1. 引言
蒸发式冷却器是结合了空冷式和水冷式优点的高效换热设备。在蒸发式冷却器里,冷却液被喷射到换热管的外部,生成一层薄薄的液膜,随后受风机推动,空气和这层薄薄的液膜直接相互作用,实现对流传热和物质转移。空气未饱和时具有吸湿性,当其进入蒸发式冷却器时,由于空气与管外喷淋水间的焓差,喷淋水会吸热蒸发成水蒸气,然后以此形式进入空气中,利用空气的干度制冷,是融合了工质显热和潜热的热量传递过程 [1] [2] 。鉴于其结构紧凑、维护方便、节能环保的特性,在石化、电力、冶炼和制冷领域的应用前景十分广泛 [3] [4] 。
蒸发式冷却器中流动与传热传质过程复杂,且受喷淋水量、进风空气量、环境干湿球温度、被冷却介质温度和流量等多种因素影响。郭亚丽等 [5] 建立了三维数值模型,对横管外两液柱间的液膜铺展及换热过程进行模拟,得到了喷淋密度对局部传热系数分布的影响。蒲亮等 [6] 利用CFD软件与UDF程序,对水平管降膜蒸发的热质传递过程进行数值分析,得出在一定范围内,雷诺数或饱和温度的增大会加大传热系数。Lee等 [7] 数值模拟逆流水平椭圆管蒸发降膜的质扩散传热,研究表明,与静止环境相比,喷淋密度为0.093 kg∙m−1∙s−1~0.186 kg∙m−1∙s−1和迎面风速为0~2 m∙s−1时平均传热效果可提升34.7%。阚翠玲 [8] 通过实验得到了换热盘管各管段内流体温度随喷淋密度和迎面风速的变化趋势。司春强 [9] 组建了蒸发式冷却器实验台,对比了不同工况下的换热量,证明空气的湿球温度是提升系统性能的重要因素。朱冬生 [10] ,杨永安 [11] 等实验研究了喷淋密度与迎面风速对传热性能的影响,得到了机组运行的最佳迎面风速和喷淋密度。申江等 [12] 采用顺流式椭圆管型蒸发式冷却器,得出单位换热面积的最佳空气流速和水速,并通过干工况运行证明了蒸发式冷却器利用水的汽化换热具有更高的换热效率。何茂刚等 [13] 综述了前人研究成果,指出水平管降膜蒸发器在工作过程中可在液固、气液界面上发生相变,既能提升换热效率,又能节约用水量。对于蒸发式冷却器热质传递方面的数值模拟和实验多集中于系统整体的传热性能,较少分析传热过程中汽化换热量与空气温升换热量随影响因素的变化情况。为进一步提高蒸发式冷却器的换热性能,深入研究汽化换热量在整体换热过程中的占比是十分有意义的。
本文利用Fluent软件对降膜蒸发式冷却器的局部水平管进行了仿真研究,并通过搭建的实验台进行了验证,获得了迎面风速和喷淋密度对管外降膜流动与热质传递性能的影响规律,为设备的结构设计及经济运行给出参考。
2. 数值模拟
2.1. 物理模型的建立
为使模拟结果能够准确地反映实验工况下的降膜流动和热质传递特性,本文构建的三维物理模型参照实验台的搭建尺寸,其几何模型如图1所示。
在模拟过程中,喷淋水从布液孔流下至换热盘管区域,并在水平管外形成较为稳定的液膜流动铺展。由于叉排盘管在空间上呈并联排布,且换热管为圆管,具有周期性和对称性。为节约计算资源,对三维物理模型进行简化,选取流动单元的1/2为本文的计算模型。其中,换热管外径25 mm,管间距57 mm,喷淋孔半径2 mm,喷淋孔间距25 mm,布液高度16 mm。
(a) 降膜流动示意图 (b) 三维物理模型示意图
Figure 1. Horizontal tube liquid falling film flow heat transfer diagram
图1. 水平管液体降膜流动换热示意图
2.2. 数学模型的建立
1) 质量守恒方程
(1)
上式可用矢量形式表达:
(2)
2) 动量守恒方程
(3)
3) 能量守恒方程
(4)
4) 两相流模型
VOF模型通过跟踪计算每个控制体积内第k相的体积分数
得到相与相的界面分布,计算公式如下:
(5)
(6)
5) 蒸发冷凝模型
蒸发冷凝模型采用Lee [14] 模型来计算,该模型通过调节蒸发冷凝速率和饱和温度实现相变求解,计算式如下:
(7)
其中
(8)
式中,
为调节系数;
和
分别为液相和气相的温度;
为相变饱和温度;
为气泡直径;
为传质时间弛豫系数。
2.3. 网格划分及边界条件
利用Fluent Meshing软件对几何模型进行网格划分,并对液膜流动区域进行局部网格加密。生成的网格模型如图2(a)所示,边界条件设置如图2(b)所示。
(a) 网格划分 (b) 边界条件
Figure 2. Grid division and boundary condition diagram
图2. 网格划分及边界条件示意图
1) 喷淋水入口为速度入口
(9)
式中,
为喷淋孔半径,m;
为喷淋水流出速度,m/s;
为相邻喷淋口间距,m。
2) 空气入口为速度入口
(10)
3) 换热管壁面为恒定壁温
(11)
4) 喷淋水出口和空气出口为压力出口
(12)
5) 其他边界为对称边界
2.4. 求解方法
本文基于非稳态模型,使用压力基求解器计算,仿真参数及设置如表1所示,气液两相的物性参数如表2所示。
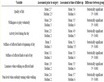
Table 1. Simulation parameters and settings
表1. 仿真参数及设置
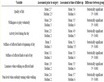
Table 2. Property of vapor and liquid
表2. 气液两相的物性参数
2.5. 模型验证
2.5.1. 网格独立性验证
如表3所示,在相同工况下,对不同网格数量下的周向角90˚处的液膜厚度进行对比。结果表明,当网格数量增加到137万之后,液膜厚度的变化趋于稳定,没有明显差异。因此,本文采用网格数量为137万的模型来进行后续的分析和讨论。
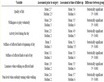
Table 3. Verification of grids independence
表3. 网格独立性验证
2.5.2. 时间步长无关性验证
如表4所示,时间步长依次选取为0.025 ms、0.05 ms、0.1 ms、0.25 ms进行分析。当时间步长为0.05 ms后,液膜厚度变化不大,故本文选用时间步长为0.05 ms。
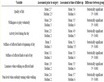
Table 4. Verification of time step independence
表4. 时间步长无关性验证
3. 降膜蒸发式冷却器实验台
本实验台的运行过程如图3所示,主要涵盖了软化水系统、可调温循环水系统、喷淋冷却水系统以及数据采集系统等。
实验过程中,热水泵将恒温水箱中的被冷却高温水泵入换热盘管内,被喷淋水蒸发冷却后从盘管上部流回恒温水箱并再次加热。喷淋水由布水装置均匀地喷洒在换热盘管表面形成换热液膜。空气由箱体下部两侧的风格栅进入冷却器,并与覆盖在换热盘管外的液膜进行热质交换,再经轴流风机引导排出。管外的喷淋水吸热后,蒸发为水蒸气由风扇吸走排向大气,而未蒸发的部分经过热交换后,留在集水箱继续使用。整个运行过程,液膜相当于传热介质,不考虑自身的热负荷。为减少水垢对换热过程的影响,设置了软化水装置对高温循环水及管外喷淋水进行处理。
本文所搭建的实验台具备多点数字采集和存储记录功能,可以实时采集冷却器的空气进、出口处的干球温度和相对湿度、空气流量、循环热水和喷淋水的温度和流量、换热盘管各管段温度等参数。实验中,通过手动阀门对被冷却热水和喷淋水的循环水量进行调节,由涡轮式测量仪LWYC-40L测得实时流量,测量精度为0.5级。通过变频器调节轴流风机风量,利用电子测风仪CATIC-AVT110在出口处进行风速测量,测量精度为 ± (0.2 m∙s−1 + 3%读数)。进口处风速由测风仪HT-8392测得,测量精度为3% ± 0.1。测温点温度由铂热电阻WZP-PT100测得,测量精度为 ± 0.5℃。而气体的温湿度则用感应计WD-PT100检测,精度为0.2级。
1——盐箱;2——软化水装置;3——恒温水箱;4——热水泵;5——热水调节阀;6——集水箱;7——喷淋水泵;8——喷淋水调节阀;9——风格栅;10——换热盘管;11——喷嘴;12——收水器;13——轴流风机;T——温度传感器;G——涡轮流量计;u——迎面风速仪;BP——变频器;PC——电脑
Figure 3. Working flow chart of the experimental bench
图3. 实验台工作流程图
4. 数据处理
1) 空气和喷淋水对流下的换热量
(13)
(14)
(15)
(16)
式中,
、
、
分别为空气吸热量、汽化换热量和空气温升换热量,W;
为空气的质量流量,kg/s;h为空气的焓值,kJ/kg;
为传质质量,kg/s;
为喷淋水的汽化热,kJ/kg;Y为水蒸气的质量分数;下脚标i和o为空气进出口的参数。
2) 汽化换热量占比
定义R为汽化换热量占总换热量的比重,计算式如下:
(17)
3) 空气传热系数
(18)
(19)
式中,
为空气传热系数,kW∙m−2∙K−1;
为空气与液膜之间的换热面积,m2;
为对数平均温差;
和
为空气进出口的干球温度;
为液膜温度。
4) 空气传质系数
(20)
(21)
式中,
为空气传质系数,kg·m−2·s−1;
为对数平均质量分数差;
为液膜饱和温度下对应的空气质量分数。
5) 喷淋密度
(22)
式中,
为单位时间内喷淋水体积流量m3/s;
为每排管数,根;
为换热管长,m。
6) 管内热水散热量
降膜蒸发式冷却器运行过程中管内热水的散热量可利用热水进出口温差和流量获得,计算式如下:
(23)
式中,
为热水的比热容,kJ/(kg·K);
为热水的质量流量,kg/s;
为各管段热水进出口温差。
5. 结果与讨论
5.1. 水平管外液膜流动铺展过程
图4为上排水平管外液膜流动铺展过程,喷淋水入口速度v = 0.76 m/s,对应喷淋密度Γ = 0.048 kg∙m−1∙s−1,喷淋水饱和温度
,逆流风速ua = 1.1 m∙s−1。从图中可以看出,喷淋水自上向下流动,当t = 50 ms时,喷淋水以柱状流形式撞击到水平管顶部,开始沿水平管轴向和周向流动铺展。当t = 90 ms时,两液柱沿水平管轴向流动铺展的液膜在中点位置处交汇融合,此时液膜在轴向上的流动铺展速度下降,但在重力和惯性力的驱动下,液膜开始以较快的速度在水平管周向上流动铺展,其上部分流动速度较慢,流径较大,下部分流动速度较快,流径较小,整体以倒三角形流态在水平管管间流动铺展。当t = 185 ms时,液膜已将水平管外壁完全包裹,在两液柱相交区域出现较为明显的扰动。当t = 215 ms时,在水平管下部的液膜交汇处逐渐形成二次液柱,但由于受逆向气流的吹举,液膜在水平管下部的流动铺展过程较慢。
如图5所示,为同一工况下液膜沿水平管流动铺展的模拟结果与实验观测结果对比。从图中可以看出,液膜铺展至相邻喷淋孔中间位置时,由于液膜的交汇融合,在轴向中线位置处形成突起,然后以倒三角形向下流动铺展,模拟结果与观测结果具有较好的一致性,说明所建模型有效。

50 ms 60 ms 70 ms 80 ms 90 ms
(a) 模拟结果 (b) 观测结果
Figure 5. Comparison of results between the simulation and the experiment
图5. 换热管外表面液膜铺展的模拟结果与观测结果对比
5.2. 水平管降膜流动与传热分析
降膜蒸发式冷却器运行过程中,热质传递主要沿管壁径向进行,基本不考虑轴向的液膜流动与传热 [14] 。故本文主要针对水平管周向角度进行液膜厚度分析和局部对流传热分析。
5.2.1. 喷淋密度对水平管降膜流动的影响
图6是逆流风速为1.7 m∙s−1时,不同周向角上液膜厚度随喷淋密度的变化关系。由图可知,喷淋密度由0.048 kg∙m−1∙s−1增长至0.136 kg∙m−1∙s−1时,液膜厚度在水平管周向上变化趋势一致,均随周向角的增大,先减小后增大,但液膜厚度最小位置随喷淋密度的增大会出现后移现象,变化区间约位于90˚~110˚。分析其原因,逆流风速不变,喷淋密度的增大使水平管外液膜受到的重力和惯性力增强,表面张力影响降低,故在水平管下半部分液膜厚度会发生一定程度的偏移。

Figure 6. The relationship between liquid film thickness and spray density at different circumferential angles
图6. 不同周向角上液膜厚度与喷淋密度的关系

Figure 7. The relationship between local heat transfer coefficient and spray density at different circumferential angles
图7. 不同周向角上局部传热系数与喷淋密度的关系
图7是逆流风速为1.7 m∙s−1时,不同周向角上局部传热系数随喷淋密度的变化关系。由图可知,局部传热系数随周向角的增加呈现先下降后回升的趋势,且随着喷淋密度的增大而显著提高。在水平管顶部区域时局部传热系数最大;当周向角位于0˚~20˚范围内时,局部传热系数迅速下降;而在160˚~180˚的周向角区间内,局部传热系数则表现出回升现象。这是因为水平管顶部受到喷淋水下落的冲击,导致热交换剧烈,局部传热系数较大;随着液膜沿圆管周向铺展,热边界层逐渐发展,增加了热阻,从而使局部传热系数减小。当液膜到达水平管底部区域时,由于液膜的交汇融合作用,产生波动,改善了传热性能,使得局部传热系数出现回升。此外,喷淋密度的增大提高了液膜的动能,加快了流动速度,从而增强了液膜与管壁间的对流换热。故随着喷淋密度的增大,局部传热系数也随之增大。
5.2.2. 迎面风速对水平管降膜流动的影响

Figure 8. The relationship between liquid film thickness and head-on wind velocity at different circumferential angles
图8. 不同周向角上液膜厚度与迎面风速的关系

Figure 9. The relationship between local heat transfer coefficient and head-on wind velocity at different circumferential angles
图9. 不同周向角上局部传热系数与迎面风速的关系
图8是喷淋密度为0.048 kg∙m−1∙s−1时,不同周向角上液膜厚度随迎面风速的变化关系。由图可知,迎面风速增大可使周向上液膜厚度增大,水平管上半部分的液膜厚度增加较小,下半部分变化明显大于上半部分。这是因为液膜在水平管外流动铺展时,下半部分区域是液膜与逆向气体对流作用的主要区域,迎面风速的存在对液膜起到托举作用,有助于减缓液膜沿壁面的下落速度,使其在管壁区域发生液膜堆积,从而导致液膜厚度的增大。
图9是喷淋密度为0.048 kg∙m−1∙s−1时,不同周向角上局部传热系数随迎面风速的变化关系。由图可知,迎面风速的增大对局部传热系数在周向上的分布影响不大,局部传热系数随迎面风速的增大略微增大。
5.3. 水平管降膜流动过程中的热质传递分析
5.3.1. 汽化换热量占比分析
图10为空气吸热量随喷淋密度和迎面风速的变化关系,图11为汽化换热量随喷淋密度和迎面风速的变化关系。由图可见,喷淋密度和迎面风速逐步增大时,汽化换热量及空气换热量走势一致。迎面风速不变,喷淋密度的增大会使换热量先增后降;而喷淋密度不变时,增大迎面风速,换热量先明显增加,然后趋向平缓。分析其原因,是由于喷淋密度由小变大时,水平管外喷淋水会逐渐湿润整个管壁,液膜和空气间有效换热面积逐步增加传热能力提高,待完全包覆换热管后,换热面积不变,液膜的厚度增加,热阻也随之变大,反而不利于传热的进行。而迎面风速的增大,会增加冷却器内的气流,使气流速度变大,从而加强了盘管外表面的液膜扰动;但当迎面风速过大时,液膜的均匀性会受到破坏,反而使蒸发冷却器的传热性能下降。
图12展示了汽化换热量占比随喷淋密度和迎面风速的变化关系。从图中可以看出,汽化换热量占总换热量的比值为0.73~0.79,随着迎面风速的增大,汽化换热量占比R变小。其原因在于未饱和空气进入系统后,与盘管区域的液膜和水珠相接触,此时在液膜与空气之间形成了温度差和水蒸气分压差,在两者的驱动下,空气会开始吸收液膜蒸发的汽化热和显热,逐步变成近饱和高温湿空气。当迎面风速持续增大时,盘管区域的空气流动及更新速度加快,从而使饱和状态无法维持,导致吸收潜热的能力下降,故迎面风速增大,汽化换热量占比变小。

Figure 10. The relationship of air heat absorption with spray density and head-on wind velocity
图10. 空气吸热量与喷淋密度和迎面风速的关系

Figure 11. The relationship of vaporization heat transfer with spray density and head-on wind velocity
图11. 汽化换热量与喷淋密度和迎面风速的关系

Figure 12. The relationship of proportion with spray density and head-on wind velocity
图12. 占比与喷淋密度和迎面风速的关系
5.3.2. 空气传热传质系数分析
图13为空气传热系数随喷淋密度和迎面风速的变化关系,图14为空气传质系数随喷淋密度和迎面风速的变化关系。由图可知,在相同的迎面风速条件下,随着喷淋密度的增大,空气的传热系数和传质系数会先上升然后下降。这是因为喷淋密度较小时,液膜和空气之间接触不均匀,此时的传热传质效果较差,当喷淋密度逐渐增大,液膜会沿着管道轴向和周向均匀铺展,传热传质效果提升的同时液膜厚度也在不断增加,致使液膜与空气间传热阻力增强,此时传热传质性能开始变弱。而迎面风速的变化,可以对液膜的湍动程度造成干扰,风速越大扰动越强,促使液膜到空气的对流传热加强,提高了液膜的蒸发速度,进而加强了传热传质性能。

Figure 13. The relationship of air heat transfer coefficient with spray density and head-on wind velocity
图13. 空气传热系数与喷淋密度和迎面风速的关系

Figure 14. The relationship of air mass transfer coefficient with spray density and head-on wind velocity
图14. 空气传质系数与喷淋密度和迎面风速的关系
5.4. 装置传热性能实验与仿真验证
图15给出了不同迎面风速下降膜蒸发式冷却器内各管段的热水温度变化。由图可知,迎面风速增大时,管内热水温度下降明显,整体的换热温差为2.5℃,考虑到各管段上的平均换热温差较小且十分的不均匀,为更好的比较实验与仿真的计算结果,取换热效果较好的管段局部换热量和仿真结果相对比。
图16给出了迎面风速
时,实验平均换热量与仿真换热量的对比。由图可知,迎面风速相同时,实验和仿真的换热量随喷淋密度变化的趋势相近,平均误差为14.5%,模拟的最佳喷淋密度在0.092 kg∙m−1∙s−1,比实验得出的最佳喷淋密度0.116 kg∙m−1∙s−1要提前。造成偏差的原因可能是实验过程中存在向外放热导致热量损失,且液膜的不均匀分布或局部干斑的形成等,导致实验条件下需要更大的喷淋密度才能达到较好的传热性能。

Figure 15. The change of hot water temperature in each pipe section
图15. 各管段内热水温度的变化

Figure 16. Comparison between experimental average heat transfer and simulation heat transfer
图16. 实验平均换热量与仿真换热量的对比
6. 结论
本文对降膜蒸发式冷却器局部水平管传热性能进行仿真与实验研究,获得以下结论:
1) 水平管外液膜流动铺展过程中,在周向上,液膜厚度先变小后变大,最薄区域位于周向角90˚~110˚内。液膜厚度整体随喷淋密度和迎面风速的增加而变大,由于托举作用,迎面风速对液膜厚度的影响主要针对于水平圆管下半部分。
2) 局部传热系数沿周向整体呈下降趋势,在周向角120˚~150˚范围内,局部传热系数减小迅速,而在周向角160˚~180内˚,由于液膜交汇融合产生液膜波动,局部传热性能回升,传热系数变大。
3) 模拟工况范围内汽化换热量占总换热量的比值为0.73~0.79,说明蒸发式冷却器主要利用汽化换热传递热量。迎面风速的增加使管外空气的更新速度变快,故汽化换热量占比随迎面风速的增加而减小。
4) 喷淋密度的增加改变了液膜与水平圆管外空气的有效换热面积及换热温差,随着喷淋密度的增加,汽化换热量与空气对流传热传质系数先变大后变小,在喷淋密度为0.092 kg∙m−1∙s−1时达到最大值,汽化换热量直接影响了蒸发式冷却器的总传热系数。
基金项目
河南省教育厅科技研究重点项目(13A470247)。
NOTES
*通讯作者。