1. 引言
由于驱动桥壳是汽车上较为重要的承载部件之一,许多设计者通常在设计的过程中会用质量冗余来保证其性能。然而,驱动桥壳的质量在汽车的比重较大,所以实现驱动桥壳的轻量化设计对减少汽车的用材消耗具有重要的意义 [1] [2] 。
国内外学者对汽车驱动桥壳的轻量化设计有一定的研究。丁文敏 [3] 对汽车驱动桥壳进行了静力学强度和模态性能分析,并直接采用改变驱动桥壳结构法对驱动桥壳进行优化,提高了其整体性能;吕国坤等 [4] 对某款乘用车的驱动桥壳进行了静力学分析以及静力学下的疲劳分析,并采用直接添加结构法和响应面法进行优化,最终提高了其静态性能并实现了轻量化;刘为等 [5] 对某驱动桥壳在最大垂向力工况下进行了静力学分析以及疲劳寿命计算,并进行了模态分析,最后采用多目标驱动的优化方法对驱动桥壳进行了轻量化优化,并取得了一定的优化效果;俞云云等 [6] 对某重型自卸车驱动桥壳进行了基于有限元的静态研究,并基于响应面优化法使用多目标驱动的方法对其进行了多目标优化,在一定程度上实现了轻量化。以上分析都对驱动桥壳做了一定的分析及优化,但是对于驱动桥壳多工况下综合分析,以及动态特性方面的研究不够深入。
本文通过建立汽车的驱动桥壳的三维模型,对其进行4种常见的工况下的静动态特性分析。基于分析结果,选取设计变量并确定优化目标,进行灵敏度分析,建立响应面并得到Kriging代理模型,采用多目标遗传算法对该模型进行寻优,最终实现在依然满足静动态性能的条件下,实现驱动桥壳的轻量化设计。
2. 驱动桥壳模型参数
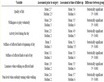
Table 1. Main parameters of the drive axle housing
表1. 驱动桥壳主要参数
本文采用SolidWorks三维建模软件对驱动桥壳的三维模型进行建模。其主要参数如表1所示。
3. 驱动桥壳常见的工况分析
根据车桥设计规范 [7] ,本文将驱动桥壳视为承受车架、车身、悬架等部件的支撑横梁,并探求在特定位置下的最大等效应力和总变形。目前对驱动桥壳的设计和强度校核通常分为4种常见的工况,其分别为:最大垂向力工况,最大牵引力工况,紧急制动工况以及最大横向力工况。
1) 最大垂向力工况
汽车满载并静止在地面上时,若单个后轮受到地面的反作用力为
,后轮重为
,则后车桥板簧受到的垂向力为
,其受力情况如图1(a)所示,此时左右板板簧座间的垂向弯矩
为:
(1)
其中:
为驱动轮的轮距,
为左右板板簧座受载处的中心距离。
2) 最大牵引力工况
在该工况下,驱动桥壳的受力情况如图1(b)所示。此时,汽车在全力加速,驱动桥壳不但要受到垂向力,而且左右后车轮还受到来自地面向前的切向牵引力,并且此时的牵引力为最大,左右板簧的垂向弯矩为:
(2)
其中:
为汽车全力加速时,驱动桥壳的质量转移系数,其取值范围一般取1.1~1.4;其余参数同式(1)。
除此之外,单个驱动轮产生的最大切向反作用力
为:
(3)
其中:
为轮胎对地面的附着系数,通常取0.6~0.9。
为汽车全力加速时,单个后车轮受到地面的垂向反作用力,其计算公式为:
(4)
3) 紧急制动工况
如图1(c)所示,当汽车处于紧急制动时,驱动桥壳不仅要受到垂向力的作用,而且地面会给左右车轮施加切向力,并把切向力传给驱动桥壳。当汽车处于紧急制动状态时,一般是直线行驶,不考虑汽车受到的横向力。并且此时两个后桥车轮在地面上受到的垂向力相等。表示为
,其计算公式为:
(5)
其中:
为汽车制动时的质量转移系数,通常取0.7~1.0。
若用
表示紧急制动时单个后轮所受的切向力,则其计算公式为:
(6)
此外,汽车在紧急制动时,驱动桥壳主体凸缘连接处还受到制动器传输的制动力矩的作用,表示为
,其计算公式为:
(7)
其中:
为车轮的滚动半径。
4) 最大横向力工况
如图1(d)所示,汽车在紧急快速转弯时,在其质心处会产生顺着转弯半径向外的离心力,同时路面会对轮胎产生顺着转弯半径向内的力。当离心力大于轮胎与路面的附着力时,车轮会发生横向滑移,这时作用在车轮上的横向力最大。此时后车轴左车轮受到的垂向反力和横向力分别为:
(8)
(9)
其中:
为后车轴左侧车轮受到来自路面的垂向反力,
为后车轴左侧车轮受到来自路面的侧向反力,
为满载时汽车的质心高度,
为汽车侧滑时后轴左右车轮对路面的附着系数,通常取0.9~1.3。
为后轮轮距。
而后车轴右车轮受到的垂向反力和横向力分别为:
(10)
(11)
其中:
为后车轴右侧车轮受到来自路面的垂直向上的反力,
为后车轴右侧车轮受到来自路面的侧向反力。
通过使用式(8) (10)可以计算出驱动桥壳所受的最大横向力,再用所得的结果通过式(9) (11)可以求出左右驱动轮所受的地面侧向反力。
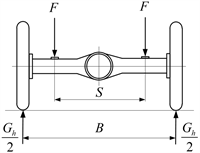
(a) 最大垂向力工况

(b) 最大牵引力工况
(c) 紧急制动工况
(d) 最大横向力工况
Figure 1. Load condition diagram of the drive axle housing
图1. 驱动桥壳受载工况图
汽车在路面行驶时,针对以上的几种常见的工况,驱动桥壳的所承受的载荷通常等效为汽车满载时的2.5倍 [7] 。根据以上驱动桥壳受力分析,得出其约束和加载情况如表2所示。
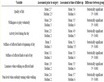
Table 2. Constraints and loads of the drive axle housing under four working conditions
表2. 4种工况下驱动桥壳的约束和载荷
4. 驱动桥壳有限元分析
4.1. 驱动桥壳静力学分析
本文设计的驱动桥壳材料为16 Mn和40 Cr合金钢,具有强度高、寿命长、比较经济等优点,其材料参数如表3所示。
本文使用Solid186三维四面体结构的单元划分网格 [8] 。最终得到网格模型的单元节点数为297,993,网格数量为188,383。
完成材料定义和网格划分后,根据表2对驱动桥壳进行4种不同工况下的约束和加载。提交求解计算后,得到驱动桥壳4种工况下的总变形和等效应力云图,如图2所示。
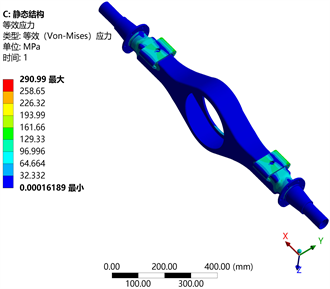
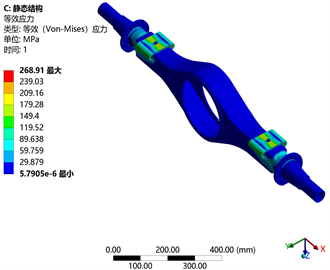
(a) 最大垂向力工况下的等效应力 (b) 最大牵引力工况下的等效应力
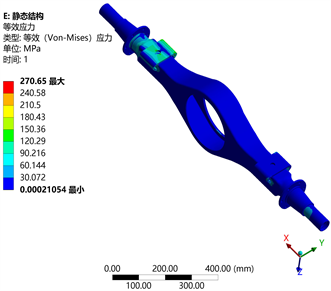
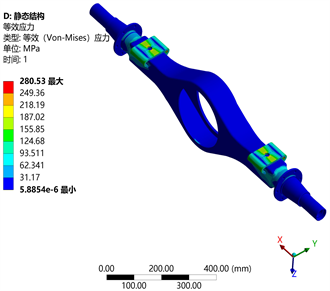
(c) 紧急制动工况下的等效应力 (d) 最大横向力工况下的等效应力
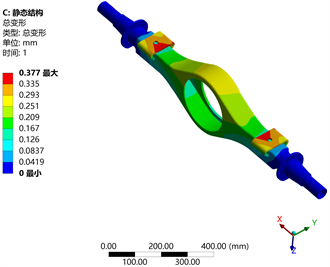
(e) 最大垂向力工况下的总变形 (f) 最大牵引力工况下的总变形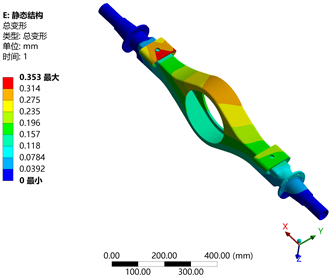
(g) 紧急制动工况下的总变形 (h) 最大横向力工况下的总变形
Figure 2. Statics analysis results of drive axle housing under four working conditions
图2. 驱动桥壳在4种工况下的静力学分析结果
由以上分析,得出4种工况下的驱动桥壳的静力学分析结果如表4所示。
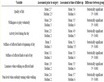
Table 4. Statics analysis results under 4 working conditions
表4. 4种工况下静力学分析结果
从表4可以知,驱动桥壳的最大等效应力出现在最大牵引力工况下,其位置发生在板簧座与桥壳连接处过度半径内侧,其值为290.99 MPa,小于桥壳材料的屈服强度345 MPa,满足强度要求;驱动桥壳的最大总变形出现在最大牵引力工况,其值为0.377 mm,其中最大每米轮距变形量为0.377 mm/1.202 m = 0.313 mm/m,符合《汽车驱动桥台架试验评价指标》(QC/T534-1999)要求小于1.5 mm/m的标准 [9] 。
由以上分析知,驱动桥壳在4种常见的工况下满足静态性能要求。
4.2. 驱动桥壳模态分析
模态分析的目的是探索驱动桥壳的固有频率特性。本文研究的是驱动桥壳的约束模态,无载荷因素,仅设置约束条件,约束条件为固定桥壳的半轴两端 [10] 。
通过提交模态求解,获取驱动桥壳的前六阶的模态振型图,如图3所示。
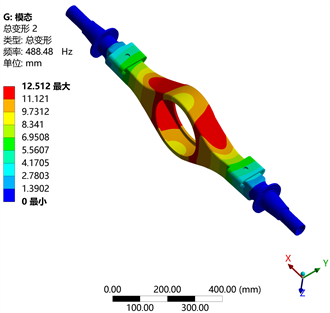
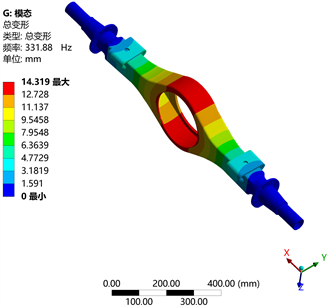
(a) 第一阶 (b) 第二阶
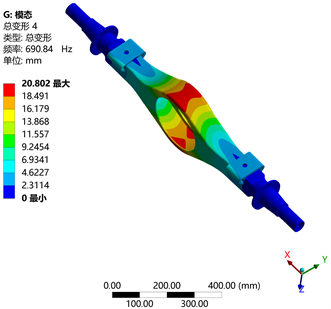
(c) 第三阶 (d) 第四阶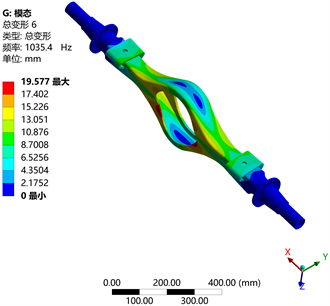
(e) 第五阶 (f) 第六阶
Figure 3. The first six modal shapes of the drive axle housing
图3. 驱动桥壳前六阶模态振型
其前六阶固有频率和振动状况如表5所示。
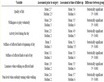
Table 5. First six natural frequencies and vibration conditions
表5. 前六阶固有频率及振动状况
在汽车行驶的路面状况中,由路面凹凸不平所发出的激励振动频率范围通常在0~50 Hz之间 [10] ,远小于驱动桥壳的一阶固有频率331.88 Hz,所以驱动桥壳在结构尺寸方面有很大的优化空间,以提高其静动态性能。
4.3. 驱动桥壳谐响应分析
谐响应分析是分析几何结构和不同频率的简谐加载下的动力响应,载荷频率变化的范围要给定出来,其通常与模态的分析的固有频率有关 [11] 。
本节使用模态叠加法进行驱动桥壳的谐响应分析,研究对象为左右板簧座,选取最大牵引力工况下的载荷,以单位简谐力的形式加载于左右板簧座,选择其频率范围为模态最高阶固有频率的1/1.5,即为0~690 Hz。进行谐响应求解后,得到左右板簧座的X、Y、Z方向的位移频谱如图4所示。从图4可以看出,左右板簧座X、Y、Z方向的位移响应曲线分别在487 Hz,329 Hz,487 Hz处出现峰值,且都为最大值,分别为3.21 mm,4.49 mm,6.87 mm。
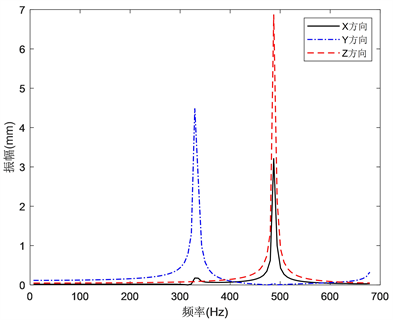
Figure 4. Displacement spectrum of left and right spring seats in three directions
图4. 左右板簧座三个方向的位移频谱
由以上分析知,左右板簧座在329 Hz、487 Hz频率激励下会产生共振,因此汽车在行驶时应避免该振动频率。两个共振频率激励下左右板簧座的总变形如图5所示。

(a) 左右板簧座在329 Hz激励下的总变形 (b) 左右板簧座在487 Hz激励下的总变形
Figure 5. Total deformation of the drive axle housing under resonance frequency excitation
图5. 驱动桥壳在共振频率激励下的总变形
5. 驱动桥壳轻量化设计
响应曲面设计法,简称响应面法(RSM),是一种结合试验设计原理和统计学的经验模型优化方法 [12] 。
5.1. 选取设计变量
驱动桥壳主要由壳体、板簧座和半轴组成,整个驱动桥壳为连续结构。考虑到设计变量的数量过多会增加计算量。所以本文选取与以上分析结果影响较大的5个设计变量,如图6所示。并根据驱动桥壳的设计标准,给出其5个设计变量的原始值以及取值范围如表6所示。
1-壳体2-板簧座3-半轴P1-板簧座与板簧安装孔尺寸P2-板簧座厚度 P3-板簧座宽度P4-板簧座与桥壳连接处过度半径P5-桥壳厚度。
Figure 6. Design variables for the drive axle housing
图6. 驱动桥壳设计变量
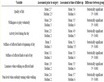
Table 6. Original values and value ranges of design variables
表6. 设计变量原始值及取值范围
5.2. 试验设计与参数灵敏度分析
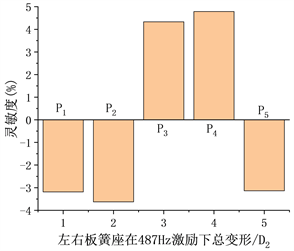
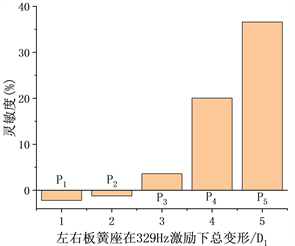
(a) 左右板簧座在329 Hz激励下总变形灵敏度图 (b) 左右板簧座在487 Hz激励下总变形灵敏度图
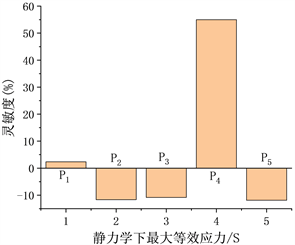
(c) 一阶固有频率灵敏度图 (d) 静力学下最大等效应力灵敏度图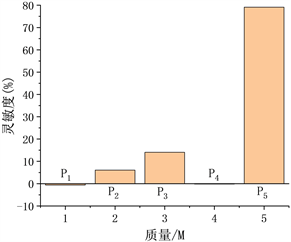
(e) 静力学下最大总变形灵敏度图 (f) 质量灵敏度图
Figure 7. Sensitivity analysis
图7. 灵敏度分析图
本文选用ANSYS Workbench的响应面优化模块中的拉丁超立方体抽样法对驱动桥壳设计变量进行试验设计,抽取试验样本总数为100个 [13] 。并且选取在原始条件下,左右板簧座分别在共振频率329 Hz和487 Hz激励下的总变形D1和D2、一阶固有频率f、静力学分析下的最大等效应力S、总变形D和质量M为目标函数。在进行完试验设计后,要进行参数灵敏度分析,以去除对目标函数影响效果不明显的设计变量。灵敏度分析如图7所示。
从以上结果分析可知,5个设计变量均对6个目标函数有显著影响,故这5个参数都要作为优化参数。其中,P4、P5对D1影响较大;P2、P5对D2影响较大;P1、P4对f影响较大;P2、P4对S影响较大;P4、P5对D影响较大;P3、P5对M影响较大。故响应面分析应该重点研究影响较大的两个设计变量对各自目标函数影响。
5.3. 响应面分析及代理模型的建立
根据以上试验结果,生成响应面并得到Kriging代理模型 [14] 。其中输入与输出参数间的响应面关系如图8。
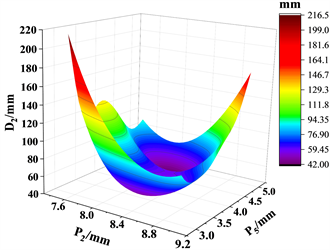
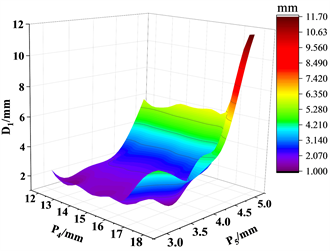
(a) P4,P5——左右板簧座在329 Hz激励下总变形/D1 (b) P2,P5——左右板簧座在487 Hz激励下总变形/D2
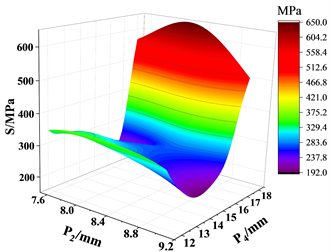
(c) P1,P4——一阶固有频率/f (d) P2,P4——静力学下最大等效应力/S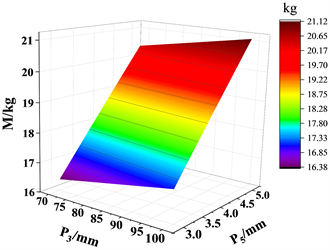
(e)P4,P5——静力学下最大总变形/D (f) P3,P5——质量/M
Figure 8. Response surface diagram of target variables and corresponding design variables
图8. 目标函数与对应设计变量的响应面图
5.4. 基于遗传算法的驱动桥壳优化
本文采用多目标遗传算法(NSGA-II)。
对驱动桥壳结构进行优化 [15] 。该优化算法的模型包括三个要素:设计变量、目标函数,以及约束条件。由于桥壳质量的降低会引起强度和刚度性能下降,所以,以桥壳质量M最小化为优化目标的前提下,同时要求左右板簧座分别在共振频率329 Hz和487 Hz激励下的总变形D1和D2最小化,一阶固有频率f最大化,静力学分析下的最大等效应力S和总变形D最小化,从而保证静动态性能依然满足设计要求。驱动桥壳的参数优化的数学模型为:
(12)
约束条件为:
(13)
其中:
为5个尺寸设计变量,其下限取值为
;上限取值为
,
为6个目标函数。
采用多目标遗传算法对桥壳的Kriging代理模型进行求解寻优,求解后得到一些列Pareto解集,再从这些解集中选取出3组候选方案,如表7所示。
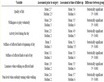
Table 7. Candidate points and verification candidate points
表7. 候选点及验证候选点
5.5. 优化结果圆整
由表7所给出的候选点,根据输出参数要求在其中进行筛选,本文筛选候选点1作为优化结果,并考虑到加工精度的要求,对该组设计变量进行圆整,圆整后结果如表8所示。
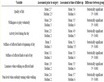
Table 8. Optimization of design variables and rounding results
表8. 设计变量优化并圆整后结果
根据表8的整理后的设计变量,重新在三维模型设计软件中修改设计变量参数,再导入ANSYS Workbench对应的模块中进行分析,得到最终的优化结果如表9。
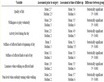
Table 9. Optimization results of objective variables
表9. 目标函数优化结果
由表9可知,对驱动桥壳进行优化后,驱动桥壳的总质量M从20.5 kg下降到18.22 kg,减少了11.1%,轻量化效果较为显著,并且优化后的其他各项静动态性能值均符合要求。
6. 结论
针对某汽车驱动桥壳进行结构建模和多工况下的静动态特性分析,并基于遗传算法对驱动桥壳进行了轻量化设计。结果如下:
1) 静力学分析结果显示,最大等效应力发生在最大牵引力工况,其位置发生在板簧座与桥壳连接处过度半径内侧,其值小于材料屈服强度,满足强度需求。
2) 模态分析和谐响应分析得出,驱动桥壳动态性能良好,不会发生低阶共振,也不会因路面激励发生共振。
3) 在强度及刚度等性能均满足的前提下,使用多目标遗传算法将桥壳质量减小了11.1%,满足设计要求。