1. 引言
薄壁件具有重量轻、易成形等特点,因此蒙皮、长桁等薄壁件在飞机结构中得到广泛应用 [1] [2] 。铆接因为连接强度高、紧密性能好和生产成本低等优点,是飞机薄壁件装配的主要连接形式之一 [3] [4] 。然而飞机薄壁件在铆接装配时由于受到铆接力、夹紧力等作用易发生形变,从而会影响飞机的装配准确度。并且由于铆接参数会对薄壁件的铆接变形产生影响,因此需要对薄壁件的铆接变形进行预测和研究铆接参数对薄壁件铆接变形的影响规律。
对于飞机薄壁件的铆接装配,国内外的研究人员都进行了大量研究。韩昊兵等 [5] 为了解决铆钉布置对飞机搭接接头强度的影响问题,基于峰值荷载和线荷载集度的指标,研究了铆接搭接接头的失效模式及机理,并通过响应面法对铆钉布置进行优化设计。Pedram等 [6] 根据田口实验设计,对各种铆接参数组合进行了有限元模拟,研究了铆接力等工艺参数对AA2024型单铆接搭接接头残余应力场和疲劳寿命的影响。Zhang等 [7] 在铝板和钢板上进行了多种自冲铆接顺序和铆接方向的试验,并研究了它们与试件宽度的相互作用。Yu等 [8] 为了预测多铆钉搭接接头的疲劳寿命,建立了考虑循环载荷和残余应力耦合效应的疲劳寿命预测模型,并与Homan模型和实验数据模型进行对比,验证了所提模型的有效性。黄涛等 [9] 为了得到干涉配合铆接镦头尺寸与干涉量的关系,基于塑性成形原理和等体积变形法建立了理论模型,并利用实验以及仿真验证理论模型的正确性。通过以上研究,目前对薄壁件铆接装配的研究都是从宏观角度进行的,将薄壁件表面视为光滑的,然而薄壁件表面在微观下并不是理想光滑的,而是粗糙不平的。而目前对于机械零件粗糙表面的研究,姜英杰等 [10] 为了揭示零件之间的微观接触性能,提出了采用结合三维数字化测量与逆向工程技术建立真实粗糙表面的零件的方法。潘明辉等 [11] 通过实验研究和有限元仿真相结合,根据分形理论模型的自相似性研究薄壁件接触表面微凸体的变化,得到微凸体的变形值与薄壁件变形值变化趋势一致的规律。
薄壁件的铆接装配变形主要包括铆接装配过程中的受力变形和铆接装配后的回弹变形,本文以铆接装配过程中薄壁件的受力变形为研究对象,首先通过分析铆接装配过程建立铆接力学模型,然后基于薄壁件铆接面的实测数据,构建真实形貌表面的薄壁件模型,最后采用有限元仿真方法研究铆接参数对真实形貌薄壁件铆接变形的影响规律。
2. 薄壁件铆接装配力学模型构建
如图1所示为铆接装配过程的三个阶段:a) 是铆钉受到冲头施加的铆接力,钉杆发生弹性变形;b) 是冲头增加位移,钉杆开始发生塑性变形并局部镦粗,钉杆材料填充满铆钉孔间隙;c) 是冲头移至最大位移处,钉杆墩粗直至形成鼓状墩头。

Figure 1. Riveting assembly process: (a) Elastic deformation of the nail bar; (b) Local upsetting of the nail bar; (c) Formation of the pier head
图1. 铆接装配过程:(a) 钉杆弹性形变;(b) 钉杆局部镦粗;(c) 墩头形成
铆接装配过程中,薄壁件因受到钉杆的墩粗对孔壁的挤压和镦头一侧的对上薄壁件的挤压而发生变形,且墩头形成时铆接力达到最大,此时铆钉和薄壁件的变形也是最大,因此需要求得墩头成形的最大铆接力。假定铆钉在镦粗过程中钉杆均匀变形,因此铆钉所受径向应力和铆钉所受环向应力相等。由于镦头侧面为自由表面,因此无外力作用,故镦头端面外侧轴向应力为0,从而可以得到 [12] :
(1)
式(1)中,
为铆钉屈服强度,
为铆钉所受轴向应力,
为铆钉与冲头接触面的摩擦系数,l1为铆钉墩头的直径,
为墩头的高度,x为墩头径向位置坐标。
由Mises屈服条件可知,此时铆钉和冲头接触端面满足:
(2)
对式(1)在
进行积分以及式(2)在
进行积分,然后对结果求和得到最大铆接力的计算公式为:
(3)
从式(3)中可以看出,铆接力的值与铆钉的材料属性,接触面的摩擦系数,镦头的高度和墩头的直径有关。
根据标准墩头尺寸要求:
(4)
式(4)中,d为铆钉孔的直径。联立式(3)和(4),可得到墩头达到标准尺寸所需的最大铆接力值的区间。
铆钉的长度可根据经验公式(5)确定:
(5)
其中,L为铆钉长度,δ为薄壁件总厚度,d1为铆钉直径。
3. 真实形貌薄壁件铆接模型构建
为了构建具有真实形貌特征的薄壁件铆接模型,首先需要获取薄壁件的形貌数据。由于主要考虑铆接装配时薄壁件铆接面的真实形貌对整体变形结果的影响,因此在扫描时中只需要扫描薄壁件铆接面的形貌,而其余表面在构建模型时假定为光滑的表面。薄壁件铆接面使用三维扫描仪进行扫描,如表1所示为薄壁件铆接面的实测数据。
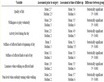
Table 1. Measured data of riveting surfaces of thin-walled parts
表1. 薄壁件铆接面实测数据
然后需要对测得的真实表面数据进行预处理,以保证能够准确的反映薄壁件铆接面的真实形貌,减少后续的分析时间。首先需要对扫描数据进行精简,将误差过大点过滤,最后将处理后的数据保存成点云文件。
最后利用三维建模软件对预处理过的数据进行拟合以实现模型的构建。建模过程中首先要应用CATIA软件对点云数据进行导入生成点云,再对点云进行优化平滑处理,生成粗糙表面,获得的粗糙表面如图2(a)所示。然后将粗糙表面采用创成式外形设计模块操作生成三维实体,获得如图2(b)所示的薄壁件三维实体模型。最后进行装配得到如图2(c)所示的薄壁件铆接装配模型。
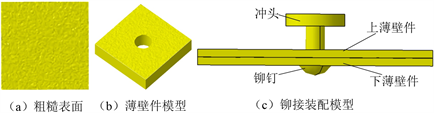
Figure 2. Riveting assembly model of thin-walled parts with real shape features
图2. 真实形貌特征的薄壁件铆接装配模型
4. 仿真分析
4.1. 有限元仿真步骤
为了研究铆接面的真实形貌特征对薄壁件铆接变形的影响,建立作为对比的真实形貌模型和光滑表面模型。薄壁件铆接装配仿真在ANSYS Workenbench软件内显示动力学模块完成。有限元仿真的具体步骤如下:
1) 几何模型创建。根据式(5)确定采用钉杆长度为10 mm,直径为5 mm的铆钉以及外形尺寸为60 mm × 60 mm × 2 mm的薄壁件,薄壁件上铆钉孔的尺寸为5.08 mm,并在CATIA软件内完成三维实体模型的创建。然后将模型导入ANSYS Workenbench软件内。
2) 设置材料属性和接触关系。薄壁件和铆钉的材料分别采用7075铝合金和2A10铝合金,材料具体参数见表2。薄壁件和薄壁件之间、铆钉和冲头之间以及铆钉和薄壁件孔壁之间设置为摩擦接触,摩擦系数设置为0.15。
3) 单元和网格划分。铆接过程中冲头几乎变形,因此将其视为刚体,采用刚性单元,而薄壁件和铆钉采用实体单元。然后进行网格划分,由于变形主要集中在薄壁件铆钉孔周边区域以及铆钉钉杆部分,因此对此区域进行网格细分。
4) 载荷及边界条件设置。限制冲头在x、y方向的自由度,仅在z方向自由。约束两薄壁件四边的自由度,设置铆钉头部固定支承,铆接力作用在冲头,铆接力作用时间为0.005 s,回弹时间为0.002 s。铆接力通过联立铆接力学模型中的公式(3)和(4)确定,求得成形标准铆钉镦头所需的最大铆接力区间为31,354~53,118 N,因此设定该仿真的最大铆接力为36,000 N。
4.2. 仿真结果分析
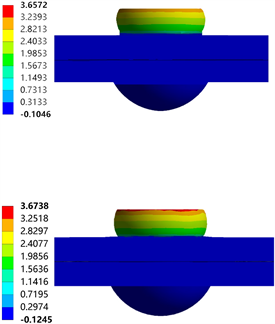
Figure 3. Cloud view of z-direction deformation of riveting model
图3. 铆接模型z向变形云图
铆接装配仿真与理论铆接过程相同,铆钉首先进行弹性变形,然后铆钉发生塑性变形,整体均匀墩粗,直至钉杆与孔壁接触迫使薄壁件发生弹塑性变形。当铆接力撤去,铆钉和薄壁件发生一定量的回弹直至稳定形成最终的墩头,仿真的z向变形仿真结果如图3所示。真实形貌模型和光滑表面模型仿真的铆钉墩头高度分别为2.327 mm和2.321 mm,均符合公式(4)中墩头的标准尺寸要求,且真实形貌模型仿真的铆钉墩头高度与理论力学模型计算值更相符。
在上薄壁件的上表面定义三条预设路径,每条路径选取20个节点,对这些节点在使用三种仿真方法时的变形值进行比较,结果如图4所示。两种仿真模型得到的总变形值变化趋势一致,随着节点越靠近铆钉孔,薄壁件的总变形值越大。而真实形貌模型相比于光滑表面模型的仿真结果,变形值在精度上有了明显的提升。
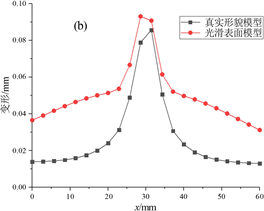
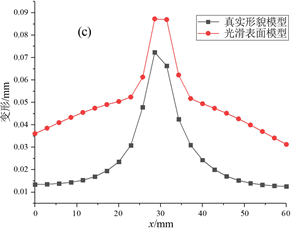
Figure 4. Comparison of the total deformation values of the predetermined paths: (a) Total deformation along line l; (b) Total deformation along line 2; (c) Total deformation along line 3
图4. 预设路径总变形值比较:(a) 沿线l的总变形;(b) 沿线2的总变形;(c) 沿线3的总变形
同时,真实形貌模型和光滑表面模型仿真的薄壁件的最大z向变形分别为0.380 mm和0.337 mm,真实形貌模型的薄壁件z向最大变形结果与光滑表面模型结果相比精度提高了12.7%,证明了考虑铆接面的真实形貌特征的薄壁件铆接装配模型的正确性和提升薄壁件预测精度的有效性。
5. 铆接参数对薄壁件铆接变形的影响
5.1. 铆钉间距对铆接变形的影响
为研究铆钉间距对薄壁件铆接变形的影响,以如图5所示的典型单排三颗铆钉的铆接结构为例,并根据铆接工艺规范选取典型的间距值,分别以真实形貌薄壁件铆接模型构建方法,构建铆钉间距为20 mm、25 mm、30 mm、35 mm、40 mm的5个薄壁件铆接模型,薄壁件的外形尺寸为120 mm × 60 mm × 2 mm,铆钉尺寸与3.1中相同,然后进行有限元仿真,仿真步骤与3.1相同。
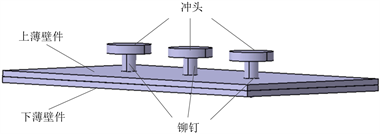
Figure 5. Riveting model of thin-walled parts with three rivets structure
图5. 三钉结构薄壁件铆接模型
如图6所示为不同铆钉间距的铆接装配模型仿真时薄壁件z向变形量。从图7可知,薄壁件的z向变形量与铆钉间距并不是呈现单调关系。当铆钉间距在20~25 mm时,随着铆钉间距增大,薄壁件z向变形量减小;铆钉间距为30 mm时,薄壁件的z向变形量最小;当铆钉间距35~40 mm范围内,随着铆钉间距增大,z向变形量也随之增大。产生上述现象的原因是:在一定距离内,随着铆钉间距的增大,第二、三铆钉的铆接位置越来越远,导致后两颗铆钉产生的z向变形量难以传递至第一铆钉处,超过一定距离时,而由于铆钉之间的距离太远,导致铆钉之间无法起到约束作用。
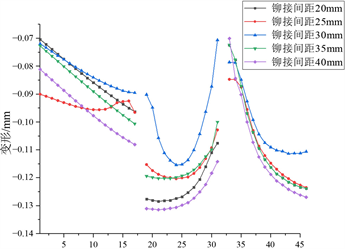
Figure 6. The z-direction deformation of thin-walled parts under different riveting spacings
图6. 不同铆接间距下薄壁件的z向变形
5.2. 铆接顺序对铆接变形的影响
为研究铆接顺序对薄壁件铆接变形的影响,根据5.2中得到最优铆钉间距布置铆钉,仍然以单排三颗铆钉的铆接结构为例。由于1-2-3和3-2-1,1-3-2和3-1-2的铆接顺序结构性对称,而导致铆接变形的结果相似,因此只以1-2-3、1-3-2、2-1-3的铆接顺序进行有限元仿真。
如图7所示为三种铆接顺序的薄壁件z向变形量分布图。由图7可知,三种序列中,1-3-2的铆接顺序下薄壁件的z向变形最小,因为在此顺序下铆接第三颗铆钉时,由于两端已经受到第一颗和第二颗铆钉的约束作用,使得第三颗铆钉引起的变形受到约束作用,因此该铆接顺序下的薄壁件变形量最小。而使用1-2-3铆接顺序进行铆接时,铆钉产生的变形一直会受到一边的约束作用。然而使用2-1-3的铆接顺序进行铆接时,由于第一颗铆钉铆接时受到的约束作用最小,所以薄壁件z向变形量最大,与1-3-2顺序相比较,变形量数值大接近一倍。
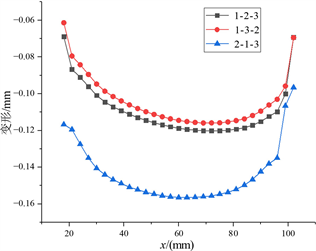
Figure 7. The z-direction deformation of thin-walled parts under different riveting sequences
图7. 不同铆接顺序下薄壁件的z向变形
6. 结论
本文基于薄壁件的实测数据,提出了一种真实形貌薄壁件的铆接模型的构建方法,以及通过有限元仿真研究得到铆接参数对薄壁件铆接变形的影响规律。
1) 通过对比分析,验证了所提的真实形貌模型相较于光滑表面模型可以有效地提高薄壁件铆接变形的预测精度;
2) 铆钉间距对薄壁件铆接变形的影响存在最优值,且铆钉间距过小或者过大都会引起薄壁件的z向变形量增大;
3) 对于单排三颗铆钉的铆接结构,以1-3-2的铆接顺序进行铆接,薄壁件的z向变形量最小。