1. 引言
截至2023年年底,我国机动车保有量为4.35亿辆,稳居世界第一。其中汽车为3.36亿辆,占比达到了77.24% [1] 。同时汽车行业正朝着轻量化方向发展,材料和结构的改变对产品的疲劳寿命有着巨大影响 [2] 。对于汽车上的关键零部件,由于它们的振动频率各不相同,当某一特定零部件受到与其固有频率相近的外部刺激时,可能会发生共振现象 [3] ,导致振动加剧,从而容易产生疲劳。汽车零部件的振动特性和轻量化设计是现代汽车设计中的重要考虑因素,而踩踏板又是汽车工作中使用频率最高的零件之一,董志新 [4] 等人利用有限元法对油门踏板和前围板进行模态及动刚度分析,结果表明增加踏板安装点的刚度能较好地减少振动传递和幅值。黄威 [5] 等人通过建立瞬态动力学模型来分析踏板并获得断裂瞬间的能量,根据仿真和实验结果来重新设计模型,使其满足动态断裂和静态强度要求。
本文以踩踏板零部件为研究对象,通过Creo建立踩踏板的三维模型,然后将模型导入到HyperMesh软件中进行自由状态下的模态分析和常用工况下的静力学分析,再使用Optistruct模块对踩踏板进行常用工况下的拓扑优化。最后通过优化前后的对比验证了此方法的可行性,对结构轻量化设计具有一定参考意义。
2. 建模
2.1. 踩踏板的三维建模
踩踏板的三维模型通过Creo软件建立。建模时对模型进行适当的处理,去除影响不大的细小防滑纹路、圆角和倒角等,这样有利于提升后续网格划分和有限元计算的速度。建立完的踩踏板模型转换成后缀名为.x_t的Parasolid文件格式导入到HyperMesh软件中,如图1所示。
2.2. 踩踏板的有限元建模
1) 定义材料属性:踩踏板零部件的材料属性参数如表1所示。
2) 划分网格:良好的网格能保证模型的准确性,由于六面体单元矩阵远小于四面体单元矩阵,因此采用六面体单元能显著提高模型计算效率。在HyperMesh软件中先划分2D单元,再以面单元生成质量更高的3D单元,如图2所示。
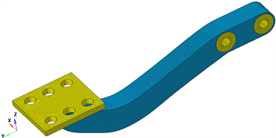
Figure 2. Finite element model of pedal
图2. 踩踏板有限元模型
3. 模态分析
模态指的是机械结构的固有振动特性,每个模态都具有特定的固有频率、阻尼比和模态振型,分析这些模态参数的过程称为模态分析。模态分析可分为计算模态分析和试验模态分析两种方法。
在HyperMesh等有限元分析软件中,模态分析是一种计算结构振动特性的数值技术,它是动力学分析的基础 [6] 。模态分析主要用于求解物体的固有特性,即固有频率和振型。当物体达到固有频率时,其振幅会变得很大,从宏观上看就是明显的震动,通常会影响正常使用。模态分析只需要材料的弹性模量和泊松比等基本材料属性。
通过模态分析,设计人员可以确定结构的频率和振型,从而在设计过程中有效规避共振问题。模态分析的最终目标是识别系统的模态参数,为结构系统的振动特性分析、震动故障诊断和预测以及结构动力特性的优化设计提供依据。
3.1. 模态分析理论
模态分析是一种使用数学方法和计算技术来研究结构的振动特性及固有频率的分析方法,系统的运动方程如下 [7] :
(1)
式(1)中:
为质量矩阵,
为加速度矩阵,
为阻尼矩阵,
为速度矩阵,
为刚度矩阵,
为位移矩阵,
为外部载荷。
求解结构的自由振动时的固有频率和阵型时可忽略外部载荷,同时当阻尼对系统影响不大时也可以忽略。最后系统的运动方程化简为:
(2)
当形成简谐振动时方程为:
(3)
在该方程中
为特征值,
是自由振动圆频率,
为自由振动频率,单位为Hz,与
对应的特征向量为
,是自由振动频率
所对应的振型。
因此,模态分析的实质是对进行简谐振动的运动方程进行特征值和特征向量的求解。
3.2. 模态分析结果
模态分析确定结构固有频率和振型是结构设计中的重要依据。汽车踩踏板振动特性取决于其刚度和质量,与外力无关,故模态分析不考虑外载荷和边界条件。而自由模态分析能更好地揭示结构固有振动特性,帮助设计优化和振动问题分析,为结构安全性和性能提供重要参考。
通过HyperMesh对踩踏板进行自由约束情况下的模态分析,分析结果过滤掉前6阶刚体模态,这些模态主要为整体平移或者转动而不是内部形变,对研究结构的振动特性意义不大。因此,对踩踏板进行自由模态分析时只提取其发生内部应变的前6阶固有频率和模态阵型,相应的阵型云图如图3所示,结果分析如表2所示。
4. 拓扑优化
4.1. 常用工况静力学分析
静力学分析通过研究结构在平衡状态下的受力情况,帮助工程师设计稳定、承载能力强的结构,确保其在外力作用下不发生失稳或破坏,从而提高结构的安全性和可靠性。静力学分析还可以为结构设计优化提供依据,降低建设成本,提高结构的效率和性能。
对踩踏板进行静力学分析,主要受到的外部载荷为50 N的踩踏力,方向垂直于踩踏面板。约束为端部的两个铰接孔与车身和阀门进行连接,只存在孔的轴线方向旋转的自由度。经过有限元静力分析,应力云图如图4所示,结果显示最大应力为6.391 MPa,位于踩踏板与阀门连接孔的下部,位移云图如图5所示,最大位移为2.326 mm,位于踩踏板的踩踏面上。
4.2. 踩踏板拓扑优化
利用HyperMesh软件中的Optistruct模块,对踩踏板有限元模型进行常用工况下的结构优化设计。分别进行定义优化区域、设置条件约束和定义目标函数后即可进行迭代运算,求解出优化后的踩踏板模型。
合理划分优化区域和非优化区域,不仅能够实现结构轻量化,而且还能很好地保留了原有结构的主要部分功能。把踩踏板的长柄部分设置为优化区域,同时设置优化区域x方向上的拔模制造约束,通过调整长柄材料的分布来实现踩踏板的轻量化设计。把踩踏面和安装孔的预留空间设置为非优化区域,这样可以保证踩踏板原有结构的基本形态和使用功能。
设置适当的优化约束和目标可提高设计效率、降低成本,确保可靠性与可行性,助力算法搜索最佳设计方案。优化约束是在进行拓扑优化时需要满足的条件,优化约束设置为踩踏板优化区域的体积分数Volumefrac为原设计区域的15%。优化目标是拓扑优化的最终目的,是需要最大化或最小化的性能指标,优化目标设置为最小化优化区域的应变能。
对优化模型进行完以上步骤后即可进行拓扑优化运算,经过73次的迭代优化,将踩踏板有限元模型的优化结果显示为单元密度,筛选出密度大于0.13的单元得到密度云图,如图6所示。
4.3. 结果校核与对比
对踩踏板进行拓扑优化后需要对优化结构进行校核和验证,目的是确保该结构是否满足强度、刚度、
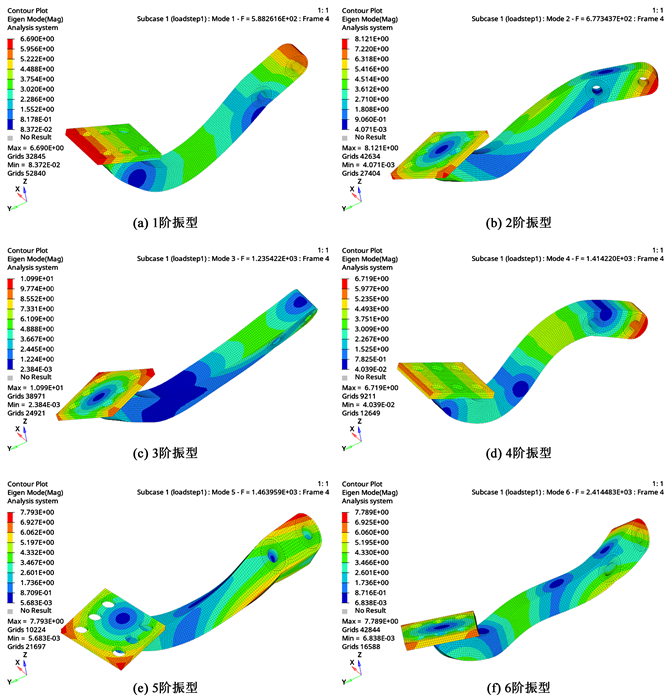
Figure 3. Pedal first 6 order modal shape figure
图3. 踩踏板前6阶模态振型图
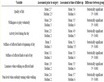
Table 2. The first six natural frequencies and modal shapes of the pedal
表2. 踩踏板前六阶固有频率和模态振型
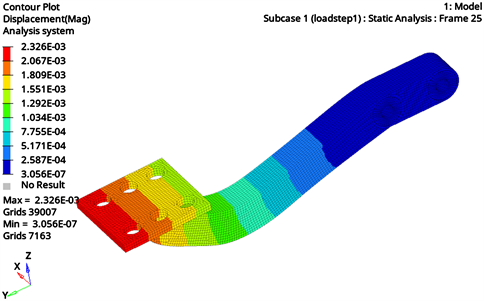
Figure 5. Deformation cloud of the pedal
图5. 踩踏板位移云图
稳定性等方面要求和评估结构的可靠性和可信度,保证其在实际工作中达到较高的安全性和可靠性。
使用HyperMesh软件的OSSmooth功能,将踩踏板优化后的结构进行常用工况下的静力学分析。经过静力学强度校核,优化模型的应力如图7所示,位移如图8所示。结果显示最大应力为20.72 MPa,位
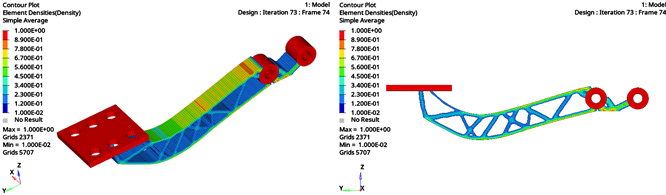
Figure 6. Element density cloud of topology optimization
图6. 拓扑优化单元密度云图
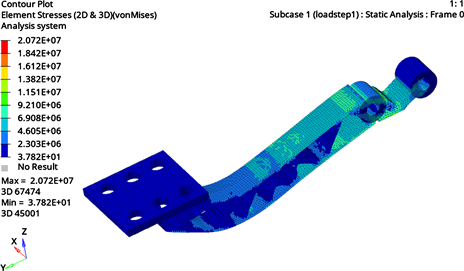
Figure 7. Stress cloud of optimization model
图7. 优化模型的应力云图
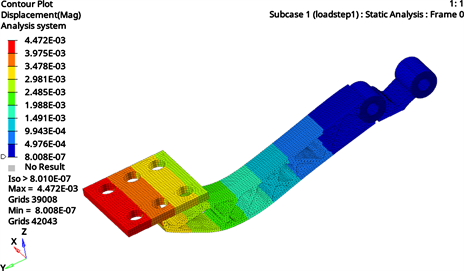
Figure 8. Deformation cloud of optimization model
图8. 优化模型的位移云图
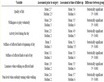
Table 3. Comparison of optimization results of pedal
表3.踩踏板优化结果对比
于踩踏板与阀门连接孔的下部,该材料的屈服应力为75 MPa,即该结构满足使用安全性。最大位移为4.47 mm,位于踩踏板的踩踏面上。优化前后性能对比如表3所示,由此可得,优化后的踩踏板在满足使用强度的情况下质量降低了45.38%,提高结构效益和经济效益。
根据优化后的有限元模型进行实体化重构,重构模型能更好地反映实际结构的几何形状和特征,方便工程师对结构进行进一步的分析、优化和设计,重构后的模型如图9所示。
5. 总结
本文采用HyperMesh软件,对踩踏板进行了有限元自由模态分析和常规工况下的拓扑优化,得出以下结论:
1) 通过HyperMesh软件对踩踏板进行了模态分析,获得了1~6阶模态振型图,从这些图中可以观察出,踩踏板发生共振时多以弯曲形态为主,原因是踩踏板结构类似于梁结构,其振动形态大部分是以梁的横向振动模式出现。当外界频率达到1400 Hz左右时,容易同时激发出4、5阶振动,将会导致结构产生非线性响应而造成更大损害。
2) 基于变密度法对踩踏板柄杆处进行拓扑优化,调整设计域中的材料分布,实现在给定约束条件下结构的最佳形状。优化后结构的最大等效应力为20.72 MPa,小于材料的许用应力75 MPa,结构满足要求情况下质量降低了45.38%,提高了结构的利用效益和成本效益,为踩踏板的轻量化设计提供了一定的参考价值。