1. 选取几何模型
首先找到一个几何模型如图1所示,然后根据轴承结构 [1] 的型号,确定模型的尺寸如图2所示,其总高度为100 mm。
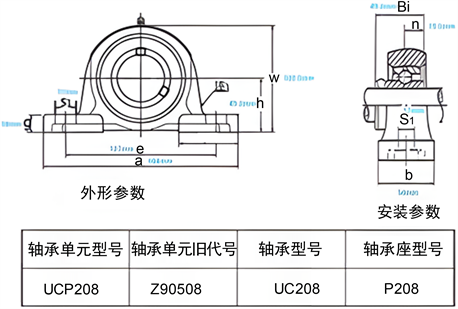
Figure 2. Bearing appearance and parameters
图2. 轴承外型及参数
2. 建立模型
使用UG对这个轴承结构进行建模,为了后续的工作做准备,如图3所示:
3. 网格划分
在划分网格的时候,要先定义单元类型,然后定义材料的属性和单元的尺寸,然后用计算机自动划分。首先将建好的几何模型导入有限元分析软件中,选择Geometry-Import Geometry。
3.1. 定义材料属性
定义材料属性,Q345本次分析类型为弹塑性结构分析,需要定义结构的弹性模量、泊松比以及密度,具体参数数值见下图4。
3.2. 导入材料
将我们定义好的材料属性导入到我们要分析的模型里面:如右图5、图6所示,导入Q345。
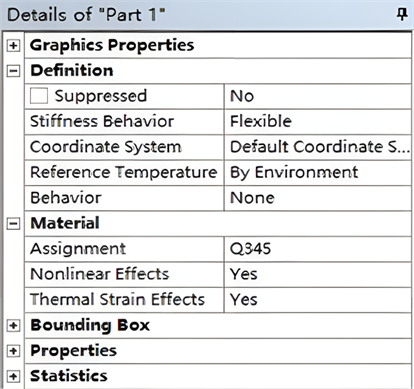
Figure 5. Material property setting diagram
图5. 材料属性设置图

Figure 6. Material attribute import diagram
图6. 材料属性导入图
3.3. 设置单元尺寸
如下图7所示设置单元尺寸为5 mm。
开始进行网格划分:
进行网格划分,首先定义网格相关度为50,定义划分质量为Medium,定义划分方法为自动网格划分形式,具体示意图如下。
因为轴承结构模型比较规则,在进行网格划分时,可以选择六面体形式的网格进行划分,划分如下图8和图9所示。
网格尺寸对结构分析结果的准确性有很大的影响:尺寸过大会导致结构分析结果不准确,尺寸过小会导致每次的计算分析时间较长。
如下图10所示,通过网格统计信息可以看到,该模型节点数量为40,200个,总单元数量为23,292个。
4. 约束及载荷施加
施加约束:底部固定,所以把底部固定住,螺栓孔固定即可,如图11所示:
施加载荷:本次分析情形为静强度分析,主要目的是在于验证整个结构在承受以下载荷的情况下,轴承结构是否能够安全运行。垂向荷载:35,000 N。具体约束和加载情形如下图12所示,与实际情形相符。
5. 查看结果
5.1. 结构变形结果
所有前处理设置完成之后就可以对模型查看结果。计算完成之后我们选择查看模型的等效应力(Equivalent Stress)云图和总的变形量(Total Deformation)云图,首先查看轴承结构的变形结果。通过位移云图13可以看出,结构的最大位移为9.351e−003 mm,发生在轴承结构的中间位置,与实际情形比较相符。在轴承结构的其他位置,结构变形很小,位移云图以蓝色和绿色为主。
整体结构的最大位移较小,并不会影响结构的正常运行,因此结构在此荷载工况下,能够安全稳定运行。
5.2. 结构应力结果
计算完成之后我们查看模型的等效应力(Equivalent Stress)云图。通过查看结构应力云图14可以看出,结构最大Mises应力为67.524 Mpa,发生在轴承结构的边缘位置,此数值远低于材料的屈服强度,因此结构足够安全。
在轴承结构的其他位置,应力云图以蓝色和绿色分布为主,大部分区域的Mises应力都比较小,说明承受上述载荷的工况下,结构能够正常运行,不会发生破坏。
6. 轴承结构的六阶模态分析
模态分析是研究结构动力特征一种近代方法,是系统辨别方法在工程振动领域中的应用。模态是机械结构的固有振动特征,每一个模态具有特定的固有频率、阻尼比和模态振型。这些模态参数可以由计算或试验分析取得,这样一个计算或试验分析过程称为模态分析。这个分析过程如果是由有限元计算的方法取得的,则称为计算模态分析;如果通过试验将采集的系统输入与输出信号经过参数识别获得模态参数,称为试验模态分析。通常,模态分析都是指试验模态分析 [2] 。
轴承结构对于整个运转体系起到承上启下的作用,同时,该结构的自然振动频率不能与驱动电机激励频率相互接近,避免发生共振。
为了研究轴承结构的振动频率特征 [3] ,这里对轴承结构单独进行了模态分析,取分析阶数为6阶。
前6阶的频率数值以及各阶的振型云图如图15所示。
如下图16所示为一阶模态分析。
如下图17所示为二阶模态分析。
如下图18所示为三阶模态分析。
如下图19所示为四阶模态分析。
如下图20所示为五阶模态分析。
如下图21所示为六阶模态分析。
7. 谐响应分析
谐响应分析用于确定线性结构在承受随时间按正弦(简谐)规律变化的荷载时的稳态响应,分析过程中只计算结构的稳态受迫振动,不考虑激振开始时的瞬态振动,谐响应分析的目的在于计算出结构在几种频率下的响应值(通常为位移)对频率的曲线,从而使设计人员能预测结构的持续性动力特征,验证设计是否能克服共振、疲劳以及其他受迫振动引起的有害效果。
谐响应分析可采用完全法,缩减法,模态叠加法求解。当然,视谐响应分析为瞬态动力学分析的特例,将简谐载荷定义为时间历程的载荷函数,采用瞬态动力学分析的全套方法求解也是可以的,但需要花费较长的计算时间。
谐响应需要选取一个特定的面来表示出应力与变形随着频率的变化而变化的关系,选取的面应该有大的变形能较为明显的体现出力的变化的关系,所以我们选择滑动轴承的地面作为响应面 [4] 。如图22所示:
选取1000~4000 HZ,进行分析:谐响应分析形变图如下图23:
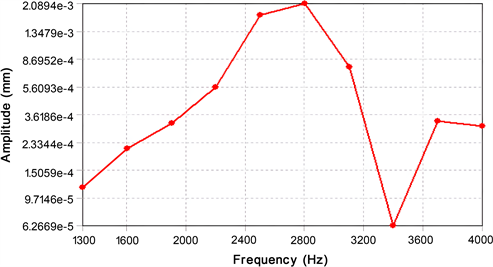
Figure 23. 1000~4000 HZ Harmonic response diagram
图23. 1000~4000 HZ谐响应图
结论:根据我们得到的上图,我们可以清晰的看到当频率为2800 HZ时形变和应力最大,为了进一步的确定我们的结论,下面我们进行不同频率区间上的不同坐标轴之间的对比分析。
当频率为1300~1700 HZ时,这个频率段远离2800 HZ,在这个区间内的X轴方向上的应力图和应变图如下图所示:
(1) 在1300~1700 HZ x轴上应力变化如下图24所示:

Figure 24. 1300~1700 HZ x-axis stress variation diagram
图24. 1300~1700 HZ x轴应力变化图
(2) 在2600~3000 HZ x轴上应力变化如下图25所示:

Figure 25. 2600~3000 HZ x-axis stress variation diagram
图25. 2600~3000 HZ x轴应力变化图
(3) 在1300~1700 HZ y轴上应力变化如下图26所示:
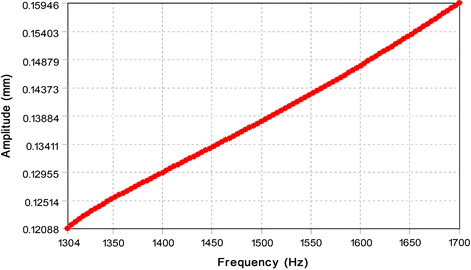
Figure 26. 1300~1700 HZ y-axis stress variation diagram
图26. 1300~1700 HZ y轴应力变化图
(4) 在2600~3000 HZ y轴上应力变化如下图27所示:
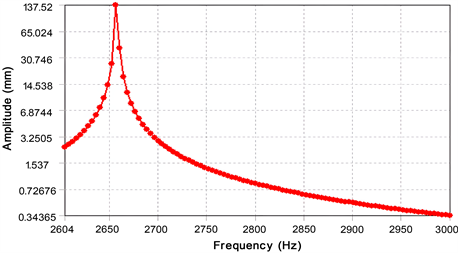
Figure 27. 2600~3000 HZ y-axis stress variation diagram
图27. 2600~3000 HZ y轴应力变化图
(5) 在1300~1700 HZ z轴上应力变化如下图28所示:
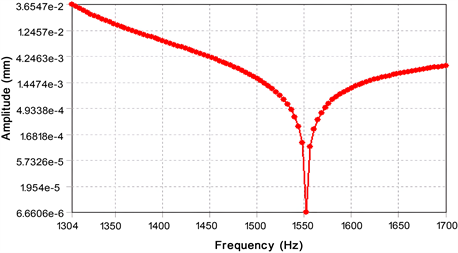
Figure 28. 1300~1700 HZ y-axis stress variation diagram
图28. 1300~1700 HZ y轴应力变化图
(6) 在2600~3000 HZ z轴上应力变化如下图29所示:
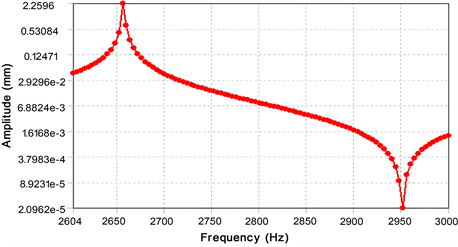
Figure 29. 2600~3000 HZ y-axis stress variation diagram
图29. 2600~3000 HZ y轴应力变化图
8. 结论
根据我们对于轴承结构的谐响应分析,不难看出在2800 HZ的时候共振最严重,造成的形变和应力最大。所以我们在使用的时候一定要注意尽量避开共振的频率。