1. 引言
液压变压器是一种液压传动装置,用于将输入的液压能转换为输出的液压能,并实现压力的变换。它类似于电气系统中的变压器,但是用于液压系统而非电气系统,液压变压器的主要作用是实现液压能的转换和传递,它可以将输入液压系统的高压能转换为低压能,或者将低压能转换为高压能,这种能量转换可以用于控制和操作液压系统中的执行器,通过联合仿真技术搭建液压变压器的动力学、运动学和液压系统模型能够在仿真环境下对液压变压器的工作状态进行模型,进而分析液压变压器受力、泄漏量和摩擦转矩损失特性,实现关键结构的分析,为其优化提供理支撑条件,本研究通过构建液压变压器模型,对其滑靴底部参数进行优化研究。
而在运行当中,滑靴副的主要磨损形式是滑靴和斜盘之间造成的磨粒磨损 [1] ,基于模型Archard方程,Chang等 [2] 人提出了一种针对于EHL情况的磨损模型,并且通过实验进行了验证,但是在分析滑靴副和斜盘磨损特性时具有一定的局限性,在磨损模型当中,对于摩擦副影响最大的就是油膜厚度,其中包括摩擦副的结构形式、结构参数等 [3] ,对于滑靴副油膜相关研究文献有很多,对于滑靴副油膜研究的重点也不一样,其中包括对于滑靴副油膜厚度的数值计算方法 [4] ,还包括对于油膜的动态特性分析的研究方法 [5] [6] ,还有研究滑靴副油膜对于摩擦副微运动的研究影响 [7] ,唐群国 [8] 对于水压式液压泵滑靴发生倾侧现象进行研究,发现失效本质,提出了减小滑靴质量达到增加抗倾覆力矩的作用,徐兵等 [9] [10] [11] 研究了滑靴倾覆失效原因,找出转动惯量造成的离心力是偏磨失效的本质,从滑靴的材质和结构入手降低离心力。
因此本文通过建立滑靴副油膜厚度方程分析油膜特性,推导出油膜雷诺方程分析滑靴副受力分布,最后建立滑靴副泄漏量和摩擦转矩损失为目标函数的粒子群算法,以滑靴副底部结构参数作为优化变量进行优化设计,通过模型仿真数据比较优化前后的泄漏量和摩擦转矩损失,数据显示优化后的参数能够显著降低泄漏量和摩擦转矩损失。
2. 滑靴运动受力分析
液压变压器缸体转动工作过程中,滑靴受到来自于柱塞内液压力、斜盘与滑靴相互作用力总共五个力的作用,其中主要的力是来自于柱塞内的液压力,滑靴的受力图 [12] ,如图1所示,来自于柱塞的三个轴向力的合力通过滑靴和滑靴与斜盘之间的油膜传递到斜盘上,斜盘具有一定的倾斜角度,该力再斜盘上可以将力分解为沿着斜盘的切向分力
和垂直于斜盘的垂直分力
,斜盘和滑靴之间形成的润滑油膜会形成一定的黏性摩擦力
和滑靴的惯性力
,可以平衡一部分沿斜盘的切向分力,来自柱塞腔内柱塞对于滑靴的压紧力
是主要作用力,此作用力是来自于柱塞的三个轴向力的合力,来自柱塞内部液压力
、滑靴组件的惯性力
以及柱塞与缸体之间的摩擦库仑力
。
1. 斜盘;2. 滑靴;3. 柱塞球头;4. 柱塞;5. 缸体;6. 配流盘
Figure 1. Force diagram of the slipper pair in motion
图1. 滑靴副运动受力图
如图1所示,斜盘对滑靴的液压支撑力
可以分解为沿缸体轴线的轴向分力
和垂直于轴线的分力
,垂直于轴线的分力驱动或阻碍柱塞带动缸体转动,此力也将导致柱塞再柱塞腔内发生偏移,导致柱塞头部和与缸体边缘处与柱塞产生力,此力可以与柱塞和缸体之间产生的油膜压力
和
平衡,轴向分力
的表达式可以表示为:
(1)
式中
——柱塞惯性力;
——柱塞液压力;
——柱塞缸体库伦力;
——黏性摩擦力。
因为柱塞和缸体之间存在润油膜的作用,其库仑力相对于其它轴向力较小,一般可以忽略,可以把上式整理为:
(2)
式中
——柱塞内液压力来自A、T和B口压力;
——柱塞的质量;
——滑靴的质量。
3. 油膜支撑力分析
轴线方向有回程盘液压支撑力
,其中
有两个部分组成,中心油池产生的液压支撑力和滑靴密封带形成的油膜产生的压力
,由于中心油池是由凹型槽形成,其中的压力可以看成是均匀分布,滑靴底面对于滑靴的液压支撑力的表达式可以表示为:
(3)
如图2所示,其中
为滑靴底面密封带的内外径,斜盘对滑靴的垂直作用力来自于滑靴和斜盘之间形成油膜产生的反推力,该推力的作用是趋向于把滑靴从斜盘表面分离开。而每一个滑靴中心凹槽池处的油液是柱塞内液压经过柱塞细长小孔流进来的,通过连通器原理可得到,中心油池处的压力与柱塞内油液压力相同。
1. 斜盘;2. 滑靴油膜;3. 滑靴
Figure 2. Clearance of the slipper swash plate oil film
图2. 滑靴斜盘油膜间隙
柱塞配流窗口后滑靴密封带半径为r点处的油膜压力为:
(4)
则上述滑靴对于斜盘的支撑力可以表示为:
(5)
4. 液压变压器配流原理
液压变压器的配流盘主要结构包含A配流窗口(共轨压力端口)、B配流窗口(连接负载端口)、T配流窗口(平衡A、B口压力变化造成的流量不平衡),缸体转动过程中柱塞与三个配流窗口相互交错连通 [13] ,通过配流窗口A进入到柱塞内的液压力驱动或者阻碍缸体进行转动,而柱塞和不同压力的配流口进行连同时造成柱塞内油液的压力冲击以及出口的流量波动,而与每个配流窗口连接的三角槽可以对油液的压力和流量波动达到很好的缓冲效果,如图3所示。
配流窗口连接的三角缓冲槽的通流面积与缸体旋转的相对位置不同而发生变化,因此在柱塞腔与不同的配流窗口相连接时用三角缓冲槽对其进行缓冲减压,降低柱塞内液体的压力冲击和震荡,并且柱塞内油液倒灌也与缓冲槽有很大的关系。配流盘三角缓冲槽的结构如图4所示。
1. 配流口B;2. 三角缓冲槽;3. 配流口T;4. 柱塞口;5. 配流口;A 6. 外密封带;7. 内密封带
Figure 3. Structure of the distribution plate
图3. 配流盘结构
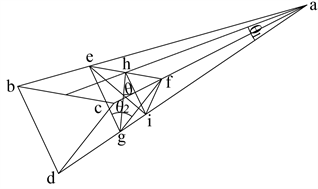
Figure 4. Structure of the triangular damping groove
图4. 三角缓冲槽结构
配流盘中用三角缓冲槽是一个三棱锥体形状,其中平面abc与平面bcd和平门efg相垂直,且
和
都为等腰三角形,两三角形都是以ef为底边两者的夹角为
,eg和fg的夹角与ei和fi的夹角相同都是
,
与地线ad的夹角为
此角为三角槽的深度角,其中
为三角缓冲槽的过流面积,且
垂直于
的中线ah,其
的面积可以表示为:
(6)
当
最小时,
的值是最大,对其进行求导可以得出当
,其
值是最大的,所以
的最小值为:
(7)
当
面积最小时,
与地线ad相互垂直,其中过流面积
和实际的最小过流面积
的误差值为:
(8)
当
越小时,误差值越小,其误差值最小时候即
时,其值
。
其中最小的过流面积可以
可以表示为:
(9)
上述表达式
可以表示为:
(10)
5. 基于液压变压器的AEMSim建模
5.1. 建立模型
本研究建立液压变压器模型参数设置如表1所示,根据液压变压器实际工况对元件进行相对应参数匹配,在液压变压器效率影响因素的研究中,完整的模型参数设置有助于更准确地模拟实际运行条件,建立的AMESim模型如下图5所示。
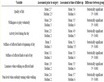
Table 1. Simulation parameter settings
表1. 仿真参数设置
5.2. 不同控制角度柱塞腔压力流量波动
通过建立的模型,设置符合工况的运行参数,输入不同的控制角度进行工况运行,观察液压变压器柱塞腔内的流量和压力的波动情况,如图6和图7所示,在保持其它运行参数不变的情况下,柱塞内的流量和压力变化情况。
如图6所示,在保持改变不同的控制角度可以看出,随着控制角度的增加,柱塞腔内的流量波动峰值逐渐增加,流量波动的频率随着控制角度的增加波动频率也随之增加,这是因为控制角度的增加液压缸体的转速随着增加,因此波动频率逐渐增加。
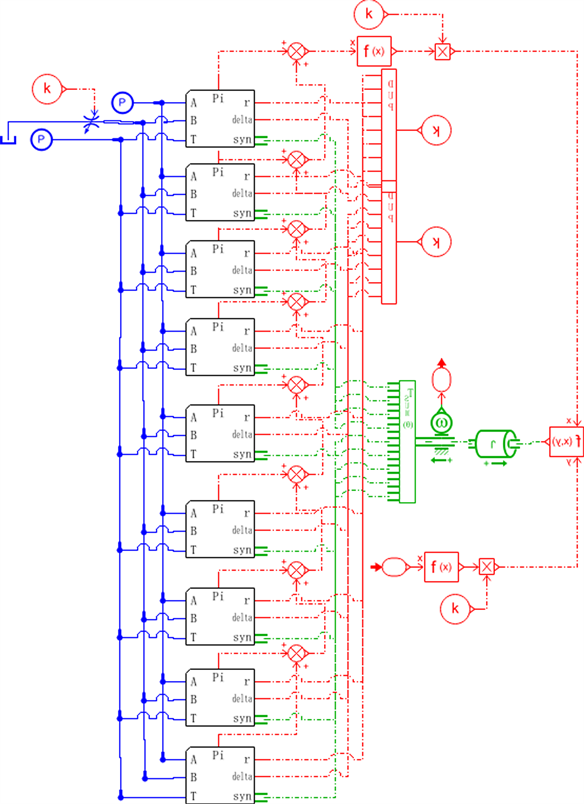
Figure 5. AMESim model of the hydraulic transformer
图5. 液压变压器AMESim模型
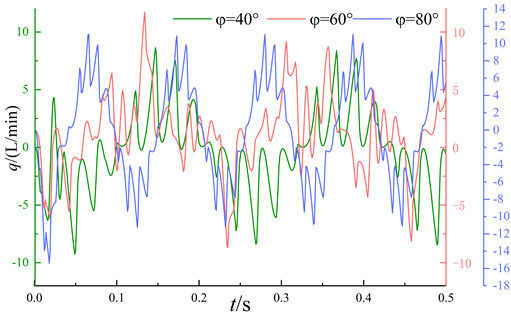
Figure 6. Flow fluctuation in different control angle piston chambers
图6. 不同控制角柱塞腔流量波动
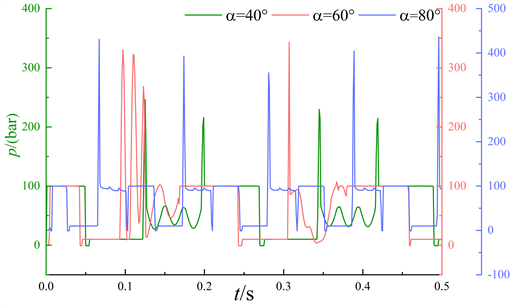
Figure 7. Pressure fluctuation in different control angle piston chambers
图7. 不同控制角柱塞腔压力波动
如图7所示,随着控制角度的增加,柱塞腔内压力峰值也随之增加,这是因为控制角度的增加,导致输出压力的增加,这也导致在柱塞腔在配流盘配流当中在配流盘的过渡区将会导致峰值突然巨大变化,随之缸体转速的增加,缸体在配流盘配流口之间的运行时间较短,因此在A、T和B三个口的间隔也会逐渐的减小。
5.3. 不同斜盘变量输出流量压力波动
设定控制角不变,斜盘偏移角为13˚、15˚和17˚,在一个运行周期内,输出流量波动和输出压力波动如下图8和图9所示。
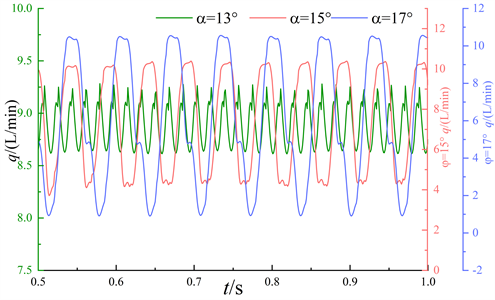
Figure 8. Output flow fluctuation with different swash plate angles
图8. 不同斜盘倾角输出流量波动
控制角保持恒定,不同斜盘倾角下输出流量变化,随着斜盘倾角由17˚降低到13˚,输出流量波动从1.02~10.23 L/min降低到8.64~9.33 L/min,波动范围降低了92.81%,输出的流量增加约63.27%。这表明,减小斜盘倾角可以有效的降低输出流量波动,当流量波动降低时,液压变压器的泄漏量减小,输出流量增加为控制角保持恒定,不同斜盘倾角下输出压力的变化情况。斜盘倾角由17˚降低到13˚,输出压力波动由0.12~70.34 bar降低到46.11~54.24 bar波动范围降低约87%,输出的压力增加约42.85%。这表明,斜盘倾角减小可以降低输出压力波动,产生机械摩擦减小,输出压力增加。
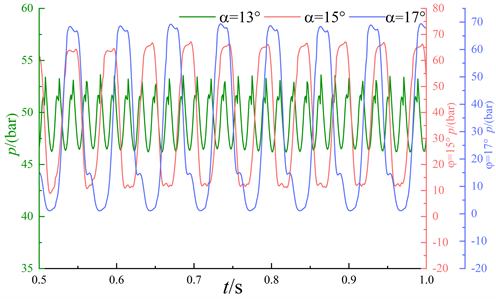
Figure 9. Output pressure fluctuation with different swash plate angles
图9. 不同斜盘倾角输出压力波动
这表明减小压力、流量波动液压变压器可以将系统能量更有效地传输给执行元件,从而提高整个液压系统效率。斜盘倾角改变会对液压变压器流量波动、压力波动和效率产生重要影响。因此,在设计和应用液压变压器时,应该充分考虑斜盘倾角的影响,以达到更好使用性能。
6. 滑靴目标函数建立
滑靴和柱塞作为一个整体绕轴转动,这是由于柱塞内液压油传输的压力作用于滑靴,将滑靴推向在主轴上的斜盘上,缸体的转动主要是由作用到滑靴的反作用力所驱动的,滑靴副随着缸体转动滑靴在斜盘上进行椭圆运动,由于压差存在,油液泄漏以及摩擦副之间产生摩擦,会造成液压变压器容积损失和机械损失,在这两部分损失影响下滑靴副的总效率可以表示为:
(11)
式中:
——容积效率;
——机械效率。
滑靴副容积效率主要受到油液泄漏量影响,其表达式为:
(12)
式中:
——理论流量;V——理论排量;n——理论转速;k——流量损失系数;
——滑靴副泄漏流量。
液压变压器流量损失系数为:
(13)
联立上方式子可得容积效率:
(14)
滑靴副摩擦损失除与柱塞腔内压力、缸体转速、滑靴组件惯性力等工作参数有关,同时与滑靴底部结构参数有密切关系,综合考虑滑靴副摩擦损失对机械效率影响,滑靴副机械效率表达式为:
(15)
式中:
——油液黏性摩擦转矩;
——滑靴副机械摩擦损失转矩;
——液压变压器驱动转矩。
滑靴副油液黏性摩擦转矩表达式为:
(16)
滑靴副机械摩擦损失主要是由于柱塞内液压力和滑靴组件惯性力造成的,机械摩擦转矩损失转矩表达式为:
(17)
驱动转矩为:
(18)
联立上式可得滑靴副机械摩擦转矩为:
(19)
采用粒子群优化算法,对于滑靴底部结构参数进行优化分析,通过建立目标函数,添加约束条件对于优化变量进行迭代更新优化变量。
7. 基于多目标粒子群优化
启发式算法单目标多变量粒子群算法通过模拟群体行为来解决优化问题,把群体当中成员当作粒子,每个粒子会根据自己当前位置和速度以及群体当中最优解位置,及时更新自己位置和速度,整个群体将会快速收敛得到全局最优解。本研究利用单目标多变量粒子群算法解决液压变压器滑靴底部结构参数的选取问题,其原理为:
粒子速度更新原理:
(20)
式中,
——惯性权值;
——粒子的当前速度;
——粒子当前最优值;
——粒子全局最优值;
——粒子的学习因子;
——表示(0 1)之间的随机数。
粒子位置更新原理:
(21)
式中,
——控制速度权重。
算法流程图如下图10所示。
利用MATLAB编写基于单目标多变量粒子群算法的优化程序,程序当中算法数据如表2所示。
启发式粒子群算法性能受到初始解的选择和随机性的影响,为提高算法鲁棒性和避免陷入局部最优,通常多次运行粒子群算法获得更好解质量,本论文通过获得的10个最优解进行比对,如表3所示,最终确定滑靴底部结构参数优化的最优解,粒子群算法所得的最优解集如表4所示,优化后的结构参数对于其容积效率和机械效率有一定程度提高,从而有效改善其滑靴副总效率。
8. 优化前后流量泄漏和摩擦转矩损失
通过粒子群优化算法对于滑靴底部结构参数进行优化,得到上表所示的优化结果,将得到的优化结果带入到建立的AMESim模型当中,得到滑靴副的泄漏量和摩擦转矩损失如下图11和图12所示。
如上图所示,通过修改优化后的滑靴底部结构参数到模型当中运行,滑靴副的泄漏量和摩擦转矩损失有着明显的降低,而且泄漏量和摩擦转矩损失的波峰有着较大的降低,因此优化后的滑靴底部结构尺寸对于滑靴副的泄漏量和摩擦转矩损失的减小有着显著的提高,对于滑靴副的效率有着较大提高。
9. 结论
通过对液压变压器滑靴副的结构进行受力运动分析,建立相关的动力学方程,分析滑靴油膜的受力
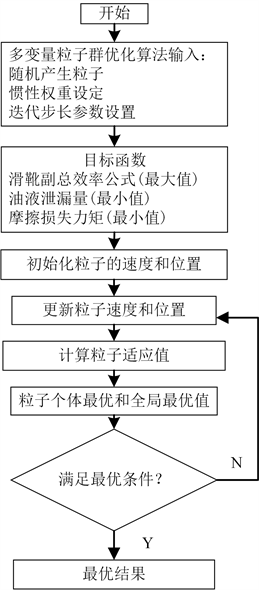
Figure 10. Flowchart of the particle swarm algorithm
图10. 粒子群算法流程图
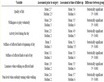
Table 2. Particle swarm algorithm parameters
表2. 粒子群算法参数
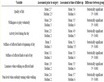
Table 3. Optimization results of particle swarm algorithm
表3. 粒子群算法优化结果表
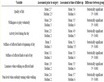
Table 4. Comparison of original and optimized parameters
表4. 原始参数和优化参数对比表
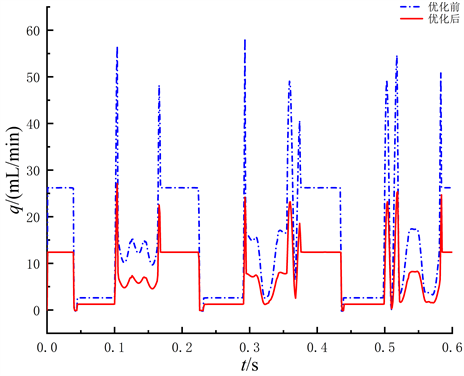
Figure 11. Flow leakage of slipper before and after optimization
图11.优化前后滑靴流量泄漏量

Figure 12. Friction torque loss of the slipper before and after optimization
图12. 优化前后滑靴摩擦转矩损失
特性,建立滑靴副泄漏量和摩擦转矩损失函数,通过粒子群优化算法建立多目标函数,对于滑靴副底部结构参数变量进行优化分析,得到优化后的滑靴底部参数,通过将优化后的结构参数带入进模型当中进行运行,柱塞内泄漏量和摩擦转矩损失波动和泄漏量有着明显的降低,因此优化后的滑靴底部结构对于滑靴副的效率有着较大的提高。说明了对滑靴副进行优化设计,可以有效的降低滑靴副处的泄漏量和摩擦转矩损失,通过对于滑靴副运动特性和受力分析进行研究,为提高滑靴副的效率提供了理论依据。