1. 引言
工程机械制造领域对钢材的强度和韧性要求越来越高,工程设计日益向轻量化、大型化等高参数化方向发展,如汽车起重机、载重汽车、泵车吊臂、推土机、挖掘机、农用机械、大型厂房结构等不胜枚举,这些领域都需高强度工程机械用钢。Q960E具有细晶粒、超洁净度、高均匀性、高强度和高韧性等良好的综合性能特征,需保证较高抗拉强度、伸长率、冲击韧性以及超声波探伤要求。
应用于重要部位的结构件一般需要良好的内部质量,而保证内部质量的方法大多采用超声波探伤的方式,在超声波探伤过程中各个中厚板生产厂家都会遇到探伤不合格的问题,表明钢板内部可能存在如分层、缩孔、孔洞、夹杂、白点、气泡、内裂、疏松、偏析及严重粗晶等缺陷 [1]。鄂钢中厚板产线自投产以来,Q960E钢板因探伤不合改判率较高,不仅造成经济损失,且影响合同兑现。
本文针对探伤不合钢板进行取样检测分析,探讨了造成钢板探伤不合的主要缺陷及其形成原因,并提出了改进措施。
2. 试验仪器
本文通过LME-2000低倍组织电解酸蚀装置对连铸坯进行检测,德国NDT在线自动超声波探伤装置对钢板进行无损探伤,对钢板缺陷部位取样后,使用Quanta 400扫描电子显微镜、Axio Observer.Alm光学显微镜以及SEM-EDS能谱分析仪对探伤不合格部位进行观察。
3. 生产工艺条件
Q960E钢板生产工艺流程为:KR脱硫→BOF冶炼→LF精炼→RH真空处理→板坯连铸→板坯加热→控制轧制→控制冷却→热矫直→空冷→精整(含探伤)→调质热处理→检验入库。Q960E的化学成分见表1。
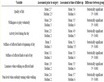
Table 1. Chemical composition (wt%)
表1. 化学成分(wt%)
4. 探伤不合原因分析
超声波探伤主要是利用超声波在不同介质中的声阻以及穿过钢板后透射率、反射率的差异,通过其反映在探伤示波仪上的波形来判断钢板内部质量的一种无损检测方法。本文重点分析Q960E钢板因中心疏松与偏析、非金属夹杂物、气体等导致的超声波探伤不合。
4.1. 铸坯中心疏松与偏析
由铸坯中心疏松与偏析引起的探伤不合比较普遍,如图1所示,此类探伤不合特点比较突出,从板面方向看缺陷遍布整块钢板,从板厚方向看,缺陷集中在钢板中心(板厚1/2处)部位。

Figure 1. Diagram of unqualified steel plate (center segregation)
图1. 探伤不合钢板图谱(中心偏析)
板坯普遍存在的问题是中心质量较差,而后续工艺也无法使在凝固过程中形成的中心缺陷得到较大的改善。铸坯凝固时,绝大部分连铸坯受到现有冶炼设备及工艺的限制,板坯中心必然存在不同程度的中心偏析,如果偏析严重(见图2),特别是含锰量高的Q960E钢,在钢板偏析部位就会产生异常组织(如马氏体或贝氏体),并在偏析带的异常组织上产生开裂 [2]。当板坯中心疏松比较严重有孔洞时,也会导致探伤不合。

Figure 2. Center segregation of Q960E cast billet
图2. Q960E铸坯中心偏析
从图3可以看出,钢板中心偏析带明显。在钢板的厚度中心因铸坯中钢水结晶凝固先后顺序不同产生成分偏析,中心位置的碳、锰含量升高,并导致钢板中心位置在轧后冷却时的CCT曲线发生右移。同时因为轧后冷却较快,在钢板心部易形成异常的过冷组织(如贝氏体、马氏体),过冷组织发生相变时应力集聚,当应力过于集中时,产生的组织应力集中在钢基体薄弱环节的一点释放形成裂纹,导致钢板探伤不合 [3]。
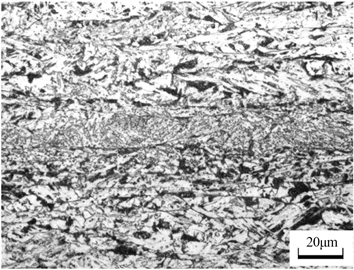
Figure 3. Local enlarged morphology of segregation band
图3. 偏析带局部放大形貌
连铸轻压下模式的压下区间、压下量等参数不当,辊间距大或设备对中状态不好等是产生偏析、疏松的主要原因。同时浇注温度过高、拉速高或波动大、二次冷却弱等也极易引起中心偏析。
4.2. 铸坯夹杂物
铸坯夹杂物引起的探伤不合从板面方向看,缺陷分布零散,从板厚方向看,缺陷集中在板厚四分之一及近表层位置(如图4所示)。

Figure 4. Diagram of unqualified steel plate (inclusion)
图4. 探伤不合钢板图谱(夹杂物)
分析认为,铸坯凝固时三角区的上部是夹杂物容易上浮聚集的位置,在铸坯的内弧1/4处易产生夹杂物的聚集。这些夹杂物极易造成钢板探伤不合,这是因为夹杂物与钢基体的弹塑性和热性存在差异,钢板在冷却过程中,萌生疲劳微裂纹,在轧制过程中微裂纹进一步扩展,形成细长裂纹,从而导致探伤不合 [4]。对Q960E钢板探伤不合部位进行能谱分析,发现缺陷处多种内生、外来夹杂物。
4.2.1. 内生夹杂
能谱分析如图5所示,可知主要为钙铝酸盐及CaS夹杂。这主要是由于脱氧、钙处理工艺不合理,以及软吹工艺控制不当,造成钙铝酸盐和CaS等复合夹杂物残留钢中。

Figure 5. Morphology, composition and size of inclusions (composite inclusions)
图5. 夹杂物形貌、成分和尺寸(复合夹杂物)
4.2.2. 外来夹杂
能谱分析如图6所示,外来夹杂物最主要的来源就是连铸保护渣卷渣,以开浇炉最为明显。连铸开浇升拉速阶段是个非稳态过程,保护渣熔化效果差,液面波动大,非常容易卷入钢中。这类外来夹杂物的特征就是能谱分析带有Na、K等保护渣特有的元素。

Figure 6. Morphology, composition and size of inclusions (foreign inclusions)
图6. 夹杂物形貌、成分和尺寸(外来夹杂物)
4.3. 钢中气体含量
对部分探伤不合钢板取样分析中还发现,钢中[H]在3~6 ppm,[N]在50~70 ppm,[O]在10~15 ppm,H含量明显过高。溶解于钢中的氢在液态钢中溶解度比固态钢中溶解度高,在钢水凝固过程中会析出,由于氢原子半径小,析出的氢原子在晶界或夹杂物界面扩散和聚集成氢分子,易造成缩孔、铸坯裂纹、皮下气泡以及中心疏松、偏析等缺陷 [5],未析出的氢在轧制冷却过程中积聚在钢材的显微组织缺陷处,引起高的内应力,形成穿晶断裂,由于应力集中,往往造成白点缺陷。白点是含Cr、Ni、Mo、Nb等合金元素钢和高碳钢易出现的缺陷,白点探伤不合格对于钢板自身的危害极高,由于应力集中,往往会造成钢板的开裂现象,影响使用。冶炼过程中精炼造渣材料、覆盖剂、合金潮湿,中间包烘烤不好会增加钢中氢含量。抽查板坯开浇炉第一块坯氢含量比连浇坯高0.7 ppm~0.8 ppm,当加入潮湿材料时,钢中氢含量可达5 ppm~8 ppm。
Q960E钢中添加了Ti,若钢中N含量高,会导致冷却过程中析出的TiN尺寸比较大,在轧制过程中,大型氮化物夹杂本身在界面处也易破碎而产生空洞,随着应力的增加,空洞互相连通形成微裂纹,最终导致探伤不合,见图7。如果能将钢中的N含量降到50 × 10−6以内,其TiN的析出温度在固相线温度以下,这时析出的TiN尺寸比较细小,对钢板质量的不利影响减小,甚至有益,因为它能阻止晶粒长大,细化晶粒 [6]。
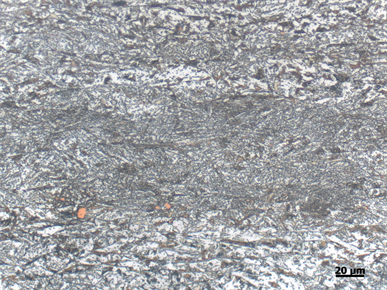
Figure 7. TiN inclusions of Q960E steel plate
图7. Q960E钢板TiN夹杂物
4.4. 轧制工艺的影响
单纯的偏析组织并不能造成探伤不合,当轧后钢板冷却速度过快,偏析组织处往往会形成马氏体或贝氏体组织,在热应力或组织应力作用下,偏析组织内产生大量细小裂纹,从而导致造成探伤不合。
5. 工艺改进措施
通过前文分析可知,造成Q960E钢板探伤不合的主要原因是连铸坯中心偏析、钢中夹杂物、气体含量高及轧制工艺不合理,因此,工艺改进措施重点在于减少连铸坯中心偏低、降低钢中夹杂物、气体含量以及优化轧制工艺。
5.1. 转炉冶炼
转炉冶炼尽可能降低钢中磷含量,如双渣脱磷,保证前期低温(约1350℃~1400℃)、高碱度(1.6~2.0)、高氧化铁,前期供氧采用软吹制度,底吹强度适当增加,前期一倒倒渣量为总渣量的二分之一,中、后期保证全程化渣,并保证碳–温协调,减少拉碳次数并防止后吹,实现前期脱P,保证终点高拉碳,以此提高出钢钢水质量。
5.2. LF精炼
钢包到站后,喂铝线将Als含量控制在0.010%~0.020%,防止测温和取样时爆吹,造成二次氧化。采用石灰 + 复合脱氧剂快速造白渣,效果较好,复合脱氧剂成分见表2。
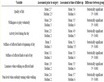
Table 2. Composition of compound deoxidizer (wt%)
表2. 复合脱氧剂成分(wt%)
白渣保持时间 ≥ 10 min,终渣成分CaO、SiO2、Al2O3、MgO、MnO + FeO含量分别按50%~60%、<10%、25%~30%、<8%、<1%控制,以保证高脱硫率和吸收Al2O3夹杂的能力。考虑到RH工序有一定铝损,LF结束时将钢中Als含量控制在0.030%~0.050%,确保钢水出站S含量 ≤ 0.003%。
5.3. RH真空
RH真正定义为“脱气站”,不允许微调成分,因每次微调成分(加合金)都是一个破空→抽真空的过程,不仅影响脱气效果,且导致真空周期延长,影响连铸稳态浇铸。RH真空度达到67 Pa后,保持时间在15 min以上,破空后进行钙处理。确保钢水中N含量 ≤ 50 × 10−6,H含量 ≤ 0.5 × 10−6。
5.4. 连铸
选用碱性覆盖剂充分吸收中间包上浮的有害夹杂物;采用合适的电磁搅拌工艺参数,消除中心裂纹,减少中心疏松;严格控制动态轻压下区间及压下量,并根据铸坯低倍检测结果修正轻压下参数。连铸坯下线后进行堆垛缓冷,充分消除应力,并使气体扩散。
5.5. 轧钢
为提高钢板探伤合格率,轧钢工序可用加热制度、轧制制度、冷却制度、钢板缓冷制度等方面改善铸坯带来的缺陷。
1) 加热制度:适当延长铸坯总在炉时间和提高铸坯出炉温度,控制铸坯加热速率9~12 min/mm,加强铸坯中心偏析元素的扩散;提高铸坯出炉温度,可确保铸坯中的Nb、Ti合金充分固溶,从而有效提高钢板的探伤质量。
2) 轧制制度:在轧制过程中,采用少道次大压下规程轧制,提高应力应变的渗透率,使粗大的柱状晶得以破碎,改善中心组织缺陷,形成细小均匀的晶粒,弥补铸坯缺陷对探伤的影响。
3) 冷却制度:优化钢板轧后冷却工艺,对于采用离线淬火工艺的Q960E调质钢,采用ACC弱冷工艺,合理调整上下水比,保证钢板均匀冷却,减少芯部异常组织的产生,降低钢板内部应力,防止钢板中微裂纹的产生。
4) 钢板缓冷制度:钢板轧后在300℃以上采用堆冷工艺,堆冷时间24 h以上。堆垛缓冷有助于钢板内部气体元素氢的扩散,还可使内部应力得到缓慢释放,以避免中心偏析带的马氏体和贝氏体组织区域因轧后冷却速度较快而产生微细裂纹,提高探伤合格率。
6. 结束语
铸坯中心偏析和疏松、内部裂纹、夹杂物富集、气体含量高以及轧后钢板冷却工艺不合理,是造成Q960E钢板探伤不合的主要原因。通过改进工艺操作,减少钢中夹杂物含量,提高钢水洁净度,同时采用合理的浇注制度,获得内部质量较高的铸坯,可以为提高探伤合格率提供好的条件;轧制过程中采取合理的加热制度、轧制制度、冷却制度以及热处理制度,也可以有效减轻铸坯质量带来的不利影响。通过采取以上措施,鄂钢Q960E钢板的探伤合格率稳定在99.5%以上。