1. 引言
涡轮机轮轴是涡轮机的重要部件。一般涡轮机的使用寿命是20年 [1],主要原因是由于涡轮机轮轴的失效导致涡轮机无法正常工作,因此在满足涡轮机轮轴强度设计的前提,尽可能的减小其应力,这可以很好地延长涡轮机的使用寿命。本文基于ABAQUS分析软件,建立有限元分析仿真模型,通过优化涡轮机轮轴中部球形区域,来减小涡轮机正常工作时的最大应力,从而达到优化的目的。这可以对延长涡轮机的寿命提供重要参考价值。
形状优化是指相关设计人员通过对模型有了一定的形状设计思路后进行的一种细节设计。目的是为了通过改变某种形状参数(几何尺寸)后达到改变模型的力学性质以达到某种具体要求(如减小应力、改变位移等) [2]。在形状优化中,优化的求解是通过修改目标任务的结构几何边界来实现的。在ABAQUS中,形状的位置是通过节点来确定的,因此修改节点的位置便可以改变目标零件的形状。针对优化的问题,许多学者已经做了很深的研究,如刘威 [3] 运用拓扑优化的方法对轮轴进行优化;黄勇 [4] 通过优化凸轴轮来提高汽车发动机的性能。
本文以涡轮机轮轴作为优化目标,在模拟涡轮机轮轴正常工况的情况下,通过小幅度地改变涡轮机轮轴某一区域表面节点的位置来达到优化涡轮机轮轴的目的。该形状优化主要用于设计开发过程接近结尾阶段,即零件的大致轮廓已经定型,只允许做一些细微的调整,通过微调来减小设计区域表面最小化目标的应力集中问题。
2. 形状优化
形状优化的目的是通过小幅度的改变设计区域表面节点的位置来最小化目标的应力集中问题,进而延长零件的使用寿命,从而达到优化的目的。形状优化主要包括:模型描述、定义材料属性、添加边界条件、施加载荷、创建优化任务、创建优化区域、创建设计响应、创建目标函数、添加约束、查看优化的结果等步骤,如图1所示。

Figure 1. Flow chart of shape optimization analysis
图1. 形状优化分析流程图
在对结构形状优化的优化过程中主要包含目标函数、设计变量、约束条件三个要素,该表达式一般为 [5]:
(1)
其中,z为目标函数;
为结构响应;s为设计变量;
,
分别为设计变量的上下限;
、
分别是等式约束条件和不等式约束条件。
3. 有限元模型建立
涡轮机轮轴在工作的过程中主要受转矩作用,故而在模拟仿真是应重点关注其应力的变化。本文涡轮机轮轴所用材料的弹性模量114 Gpa,泊松比0.25。运用UG对涡轮机进行三维建模,将建立好的三维模型导入ABAQUS软件中,如图2所示。
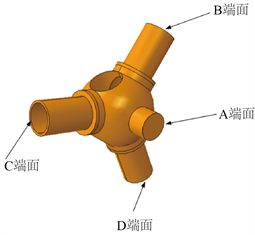
Figure 2. Schematic diagram of wind turbine axle
图2. 涡轮机轮轴示意图
其中A、B、C三个端面呈120˚分布。采用二阶四面体单元进行网格划分。得到涡轮机轮轴的网格模型示意图如图3所示。
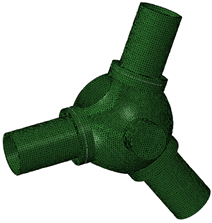
Figure 3. Schematic diagram of grid model of wind turbine axle
图3. 涡轮机轮轴的网格模型示意图
4. 边界条件和载荷
涡轮机轮轴在工作过程中承受周期变化的外力作用。一般来说,轮轴的破坏大多数都是由弯矩过大造成的,因此在应力分析计算时,主要考虑最大弯矩的工况来进行计算。本文以图4所示的涡轮机轮轴中部球形的区域作为优化区域,针对涡轮机轮轴的正常工况进行优化。
在Interaction中分别定义涡轮机轮轴端面B、端面C分别与其中心参考点进行耦合。如图5(a)所示。在端面B参考点施加沿X方向的力矩,端面C参考点施加沿-X方向的力矩,如图5(b)所示。
(a)
(b)
Figure 5. Coupling and applied load diagram. (a) Coupling diagram; (b) applied load diagram
图5. 耦合及施加载荷图。(a) 耦合图;(b) 施加载荷图
5. 创建优化任务
5.1. 建立优化任务
在形状优化前,需要选择优化的类型、选择需要的优化算法。同时,为了保证在最终设计过程中的网格质量较好,需要对网格进行光滑操作,使得内外部节点位置合适。由于光顺算法是基于单元的,如果对整个模型进行光顺化处理比较费时,可以只对优化区域内的单元指定网格光顺化处理 [6]。
5.2. 建立设计响应
设计响应的目的是为定义优化目标或约束。一般来说,形状优化可以使用特征频率、应力、接触应力、应变、节点应变能密度和体积作为设计响应,其中仅体积设计响应可被用于约束定义。一般利用回归分析设计变量与响应间的关系。在响应面模型中,常用的主要有可以提供设计变量和响应之间的关系的一次和二次多项式响应面模型。通常二次多项式响应面模型(quadratic polynomial response surface, QPRS)的一般数学表达式如下 [7]:
(2)
式中:
是二维自变量
的第
分量;
,
,
是未知参数,构成列向量
。
本文采用应力作为设计响应。选择涡轮机轮轴中部球形区域作为优化区域。
5.3. 建立形状优化目标函数和限制
5.3.1. 建立目标函数
形状优化的任务目标是在相对模型体积不变的条件下,通过在迭代循环中优化表面的节点,使优化区域的最大应力最小化(相当于最大化刚度),达到优化的目的。考虑到形状优化问题的数学表达式一般可以表示为 [8]
(3)
其中,
为第
个组件的体积;
为弹性模量;
为第i个体积约束;
为非重叠约束。
5.3.2. 创建几何限制
几何限制是对形状优化的额外约束,使得优化更加符合实际。施加合适的限制能够加速优化的进程,节省优化的时间。如果不设置几何限制的话,一方面,添加几何限制也能得到工件所需的对称性或尺寸大小的约束等;另一方面,可以使形状优化结果更加贴切实际中的生产技术制造。同时,为了在模型中保持原始的设计意图,可以通过建立运动耦合模型将负载从一端传输到另一端,同时需要固定载体的所施加区域,对于不需要优化的区域加以冻结。
1) 对称几何限制
在模型树中的几何约束(Geometric Restrictions)创建几何限制。考虑到本文所要优化的模型为轴对称的,故而将限制条件设为轴对称(Rotational Symmetry)类型。编辑几何约束。在设置Vector时,采用2点法确定Vector的具体参数,其中第一个点设为(1, 1, 1),第二个点设为(2, 1, 1),同时勾选创建一个陈列,将阵列角度设置为120˚。
2) 固定几何限制
在模型树中的几何约束(Geometric Restrictions)固定几何限制。在固定几何限制时,我们一般选则固定区域类型(Fixed Region)。选择限制区域,点击继续,将1,2,3个方向全部勾选,同时将在第一个设计循环中忽略勾选。此时,将限制设置完成后如图6所示。
5.4. 设置停止条件及查看结
5.4.1. 停止条件
停止条件就是形状优化分析的最大迭代次数,会在每次迭代中检查最大的迭代次数是否满足收敛条件并得到优化的结果。形状优化模块会提供整体和局部停止条件,一般局部条件很少需要用到。形状优化的一般默认的最大迭代次数为10次(软件自带),故而本文将最大的迭代次数设为8次(根据情况设定)。
5.4.2. 形状优化结果分析
优化完成后,点击监控,同时单击Plot,绘制优化目标曲线,如图7所示。
在可视化模块中查看优化结果。首先需要将优化结果组合(Combine)到一个输出文件中(odb),在特殊条件下,为了减少输出数据库文件的大小,我们只需保留在第一个和最后一个设计周期的分析结果。对于分析结果,只需在优化期间保留模型中的应力和位移,即场输出变量为S (应力)和U (位移)。
优化前和优化后的应力结果如图8所示。
(a)
(b)
Figure 8. Comparison diagram of stress analysis. (a) Stress nephogram before optimization; (b) stress nephogram after optimization
图8. 应力分析对比图。(a) 优化前的应力云图;(b) 优化后的应力云图
由图中结果可知,优化前的应力各项数值均大于优化后的结果。优化前应力最大值1.489e5,优化后应力最大值1.360e5,优化前后应力最大值同比下降了8.6%,说明优化后在满足基本刚度的条件下,零件所受的应力峰值有所下降,满足设计要求。
6. 结语
本文基于ABAQUS软件,对涡轮机轮轴进行形状优化。详细介绍了形状优化的任务、设计响应、目标函数和约束设置等。通过优化循环对涡轮机轮轴表面进行微调,使最小化工作过程中的最大应力由1.489e5变为1.360e5,理论上可以延长涡轮机的使用寿命。同时形状优化能为应力集中问题提供可行的解决思路。