1. 引言
涡轮叶片磨榫齿是一项精密复杂的工序,在实际磨榫齿时需要频繁调整叶片位姿,目前常用的是通过人为反复垫塞尺的方式进行叶片位姿调整、工装角度找正,这种人为操作的方式效率低而且加工精度也很低 [1] [2] 。
为了提高装夹效率和加工精度,需要研发一个能调节小角度的装置,实现工装角度的可视化快速可调,达到0.1˚调整精度的目标,以取代叶片加工时人工垫塞尺调整工装角度的低效做法。目前有一些类似的研究方法,但都不能满足实际的需求 [3] [4] [5] 。
2. 小角度微调装置系统设计
2.1. 需求分析
涡轮工作叶片材料为镍基高温合金材料,榫齿齿形通常采用枞树型双面榫齿结构,加工难度大。具体流程是叶片安装到夹具上以后,先人工试磨,然后拆下并检测磨出来的面与理论模型的角度差,然后安装回工装上,通过所测的角度差计算得出待垫塞尺的高度,用塞尺垫到夹具底座下面,通过这种反复试磨–垫塞尺的方式调节工装角度。
这种方式有两个问题:一是通过垫塞尺所垫的角度值无法准确判定,需反复垫、磨和测,加工准备时间长;二是垫塞尺流程复杂,需要先把夹具底座抬起,再在下面垫塞尺,而且此时底座方向还会改变,磨出的榫齿位置又会不准确,垫好以后还需要把夹具再固定。按照这样的操作流程,每次垫塞尺和调整的时间基本都在2小时以上,效率低,精度差。为了提高效率和加工精度,亟需一套小角度微调装置,以实现工装的快速布置、快速响应。
对于涡轮叶片磨榫齿的工艺流程,初次磨削后的平面测量角度据统计全部都在±0.5˚以内,因此设计小角度微调装置实现角度调整范围在±0.5˚之内,调节精度达到0.1˚即可满足使用需求。为了让工艺人员实时掌握调整角度的具体值,微调装置还需要有角度显示功能,以将调整角度可视化显示;由于工作台上转台、垫块、夹具、通用安装底板大约重量80公斤,故小角度微调装置的承重需要到100 Kg。综上所述,为了优化现阶段涡轮叶片磨榫齿的加工工艺,亟需设计满足下列功能要求的小角度微调装置:
a) 实现角度微调,调节范围 ≥ ±0.5˚;
b) 调节的精度及分辨率优于等于在0.1˚;
c) 实时角度显示功能;
d) 承载 ≥ 100 KG。
2.2. 方案设计
在确定基础功能和指标需求后,本文采用静压顶升机构实现小角度的微小调整。
1) 液压顶升机构
a) 液压动力源与液路设计
经过对液压原理进行分析,决定采用静压技术的液路结构。通过将动力输入液压缸的腔体与动作液压缸连接导通,在液压线路内通过一个小型回转轴系将动力输入轴的回转运动转换为直线运动,随动力输入轴的回转推动活塞进行往复移动;借由液体基本无法压缩的特性,将动力油缸活塞的往复运动精确传递至动作油缸,完成工作台俯仰角度的精确调整(见图1)。其总体结构如下图所示。
b) 液压顶升锁紧
工作台角度调节后,需要对该角度进行锁紧后加工,加工过程中该角度不能有任何变化,通过对工作台的受力分析,确定锁紧装置应位于回转轴远端,以保证最佳的锁紧状态(见图2)。
经过方案细化,将任意位置的锁紧机构设计为如下图所示结构。通过L型倍增力臂,将T型连接杆推向滑动球座,随力加载完成锁紧,与T型连接杆相接触的2个半球面可顺利的适应工作台俯仰角带来的接触位置变化(见图3),从而保证在任意角度下都可以有效锁紧。
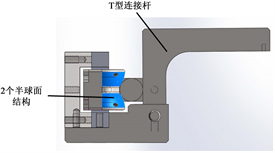
Figure 3. T-bar and hemispherical structure
图3. T型杆和半球面结构
液压顶升机构的精密微调
在本结构尺寸下,若需获取0.1˚的可调精度,则对应顶升液压缸动作0.035 mm。在设计时为了保证装置工作台平稳抬升,使用多顶升缸组的结构特性,进一步进行了比例细分。
当抬升气缸与压力输入缸直径相等时,其动作量比值
基于此,压力缸动作
时,即满足0.1˚角度调整。
液压顶升机构的角度显示和较准
完成操作分辨率的设计后,我们还需要提升数显分辨率到0.1˚。当更换更高分辨率编码器后,即可实现0.1˚以上分辨率调整,最终优选堡盟进口编码器,结合数显表实现0.036˚的分辨率,完全满足车间使用需求。
我们随机将小角度微调装置的角度调整到任意值,并在三坐标测量机上将实测值与编码器数显值进行较准(见表1)。如表1所示,对比结果表明该装置能实现0.1˚以上分辨率的精确调整,满足了涡轮叶片加工的工艺要求。
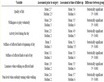
Table 1. Deviation angle accuracy value
表1. 偏角精度值
3. 实验测试
3.1. 承重测试
可视化小角度微调装置的承重要求是100公斤,承重实验时我们将载重加到了120公斤。将微调装置设定到任意角度,在不进行角度锁紧时进行了加载测试(见图4)。微调装置的角度在经过24小时的加载测试后没有变化,此次实验表明微调装置具有很好的承载性能,并且其内部的液压系统工作正常。
3.2. 锁紧可靠性测试
测试锁紧装置的可靠性时,先将微调装置随机调整到某一角度,负载加到120公斤并锁紧工作台,然后去掉底部的液压支撑使工作台完全悬空(见图5),此时所有的重量都加载到角度锁紧机构,随后在微调装置的工作台面上架设千分表,经过24小时的负重测试后,发现千分表示数没有任何变化,说明微调装置的角度锁紧机构工作正常,稳定可靠。
3.3. 零件实际加工测试
利用新研制的可视化小角度微调装置,只调整一次角度,每次不超过半小时,加工9批次零件(见表2),9批次零件的最终加工尺寸100%合格,其中关键尺寸6.5553,8.3947和11.6616的合格率为100%,而且尺寸一致性非常好,同时角度调整效率提高2倍以上!
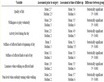
Table 2. Multi batch machining dimension data of turbine blades
表2. 涡轮叶片多批次加工尺寸数据
4. 结论
1) 可视化小角度微调装备的测试结果表明,其能实现工装角度的可视化快速可调,并达到0.1˚调整精度的目标,相比于传统的人工调姿流程效率提高了2倍以上,显著降低了加工准备时间,提高了涡轮叶片的加工效率。
2) 基于静压顶升机构和液压锁紧机构的调姿装备不仅能实现工装角度的快速可调,还能保证调姿精度和产品加工质量的一致性,最终产品的加工质量100%合格,这显著提高了涡轮叶片的机加工质量。