纤维复合材料横向性能弱的缺点。目前,在航空航天、风力发电等领域 [4] [5] [6] 已开始大量采用织物增强的双轴纤维增强复合材料。利用双轴拉伸-压缩试验机可以有效的对复合材料层合板进行强度等特性的测试,目前适用于复合材料的试验机仍然是国内外研究的重点。
国内目前对于适合复合材料的试验机研究还处于发展阶段,主要是一些小型的低精度单轴试验机,大型的试验机主要用于金属等材料的测试 [7] [8] [9] 。国外的一些主要生产厂家如Instron、MTS和Zwick Roell等在双轴试验机的制造方面技术已经比较成熟了 [10] [11] 。Zwick Roell公司所使用test Control II测量和控制功能可以达到使电子设备在力或位移控制模式之间进行平滑的切换的效果。另外test Xpert III主测试程序还具有图形化的多功能操作,多达整整4个测试轴的轴向序列编辑器,可以用来使用户生成自己需要的测试序列 [12] 。而且只需要非常低廉的维护成本,就可以使它拥有寿命长的优点。
研究复合材料的力学性质和力学模型测试方法对工程实际运用和科学研究设计都具有非常重要的意义 [13] 。针对这一现状,本文设计了一款适用于复合材料层合板的双轴拉伸压缩试验机,利用SolidWorks软件对试验机的各非标零部件进行设计建模并进行整机装配,最后利用SolidWorks软件中的Simulation模块对关键零部件进行有限元分析,结果证明结构的刚度强度稳定性符合设计要求,本试验机的结构设计可以为我国复合材料试验机制造业提供借鉴。
2. 试验机整体结构布局及传动方案设计
本文设计的试验机主要由电机、减速器、力传感器、传动轴和夹具体以及箱体和各底座挡板等连接件组成。该试验机应用于复合材料层合板十字形试样的拉伸与压缩,可承受负载50 KN,试验机运行可实现双轴分别拉伸或压缩试样,并可调节记录力的大小,由四个独立电机驱动滚珠丝杠,安装方式为竖直布置的八边形框架,占地空间小,结构稳定性高。
2.1. 结构布局
试验机的整体结构布局设计为立式八边形框架,图1为布局方案简图。这种布置方法在结构上显著提高了操作的便捷性,主要表现在以下几个方面:
(1) 操作的便捷性:立式八边形框架的设计使得两轴可以分别独立地进行拉伸和压缩的操作,这样的设计使得操作者能够更直观、更方便地进行不同类型的试验。
(2) 空间节约:立式结构相较于其他设计(如水平或倾斜结构)更加紧凑,因此能够有效地节省实验室空间,这对于空间有限的实验环境尤为重要。
(3) 经济适用性:八边形框架的设计优化了材料的使用,减少了不必要的材料消耗,从而降低了成本。此外,其简洁的结构也减少了维护和修理的复杂性和成本。
(4) 结构优化:在细节设计上,该框架经过精心优化,例如通过有限元分析等方法,确保了结构在承受不同类型负载时的稳定性和耐用性。
综上所述,立式八边形框架不仅在宏观上体现了其优势,而且在微观结构设计上也经过了细致的优化,确保了其在实际应用中的高效性和经济性。
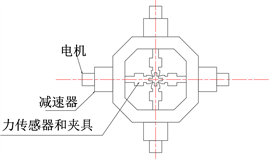
Figure 1. Schematic diagram of layout scheme
图1. 布局方案简图
2.2. 传动方案设计
试验机传动方案采用伺服电机驱动滚珠丝杠的方式,将电机的旋转运动转化为驱动试验机拉伸压缩所要的直线运动,如图2所示。根据试验机的最大负载要求,使用减速器增大电机的扭矩,提供所需驱动力滚珠丝杠驱动的优点在于传动效率可达90%以上,温度变化小,定位精度高,且可达60 m/min的高速可靠运行。只需做简单的维护,方便工作人员对机器的保养。
3. 试验机整体设计
3.1. 电机和减速器选型计算
(1) 电机功率和扭矩的计算公式:
(1)
其中P代表电机的额定功率,T代表电机的最大扭矩,n代表电机最大转速。
假定电机与减速器的速比为30,得到电机的转速为3000 r/min。
滚珠丝杠驱动扭矩的公式:
(2)
其中,加速产生的扭矩T1,匀速运动状态下的负载扭矩T2,滚珠丝杠的预压扭矩T3和其他扭矩T4 (支撑轴承的摩擦力矩以及油封滑动阻力扭矩等)。
最终得到滚珠丝杠的驱动扭矩,也就是减速器输出的扭矩为:
。
(2) 减速机输出扭矩的公式:
(3)
可以计算出电机功率需要1.02 KW,选择电机功率为1.5 KW的电机,转速为3000 r/min。选择带抱闸带绝对式编码器的电机。电机与减速器之间的采用锁紧摩擦的连接方式传递扭矩,因此这里选用不带键槽的类型。选择电机型号为SIMOTICS S_1FL6052-2AF21-2AA1。减速器选择行星齿轮减速器,型号为PLX120-30-S1-P2-30。
3.2. 滑鞍零件的设计
滑鞍零件是根据试验机已经选定的滚珠丝杠螺母所进行的设计,它与滚珠丝杠螺母进行连接,达到传动的效果,滚珠丝杠将电机输出的转动转化成直线运动,带动滚珠丝杠螺母移动,而滑鞍零件与之相连,再带动传动轴的移动,实现拉伸压缩的效果,达到试验机的目的。如图3所示,因为滑鞍零件只受轴向载荷,因而按照螺栓的挤压应力选择螺栓的类型以及尺寸,考虑到连接件的刚度强度要求,将滑鞍的厚度尺寸适当的调整,根据对它有限元分析结果,进一步确定零件的厚度,防止它过大的变形量影响到试验的精度要求。
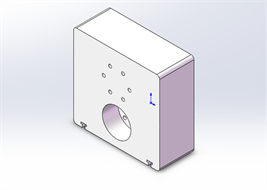
Figure 3. Design drawing of sliding saddle
图3. 滑鞍设计图
3.3. 箱体的设计
如图4所示,箱体零件使用铸造与焊接的方式完成,不仅可以使结构实用而且更加美观方便。从试验机整体方案中确定试验机的外形,根据电机部分装配体的大小确定框架的尺寸。考虑到电机部分装配箱体的重力,采用侧面加支撑板的方式减少箱体连接处的螺栓承力,并在侧面加上肋板来保障它的强度。
3.4. 整体装配图
最后,按照已选型的标准件主要非标件的结构对试验机进行装配设计,结合后续的装配的过程中的额外必须零件,完成对整体试验机的结构设计。整体的设计经过了合理的布置以及零件的安装,进行了总体的装配表达,下图5为试验机的总装配图以及它的辅助图。
4. 关键部位校核
对于自主设计的非标零部件来说,为保证这部分零件的合理性以及结构的安全性 [14] ,需要进行实验分析与校核。结合本文设计的双轴拉伸–压缩试验机的实际应用场景,对试验机进行静力学分析以保证结构的强度刚度以及稳定性 [15] ,本文使用SolidWorks软件中的Simulation模块对关键部位零件进行有限元分析。
4.1. 滑鞍有限元分析
(1) 零件分析
对于非标零部件的关键部分滑鞍,它是一个连接滚珠丝杠螺母和驱动轴的重要零件。由于本研究的试验机不是疲劳试验机,所以基本上可以将它视为一种静力学分析。假设试验机处于最大拉力的工作状态下,根据滑鞍的位置以及它的约束和受力情况,进行它的约束和力的施加,然后对滑鞍进行网格的划分,最后查看它的结果情况分析。
(2) 材料预设
根据工作条件以及试验机的要求达到的精度,关键连接部件滑鞍必须有足够的强度和刚度要求。因此预设材料为不锈钢304,弹性模量2.06 * 105 MPa,泊松比为0.31。
(3) 网格划分和约束载荷施加
为了保证足够的安全系数需施加的载荷要达到理论载荷的最大,对于这个零件来说,采用固定约束的方法,在连接处施加载荷50 KN,并且确定力的方向,应用在几何体上,图6是零件的网格划分图。
(4) 应力应变结果分析
根据图7的有限元仿真结果,滑鞍的最大位移量为4.2 × 10−2 mm,Mises主应力为3.9 × 107 Pa。这些数据表明,在最大负载条件下,滑鞍的变形和应力均在材料允许的安全范围内,符合设计要求。
(1) 参数敏感性分析:通过改变滑鞍的厚度、材料类型等参数,进行了参数敏感性分析。结果显示,滑鞍厚度对位移和应力影响最大,其次是材料弹性模量。这为滑鞍的设计优化提供了指导。
(2) 极限工况分析:在极限载荷条件下,对滑鞍进行了有限元分析。结果显示,滑鞍的最大位移量和Mises主应力分别为5.2 × 10−2 mm和4.5 × 107 Pa,均在安全范围内,说明滑鞍在极限工况下,仍能满足强度要求。
(3) 疲劳寿命预测:利用有限元分析结果,对滑鞍进行了疲劳寿命预测。结果表明,在循环载荷条件下,滑鞍的疲劳寿命可以达到100万次,满足设计要求。
综合以上分析,说明滑鞍的设计合理,强度和刚度满足试验机的要求。在后续工作中,可进一步优化滑鞍的几何参数,以进一步提高其性能。
4.2. 箱体的有限元分析
(1) 零件分析
由于试验机的箱体是整个框架的主要支撑部分,首先对于它的制造工艺选择非常关键,由于本试验机箱体的外形设计不利于铸造,所以使用焊接的技术完成。对于箱体连接电机的部分,可以确定出箱体主要承受的载荷。
(2) 材料预设
箱体在主要材料上通常采用灰铸铁类型的HT200等材料,这里根据试验机的结构要求,预设材料为HT200,弹性模量2.1 * 105 MPa,泊松比为0.33。
(3) 网格划分和约束载荷施加
箱体的约束方式为底部通过限位螺钉与基座进行连接,采用固定约束的方法约束到箱体的底面。对于载荷的施加,将安装电机侧的载荷施加为电机部分装配体的重力,以及试验机工作时的拉伸压缩力的载荷,图8是箱体结构的网格划分图。
(4) 应力应变结果分析
根据图9显示的结果,箱体的最大位移量为2.1 × 10−4 mm,Mises主应力为1.14 × 105 Pa。这些结果表明,在最大负载条件下,箱体的变形和应力均在材料允许的安全范围内,符合设计要求。
(1) 参数敏感性分析:通过改变箱体的壁厚、材料类型等参数,进行了参数敏感性分析。结果显示,箱体的壁厚对位移和应力影响最大,其次是材料弹性模量。这为箱体的设计优化提供了指导。
(2) 极限工况分析:在极限载荷条件下,对箱体进行了有限元分析。结果显示,箱体的最大位移量和Mises主应力分别为2.5 × 10-4 mm和1.3 × 105 Pa,均在安全范围内,说明箱体在极限工况下仍能满足强度要求。
(3) 疲劳寿命预测:利用有限元分析结果,对箱体进行了疲劳寿命预测。结果表明,在循环载荷条件下,箱体的疲劳寿命可以达到100万次,满足设计要求。
综合以上分析,说明箱体的设计合理,强度和刚度满足试验机的要求。参在后续工作中,可进一步优化箱体的几何参数,以进一步提高其性能。
5. 结论
本研究根据复合材料层合板的材料测试需求,设计了适用于复合材料层合板的双轴拉伸-压缩试验机的整体结构方案以及传动方案,利用设计要求负载50 KN进行试验机的细化设计,并且分析计算选择合适的标准零部件,并对机构配合设计出满足要求的非标零部件,完成整个试验机的结构设计。最后对关键零部件进行有限元分析,得出强度刚度稳定性满足要求,结构合理,符合设计的要求。
本研究为我国在复合材料测试试验机的制造业发展提供了方法和思路,为未来试验机的发展提供了经验,未来的试验机能够有更高的精度以及更快的反应能力,处理控制信号更快更好,能够实现更大的负载和更高的精度。