1. 引言
7075铝合金结构紧密,具有较好的普通抗腐蚀性能和良好机械性能 [1],被广泛应用于航空航天、船舶制造和武器装备等领域 [2] [3] [4]。通过对铝合金进行微弧氧化处理,使其表面生成氧化铝陶瓷膜层,可以进一步提升材料的耐磨损、耐腐蚀、耐高温等表面性能 [5] [6] [7] [8],因而使得该技术在铝合金应用领域得到大规模推广。但是,由于微弧氧化陶瓷膜生长过程中,难易避免放电微孔和裂纹的出现,从而导致材料表面耐磨损、耐腐蚀、耐高温性能提升的同时,粗糙度变大,影响待处理元件本身的精密度 [9]。因此在对铝合金进行微弧氧化处理时,往往需要在提高膜层耐磨损、耐腐蚀、耐高温性能的同时,尽可能降低膜层的粗糙度。特别是扫描式微弧氧化处理中,由于极间距小,加上电极形貌和扫描运动的影响,膜层均一性更容易受到影响 [10],对降低膜层粗糙度的要求更高。
本文主要针对网状电极微小极间距条件下的微弧氧化处理进行研究,通过正交试验,分析电参数对微弧氧化成膜粗糙度的影响,研究如何通过电参数的优化对氧化膜粗糙度进行靶向控制。以期对微弧氧化处理工艺的发展提供必要的理论依据。
2. 试验条件和方法
2.1. 试验条件
微弧氧化电源为济南能华机电设备有限公司生产的NHSM800-5型开关直流双脉冲电源。动阴极使用直径16 mm的网状电极,材质为304不锈钢。阳极为待处理的7075铝合金,内部各元素含量如表1所示。试验极间距为2 mm。电解液为Na2SiO3、NaOH、NaF混合溶液,配比参数见表2。
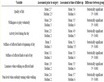
Table 1. Content of elements in 7075 aluminum alloy (wt%)
表1. 7075铝合金中各元素含量(wt%)
2.2. 正交试验设计
为节省研究时间和精力,采用正交实验法,利用标准的正交矩阵对试验进行设计、比较、分析。固定反向电压为−200 V,总占空比50%,反应时间300 s。挑选具有代表性的因素(正向电压、占空比、频率等电参数)利用正交表安排试验如表3所示。
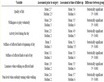
Table 3. Combination of electrical parameters
表3. 电参数组合
2.3. 粗糙度测量
利用北京吉泰科仪检测设备有限公司生产的TR200表面粗糙度检测仪(如图1所示),测量本研究所得试验样品表面膜层粗糙度。该表面粗糙度检测仪体积小,操作简便,功能全面测量快捷,精度稳定,测量参数符合GB/T3505国家标准。测量精度0.001 μm,测量范围0.005 μm~16 μm,取样长度0.25 mm、0.8 mm、2.5 mm三档可选,评定长度1~5倍取样长度可选。

Figure 1. TR200 surface roughness tester
图1. TR200表面粗糙仪
本研究中为了尽可能得到整个样品表面的整体粗糙度情况,在样品的4处不同位置分别测量7.5 mm长度上的平均粗糙度,即取样长度设置为2.5 mm,评定长度设置为5,计算4次测量结果的平均值,看作最终膜层粗糙度。试验结果如表4所示。
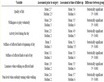
Table 4. Measurement results of film surface roughness in electrical parameter comparison test
表4. 电参数对比试验膜层表面粗糙度测量结果
2.4. 表面形貌观测
使用VEGA XMU扫描电子显微镜(SEM)对生成氧化膜表面形貌进行观测,通过分析不同电参数条件下微弧氧化膜层表面放电微孔和裂纹的变化规律,研究电参数对膜层粗糙度的影响机理。
2.5. 数据分析
通过极差分析法对结果进行分析,计算膜层硬度在同一个电参数水平上的平均值、极差值(最大值–最小值)和相对极差(极差/平均值)。通过相对极差值分别表示各个参数对陶瓷膜层硬度的影响程度 [11],相对极差越大说明该参数的对成膜厚度影响程度越大,即该电参数的变化将最大程度影响膜层生长速度,若要提高膜层生长速度,则应优先考虑对该电参数进行优化;通过不同电参数下膜层硬度平均值的变化,研究电参数对膜层硬度的影响规律,确定该电参数应增大还是减小。
3. 正向电压对膜层粗糙度的影响
利用表4的测量结果,针对正向电压对样品陶瓷膜层粗糙度影响的进行极差分析,分析结果见表5。表4中1至3号电参数组合中正向电压相同,均为300 V,试验样品陶瓷膜层的粗糙度最大值为0.497 μm,平均值0.396 μm。4至6号试验中,正向电压均为400 V,生成样品的陶瓷膜层粗糙度最大值为0.899 μm,平均值为0.675 μm,相对300 V时的试验样品,陶瓷膜层平均粗糙度增加了0.279 μm,增比高达70.4%,正向电压增高导致的膜层粗糙度差,且变化明显。7~9号试验中,正向电压同样又增加100 V,增加至500 V,生成样品的陶瓷膜层粗糙度最大值为1.136 μm,平均值为0.792 μm,陶瓷膜层平均粗糙度增加了0.117 μm,增比17.3%,膜层粗糙度虽有增加,但增幅已明显降低。
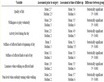
Table 5. Effect of forward voltage on film roughness
表5. 正向电压对膜层粗糙度的影响
如图2所示,微弧氧化时间相同的情况下,正向电压增大会使微弧氧化反应生成的陶瓷膜层粗糙度增大,当正向电压达到一定程度时,粗糙度变化减缓。这是因为,正向电压增高,反应中放电能量高,反应更加剧烈,当击穿放电正向电压过高时,由于放电能量过高,很容易造成反应过于剧烈,使氧化陶瓷膜局部出现烧烛现象。同时随着反应电流密度的增大,脉冲能量不断升高,会使陶瓷膜层表面的放电微孔尺寸增大,氧化膜表面粗糙度变大,表面裂纹增多。图3为正向电压不同时陶瓷膜层表面SEM图像,其中图3(a)~(c)分别为1、5、8号试验参数下反应生成的陶瓷膜层,正向电压分别为300 V、400 V、500V。正向电压为300 V时放电微孔小而密,最大微孔直径1.56 μm;正向电压为400 V时,微孔数量变少,但放电微孔直径变大,最大微孔直径1.73 μm,而且陶瓷膜层表面出现明显的裂纹;正向电压为500 V时,微孔数量继续增大,裂纹增多,最大微孔直径也增大至2.47 μm。可见,铝合金微弧氧化陶瓷膜层厚度增加,必将带来放电微孔增大的问题,从而影响陶瓷膜层的粗糙度和耐腐蚀性。
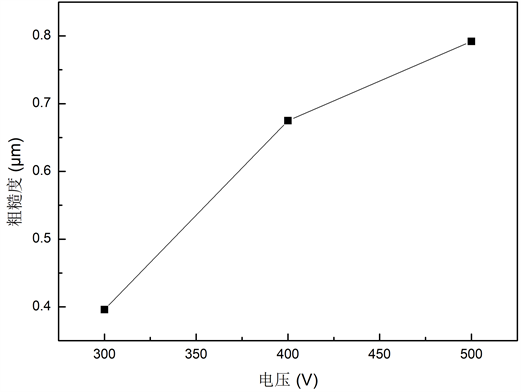
Figure 2. Effect of forward voltage on film roughness
图2. 正向电压对膜层粗糙度的影响
(a) 300 V
(b) 400 V
(c) 500 V
Figure 3. SEM images of the film surface generated under different forward voltage
图3. 不同正向电压生成膜层表面SEM图像
另外,由表5中的极差分析可知:正向电压均为300 V时,3组试验样品陶瓷膜层的粗糙度极差为0.154 μm,相对极差0.39,此时膜层粗糙度变化受其他参数影响较小。4至6号试验中,正向电压400 V,3组试验样品的膜层粗糙度极差为0.497 μm,相对极差0.74,相互之间的差异明显,说明在该正向电压下,其他电参数对试验样品陶瓷膜层粗糙度的影响显著增大。7~9号试验中,正向电压增加至500 V,生成样品的陶瓷膜层粗糙度极差为0.934 μm,相对极差1.18,相互之间的差异更加明显,说明铝合金微弧氧化试验中,极间正向电压越高,其他电参数对生成氧化陶瓷膜层粗糙度的影响越大,更需要对频率、占空比等电参数进行更为精细的选择。
4. 占空比对膜层粗糙度的影响
利用表4的测量结果,对占空比相同的试验所得陶瓷膜层进行粗糙度的平均值、极差和相对极差分析,结果如表6所示。1号、4号和7号电参数组合中占空比设置相同,反向占空比为40%,正向占空比为10%,试验样品陶瓷膜层的粗糙度平均值0.315 μm。2号、5号和8号试验中,反向占空比为30%,正向占空比为20%,生成样品的陶瓷膜层粗糙度平均值为0.705 μm,相对反向占空比为40%的试验样品,陶瓷膜层平均粗糙度增加了0.390 μm,增比高达123.8%,反向占空比减小后,生成陶瓷膜层的粗糙度明显增大。3号、6号和9号试验中,反向占空比为20%,正向占空比为30%,生成样品的陶瓷膜层粗糙度平均值为0.844 μm,陶瓷膜层粗糙度平均值增加了0.139 μm,增比19.7%,膜层粗糙度增幅不明显。
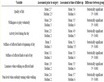
Table 6. Effect of reverse duty ratio on film roughness
表6. 反向占空比对膜层粗糙度的影响
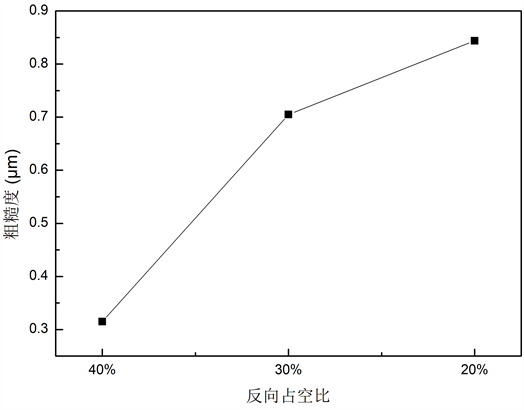
Figure 4. Effect of reverse duty ratio on film roughness
图4. 反向占空比对膜层粗糙度的影响
如图4所示,微弧氧化时间相同的情况下,随着反向占空比减小,生成氧化陶瓷膜层粗糙度逐渐增加,但增速减缓。经分析认为,可能的原因是由于总占空比50%不变,反向占空比减小,正向电压占空比增大,正向脉冲宽度变大,单脉冲放电时间增加,导致单脉冲放电能量大大增加,增加了火花放电的持续时间,从而影响微弧氧化反应的剧烈程度,由于火花放电而导致的熔融氧化物必然增多,电通道周围的冷凝氧化物颗粒随之增加,氧化物颗粒在局部区域沉积增厚的情况也更为严重,单个氧化物颗粒尺寸变大,致使陶瓷膜层表面粗糙度增大。另外,由于火花放电能量增大,会导致放电通道直径变大,使得放电微孔尺寸变大;同时,由于负脉冲过程中,析氧的还原反应会使已经生成的氧化陶瓷膜表面发生溶解,凸起的熔融物距离阴极更近,更容易发生还原反应而溶解,从而改善膜层表面的粗糙度,因此反向占空比越大,陶瓷膜层粗糙度越小;而且,由于高能量使得反应温度更高、压强更大,进而使陶瓷膜层生长过程中受到的热应力变大,导致膜层表面裂纹增多,裂纹长度和宽度增大,同样造成陶瓷膜层表面粗糙度增大。
图5是4、5、6号试验参数所得到的陶瓷膜层表面SEM图像,它们的正向电压相同,均为400 V时,反向占空比各不相同。其中图5(a)为4号试验参数,即反向占空比40%生成的氧化陶瓷膜层,由图像可以看出,此时放电微孔孔径较小,且尺寸差异小,平均值约为1.10 μm,微孔数量多而密集,膜层表面无裂纹。图5(b)和图5(c)分别为5号、6号试验参数,反向占空比为30%和20%,明显出现多个孔径较大的放电微孔,不同微孔尺寸差异明显,相比图5(a),微孔数量明显减少,膜层表面出现多条裂纹,火山口状的熔融物沉积现象也更加明显。这与粗糙度测量所表现出的规律相一致,也与之前的理论分析结论相吻合。
(a) 40%
(b) 30%
(c) 20%
Figure 5. SEM images of film surface generated under different reverse duty cycle
图5. 反向占空比不同生成膜层表面SEM图像
另外,由表4中的极差分析可知:反向占空比为40%时,3组试验样品陶瓷膜层的粗糙度极差为0.201 μm,相对极差0.64,此时膜层粗糙度较低,相对变化也不大,受其他参数影响较小。反向占空比为30%时,3组试验样品的膜层粗糙度极差为0.689 μm,相对极差0.98,是整个表格中相对极差最大的,说明在该占空比参数下,其他电参数对试验样品陶瓷膜层粗糙度的影响显著增大。反向占空比为20%时,生成样品的陶瓷膜层粗糙度极差为0.639 μm,相对极差0.76,相比反向占空比为30%时的试验结果,相对极差减小,在增加氧化陶瓷膜粗糙度方面,更不容易受其他电参数影响,即该反向占空比值对膜层粗糙度影响程度更大。
5. 脉冲频率对膜层粗糙度的影响
利用表4的测量结果,对脉冲频率相同的试验,所得陶瓷膜层进行粗糙度的平均值、极差和相对极差分析,结果如表7所示。表4中1号、6号和8号电参数组合中频率设置相同,为200 Hz,试验样品陶瓷膜层的粗糙度平均值0.760 μm。2号、4号和9号试验中,频率设置为250 Hz,生成样品的陶瓷膜层粗糙度平均值为0.629 μm,相对频率为200 Hz的试验样品,陶瓷膜层平均粗糙度减小了0.131 μm,减小的比例为17.2%。3号、5号和7号试验中,频率设置为300 Hz,生成样品的陶瓷膜层粗糙度平均值为0.474 μm,陶瓷膜层粗糙度平均值减小了0.155 μm,减小的比例为24.6%。
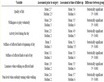
Table 7. Effect of pulse frequency on film roughness
表7. 脉冲频率对膜层粗糙度的影响
膜层粗糙度随脉冲频率的变化曲线如图6所示,在微弧氧化时间相同的情况下,随着试验脉冲频率增大,生成样品的陶瓷膜层粗糙度逐渐减小,但减小程度有所下降。经分析认为,当脉冲频率较小时,单次脉冲周期长,氧化陶瓷膜表面单次放电时间更长,能量更大,放电火花也更大,留下的放电微孔孔径较大,影响了陶瓷膜层表面的粗糙度;同时,更大的放电能量和更长的单次反应时间,使得火花放电喷出的氧化物熔融冷凝颗粒尺寸更大,因而膜层表面起伏较大,凸凹不平的情况更为严重,造成表面粗糙度变大;另外,由于单次放电能量高、周期长,使得反应温度更高、压强更大,反应过程中陶瓷膜层受到的热应力更大,可能导致膜层表面裂纹增多,裂纹长度和宽度增大,同样会造成陶瓷膜层表面粗糙度增大。当脉冲频率较大时,单脉冲周期短,放电能量少,反应剧烈程度会减缓,相应的放电微孔孔径、放电通道周围熔融物冷凝颗粒都会减小,裂纹情况也能得以改善。
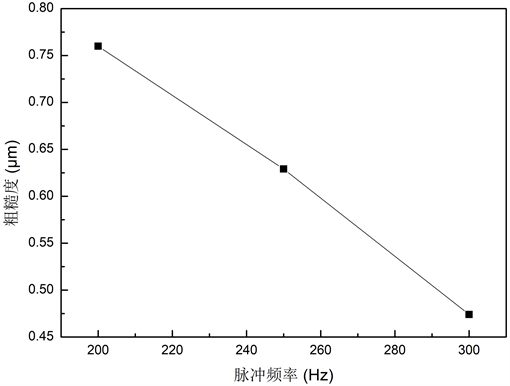
Figure 6. Effect of pulse frequency on film roughness
图6. 脉冲频率对膜层粗糙度的影响
图7是7、8、9号试验参数所得到陶瓷膜层的表面SEM图像,它们的正向电压相同,均为500 V时,反向占空比和脉冲频率都不相同。其中(a)为7号试验参数,即频率300 Hz生成的氧化陶瓷膜层,由图像可以看出,此时放电微孔孔径较小,且尺寸差异小,最大值为1.93 μm,微孔数量多而密集,膜层表面无裂纹。(b)和(c)的试验参数分别使用了8号、9号,脉冲频率分别为200 Hz和250 Hz,膜层表面明显出现多个孔径较大的放电微孔,不同微孔尺寸差异明显,相比图7(a),微孔数量明显减少,膜层表面出现多条裂纹,火山口状的熔融物沉积现象也更加明显。这与粗糙度测量结果所表现出的规律相一致,也与之前的理论分析结论相吻合,即频率降低会使得生成陶瓷膜层表面粗糙度增大。
由表7中的极差分析可知:脉冲频率为200 Hz时,3组试验样品陶瓷膜层的粗糙度极差为0.697 μm,相对极差0.92,此时膜层粗糙度平均值最大,但相对变化也较大,说明受其他参数影响较大。脉冲频率为250 Hz时,3组试验样品的膜层粗糙度极差为0.786 μm,相对极差1.25,在平均粗糙度降低的同时,相对极差却增大,其他电参数对该频率下试验样品陶瓷膜层粗糙度的影响显著增大。脉冲频率为300 Hz时,生成样品的陶瓷膜层粗糙度极差为0.523 μm,相对极差1.10,虽然平均粗糙度降低,但是相对极差仍然较大,该频率下膜层粗糙度仍然容易受其他电参数影响。由于3组数据反映出的相对极差都较大,说明膜层粗糙度受其他电参数影响程度较大,受频率的影响程度较小。
(a) 300 Hz
(b) 200 Hz
(c) 250 Hz
Figure 7. SEM images of the film surface generated with different pulse frequencies
图7. 脉冲频率不同生成膜层表面SEM图像
6. 不同电参数对膜层粗糙度的影响程度
通过计算同一水平因素下,所得样品粗糙度的相对极差,进一步分析各电参数对膜层粗糙度的影响程度,确定影响陶瓷膜层粗糙度的各个因素的主次。根据表5的数据计算可得,正向电压不同时,膜层粗糙度测量的极差为0.396 μm,相对极差为0.64,用Ra表示;根据表6的数据,计算反向占空比不同时,膜层粗糙度平均值的相对极差为0.85,用Rb表示;根据表7的数据,计算脉冲频率不同时,膜层粗糙度平均值的相对极差为0.46,用Rc表示。相对极差由大到小排列为:Rb > Ra > Rc,即三个因素中,反向占空比对微弧氧化膜粗糙度影响程度最大,其次是极间正向电压,脉冲频率影响最小。
7. 总结
本文通过电参数正交试验,研究了微小极间距条件下,电参数对7075铝合金微弧氧化膜层粗糙度的影响。研究发现铝合金微弧氧化陶瓷膜层粗糙度会随着两极间正向电压的增大而增大;当减小反向占空比,增大正向占空比时,生成陶瓷膜层也会粗糙度增大;随着脉冲频率减小,膜层粗糙度逐渐增大。通过相对极差分析发现,在三个电参数中,反向占空比对微弧氧化膜粗糙度影响程度最大。因此,在进行扫描式微弧氧化处理时,想要在提升材料其他表面性能的同时降低膜层粗糙度,应优先考虑增大反向占空比。