1. 引言
镁被认为是汽车和航空航天结构应用中使用的传统金属(铝、钛、铁等)的正确替代品,具有理想的特性,如低密度、高比强度、易回收利用且经济实惠。然而,延展性差、腐蚀性和耐磨性等限制因素限制了其在实际应用中的使用 [1]。根据Von Mises准则,需要5个独立的滑移系统来实现均匀塑性变形 [2]。这对于纯镁来说是无法实现的,因为塑性流动只能通过室温下的基底滑移实现。为了克服这些局限性,在纯镁中加入多种不同可溶元素形成镁基合金 [3] [4],如AZ、AM、AXE、ZE、ZK等。其中AZ31合金因其丰富的商业可用性和良好的拉伸特性而被广泛使用,但是由于屈服强度低和铸造缺陷,AZ31镁合金在铸态下的使用寿命有限。
如何提高变形镁合金在室温下的成形性能是目前镁合金研究领域有待解决的关键问题之一 [5],目前的研究是通过激烈的塑形变形改善镁合金的孪晶组织,使得晶粒细化和织构弱化 [6]。Watanabe [7] 和Huang [8] 等人通过异步轧制弱化AZ31基面织构强度,大幅提高室温成型性能。任国成 [9] 采用数值模拟与实验分析相结合的方法对镁合金的ECAP变形工艺进行研究,发现等通道挤压最优变形温度为250℃,经过不同路径四道次ECAP工艺处理后,其室温力学性能有明显的提高。支晨琛 [10] 经过交叉工艺轧制后晶粒明显细化,大部分晶粒已发生完全动态再结晶,小角度晶界数量减少,基面织构峰值强度也从23.68最低可降为7.62。更加细小的晶粒不仅可以产生更大面积的晶界,同时弱化基面织构,明显抑制裂纹的扩展,控制边裂的生成。田静 [11] 通过弯曲矫直使板材性能提升,其中波腰处组织起主要作用。
本文通过模拟与实验相结合的方法,对AZ31镁合金压弯–轧平复合形变进行研究,分析镁合金的组织性能和组织变化,织构弱化规律。
2. 实验
2.1. 实验方法
实验采用厚度为3 mm和5 mm的商用AZ31B板材,长宽为100 × 100 mm,具体成分见表1。实验前对板料进行400℃保温20 min。随后进行压弯实验,压弯模具装配在3150KN四柱液压机上,液压机参数见表2。压弯模具如图1所示,压弯模具齿间距为30 mm,齿深为8 mm。压弯之后保温20 min后进行轧制实验,轧机参数见表3。轧制时采用两种送进的方向,即轧制方向和压弯方向相同、轧制方向与压弯方向垂直。将压弯之后的板材轧平为一道次,两道次之间夹角为90˚,不同道次轧制方向相同。对比不同轧制方向和不同道次对板材微观组织影响。
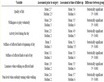
Table 1. Chemical composition of AZ31 magnesium alloy (mass fraction/%)
表1. AZ31镁合金的化学成分(质量分数/%)
(1) 模具二维图
(2) 模具实物图
Figure 1. Press-bending tooling diagram
图1. 压弯模具图
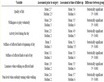
Table 2. Basic performance parameters of four column hydraulic press
表2. 四柱液压机基本性能参数
2.2. 有限元模型
在有限元软件中建立本实验所需要的模具三维模型比较困难,因此通过专业三维造型软件建立模具及板材的三维模型,保存为STL格式并导入到前处理中。模具及板材几何模型如图2所示。
(a) 压弯变形三维模型
(b) 轧制变形三维模型
Figure 2. Mold and plate 3D model
图2. 模具及板材三维模型
因为所使用的有限元软件的材料库中无AZ31镁合金数据,故需手动输入相关参数 [12]。利用真应力–应变曲线数据 [13],构建AZ31镁合金在高应变速率下的本构。
(1)
式中
为应变速率,s−1;Q为变形激活能,J/mol,与材料有关;σ为流变应力,MPa;n为应力指数;T为绝对温度,K;R为摩尔气体常数,8.314 J/(mol∙K);A和α为与材料有关的常数。
2.3. 微观组织模型
AZ31镁合金材料微观组织模拟需要的相关参数见表4。
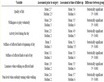
Table 4. AZ31 magnesium alloy material parameters
表4. AZ31镁合金材料参数
2.3.1. 元胞自动机
元胞自动机(cellular automata, CA)早在20世纪90年代就被应用于金属塑性变形时的微观组织模拟研究。镁合金在塑性成形过程中的发生的孪生及动态再结晶现象无法通过直接观察而获得。本章通过有限元模拟软件的Microstructure模块对镁合金网格式壁板的压弯成形过程使用CA法进行模拟,可以模拟在不同的实验工艺参数下镁合金壁板的微观组织演变,分析动态再结晶行为。使用CA模拟动态再结晶过程之前,需要在CA中嵌入适当的演化规则。因此,CA模型由位错密度、动态回复(DRV)、DRX的成核和长大模型组成 [14]。
2.3.2. 位错密度模型
镁合金在热塑性变形过程中会发生加工硬化,导致位错大量增殖、堆积和纠缠,以致位错密度不断升高,动态回复与再结晶使位错合并导致位错密度下降。采用修正的Laasraoui-Jonas (L-J) [15] [16] 位错密度模型表示晶粒内部位错密度的演变。
(2)
式中:ρi表示第i个新晶粒的位错密度,ε表示应变,h表示应变硬化系数,r表示动态回复软化系数。式中硬化系数和动态回复软化系数是温度和应变速率的函数,见式(3)、式(4)。
(3)
(4)
应变速率修正常数
一般取1;应变硬化参数h0和应变回复参数r0均为常数;m为应变率灵敏系数;Q是扩散激活能;R是气体常数;T是变形温度。
将表3中的数据带入到式(3)、(4)中,可以求出硬化参数和动态回复软化系数,见式(5)、式(6)。
(5)
(6)
2.3.3. 再结晶形核模型
动态再结晶的形核条件与位错密度有关,位错密度,一旦位错密度增加到动态再结晶的临界位错密度ρc时,动态再结晶开始在晶界处开始形核。DING R和GUO Z X [17] 认为形核速率与温度、应变速率的关系可以由式(7)表示。
(7)
式中:
为形核速率;C为材料常数;QD为动态再结晶热激活能。
2.3.4. 晶粒长大模型
位错密度、应变达到了临界值后开始发生再结晶。DING R等 [18] 采用式(8)表达第i个新晶粒生长速度(vi),Fi表示第i个新晶粒的趋动力(见式(9)):
(8)
(9)
式中:D表示自扩散有效系数;vi表示第i个新晶粒的生长速度;K表示波尔赫兹常数;ri表示第i个新晶粒的半径;ρm表示基体晶粒位错密度;τ表示位错线能量;γi表示第i个新晶粒的晶界能。
3. 结果分析
3.1. 应力分析
图3为压弯轧制时的应力场分布情况,可见在压弯过程中最大应力集中在波峰和波谷处,轧制过程中应力集中在轧辊与波峰波谷接触位置,因为波峰波谷处形变量最大,大塑性变形导致位错密度上升,以致波峰波谷处应力较大。所以选波峰波谷处作为特征点进行应力分析。图4为特征点选取位置。
(a) 压弯过程中应力场
(b) 轧平过程中应力场
Figure 3. Stress field distribution during deformation
图3. 变形过程中应力场分布
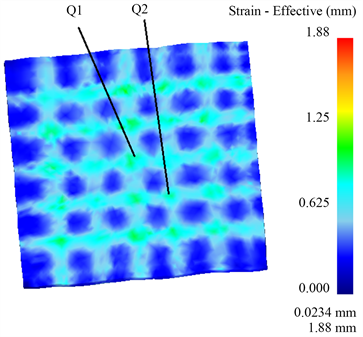
Figure 4. Feature point selection location
图4. 特征点选取位置
图5、图6为两道次复合形变特征点等效应力变化情况,Q1和Q2特征点应力增长速度从某点开始有明显下降,该点之前为弹性变形阶段,该点之后为塑性变形阶段。之后等效应力开始增大,当变形程度继续增加,板材发生了加工硬化使得所需要的变形力继续增加,与此同时壁板的内部发生了动态再结晶,晶粒逐渐细化,镁合金壁板的塑性有所提高,但加工硬化仍大于动态再结晶,所以等效应力继续增加,但坡度变缓。
第二道次等效应力比第一道次高,这是因为第一道次变形使该处位错密度升高,即二道次变形初始状态位错密度大于第一道次,加工硬化现象更明显。5 mm板材变形过程中等效应力较3 mm板材低,因为板材厚度增加使位错密度降低,不容易产生应力集中,所以5 mm板材等效应力较3 mm板材低。在压弯过程中波峰相交点Q1比波谷相交点Q2等效应力稍高,因为在压弯过程中压弯模具直接接触波谷,波峰处无模具接触,如图7,这导致波峰应变较波谷大,所以波峰处等效应力较波谷处稍大。轧制产生的应力基本小于弯曲所产生的应力。轧制方向对最大等效应力影响不大。变形过程中最大等效应力如表5所示。
(a) 轧制垂直与压弯
(b) 轧制平行于压弯
Figure 5. Thickness of 3 mm plate two times the composite deformation equivalent force
图5. 厚度为3 mm板材两道次复合形变等效应力
(a) 轧制垂直与压弯
(b) 轧制平行于压弯
Figure 6. Thickness of 5 mm plate two times the composite deformation equivalent force
图6. 厚度为5 mm板材两道次复合形变等效应力
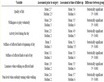
Table 5. Maximum equivalent force values for different thicknesses of plates, rolling directions, and passes (unit: MPa)
表5. 不同厚度板材、轧制方向、道次最大等效应力值(单位:MPa)
3.2. 微观结果
图8为微观组织模拟结果和实际结果对比,在单道次复合形变之后,组织中存在被拉长的晶粒,也存在因复合形变而破碎的晶粒,再结晶晶粒主要在原始晶界处形核。在单道次复合形变轧制垂直于压弯方向的组织内出现少量孪晶,因为其变形剧烈程度比轧制平行于压弯大,镁合金柱面和锥面滑移系在高应变速率下不足以支持完成大塑性变形,变形机制为滑移与孪生。在两道次复合形变后晶粒更加细化,随着变形量的增加,两种轧制方向均发生孪晶现象。仍然存在复合形变之后被拉长的晶粒,同时可以观察到再结晶在晶界处呈链状分布,这与孪晶诱导再结晶有关 [16]。轧制方向与压弯平行时晶粒细化程度较大,两道次晶粒细化更加明显。不同工艺复合形变下板材的平均晶粒尺寸和模拟组织的平均晶粒尺寸对比及细化程度如表6所示,模拟晶粒尺寸与实际晶粒尺寸误差在7%以内,说明组织模拟结果与实际微观组织结果相吻合。可知,模拟过程中所设置的参数合理,能预测AZ31镁合金复合形变过程中的动态再结晶演变过程,模拟具有一定指导意义。
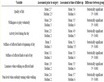
Table 6. Average grain size of simulated and actual tissues under different processes
表6. 不同工艺下模拟组织与实际组织平均晶粒尺寸
3.3. 织构分析
镁合金原始板材在{0001}方向上织构强度最大,所以讨论在该方向上的织构情况。可以看出单道次复合形变使织构强度降低,单道次轧平反方向与压弯平行时弱化较明显,随着道次的增加,板材织构进一步弱化,这是因为随着复合形变的进行,材料内部动态再结晶和孪晶的产生引起了织构的改变,弱化了板材织构强度(图9)。
4. 结论
本工作通过建立宏观有限元模型和微观再结晶模型对AZ31镁合金板材进行压弯–轧平复合形变宏微观模拟。研究了AZ31镁合金在压弯–轧平复合形变过程中应力变化和组织演变过程。结论如下:
1) 所选特征点第二道次的应力值大于第一道次,波峰处应力值略小于波谷处,5 mm板材平均应力小于3 mm板材,轧制方向对应力影响不大。
2) 单道次复合形变再结晶形核区域在原始晶粒附近,且存在被拉长的晶粒。单道次复合形变轧制垂直于压弯出现少量孪晶,两道次复合形变均出现孪晶现象,再结晶程度更大,两道次变形平均晶粒尺寸较单道次晶粒尺寸小。
3) 采用元胞自动机法对镁合金板材的微观组织演变进行了数值模拟。模拟结果与实验结果基本相吻合,平均晶粒尺寸的最大相对误差为6.34%。
4) 压弯–轧平复合形变能有效地弱化板材织构,轧平反方向与压弯平行时弱化较明显,两道次弱化程度较大。
基金项目
辽宁省教育厅科学研究经费项目(LG202010)。