1. 引言
冷喷涂技术自20世纪80年代诞生以来,因其独特的沉积机理而受到广泛关注 [1] 。相比热喷涂,冷喷涂可避免材料在沉积过程中的氧化、再结晶等问题,可沉积温度敏感材料,在新材料开发与先进制造领域展现出巨大应用潜力 [2] 。经过几十年的发展,冷喷涂技术已经成功应用于航空航天、汽车、能源、生物医学等领域。
冷喷涂可以分为低压冷喷涂(LPCS)和高压冷喷涂(HPCS)两类,低压冷喷涂通常≤1 Mpa,高压冷喷涂通常>1 Mpa,甚至达到100 Mpa,大部分的金属和合金都可以使用高压冷喷涂系统进行沉积 [3] 。与高压冷喷涂相比,低压冷喷涂具有易携带以及低成本的优势。高压冷喷涂的高沉积效率(高达90%以上),在喷涂过程中很难精确的控制沉积形状,甚至于太快的沉积导致与喷枪的很容易相撞,因此偶尔适度低的沉积效率可以使冷喷涂在增材制造技术(Addictive Manufactory)领域发挥更大的优势 [4] 。
而在增材制造技术当中,制造精度很大程度上取决于空间分辨率这一关键参数。对于选择性激光熔融(SLM)技术,其空间分辨率是由激光束的尺寸和粉末的粒度决定 [5] 。对于冷喷涂的空间分辨率则取决于喷涂点的尺寸和形状,与喷嘴的出口直径密切相关,典型的冷喷涂的喷涂尺寸在5~10 mm [6] ,但却难以满足某些高精度以及复杂的制造任务。为缩小冷喷涂的喷涂点尺寸,目前主要有两种研究思路。一是采用外部辅助装置,如在基板上的上方使用一个遮罩,使大部分颗粒无法到达基板上,从而改变沉积层的几何形状 [7] 。但这中方法会造成大量的浪费,也不适用于增材制造。另一思路是通过优化喷嘴结构自身来减小喷嘴出口的气流直径。R.Lupo和W.O’Neil的研究当中 [8] ,可以通过设计特殊的粉末喷射器来控制喷涂点的尺寸大小的可能性。X.K.Suo, T.K.Liu等研究发现喷嘴出口气流湍流强度会影响颗粒分布 [9] 。Zaikovskii等提出特殊外形喷嘴可以改变气流射流尺寸,从而影响喷涂点大小 [10] 。特别值得一提的是,A.Sova等通过将Laval喷嘴缩小到喉部直径0.5 mm、出口直径1 mm,实现了宽度仅1 mm的细小喷涂点 [11] 。在后续研究中,Sova和Smurov使用该微型喷嘴沉积铝粉末,喷涂点直径可控制在1.7~1.8 mm以内,但涂层密度和结合强度较差,表明微型喷嘴仍需进一步优化 [12] 。除Laval喷嘴外,收敛–筒型和收敛–发散–筒型喷嘴也常用于冷喷涂。但收敛–发散喷嘴不适合低压条件,低压时难以实现良好的颗粒虹吸 [13] [14] 。因此,低压冷喷涂多采用收敛–发散–筒型喷嘴,且进粉位置对虹吸效应至关重要 [15] 。综上所述,喷嘴结构优化是减小冷喷涂喷嘴的关键所在,但现有研究多停留在理论探讨或仅适用于高压条件,鲜有系统研究不同喷嘴参数对低压冷喷涂沉积质量的影响。此外,针对CDB (convergent-divergent-barrel)喷嘴几何结构优化以改善低压冷喷涂性能的研究也较少,这可作为未来研究的重点方向。
因此,本研究拟采用数值模拟与实验相结合的方法,研究低压冷喷涂中常用的收缩–发散–直筒型喷嘴的几何结构参数对气流场和颗粒动力学的影响规律,实现对喷嘴结构的优化设计,以期获得更高精度的微细喷涂,为进一步提升低压冷喷涂的质量提供理论指导。
2. 数值仿真和实验
2.1. 数值仿真过程
数值仿真的模型是使用商业软件Fluent (Ver 21.1)建立的,通过该软件模拟冷喷涂过程中喷嘴的内外流场的情况,同时也计算颗粒了的加速行为与特性。由于不研究中模型的不对称特性以及模拟的准确性,建立了喷嘴完整的三维模型,计算区域如图1所示。将气体流动的预热室设置为压力入口,压力值设为0.7 MPa,温度为773 K,将粉末注射管上端的出口面以及自由射流的区域的边界设置为压力出口,其大小为0.1 Mpa,温度为室温喷嘴的出口面设置为内部流场,其他涉及到的面均设置为标准壁面进行仿真计算。粉末颗粒通过压力出口的出口1注入喷嘴内部,初始的速度设置为0 m/s,方向是Y轴的反方向。而在真实的实验当中,粉末的注入管的长度接近2 m,如果采用真实情况建模,这样长的区域会占用巨大的计算资源,而得到的结果相差不大,为了简化计算,只考虑了很短的一段长度,简化后的粉末注入管如图所示。壁面条件设置为不可移动以及绝热的,采用标准壁面函数进行近壁处理,这对广泛的壁边界流动相当有效 [16] 。
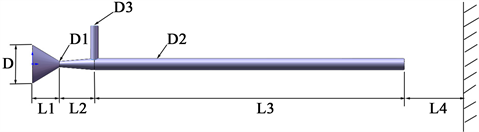
Figure 1. Schematic diagram of computational domain
图1. 计算区域示意图
喷嘴模型网格是由蜂窝–六面体状网格划分组成,如图2所示。最大网格尺寸设置为0.3 mm,最小尺寸网格设置为0.05 mm。采用膨胀层网格对边界层进行网格划分并对喷嘴出口处网格进行加密处理,如图2所示。总体的网格数量是880,000以上,检查了网格密度无关的计算结果。对比了约440,000、1,000,000和15,000,000的网格数量的结果,发现在440,000网格的情况下,由于网格的质量差,计算无法达到收敛,而在其余两种数量下的网格尺度下,与880,000网格数量的结果没有明显的差异。
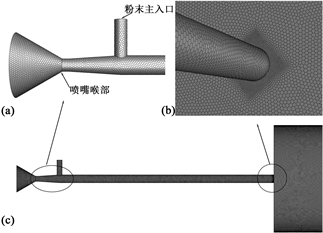
Figure 2. Schematic diagram of polyhedral meshing strategy for computational domain. (a) Nozzle and powder feeder pipe, (b) Nozzle exit surface and (c) Barrel part and exit region
图2. 计算域的多面体网格策略示意图。(a) 喷嘴和送粉管,(b) 喷嘴出口表面,以及(c) 筒体部分和出口区域
采用可压缩空气作为驱动气体,设置为理想且可压缩的,空气比热容Cp为1006.43 j/kgK,气体的分子质量是28.966。基于上述假设,雷诺平均一般守恒形式的连续性、动量和能量守恒方程被用于包括和解释流场中湍流的影响,并写成方程(1)~(3)。显然,标准的k-ε模型不适合这个从粉末进料点虹吸气流的3D问题。Realizable k-ε模型不考虑低雷诺数粘度,例如壁附近的流动。湍流涡流的精度是整个仿真过程中需要考虑的重要因素,故在喷嘴内部的气体流动的使用的是由Yakhot等人 [17] 以及Ounis等人 [18] 提出的(RNG) k-ε模型进行计算预测,如方程中的(4)~(5)所示,这个湍流模型能准确的模拟出流场中高速以及低速流动区域。
质量:
(1)
动量:
(2)
能量:
(3)
湍流能量:
(4)
湍流耗散能:
(5)
可压缩流动过程,描述理想气体状态方程是:
(6)
k是k方程系数,
是湍流耗散能系数,
是有效粘度系数,系数
,
和
分别是能量方程k和
方程的有效普朗特倒数,S是平均速度应变率张量系数,常数
,
和
的值分别是0.085,1.42,1.68。
在本次仿真中采用的是铝颗粒,密度为2.7 g/cm3,分子质量是87 g/mol,颗粒的直径设置为20 μm,颗粒的加载率0.5 g/s,使用Fluent中DPM离散相模型来计算颗粒的加速过程以及分布情况,由于冷喷涂中颗粒体积在气体体积中占比很小,可以视为稀释流,故不考虑颗粒对气体的影响。颗粒的阻力模型选择软件中默认的Spherical模型,为了考虑湍流效应引起的粒子分散,启用了随机跟踪型模型,在这种情况下,使用离散随机游动(DRW)模型来预测粒子速度的波动分量 [19] 。
2.2. 仿真中涉及的参数
采用密度基求解器进行模拟计算。对入口,出口1,以及出口在每一次计算中进行质量流量的监测。在达到收敛标准时,或者两个监测点处的质量流量彼此相等,计算停止。库朗数设置为2,松弛因子在需要的情况下可适当的调整。
在低压冷喷涂条件下,为了CDB喷嘴中喉部直径,收缩短段长度,以及粉末注入角度对气体流动,颗粒加速行为以及涂层性能的影响,预热室压力入口的压力设置为0.8 Mpa,温度为773 K,喉部直径的值分别是1.5,1.8,2.0 mm。收缩段的值分别是5,7,9,11,13 mm。直筒段的值分别选取:60,70,80,90,100,110,120 mm。粉末注射角度则选取30,45,60,75,90度,其余所涉及到的参数如表1所示。
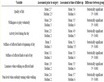
Table 1. Summary of nozzle geometric parameters
表1. 喷嘴几何结构的参数
2.3. 实验过程
根据仿真所得到的结果,分别加工出三种不同喉部直径的喷嘴,至于喷嘴入口直径,收缩段长度,粉末入口直径,发散段长度,直筒段长度都相同,且分别为10 mm、2 mm、7 mm、9 mm、80 mm,喷嘴的材质采用黄铜,使用黄铜喷嘴可以使颗粒温度达到一个高值,然而颗粒温度越高,颗粒临界速度降低,从而提高沉积效率。如图3所示,实验中所用到的低压冷喷涂设备由北京天诚宇新材料技术有限公司生产。使用Q235钢作为喷涂的基底,使用线切割方法得到基板样本,并依次用编号为280和600的砂纸打磨。使用铝粉末作为喷涂颗粒,大小在10~50 μm之间。采用压缩空气作为驱动气体,在预热室腔的压力为0.8 Mpa和773 K,使用可压缩空气作为工作气体,喷嘴出口到基板的距离为20 mm。在获得铝涂层样品后,首先采用线切割法得到涂层截面。然后,使用自动金相抛光机对涂层截面进行抛光处理,以确保表面平整而不产生划痕。抛光完成后,使用氢氧化钠标准溶液对铝涂层横截面进行蚀刻,以清晰显露铝合金基体和沉积颗粒的界面。最后,使用光学显微镜在适当倍数下观察涂层的微观结构,观察颗粒变形情况。
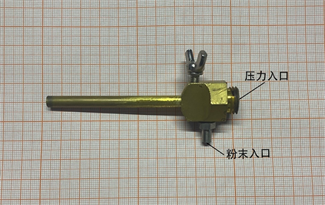
Figure 3. Convergent-divergent-barrel nozzle
图3. 收敛–发散–直筒型喷嘴
3. 结果与分析
3.1. 数值仿真结果及分析
3.1.1. 喉部直径对颗粒速度和温度的影响
图4显示不同喉部直径在入口压力为0.8 Mpa,温度为773 K下喷嘴内的气体压力与速度变化。从图中可知三种不同喉部直径喷嘴内气体速度在发散段的末端达到最大,其中喉部直径为1.5 mm的气体速度最高达到了接近1000 m/s,但随后速度开始急剧下降到350 m/s,但喉部直径为1.8 mm和2.0 mm的喷嘴内的速度变化显然不同,气体从发散段到直筒段,速度并未急剧的下降,而是以大约为850 m/s速度保持一段距离,而后开始急剧下降,其后三种类型喷嘴内速度变化类似,先缓慢上升,在喷嘴出口外速度出现震荡,随后速度下降至零,压力变化则相反。造成这一现象的原因是,较大的喉部直径可以通过更多的气流,可以使气体得到膨胀的时间加长,因此,气体能维持较高速度的距离较长,喷嘴在出口处形成了冲击波,这是因为,对于CDB喷嘴,直筒段的高压气体急剧膨胀到大气中。
(a)
(b)
Figure 4. (a) Gas pressure variation along the centerline; (b) Gas velocity variation along the centerline
图4. (a) 喷嘴内气压沿中心轴线的变化;(b) 喷嘴内速度沿中心轴线的变化
图5显示了不同喉部直径在对颗粒冲击速度和温度的影响,清晰的显示了,随着喉部直径增加,颗粒的速度是显著提升的,而温度则是相反,尤其当喉部直径从1.5 mm变化到1.8 mm的时候,颗粒的冲击速度增加尤为迅速。而根据以往的数据可知,铝颗粒的临界速度相对较高,故喉部直径为1.5 mm可能很难形成有效的沉积,造成该种现象的原因,是不同喉部直径喷嘴内气体速度变化的结果,喉部直径较大的喷嘴直筒段内的气体速度达到了一个相对较高的值,且保持了一段距离,而喉部直径较小的喷嘴只有相对较短的距离气体的速度是达到一个高值,故颗粒在喷嘴内得不到没有经过较高的气体速度充分加速,从而颗粒的冲击速度相对较低。因此,在设计低压冷喷涂喷嘴时,由于所使用气体的压力多数在1 Mpa以内,喷嘴的喉部直径是一个关键的参数,应当选取相对较大的喉部直径。
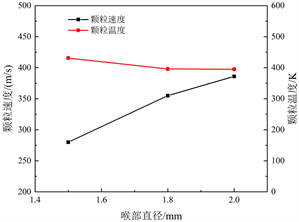
Figure 5. Effect of throat diameter on particle velocity and temperature
图5. 喉部直对颗粒速度和温度的影响
3.1.2. 喷嘴发散段长度和直筒长度对颗粒速度和温度的影响
图6显示了喷嘴扩散段长度对颗粒速度和温度的影响。清晰的展示了,随着发散段长度的增加,颗粒的冲击速度先迅速上升热而后略有下降,其中在发散段长度为11 mm的时候达到了一个峰值,这与传统的拉法尔喷嘴的发散段长度增加导致颗粒速度变化趋势现象相类似。这个结果说明,在CDB喷嘴中,设计合适的发散段长度能显著的提高颗粒的冲击速度。此外还可发现,温度的变化趋势则与颗粒冲击速度变化趋势相反。
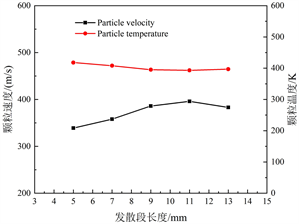
Figure 6. Effect of convergent length on particle velocity and temperature
图6. 发散段长度对颗粒速度和温度的影响
图7展示了喷嘴直筒长度对颗粒速度和温度的影响,随着直筒长度的增加,颗粒的速度先随之增加,颗粒速度在直筒长度为80 mm的时候达到最高,而后出现下降的趋势。这是因为,采用的CDB型喷嘴,喷嘴的发散段长度相对较短,气体在喷嘴内发生膨胀的距离相对较短,直筒内只有一段距离使气体达到了很高的速度,而后一段距离的气体速度相对较低,随着直筒长度的增加,从仿真结果的速度云图中可看到,速度较快的一段的距离并未增加,而增加气体速度相对较低的那一部分,因此颗粒得不到充分加速,反而使颗粒的速度降低了。此外,颗粒的温度随着直筒长度的增加而增加。
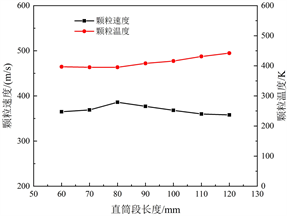
Figure 7. Effect of barrel length on particle velocity and temperature
图7. 直筒段长度对颗粒速度和温度的影响
3.1.3. 粉末注入角度对颗粒速度和温度的影响
图8显示了不同粉末注入角度对颗粒的冲击速度和温度的影响。从图中可以清晰看出,随着粉末注入角度的增加,颗粒冲击速度略有上升,但当注入角度超过60˚后,颗粒冲击速度变化不大,基本保持稳定。这说明在低压冷喷涂条件下,粉末的注入角度对颗粒最终获致的速度影响相对较小。因此,采用低压冷喷涂时,可以直接选择径向垂直的注入方式,而不必过分考虑注入角度的调节。之所以出现这种现象,主要是由于低压冷喷涂采用虹吸效应将粉末吸入喷嘴,不同于高压条件下的机械加压方式。在虹吸效应下,气流在喷嘴收缩段会形成负压区,产生强大的吸力作用在粉末上,粉末被气流吸入喷嘴内部。此时粉末所获得的轴向动量主要来源于喷嘴内部气流,而非注入时的初始动量。因此,只要粉末能够顺利进入喷嘴收缩段,其初始注入角度对最终冲击速度的影响不大。
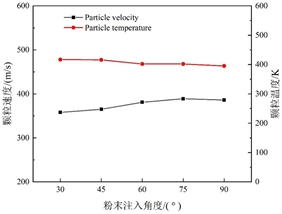
Figure 8. Effect of injection angle on particle velocity and temperature
图8. 粉末注入角度对颗粒速度和温度的影响
综上所述,采用低压冷喷涂技术时,可以直接选择简单的粉末径向垂直注入方式,而不必考虑调节注入角度,从而简化了系统的设计和操作,这也是低压冷喷涂采用虹吸供粉的一个优势所在。
3.2. 实验结果及分析
在上述低压冷喷涂条件下,对不同喉部直径喷嘴进行了单点喷涂试验如图9所示。结果发现,当喉部直径为1.5 mm时,无法形成有效的涂层,原因是颗粒速度过低。而喉部直径为1.8 mm的喷嘴能生成涂层,但表面存在大量凹坑,使用细度范围为10~50 μm的铝粉末,该喷嘴仅能使部分细小颗粒达到临界速度。当喉部直径增大至2.0 mm时,涂层质量明显改善,呈圆锥形,但直径达到5 mm,大于喷嘴出口直径3 mm。分析原因可能为喷嘴直筒段末端压力较大,气体剧烈膨胀增加颗粒分散以及粉末与喷管内壁碰撞造成散射现象。图10是使用光学显微镜在200倍放大下观察铝涂层截面的微观结构显示,由于喉部直径为1.5 mm的喷嘴无法形成有效涂层,故无法对其进行观测。可以清晰的观察到,喉部直径为2.0 mm的喷嘴得到的涂层得到明显的改善,其孔隙率低于喉部直径1.8 mm的涂层。这是由于2.0 mm喷嘴沉积的颗粒直径分布范围更广,能使更多粒子获得足够的加速达到较高冲击速度。这一实验结果验证了数值仿真的预测,即喉部直径越大,高速气流区越长,颗粒获得更充分的加速,最终获得更高的冲击速度和更好的沉积质量。本研究表明,选择合适的喉部直径是优化低压冷喷涂沉积质量的关键。
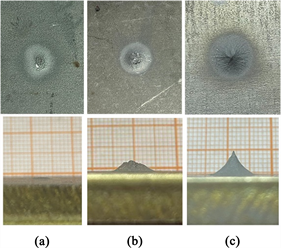
Figure 9. Coatings of CDB nozzle with different throat diameters. (a) 1.5 mm, (b) 1.8 mm, (c) 2.0 mm
图9. 不同喉部直径收敛–发散–直筒喷嘴的喷涂结果。(a) 1.5 mm,(b) 1.8 mm,(c) 2.0 mm
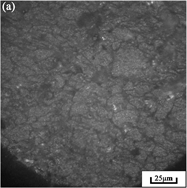
Figure 10. OM microstructures of the cross-section of Al coating deposited using different throat diameters of CDB nozzle. (a) 1.8 mm, (b) 2.0 mm
图10. 光学显微镜下使用不同喉部直径CDB喷嘴沉积的铝颗粒的微观组织。(a) 1.8 mm,(b) 2.0 mm
4. 结论
基于数值仿真和实验结果可以得出,对于喉部直径较小的收缩–发散–直筒型喷嘴,影响颗粒速度的最关键参数是喉部直径。喉部直径越大,可以产生越高的颗粒速度。此外,合适的发散段长度和直筒段长度也可以显著提高颗粒速度,需要进行优化选择,粉末的注入角度越小,颗粒的冲击速度越小,但角度超过60度以后,对颗粒的冲击速度影响不大。实验验证结果表明,喉部直径不应小于1.8 mm,否则无法形成有效的涂层。综合数值仿真和实验结果,本文实现了对低压冷喷涂喷嘴几何参数的优化设计,这为进一步提高低压冷喷涂的精度和质量提供了理论指导。但喷嘴设计仍然存在一定局限性,实验得到的涂层结果并不符合预期设想,后续工作将考虑采用特殊形状喷嘴以及更小粒径颗粒等方法,以期获得更高精度的微细喷涂。
基金项目
工信部2021年产业技术基础公共服务平台项目(2021-0174-1-1)。