1. 引言
机床作为制造业领域的航母,承载着各种核心产业的基础工作,大到航天卫星的生产制造,小到手机壳等小部件的量产,均起着基本而又关键的作用。如何提高机床的加工精度、产品的加工质量以及削减工作成本,是中国乃至全世界工业强国不断追求的目标之一 [1] 。随着数控加工的高速化、高精度化,在传统加工条件下对加工精度影响不大的机床结构动力学特性因素成为了严重阻碍数控机床加工性能提高的瓶颈 [2] 。
机床的动态性能并不是单一针对某个特性,它是一系列性能的总称,比如工作产生的噪声、振动、几何误差、热变形等。这些特性导致机床在工作时不可避免的会产生一些结构位移,其中振动引起的结构变化最为显著,因此对于当前机床领域的研究,用抵抗变形的能力来描述机床的动态性能。目前国内外学者对于机床动态特性的研究主要通过有限元法和实验模态分析法(Experimental Modal Analysis, EMA)来获取机床模态参数,并通过对机床模态参数进行辨识对机床动态特性进行表征。李天箭 [3] 等利用灵敏度分析法对模态实验数据进行灵敏度分析从中找出机床对刚度和质量灵敏度高的结构从而对其进行优化。郭阳 [4] 等利用Workbench分析磨床静动特性,分析了床身不同材料、结构对整机动特性的影响,并选取不同接触刚度因子,对磨床整机动特性的影响进行了分析。赵天义 [5] 等人利用Workbench分析立式加工中心的动态特性仿真计算机床固有频率,分析机床动态性能。通过整机模态试验验证了仿真的结果,修正了有限元模型,同时还针对修正后的有限元模型进行了谐响应分析,确定机床关键部件,为后续机床二次设计与优化提供了重要依据与方向。钱隆 [6] 等讨论了机床整机模型简化分析方法,以整机为研究对象,通过分析机床部件是否处于机床整机闭合力学系统等准则,确定了不同部件的简化必要性和策略,形成了一套完整高效的整机性能分析简化方法,从而减少机床这种大型部件的有限元计算时间。本文将结合实验模态分析法找出结构关键点,然后使用有限元法来对机床动态性能进行分析优化。
2. 优化依据及前处理
本文主要优化依据来源于实验模态分析之后所得到的初步优化方案。首先使用锤击法采集机床模态信息分析机床模态频率和振型等数据 [7] 。由于本文中讨论的优化目标主要针对结构第一阶模态频率和振型,所以只讨论模态前三阶固有频率及振型。表1为机床的前三阶固有频率,前三阶频率振型如下图所示。
图1为实验模态分析所得机床一阶模态振型。
图2为实验模态分析所得机床二阶模态振型。
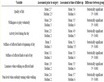
Table 1. The first three mode frequencies
表1. 前三阶固有频率
图3为实验模态分析所得机床三阶模态振型。
从模态振型和实际优化需求初步推断,影响机床一阶频率和振型的主要因素是机床的横梁部件。单独建立横梁点位如图4所示,使用灵敏度分析法,对横梁上的点位进行刚度灵敏度分析,找出对固有频率和振型影响最大的点位。横梁刚度灵敏度如图5所示。
根据分析横梁上各点间灵敏度可以得知,108-95和107-96这两对点之间的刚度值变化对整机模态频率的影响最为明显,所以初步优化方案为在横梁背面加上一组交叉筋来增加这一对点的刚度。通过对交叉筋设置参数集,并计算仿真结果寻找最优的设计方案,再使用Workbench分析优化前后结构的静力特性和模态频率的变化,以此为下一步更进一步的优化提供参考。
3. 建立机床3D模型
由于机床体积较大,整体模型较为复杂,床身以及其它部件中有很多开孔和细小零件,在有限元计算时会占用较大的计算机内存,影响结果的计算时间。为了计算方便减少程序计算时间,在不改变原有结构的情况下对机床模型进行简化处理。如图6所示,在SolidWorks中建立机床三维模型。
4. 基于Workbench的有限元模型建立
4.1. 模型材料赋予
本文主要的有限元分析是针对机床整机的模态分析和静力学特性,使用的有限元分析软件是Ansys2022R中的Workbench平台。首先进行的是初始状态下整机的静力学仿真和模态仿真。待优化机床使用到的材料有大理石、灰铸铁和结构钢,其参数性能如表2所示。
4.2. 接触条件设置
接触条件的设置极大程度影响有限元软件的计算结果,机床是大型可动机械,如果将部件间的连接关系笼统地设置为固定连接,则无法反映机床的真实情况,其中特别是机床导轨与滑块间的接触设置,将接触条件设置的足够贴合实际情况,则仿真计算结果就能够更好反映结构的真实变形情况和模态频率,为后续的优化提供参考。
本文中根据导轨厂家给出的刚度建议值来对导轨与滑块间的连接进行定义,如图7所示是对导轨之间的接触设置,如图8所示为滑枕导轨与滑座之间的接触设置。
其中要注意的是滑枕滑座在相对运动方向的刚度系数一般为平行导轨方向刚度系数的两倍,其他导轨与滑块的设置同理。如图8所示为横梁与滑枕之间刚度系数设置。
4.3. 网格划分
使用自动网格划分对模型进行单元格划分,由于机床模型较大且孔洞较多,再根据程序自动划分后的仿真需求进行尺寸调整,尽可能地减少网格划分过程中的警告信息,图9为网格划分结果。
5. 仿真结果及对比
对结构振动而言,动态特征灵敏度定义为结构的特征对关于结构参数或其他设计变量的改变率 [8] 。所以在仿真中,我们主要关注的是该结构静态下的位移变化和模态频率振型。结合Workbench中对模型的仿真结果与机床自身结构特点,进行初步优化,再对优化后的模型进行仿真分析,对比前后模型的仿真结果验证优化效果。
Workbench的静力学分析能够很好的分析结构在静定平衡状态下的应力应变情况和结构的稳定性,静力学主要方程如下:
式中:[δ]——位移向量;[K]——系统的刚度矩阵;{P}——静载荷向量。
模态分析是机械结构分析中常用的分析方法,它主要分析结构本身的固有频率,振型以及振动形态。在机床设计时通常会尽可能的提高第一阶固有频率来提高机床的稳定性,减少被加工产生的振动影响的可能。忽略阻尼对模态系统的影响,对于机床振动结构,其多自由度离散系统的自由振动方程为:
式中:[M]——系统的质量矩阵;x——系统产生的位移。
图10为优化前整机静力学仿真结果。
因为本文以机床整体第一阶固有频率和振型为优化目标,所以这里仅给出前三阶模态振型作为参考。图11为机床优化前前六阶固有频率,图12为优化前整机第一阶模态振型仿真结果。
图13为优化前整机第二阶模态振型仿真结果。
图14为优化前整机第三阶模态振型仿真结果。
对比实验得出的模态振型和固有频率可以看出前后模态顺序和模态振型基本一致,固有频率稍高的原因可能是导轨的刚度值比实际稍有出入所导致的,但基本可以用来作为下一步优化依据。
6. 响应面优化
6.1. 交叉筋参数化
基于前面提到的实验模态分析结果和仿真结果,对机构进行初步优化,在横梁上两组灵敏度较为突出的点位间设置交叉筋,设置筋板宽度P1和筋板厚度P2两个参数。交叉筋位置如图15所示。
6.2. 优化过程
在实际优化过程中,筋板的参数条件受多方面条件制约,为保证优化数据的合理性本研究为优化参数设置优化范围。
确定完参数的约束条件后进行实验设计,将一阶频率设置为首要优化目标总变形为次要优化目标生成实验参数进行优化。图16为设计参数P1、P2在各自范围内的取值,对所有数据生成点进行计算。
从上述设计点生成的报告中选取一阶频率最大的设计点作为优化设计方案,下面就是优化后模型的静力学仿真结果和前三阶模态振型结果。通过计算得出连杆一阶模态最大变形为1.5574 mm,发生位置是滑枕下端部。图17为优化后静力学仿真结果。
通过计算得出优化后机床整体模态频率皆有所上升,其一阶模态频率上升至58.237 Hz并且其一阶模态最大变形下降至1.5574 mm。图18为优化后机床的第一阶模态振型仿真结果。
图19为优化后机床的第二阶模态振型仿真结果。
图20为优化后机床第三阶模态振型仿真结果。
下表3为机床整机优化前后,前三阶频率和一阶模态最大变形对比数据和变化值。
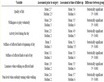
Table 3. Comparison before and after
表3. 优化前后对比
从优化前后的数据中可以看出,该方案优化后整机的前三阶固有频率有所提升,一阶频率由原来的40.557 Hz提升至58.237 Hz,二阶频率由原来的45.671 Hz提升至60.7 Hz,三阶频率由原来的69.519 Hz提升至92.685 Hz,其一阶模态最大变形也有小幅度降低。
7. 结论
1) 通过使用Workbench对该机床模型进行优化,使其一阶固有频率提升了43%,其一阶模态变形也有小幅度提升,达到了优化目的。
2) 优化后的机床模型能够满足更高要求的加工需求,机床整体稳定性有所提升。
3) 使用Workbench优化平台能够很好的解决工程上的结构优化问题,能够满足以模态频率和静力变形作为优化目标的优化问题,为实际优化解决方案提供有价值的参考。