1. 引言
钢箱梁易于拼装,施工效率高,平顺性、稳定性好,近年来广泛用于公路和铁路桥梁。但钢箱梁对施工精度要求高,施工吊装机械对于工作空间也有较高要求。国内外学者对上述问题的研究进展概述如下。施工空间受限问题,分为上部空间受限、下部空间受限。对于上部空间受限的桥梁吊装施工问题:朱晓明、付学军 [1] 采用菱形桥面吊机吊装钢箱梁,吊机尾端横撑采用可开合式结构,既保证了斜拉索在中间安装的操作空间,又保证了吊机纵移时,通过开合横撑避让斜拉索,创新设计的吊机完成了八尺门大桥钢箱梁施工任务。丁延书、魏维、李兴林 [2] 指出,可根据周围环境和实际需求,通过增加施工平台或机械系统轨道来实现移动模架现浇箱梁施工的高度机械化。方向升 [3] 对径河桥梁上跨径河、下穿在运行硚孝高速公路的预制梁吊装施工工艺进行了详细阐述,运用导梁及大型折臂吊车等施工措施,在新建桥梁与硚孝高速梁底最小高差为4.5 m低净空的情况下,将重28 t、长16 m的预制梁吊装安装到指定位置。陈玉发、罗成 [4] 在施工过程中充分利用桥面纵梁和自主研发的滑移车、安装装置等简易工具滑移施工,减少专业安装机械的使用,简化了吊装作业并增加的工作面。对于下部空间受限的桥梁吊装施工问题:王鑫、祝新顺、沈燕飞、吴永国、卓鑫 [5] 比选了“钢平台 + 履带吊”、“钢平台 + 卷扬机”与“钢平台 + 起重支架”吊装方案,确定采用“钢平台 + 起重支架”法进行下部空间受限的新建高架桥基础的吊装施工。对于双层钢梁桥施工技术问题:龙厚全、辛保成 [6] 研究了在狭窄的交叉口范围内加建多层互通式立交桥施工技术。王思伟、宋晓、屈波 [7] 采用单层框架桥和双层框架桥相结合的顶进设计方案,将高覆土顶进框架桥转变为低覆土顶进框架桥,有效减小了高覆土顶进施工时框架桥易扎头、路基易坍塌的风险。
对于桥梁吊装方案的结构计算问题:汪劲丰、张良、向华伟、陈春雷 [8] 提出剪刀撑加强方案,在梁段的腹板与顶板开口处及缺失腹板处沿顺桥向增设剪刀撑。采用MIDAS Civil建立中跨有限元模型,分析吊装及安放过程中各梁块跨中处的位移与应力,并对实桥应力进行监测。苗建宝、骆佐龙 [9] 采用ABAQQUS进行了港珠澳大桥连续钢箱梁吊装过程中的大节段受力分析、吊点优化分析及支座预偏分析。曾准 [10] 通过BIM进行施工模拟,对临近高压线的高架桥钢箱梁吊装施工过程进行了分析。邓海、乐威 [11] 利用MIDAS Civil有限元分析软件建立全桥模型,对武汉市二环线钢箱梁在长丰大道常码头立交施工过程中的应力和变形等受力状况进行仿真计算分析,评价其结构安全性。Tian、Luo、Wang [12] 以某立交桥钢桥施工项目为背景,将BIM与无人机(UAV)相结合,简化了吊装作业计划和施工监控。叶锦华 [13] 提出了龙门吊拆除旧梁的方法。针对龙门吊拆除空心板梁施工,基于BIM技术仿真模拟了龙门吊拆梁过程,得到施工控制参数。
对桥梁吊装方案的一般性问题,主要围绕旧桥修复 [14] 、温度力影响 [15] [16] [17] 、匝道桥钢箱梁施工 [18] [19] 等问题展开。上述文献研究表明,对于空间受限的钢箱梁施工问题,国内外已有学者进行了研究,但针对双层钢箱梁施工空间受限的问题,目前相关文献较少。在软件应用方面,MIDAS和BIM是进行结构分析和施工过程管理的有效软件。本文通过BIM软件对施工过程进行精细化Revit建模,确定关键控制参数,研究如何通过优化双层钢箱梁临时支架搭设顺序及钢箱梁吊装顺序解决双层钢箱梁施工空间受限问题。并采用MIDAS Civil软件对施工过程中最不利工况情况对应的临时支架、钢箱梁和基础进行检算,评估本文提出的方案的合理性。
2. 有限空间钢箱梁吊装工艺
2.1. 工程背景
石龙坑1、2号特大桥左线第三、四联为(57 + 80 + 70 + 55) + 60 m双层变截面钢箱梁结构,桥墩采用双层门架墩、桩基础。钢箱梁节段预制,通过现场焊接形成整体。主梁采用三箱单室全焊钢箱梁,设6道纵腹板,其中左右线第3联变高钢箱梁,跨中及梁端标准梁高2.5 m (钢箱梁中心线处),连续墩顶标准梁高3.6 m,采用2次抛物线过渡,顶板全宽20.5 m,单箱室顶板宽3.3 m,单箱室底板宽3.3 m,直腹板,行车道外侧设0.5 m宽防撞护拦。顶板厚16~24 mm,腹板厚16~20 mm,底板厚18~24 mm。左右线第4联等高钢箱梁,标准梁高2.7 m (钢箱梁中心线处),顶板全宽20.5 m,单箱室顶板宽3.3m,单箱室底板宽1.95 m,腹板斜率4:1,行车道外侧设0.5 m宽防撞护拦。顶板厚20 mm,腹板厚16 mm,底板厚24~40 mm。钢箱梁沿路线设计线分成节段制造出厂,在现场吊装后将节段焊接成桥。为保证成桥后主梁线形,全桥均设置预拱度,由跨中向支点过渡,采用二次抛物线设置。钢箱梁按实际曲线线形设计,钢箱梁两侧悬臂宽1.8 m,根部高0.65 m,端部高0.35 m。横隔板标准段间距2.0 m,厚12 mm,支点横隔板厚20 mm。
桥址位于市区,第四联跨越寮步河,本项目采用钢箱梁施工钢箱梁使用50t、100t汽车进行支架的安装,再使用180 t、220 t、350 t、450 t汽车吊直接吊装至成桥位置,并在支架上进行精调及环缝、纵缝的焊接。主要施工难点为:1) 按传统的先施工下层钢箱梁在施工上层钢箱梁的方法,汽车吊工作半径受限。2) 支架利用率低下。为解决这一难题,本项目对支架安装顺序及钢箱梁吊装顺率进行了优化,整体吊装顺序为先吊装下层钢梁再吊装上层钢梁,下层钢梁挑臂节段在上层钢梁全部吊装完后再进行吊装。
临时支墩的结构形式如图1所示。
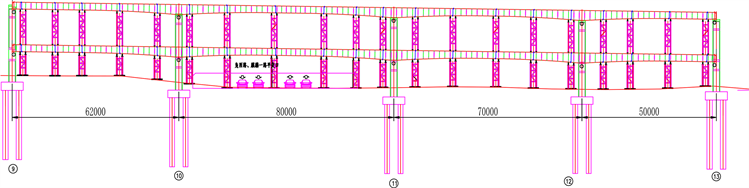
Figure 1. Schematic diagram of vertical layout for the third and fourth links
图1. 第三联、四联临时支架立面布置示意图
钢箱梁横向吊装顺序如图2所示。
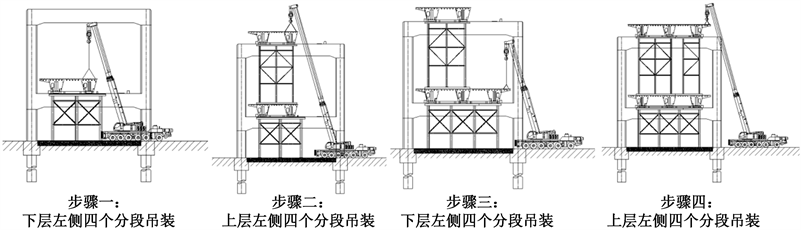
Figure 2. Transverse hoisting sequence of steel box girder
图2. 钢箱梁横向吊装顺序
2.2. 基于BIM精细化建模的施工过程模拟
以石坑特大桥第三、四联为例,通过BIM模型得出了精确的吊装施工过程中主要控制要素。主要为:钢箱梁吊点位置、现场存梁位置、汽车吊作业站位位置、汽车吊吊臂抬升角度范围、汽车吊吊臂旋转范围,确定了上述参数的采集时间、采集频率,控制指标,有效指导了工程的施工方案和安全措施的制定。以下为BIM精细化模拟施工过程模型分析。
步骤一:下层右侧钢箱梁节段一吊装,采用一台220 t汽车吊吊装,作业半径14 m,臂长33.7 m,额定吊装吨位51 t,钢梁最大吨位37 t;负荷率为72.5%,满足吊装要求。吊装平面图及BIM模型图如图3所示。

Figure 3. Hoisting drawing for girder section I of lower right steel box
图3. 下层右侧钢箱梁节段一吊装图
步骤二:下层右侧钢箱梁节段二吊装,吊装下层右侧钢梁,采用一台450 t汽车吊吊装,作业半径18 m,臂长37 m,额定吊装吨位72.3 t,钢梁最大吨位65 t;负荷率为89.9%,满足吊装要求。满足吊装要求。吊装平面图及BIM模型图如图4所示。
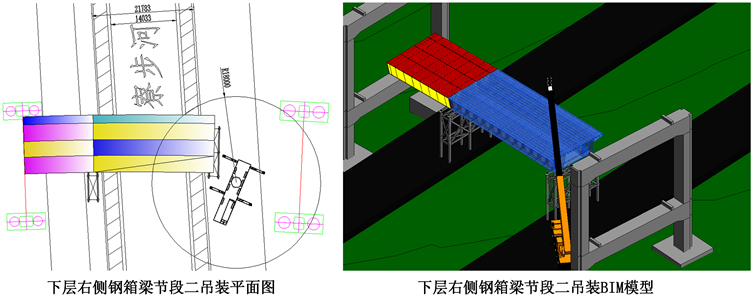
Figure 4. Hoisting drawing for girder section II of lower right steel box
图4. 下层右侧钢箱梁节段二吊装图
步骤三:下层右侧钢箱梁节段三吊装,吊装下层右侧钢梁,采用一台220 t汽车吊吊装,作业半径14 m,臂长33.7 m,额定吊装吨位51 t,钢梁最大吨位39 t;负荷率为76.4%,满足吊装要求。吊装平面图及BIM模型图如图5所示。

Figure 5. Hoisting drawing for girder section III of lower right steel box
图5. 下层右侧钢箱梁节段三吊装图
步骤四:上层右侧钢箱梁节段一吊装,采用一台220 t汽车吊吊装,作业半径14 m,臂长33.7 m,额定吊装吨位51 t,钢梁最大吨位37 t;负荷率为72.5%,满足吊装要求。
步骤五:上层右侧钢箱梁节段二吊装,采用一台450 t汽车吊吊装,作业半径18 m,臂长37 m,额定吊装吨位72.3 t,钢梁最大吨位65 t;负荷率为89.9%,满足吊装要求。
步骤六:上层右侧钢箱梁节段三吊装,采用一台220 t汽车吊吊装,作业半径14 m,臂长33.7 m,额定吊装吨位51 t,钢梁最大吨位39 t;负荷率为76.4%,满足吊装要求。BIM模型图如图6所示。
步骤七:上下层左侧钢箱梁三个分段吊装,吊装参照步骤1~6。BIM模型图如图7、图8所示。
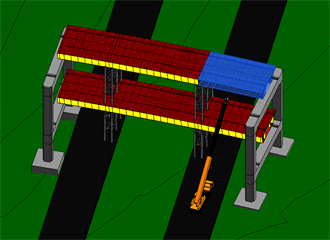
Figure 6. BIM model for hoisting of section III in upper right steel box girder
图6. 上层右侧钢箱梁节段三吊装BIM模型
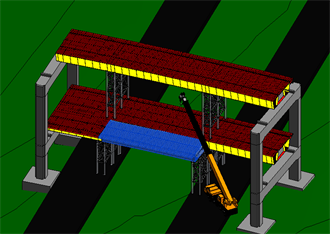
Figure 7. BIM model for hoisting of section III in lower left steel box girder
图7. 下层左侧钢箱梁节段二吊装BIM模型

Figure 8. BIM model for hoisting of section III in upper left steel box girder
图8. 上层左侧钢箱梁节段三吊装BIM模型
3. 吊装有限元模型计算分析
3.1. 计算荷载
主要考虑了钢箱梁吊装竖向荷载、施工荷载、风荷载。
根据钢箱梁节段划分,选取验算的支架考虑其承受的分段重量。钢箱梁各分段采用4个调平管支撑,调平管位于支架分配梁上。考虑各调平钢管受力不均匀系数1.2施加竖向荷载。
施工机具、人员荷载按1 kN/m2考虑。
验算风力取工程所在地10年一遇,相应风速为25.6 m/s。风压通过计算取573.44 Pa。
3.2. 计算模型
采用MIDAS Civil计算软件建立吊装支架的整体模型。钢管立柱、联结系、分配梁均采用梁单元模拟;分配梁与钢管立柱之间连接采用固定转动约束的刚性连接模拟,支架焊接点采用共节点方式处理,铰接点采用释放梁端约束的方式处理,钢管立柱底部采用固端约束。第3.1节所述各项荷载换算为相应节点及单元荷载施加至对应位置。支架共计72个节点,129个节点。计算模型如图9、图10所示。
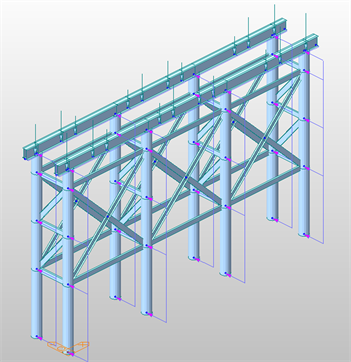
Figure 9. Calculation model of hoisting temporary support at the lower layer
图9. 主线钢箱梁下层吊装临时支架计算模型
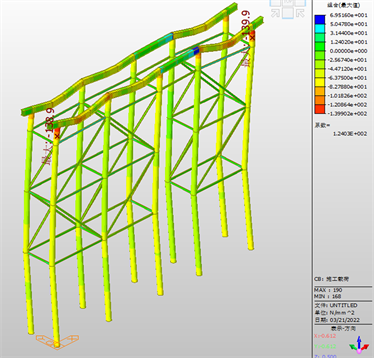
Figure 10. Maximum combined stress of upper temporary support
图10. 上层钢箱梁临时支架最大组合应力
3.3. 计算结果
临时支架钢材为Q235,上层支架最大组合应力为139.9 MPa < 170 Mpa,强度满足要求。上层支架整体稳定性系数为15.2 > 4,下层支架整体稳定性系数为4.4 > 4,稳定性均满足要求。钢箱梁材料为Q355C,最大组合应力为21 MPa < 295 Mpa,强度满足要求。
支架支反力最大位置浇筑混凝土面积为4 m × 17 m,片体支架需整体浇筑混凝土,混凝土厚度不小于50 cm,强度等级为C25,MIDAS Civil仿真模拟的钢管支架最大反力为2136.8 (kN),混凝土扩大基础浇筑面积为A = 4 m × 17 m = 68 m2,基础底部应力为2136.8/68 = 31.5 (kPa)。混凝土扩大基础底部承载力不小于50 kPa,故该施工方案地基承载力满足要求。该桥已于2022年9月完成主体施工,施工监测数据与MIDAS Ciivil计算结果一致,地基累计最大沉降22 mm,相邻不均匀沉降差3 mm,满足《公路桥涵地基与基础设计规范》(JTG 3363-2019)关于基础沉降验算的要求,说明上述施工吊装方案设计及计算结果是合理的。
4. 结论
针对双层钢箱梁空间受限问题,基于BIM建筑信息建模,结合专业有限元软件,以莞番高速石龙坑大桥第三联为例,本文提出了一种适用于在有限空间进行双层钢箱梁吊装施工的工艺流程。主要结论有以下几点:
1) 将该桥按右侧下层钢箱梁、右侧上层钢箱梁、左侧下层钢箱梁、左侧上层钢箱梁的顺序进行吊装工艺设计,可完美解决双层钢箱梁施工空间受限的问题,提高双层钢箱梁的空间利用效率,提高支架利用效率,节省建设成本。
2) 通过BIM精细化建模模拟,确定了钢箱梁吊装的关键控制参数为:钢箱梁吊点位置、现场存梁位置、汽车吊作业站位置、汽车吊吊臂抬升角度范围、汽车吊吊臂旋转范围;以及参数采集时间、采集频率,控制指标。
3) 采用MIDAS Civil模型对临时支架、钢箱梁的强度、稳定性、地基承载力进行分析验算。计算结果与施工过程中实测数据一致,表明本项目设计的临时支架结构可用于双层钢箱梁施工。本文提出的有限空间双层钢箱梁吊装工艺合理可行,可推广应用于同类桥梁的施工。