1. 引言
自1844年美国医生John Gorrie使用刚发明的机制冰对阿伯拉契科拉医院的气温进行调节,至1890年前后空调才取得初步成果,即有工业空调也有民用空调。随着时代和科技的不断发展,空调被广泛应用到生活家居、交通运输业、工业生产以及航空航天等各领域 [1] [2] [3] [4]。虽然我国空调行业在上世纪90年代中期才起步,但近年来其普及速度十分迅速 [5]。伴随着国内城市化进程不断加快,以及人们对生活环境的要求也不断提升,使得市场对空调的需求也在不断扩大 [6]。从而制造空调时其内部零件的需求量也在不断增加 [7]。单向节流阀作为最简单的自控元件在不同类型的制冷系统中有广泛的应用 [8]。然而在大量订单的积累下,多数生产企业仍沿用传统的人工加工的方式来制作单向节流阀,这很显然已经不能满足当前市场的需求。
随着国内制造业转型升级的不断推进,各生产企业都着力于提升生产环节的自动化程度。通过现代化、自动化的设备逐步取代人工从而推动企业转型升级。机械手作为抓取零件的执行件,已广泛地应用在自动化设备中,杨金祥等 [9] 设计了一种全自动总成检具的机械手上料装置,使用多滑块夹紧机构,并利用无杆气缸提供动力,能够很好地实现总成检具的全自动精确上料定位;田永庆 [10] 设计的双电磁吸盘上下料机械手和数控机床有机融合,实现了工件的自动上下料、装夹以及加工等;郭一行等 [11] 对滚珠丝杠在升降输送机工作过程中的受力情况及产生径向载荷的原因进行了研究,提出了两种能有效减小滚珠丝杆径向载荷的方法;Gao Mingyu等 [12] 提出了一种能适应复杂环境的机器人手臂抓取系统,在设备速度较高的情况下,其抓取成功率接近88%;韩岩等 [13] 设计了一种水下目标抓取及打捞装置,设计的机械手结构更便于抓取,在此基础上还具备锁定功能,能够较好的完成水下、水面打捞工作;熊彬州 [14] 设计了一种液晶显示器光学薄板的自动抓取设备,利用PLC控制器,极大地提高了显示器生产的自动化程度;常数数 [15] 设计了一种西兰花采收装置,极大地降低了采收成本,提高了采收效率。通过对相关抓取装置以及设备的对比分析,结合单向节流阀现有的生产工艺流程,使用SolidWorks对设备的零部件进行设计与建模,设计装配出设备整机;通过PLC控制设备各装置的运行从而实现设备的自动化;此外,设备搭载触摸屏,设计的人机交互界面更利于操作员较好地监控与使用设备。
2. 单向节流阀的构造原理
单向节流阀其结构虽然简单,但其以既可作为单向阀,又可作为节流阀的特性而广泛使用在液压控制系统的回路中。单向节流阀主要由阀体、过滤网、阀芯座组件等构成,其零件示意图如图1中所示。其中,阀芯座组件由阀芯与阀芯座组成,是实现节流阀节流与内部单向导通的主要部件。其工作原理为:回路中的液体由缩口端(图1单节流阀右侧)流入,经过过滤网4后流入阀芯座组件内,流出阀芯座组件后再经由过滤网2流出阀体;当回路中的液体反向流动时,阀芯的斜面与阀芯座的斜面贴合,阻挡液体流通,由此实现单向导通的特性。
1-单向节流阀阀体;2-过滤网;3-阀芯座组件;4-过滤网
Figure 1. Schematic diagram of one-way throttle valve parts
图1. 单向节流阀零件示意图
3. 单向节流阀加工工艺过程及加工布局安排
3.1. 单向节流阀机械加工工艺过程
单向节流阀从原料配件加工至成品需经过:滚字、装阀芯座组件、装过滤网、缩口以及打点等工艺,其工艺过程流程图如图2所示。在加工过程中对阀芯座组件以及过滤网的安装位置有着较高的精度要求。由于缩口端的外圆柱直径和外圆柱面是与其他零部件装配时的重要接触面,其缩口后外圆柱直径和外圆柱面的圆柱度要控制在较小的范围内。
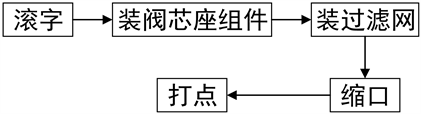
Figure 2. Flow chart of machining process of one-way throttle valve
图2. 单向节流阀机械加工工艺流程图
3.2. 单向节流阀加工布局安排
根据单向节流阀生产工艺,考虑到加工过程中需往阀体内装配入阀芯座组件、且阀芯座组件两端均需装入过滤网,在过滤网装入后有夹紧工序。若采用铜管水平放置装配的方式,在装入内部零件以及打点时,有较大的概率铜沫会顺着装配滑入管内;在单向节流阀使用的过程中,滑入的铜沫会导致阀芯座组件堵死的现象。由于竖直方向上铜管上端无法固定,故缩口工艺不适合在竖直方向上进行。考虑到设备布置的合理性,使用激光打字工艺代替原有的滚字工艺。由此确立了激光打字、装阀芯座组件以及装过滤网等工序以铜管竖直放置的方式加工;缩口、打点等工序以铜管水平放置的方式进行加工。其生产设备如图3中所示。
1-抓取装置;2-平移装置;3-铜管下料装置;4-激光打字装置;5-装阀芯座组件装置;6-夹紧装置;7-装过滤网装置;8-旋转装置;9-缩口装置;10-打点装置
Figure 3. One-way throttle valve automatic production equipment
图3. 单向节流阀自动化生产设备
缩口装置位于图3~9处,铜管移载至缩口装置处时:未缩口端处有挡板做支撑,缩口模具在气缸的带动下挤压铜管缩口端。下由此,采用ABAQUS分析软件对缩口工艺进行仿真模拟。
4. 铜管缩口的仿真与分析
铜管的缩口加工为设备中倒数第二道工序,在铜管收缩过程中如何控制好收缩量;以及如何将冲击控制在合理范围内是设备设计制造过程中的重点与难点。因此采用ABAQUS仿真软件建立铜管一端固定另一端进行缩口工艺的模型进行仿真分析,探究铜管在缩口过程中管体受最大压力与变形情况便于气缸选型。
4.1. 铜管的缩口有限元模型与参数设置
根据实际加工情况,查阅相关文献,铜管的内外径、长度、密度、杨氏模量以及泊松比等参数如表1中所示。
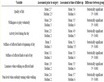
Table 1. Related parameters of copper pipe model
表1. 铜管模型的相关参数
在缩口过程中,铜管一端受缩口模均匀的挤压,在缩口模具中压制成预设的形状。本文采用静力学仿真(Standard),在ABAQUS中采用轴对称单元,将三维模型转换为二维模型,简化计算过程,并将铜管轴心设置在Y轴上。最终结果在采用扫描(sweep elements)指令将其还原成三维。
4.2. 边界条件与网格划分
基于实际加工中,铜管在进行缩口工艺时,无缩口端贴合在模具上。因此在模型中设置边界条件是,将无缩口端处的边界线固定且无缩口端与该边界线绑定,设置缩口模具U2方向的进给量为11.99 mm。由于缩口模具与边界固定线设置为解析刚体,无需进行网格划分,只需将铜管采用六面体单元进行划分;由于铜管壁厚较薄,默认划分情况下在壁厚处不足4个单元,为保证整个模型具有良好的网格质量与仿真结果的正确性,因此需单独将壁厚处的网格划分为4个单元;该铜管划分网格后有1685个节点,1344个单元,并设定网格单元为轴对称应力中的CAX4R (四结点双线性轴对称四边形单元,减缩积分,沙漏控制)。边界条件与网格划分如图4所示。
(a) 载荷(b) 网格划分
Figure 4. Copper tube boundary conditions and meshing diagram
图4. 铜管边界条件与网格划分图
4.3. 仿真结果与分析
在ABAQUS中仿真得出,在缩口模具不断向铜管压制的过程中,其向受应力情况云图如图5所示。由图5(a)中可知铜管受S11方向上的应力主要集中在缩口模具与铜管接触的较小区域内,且最大点发生在与缩口模具接触的一圆线上,且随着缩口模具向铜管推进的过程中,最大应力范围也不断上移,但应力始终集中于铜管缩口斜面下方处;有图5(b)中可知,在S12方向上,铜管所受的应力较小,在模具与铜管接触处,出现应力集中区域;最大应力发生在距缩口模具与铜管接触上方约1/4铜管外径处;由图5(c)中可知,在S22方向上,最大应力发生在铜管斜面下方约1/4铜管外径处,且呈现中间大,往两侧不断减小的趋势;由图5(d)中可知,在S33方向上最大应力发生在铜管口处且沿铜管方向上应力不断减小。由此可知,模具沿铜管轴向进行挤压缩口时,S22与S33方向上的受应力情况可较好的体现铜管的压应力变化。因此为减小铜管形变量,应控制轴心方向上的冲击。
缩口过程中铜管受冲击的大小与缩口模具速度成正比,速度越大,其对铜管产生的冲击越大,较大的冲击会使得铜管在缩口过程中产生形变。在建立仿真模型时,分别选取缩口模具速度50 mm/s、150 mm/s、450 mm/s各一组进行仿真模拟;发现缩口模速度在50 mm/s 时铜管缩口处无明显变形,且外圆面圆柱度符合装配要求;缩口模速度在150 mm/s时铜管缩口端产生轻微变形,其模具速度在150 mm/s时缩口过程中管口形状变化如图6所示,缩口模速度在450 mm/s时铜管缩口端产生较为明显的变形,其外圆直径与外面面圆柱度无法满足装配要求,故在缩口过程中应将缩口模具速度控制在150 mm/s以下。
缩口模具速度分别为50 mm/s、150 mm/s、450 mm/s时其缩口后管口变形情况如表2中所示。由于缩口后外圆柱直径和外圆柱面的圆柱度是单向阀与其他零件配合的重要参数,因此要保证模具速度小于等于150 mm/s。
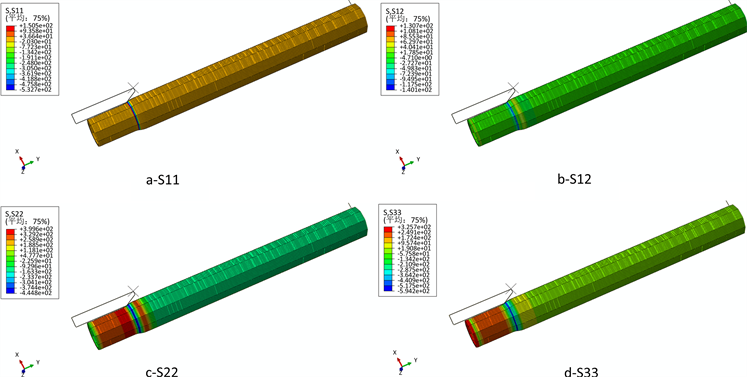
Figure 5. Force cloud map of copper tube necking
图5. 铜管缩口受力云图
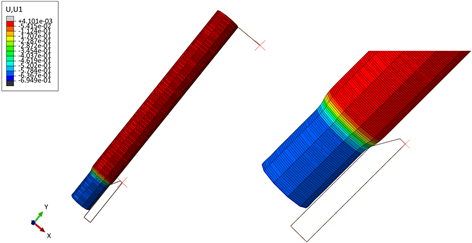
Figure 6. The shape change diagram of the nozzle during the copper tube shrinking process
图6. 铜管缩口过程中管口形状变化图
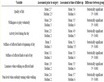
Table 2. Deformation of copper pipe nozzle at different speeds
表2. 不同速度铜管管口变形情况
在缩口过程中,铜管受力大小随时间变化情况如图7中所示。由图可知,铜管所受最大压力约为2000 N。由于缩口模具的移动采用气缸来完成,缩口仿真过程中气缸在铜管上的实际负载需不小于2000 N,在实际生产中,考虑气压、缩口模具的重量等因素的影响,适当将其增加20%作为气缸选型的标准。
4.4. 缩口气缸的选型
设计设备单工艺步时间为4 s,其中抓取装置抓取转运铜管需占用2 s,设计的缩口模由起始端至缩口完毕端位移量约为50 mm;假定气缸匀速运行,气缸伸缩距离为两倍的位移距离,即100 mm。

Figure 7. The pressure condition of the copper tube shrinkage
图7. 铜管缩口受压力情况
由位移与速度关系公式
(4-1)
v-气缸运动速度;
s-气缸位移量;
t-气缸运动时间。
将s = 100 mm,t = 2 s,代入式4-1中可得v = 50 mm/s。
表3为伸缩气缸负载率使用表。
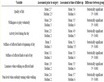
Table 3. Telescopic cylinder load rate usage table
表3. 伸缩气缸负载率使用表
根据气缸理论输出力计算公式:
(4-2)
F0-气缸理论输出力;
F-气缸的实际负载;
η-负载率。
由表3,取负载率η = 65%,将铜管所受最大压力F = 2000 N代入式4-2中,可得气缸理论输出力
,取整后F0为3700 N。
由气缸缸径计算公式:
(4-3)
F0-气缸理论输出力;
r-气缸半径;
P-气缸缸内压强。
气缸的工作压力一般为0.4~0.6 MPa,取P = 0.5 Mpa,将
代入式4-3中,可得r = 48.55 mm,则D = 97.10 mm,将D取整D = 100 mm。
选取SMC品牌型号为C95EB100-100的气缸作为执行气缸可满足使用需求。
5. 结论
本文以单向节流阀加工过程中铜管缩口工艺为主要研究对象,对缩口工艺进行仿真分析,得出下述结论:
1) 铜管缩口时受模具挤压其应力最大发生在铜管轴线处(模具运动方向上),且应力最大处于缩口部分中部,呈现向两侧逐渐递减的趋势;
2) 铜管受冲击的大小与模具运行速度相关:速度越大,冲击越大,当速度达到150mm/s时缩口端开始产生较为明显的形变;
3) 铜管在缩口过程中所受最大压力约为2000 N,依此作为模具气缸选取的重要条件。
综上,本研究通过对单向节流阀缩口工艺的分析,探究了其在缩口过程中的应力分布、受最大压力值以及在不同速度下缩口模具对铜管的冲击情况,为提升单向节流阀缩口工艺质量提供了理论依据。