1. 引言
某含硫集输管线气液混输,输送介质包括未经处理的原料气和为气田水,日输气量15万方,日输水量大于200方,运行温度40℃~70℃,CO2含量为1.739%,H2S含量为0.563%,气田水为弱酸性,pH值为6.55,矿化度118.429 g/L,Ca2+浓度2470 mg/L,Na+浓度33,331 mg/L,Cl−浓度30,000~90,000 mg/L,水型为氯化钙水型。管线为L360QS无缝钢管,规D219 × 7.1-1.2 km,管线腐蚀穿孔形貌如图1、图2所示,穿孔部位位于管线6点钟方向焊缝位置,正处于焊缝区域,管线外部无明显腐蚀现象,是由内向外发生腐蚀穿孔。
为找出管线腐蚀穿孔的原因,对失效管段进行了一系列分析及检验,以期此类事故不再发生 [1] 。
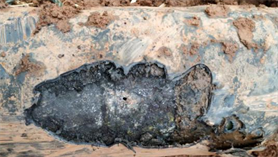
Figure 1. Macro morphology of corroded pipeline
图1. 腐蚀管线宏观形貌
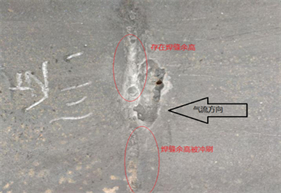
Figure 2. Macroscopic morphology of corrosion perforation
图2. 腐蚀穿孔处的宏观形貌
2. 腐蚀环境分析
2.1. 管线服役工况条件模拟计算
该管线高程走势如图3所示。本次穿孔位置位于760 m~818 m之间,属于爬坡段。
通过pipephase软件,模拟管线内液相、气相流动状态,模拟计算管线内流体流态。计算出管线内液相流速0.89 m/s,雷诺数为44,719,根据相应标准分类,管线内流体流态为湍流。
一般来说层流时,由于流体的粘度,在沿管道截面有一种稳态的速度分布;湍流时,破坏了这种稳态速度分布,这不仅加速了腐蚀介质的供应和腐蚀产物的迁移,而且在流体与金属之间产生切应力,能剥离腐蚀产物,从而加大了冲蚀速度。
即在该管线服役条件下:运行温度40~70℃,Cl−浓度较大,77,000 mg/L,气田水呈弱酸性,H2S浓度0.563%,CO2浓度1.739%,各腐蚀影响因素都处于较敏感区域,管线内流体流态为湍流,加大了冲刷应力,腐蚀环境恶劣 [2] [3] 。
2.2. 管线腐蚀监/检测结果

Figure 4. The straight front end of the upper elbow of the pipe behind the separator in the upstream well station of the pipeline
图4. 管线上游井站分离器后汇管上弯头前端直管段
对管线上游井站分离器后汇管上弯头前端直管段开展内腐蚀扫描成像检测,以焊缝下游12 cm,管线12点处为起点,焊缝上游25 cm、管线6点种位置为终点开始扫描,扫描面积40 cm × 35 cm。结果如图4所示,结果显明:管线焊缝上游下部(易受流体冲刷、积液部位)减薄量明显高于顶部。减薄位置最严重部位出现在焊缝前2 cm。即管线底部减薄较明显,尤其是在焊缝上游附近位置。
3. 理化检测
3.1. 化学成分
采用ARL 4460直读光谱仪对管线基体、焊缝部位区域进行化学成分分析。检测结果见表1。结果表明:腐蚀管线的化学成分符合标准要求。
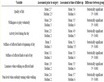
Table 1. Chemical composition analysis of corroded pipe
表1. 腐蚀管线化学成分分析结果
3.2. 力学性能测试
拉伸试验在室温下进行,采用12.7 × 50 mm全壁厚纵向板状拉伸试样;冲击试验温度为20℃,采用10 × 10 × 55 mm横向试样,三个试样为一组进行试验。硬度试样为横向1/6圆全壁厚试样。试验结果见表2,结果表明:管线基体、焊缝部位样品材料力学性能(拉伸、冲击、硬度)指标符合标准要求。
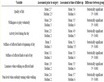
Table 2. Chemical composition analysis of corroded pipe
表2. 腐蚀管线化学成分分析结果
3.3. 非金属夹杂物评级
在管线基体、焊缝部位发生均匀腐蚀区域切取样品进行金相显微组织观察和非金属夹杂物评级,结果如图5、图6所示,结果见下表3。
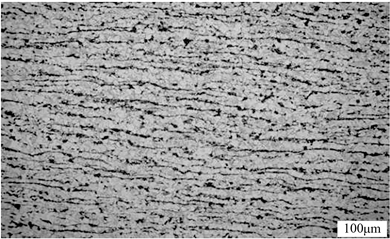
Figure 5. Metallographic observation of matrix parts
图5. 基体部位金相观察
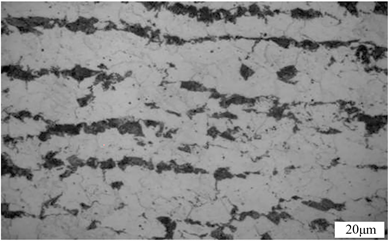
Figure 6. Metallographic observation of weld parts
图6. 焊缝部位金相观察
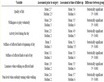
Table 3. The results of rating of non-metallic inclusions
表3. 非金属夹杂物评级结果
标准未对管线中非金属夹杂物级别进行要求,但应尽量将非金属夹杂物控制在较低级别。
3.4. 腐蚀产物分析
采用TESCAN VEGA II扫描电子显微镜及其附带的XFORD INCA350能谱分析仪(EDS)对腐蚀穿孔区域表面与截面的腐蚀产物进行物相分析,见图7~图11、表4。试样表面覆盖了一层腐蚀产物层。腐蚀产物层结构疏松,其横截面上密布孔洞,出现了破裂。表面腐蚀产物层主要以Fe、S、C、O等元素为主,基体主要以Fe、C、O为主,同时含有少量焊接材质Mn、Mo、Cr、Si等组成。

Figure 7. Surface scanning electron microscopy of corrosion site
图7. 腐蚀部位表面扫描电镜

Figure 8. Scanning electron microscopy of corrosion site section 1
图8. 腐蚀部位截面1扫描电镜
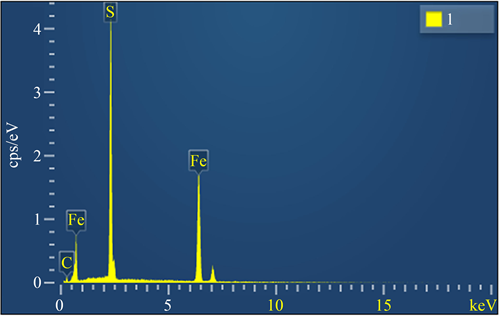
Figure 9. Spectrum analysis of corrosion site section 1
图9. 腐蚀部位截面1能谱分析
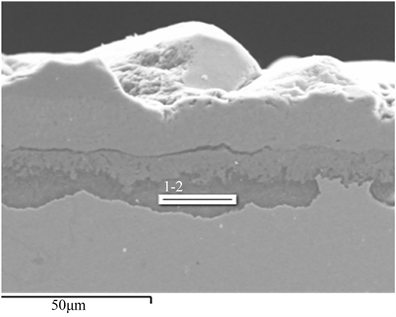
Figure 10. Scanning electron microscopy of corrosion site section 2
图10. 腐蚀部位截面2扫描电镜
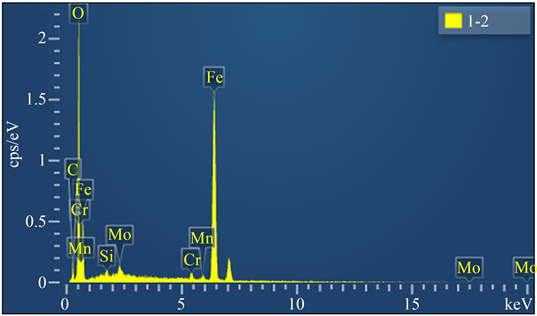
Figure 11. Spectrum analysis of corrosion site section 2
图11. 腐蚀部位截面2能谱分析
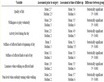
Table 4. The results of energy spectrum analysis of corrosion site
表4. 腐蚀部位能谱分析结果
3.5. 焊缝检测
截取一段腐蚀坑周边未被冲刷掉的焊缝余高、打磨后通过体式显微镜放大观察,见图12、图13,发现焊缝表面存在部分气孔缺陷,气孔存在会影响焊缝承载能力,若气孔贯穿了焊缝表面,介质进入孔穴内,若介质具有腐蚀性时,将形成集中腐蚀,孔穴逐渐变深、变大,以致腐蚀穿孔而泄露。

Figure 13. The welding seam sampling site was observed under the type microscope
图13. 焊缝取样部位体式显微镜观察
4. 分析与讨论
对于输送湿气的管线而言,内腐蚀是导致管线失效的主要形式 [4] ,而焊缝是整条管线的薄弱环节,由于焊接操作和自身性能特点的原因,在服役过程常常会先于管体发生腐蚀破坏,造成失效,影响生产 [5] [6] 。
基于以上分析及检测结果,该管线腐蚀穿孔原因总结为以下几个方面。
1) 该管线在服役条件下,内壁形成酸性腐蚀环境,各腐蚀影响因素都处于较敏感区域,该条件下易发生H2S电化学腐蚀。
2) 输送管线底部腐蚀性流体形成的湍流对金属表面有较强的冲刷作用,特别在焊缝余高部位,余高影响了流体在此处的流态,使流体对此部位冲刷应力迅速增加,金属表面受到的冲击作用越强,湍流更激烈,冲刷作用也越强。在未被冲刷掉的焊缝余高前端金属表面反复冲刷磨损,破坏金属表面保护膜,同时加速腐蚀介质与金属直接接触,加速了电化学腐蚀,形成较大的冲刷腐蚀坑。
3) 根据检测焊缝中存在部分气孔缺陷,当焊缝余高被冲刷,形成腐蚀坑以及气孔暴露时,腐蚀介质进入孔穴内后,形成集中腐蚀。孔内金属阳离子不断增加,其水解作用导致氢离子活度增加,即发生酸化作用,pH值降低。为了维持腐蚀坑内溶液的电中性,外部的阴离子将向坑内迁移,尤其是腐蚀介质中的Cl-将优先扩散到腐蚀坑内部,造成坑内溶液的化学和电化学状态和坑外溶液不同。此处,pH值较低,氯离子浓度较高,从而使与之相接触的金属的电极电位低于外部溶液中金属的电极电位,造成腐蚀坑内反应加剧,加速了腐蚀穿孔。
此管线服役条件下,电化学与冲刷腐蚀共同作用相互促进,是一种自带催化效应的严重腐蚀,两者相互协同作用远大于作用之和,再加上此段焊缝本身存在气孔缺陷以及流体中的腐蚀介质性质进一步加速了腐蚀穿孔。
5. 结论与建议
5.1. 结论
1) 该管线化学成分、力学性能、金相组织、晶粒度和非金属夹杂物均满足GB 9711.3-2011《石油天然气工业输送钢管交货技术条件第3部分:C级钢管》要求,但焊缝发现有少量气孔缺陷;
2) 现场管线壁厚减薄与电化学腐蚀集中在距焊缝上游20 cm,管线4~7点部位;
3) 此管线腐蚀穿孔直接原因是水存在条件下H2S电化学腐蚀与管线内流体湍流对焊缝周边冲刷腐蚀的协同作用,间接原因为焊缝存在少量气孔缺陷促进了腐蚀过程加速。
5.2. 建议
1) 针对该管线及采气工艺类似管线,一是对施工期间焊缝质量进行复片,重点查看管线底部(4点~7点)附近有无缺陷;二是开挖检测时,重点在焊缝部位多开挖几个探坑,以检测管体腐蚀情况。
2) 针对该管线及采气工艺类似管线,一是采取控制管线输水量,由气液混输调整为气液分输,降低流体对管线的冲刷腐蚀及腐蚀介质与管线内壁金属直接接触几率;二是完善管线缓蚀剂防腐工艺,如:建立清管预膜装置,定期开展缓蚀剂预膜,降低或避免管线内壁发生H2S电化学腐蚀;或者使用具有优良耐磨性能的内腐蚀技术 [7] ,如:内涂层管线等。