1. 引言
星用SAW滤波器应用在卫星测控、通信、数传等分系统的转发器、接收机、应答机电路中,对信号进行滤波处理,抑制电子信息设备高次谐波、镜像信息、发射漏泄信号以及各类寄生杂波干扰 [1] 。
目前我国卫星用声表面波滤波器大部分是插针封装形式,插针封装形式存在以下不足之处:体积大、不便于多层板安装布线,占用了卫星上较多的空间和负载资源。相比较而言,表贴封装更有利于系统的小型化、轻薄化和集成化。欧空局(ESA)和美国国家航空航天局(NASA)已确认表贴声表面波滤波器满足星用环境使用要求,并获得了实践证实。因此大力发展国产表贴星用高频声表面波滤波器、提高表贴星用高频声表面波滤波器的可靠性等任务已迫在眉睫。
电子元器件的可靠性又是整个航天产品可靠性的基础。由于航天产品不具有可维修性,电子元器件的失效很可能会导致整个航天产品的失效。多年来,金属封装的SAW滤波器在航天产品上已有大量应用,设计、工艺相对成熟,表贴高频SAW器件封装结构有了较大的改变,必须对制作工艺进行相应的调整。
我单位与中国空间技术研究院微波电子元器件可靠性中心在提高小型化表贴产品可靠性方面共同进行了摸索,对生产工艺进行了改进,满足航天产品对星用高频表贴SAW滤波器的要求。
2. 星用SAW滤波器可靠性要求
由于星用高频表贴SAW器件的应用环境比较特殊,需要器件能够承受高强度机械应力、热应力、射线辐射应力、环境应力等苛刻的环境条件。
星用SAW滤波器可靠性要求主要依据航天五院CAST采购规范,具体要求主要包括:
工作温度范围:−55℃~85℃。
贮存温度范围:−55℃~125℃。
按照GJB548B进行温度循环、PIND、机械冲击、随机振动、高温寿命、气密性检测、三温测试等一系列筛选试验及质量一致性试验。
此外,还应进行粘接/剪切强度、内部目检、扫描电镜检查、键合拉力检测、内部水汽含量测试等一系列DPA试验。
内部水汽含量:≤5000 ppm。
3. 高可靠SAW滤波器的工艺制作
3.1. 原材料的选择
星用高频表贴SAW器件的关键原材料包括:外壳、基片、键合丝、粘接胶等。
在外壳方面,选择结构强度、膨胀系数、环境稳定性方面满足星用要求的小尺寸陶瓷表面贴装气密封装外壳(如图1所示):

Figure 1. Schematic diagram of SMD package
图1. 表贴外壳示意图
SAW器件基片材料选用压电单晶基片,如铌酸锂、钽酸锂等,星用高频SAW器件频率普遍达到1 GHz以上,最细线宽达到亚微米,必须采用步进投影曝光机进行光刻,对基片表面平整度、翘曲度和表面缺陷(划痕、凹凸不平等)提出了更高的要求(划痕典型情况如图2所示)。在基片采购技术协议中,LTV (局部厚度偏差)、PLTV (局部厚度偏差率)、FPD (焦平面偏差)成为必须进行规定的指标。

Figure 2. Schematic diagram of substrate surface failure (10×)
图2. 基片表面不合格示意图(10×)
键合丝要具有一定的机械强度,一般选用硅铝丝(含硅1%),焊点及尾丝控制满足GJB548B-2005中的要求,焊点的宽度为压焊丝直径的1.5~5倍,长度为压焊丝直径的0.5~3倍,合适的焊点及尾丝如图3所示;星用表贴高频器件普遍使用小尺寸(<5 × 5 mm2)管壳,芯片尺寸达到1 × 1 mm2以下,压焊区版图设计空间有限,25 μm规格的硅铝丝将逐步取代50 μm规格的硅铝丝。
粘接胶要能够满足粘接/剪切强度的要求,膨胀系数与芯片、管壳匹配,同时其成分稳定,在150℃高温下水汽释放量小,能够经受一定强度的辐射而不发生特性变化。此外,表贴产品普遍采用再流焊接方式进行装配,在进行再流焊后,粘接强度衰减量应在可控范围内。

Figure 3. SEM of pressure welding wire tail wire
图3. 压焊丝尾丝SEM
3.2. 工艺流程概述
星用高频表贴SAW滤波器的制作工艺流程采用微细加工的平面工艺,具体流程包括:
基片清洗→镀膜→光刻→钝化→划片→粘片→键合→内部目检→测试→封装→标识→筛选→包装入库。
其中前道工艺(含光刻、镀膜等)制作芯片图形,主要实现器件的电参数性能;后道的封测工艺(含划片、粘片、键合、封装、标识等)主要保证器件的可靠性。本文主要针对后道封测工序过程中的工艺流程进行说明。
4. 提高器件可靠性采取的工艺措施实例
星用高频表贴器件需要满足GJB548C-2021中对器件内部目检的要求,主要包括:控制芯片崩边、键合丝的拱高、芯片内部多余物等,同时器件的外观也需要满足外部目检的要求。
4.1. 控制划片造成的芯片崩边
划片的方式主要有:机械切割和激光切割,机械切割又分为砂轮划片和金刚刀划片两种。
对三种划片方式各项指标比较(见表1)。
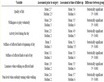
Table 1. Comparison of three scoring methods
表1. 三种划片方式比较
星用SAW器件对芯片崩边要求控制在40 μm以下,由于高频表贴产品芯片尺寸更小,相应的划片街区间距大幅度减小(达到1 mm以下),原有金刚刀划片工艺已不适用,为满足星用产品要求,采用砂轮划片的方式,砂轮划片效率高、质量好(合格率 > 97%),便于和自动贴片机配合。砂轮划片机的精度一般很高,转动轴在160 mm行程范围内误差 < 5 μm,刀高控制精度达到0.1 μm,90˚旋转误差 < 15。
4.1.1. 砂轮划片刀的选择
砂轮划片刀是影响划片的主要影响因素,根据SAW器件基片为硬脆材料的特点,选用与其匹配的金刚砂颗粒度较小、结合强度稍低的树脂类刀片。
4.1.2. 划片工艺参数优化
对划切道宽度及边沿崩边大小的主要因素是:主轴转速、划切速度、划切深度、刀片冷却量及冷却方式。主轴转速高,划切速度慢,划切道宽度大,崩边小;划切速度快,划切道宽度小,崩边大;划切深度小,冷却水流量适中,则划切宽度小、崩边小。此外,刀架端面精度直接影响划片质量。
为有效的降低崩边尺寸,采用了提高主轴转速、降低进刀速度的方案,同时,对划片刀修调周期进行了规定 [2] 。
通过优选划片刀及进行划片工艺试验,确定主轴转速为30000 rpm,进刀速度3 mm/s。
工艺优化前后的崩边尺寸对比如图4、图5所示。

Figure 4. Edge chipping diagram of grinding wheel before optimization (100×, maximum edge collapse 106 μm)
图4. 优化前砂轮划片崩边图(100×,最大崩边106 μm)

Figure 5. Edge chipping diagram of grinding wheel after optimization (100×, maximum edge collapse 15 μm)
图5. 优化后砂轮划片崩边图(100×,最大崩边15 μm)
4.2. 粘接胶可靠性验证
对声表器件而言粘接胶的要求包括:在机械性能方面要有较好的抗拉、抗剪、抗压、抗弯强度及适宜的硬度;在物理性能方面,要有良好的耐热、耐湿、耐溶剂、耐高低温冲击等性能,并且有合适的热膨胀系数,高的绝缘性;此外,还必须在高温和低气压下,没有挥发物出现;还要有良好的吸声效果等。粘合剂主要分为室温固化、热固化、光固化。其中热固化(室温固化)粘合剂主要成分为环氧树脂或硅橡胶,光固化的粘合剂主要成分为丙烯酸酯。其中环氧树脂有优异的物理、机械和电气性能级良好的吸声效果,固化过程无副产物生成,固化后的收缩率在热固化树脂中为最小(<2%),有较低的吸水率(0.5%)。硅橡胶粘接材料的具有良好的高低温性能(−200℃~200℃)、电气性能、防潮性能。
表贴声表面波滤波器的外壳为陶瓷表贴外壳,适合进行再流焊,对该产品采用的压电芯片和有机粘接胶是否能够承受再流焊温度进行验证。分别采用现有的环氧粘接材料A和硅橡胶粘接材料B,经过再流焊后粘接强度和再流焊前粘接强度进行数据对比,确定表贴器件经过再流焊后对其粘接强度的影响。采用的再流焊工艺包括:
1)进炉温度96℃,预热160℃/140 s,焊接:235℃/70 s,最高显示温度235℃。
2)进炉温度99℃,预热160℃/140 s,焊接:245℃/70 s,最高显示温度245℃。
试验结果如下表2所示:
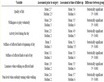
Table 2. Comparison of bonding strength of devices after reflow soldering
表2. 再流焊后器件粘接强度对比
从以上数据可以看出,经过再流焊后其粘接强度平均值均略有减小,但是最小值无明显变化,所有样品都符合器件粘接强度要求且有较大余量(最小值均为合格判据的2.5~4倍)。
4.3. 控制压焊丝的弧度及排布
引线键合应具有较低的接触电阻,合适的机械强度,长期的金相稳定性和小的寄生参量,常用方法有热压键合、超声键合、热超声键合。由于声表器件的压电基片以铝为主,而铝丝超声键合工艺具有不需加热,Al-Al系统不易受腐蚀,有好的可靠性,成本低等优点,因此超声键合是声表器件键合技术的首选。功率、时间、压力是超声键合的关键控制参数,相互关联,应根据铝丝直径和被焊接面的材料性质及表面状态、劈刀类型等进行调整。
压焊丝要有一定的弧度,引线过长会倒丝、塌丝,造成短路;引线过直,温度变化时,引线受热应力作用,会降低焊点可靠性。
为保证星用高频表贴SAW器件带外抑制特性,采用了特殊的引线设计方式,将两个地电极放置在芯片中心位置,进行电气互联时,压焊丝跨过换能器将地电极与管座接地焊盘相连。
由于小型化表贴外壳(<5 × 5 mm2)内空间有限,为避免压焊丝与盖板接触,需要控制压焊丝拱高,但带来的问题是压焊丝接近焊点的部位与芯片夹角过小,压焊丝与芯片图形距离不满足GJB548B要求,导致内部目检不合格(如图6所示)。

Figure 6. The arc of the welding wire is too low
图6. 压焊丝弧度过低
为解决此问题,采取了如下措施:
1) 调整压焊电极的位置,增大电极面积,延长压焊时焊点与换能器的距离,保证压焊丝的弧度、压焊丝与跨接区的距离以满足内部目检的要求(如图7所示)。
2) 在芯片表面制作钝化层,进一步提高器件的可靠性。

Figure 7. The physical image after pressure welding optimization
图7. 压焊修正后实物图
4.4. 平行缝焊工艺控制
在封装过程中通常要求:芯片的温度不得超过允许值,管壳内不能有金属微屑,不得释放有害气体或杂质,封装应在净化和低湿度的环境中进行,封装要有良好气密封。平行封焊是利用脉冲大电流通过盖板和底座焊环间高阻点所产生的热量,把盖板和焊环相接触的一个小区域熔接起来。由于焊轮作匀速直接滚动运动,而焊接脉冲电流不断产生,在盖板边缘形成两条平行的、由重叠的焊点组成的连续焊接。平行封焊是通过自动送料、自动对准、自动封焊、自动传送来完成器件的平行封焊。平行封焊具有洁净、高可靠、高强度等特点。由于在封装是对管壳热冲击很小,非常适宜于高频声表面波器件片式封装。
表贴声表面波滤波器向小型化高可靠方向发展,在进行平行封焊工艺技术攻关时需综合考虑气密性和水汽含量要求,由于器件小,对封焊工艺参数的控制存在一定难度。
平行缝焊主要的参数是放电功率(电流),放电周期(时间),焊接速度,放电延迟距离等 [3] 。放电功率过大,放电周期过短,焊接速度过慢,放电延迟距离过短会导致焊接热量过大,盖板与管壳焊缝处有烧蚀痕迹,拐角处过焊严重(如图8所示)。

Figure 8. The physical image of unqualified welding appearance
图8. 焊接外观不合格实物图
为了解决此类问题,通过减小封焊功率及放电时间,增加焊接延迟距离,加快封焊速度,降低热冲击对外壳的影响,得到较为良好的封焊外观,如下图9所示:

Figure 9. The physical image of qualified welding appearance
图9. 焊接外观合格实物图
4.5. 激光标识的外观控制
器件封装完毕后要对盖板进行激光标识,表贴器件的盖板面积较小,但星用高频表贴器件对标识内容及位置均做出详细的规定,需在有限的空间内标识完整。
在标识过程中出现以下问题:
1) 标识字符连体(如图10所示)。

Figure 10. Schematic diagram of connecting identification characters
图10. 标识字符连体示意图
2) 标识字符位置管壳镀层偏薄,颜色较深。
针对以上问题,判断字符连体是由于激光器参数设置未随标识尺寸变化而更改,通过调整激光器的延迟参数,得到满足要求的标识字符,如图11所示。

Figure 11. Schematic diagram of optimized identification characters
图11. 标识字符优化后示意图
激光标识颜色过深,镀层较薄的原因是盖板镀层与金属封装管帽镀层存在差异,通用工艺移植后未进行调整,功率偏高。对激光输出功率进行调整,调整后字迹清楚,标识深度符合要求。
4.6. 静电控制
SAW器件采用的铌酸锂、钽酸锂单晶基片具有高透过率和高热释电性的特点,对高频SAW器件制作工艺十分不利,高热释电性使基片表面很容易聚集大量静电荷,电荷放电时会烧毁叉指电极(尤其是高频器件),增加器件次品率;高透过率会导致基片背面形成漫反射,器件容易出现不连续的线宽。静电放电带来的另一个重大问题在于一旦基片表面有了电荷积累,产生的电场就能吸引带点颗粒或者极化并吸引中性颗粒到基片表面。颗粒越小,静电对其吸引作用就越明显。随着器件关键尺寸的缩小,ESD对更小颗粒的吸引变得重要起来,能产生致命缺陷。为减小颗粒沾污,静电放电必须得到控制。
针对高频表贴SAW器件,采取以下措施进行静电控制 [4] [5] :
1) 对容易产生人体静电的区域通过防静电措施进行静电消除;
2) 对于产生热释电效应的工序,采用了控制升降温速率的方法减少静电的产生,同时,针对粘片后烘烤过程产生静电较多的情况,对粘片后芯片固化进行调整,采用压焊后进行烘烤的工艺,将烘烤过程中由于热释电效应产生的静电通过压焊丝释放,取得了较好的效果。
同时,拟引进在CO2 (90%)、H2 (10%)的混合气氛在400~800℃下退火热处理的铌酸锂和钽酸锂低静电黑片,进一步消除热释电效应。
5. 结论
本文对星用高频表贴SAW滤波器的工艺过程进行了简单的叙述,着重针对后道划片崩边、压焊丝弧度过低、激光标识不清晰等生产及工艺过程中出现的问题进行讨论,并依据实例给出了解决的方法及措施,满足了星用高频表贴产品实际的使用要求。