1. 概况
失效连续油管信息见表1。2019年8月,该连续油管在泰国海上油田用于钻磨(Milling)时发生断裂,断裂时工况见表2。带断口的一侧连续油管于2019年10月送到中国石油集团石油管工程技术研究院,如图1所示。该连续油管要求参照API Spec 5ST-2010(R2015)《连续油管规范》中的CT90钢级进行检测分析。
现场提供的断裂失效前作业过程:早上5:45夜班监督在连续油管1367米处(鹅颈上)发现泄漏,此时POOH (Pull Out of Hole)状态悬重3765 kg (8300 lbs),接着RIH (Run in Hole)状态悬重1360 kg (3000 lbs),悬重减少。5:48,RIH状态悬重突然降到−1360 kg (−3000 lbs),保持泵压,连续油管继续下放23米,到1390米,关闭防喷器。连续油管压力900 psi,继续泵送。7:30白班监督施加拉伸,直至悬重4082 kg (9000 lbs),停止泵送液体,打开防喷器,悬重降到−454 kg (−1000 lbs),提拉连续油管到1373米(估计此时连续油管在防喷器上部断裂)。关闭防喷器。8:25打开防喷器。8:40发现连续油管断裂,掉井连续油管1367米 + BHA4.5米。
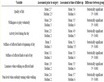
Table 1. The information of coiled tubing
表1. 连续油管信息
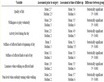
Table 2. Working conditions of fracture
表2. 断裂时工况
2. 实验方案
为找出失效原因,根据失效管材所处的服役环境(概况),结合管材特点特制定以下方案,如图2所示:
3. 实验设备
ARL4460直读光谱仪,SHT4106材料试验机,UH-F500KNI材料试验机,RB2002T洛氏硬度计,KB30BVZ-FA维氏硬度计,OLS4100激光共聚焦显微镜,扫描电子显微镜,超声波测厚仪。
4. 实验结果及结果分析
4.1. 宏观形貌分析
现场失效连续油管断口表面形貌如图3(a)所示;送到实验室时连续油管表面已锈蚀,如图3(b)所示。失效连续油管断口附近管体无明显塑性变形,部分断口外表面边缘向外凸出。断口附近外径和壁厚检测结果见表3。在断口附近外表面发现两条近似平行的凹痕变形,最宽4 mm,向管体延伸,逐渐消失,如图4(a)所示。其中凹痕1肉眼可辨识长度约30 mm,凹痕2在管体外表面肉眼可辨识长度约33 mm,延伸至断口,并继续沿断口延伸约20 mm,如图4(b)所示。凹痕1在断口处检测壁厚为2.35 mm,如图5(a)所示,截取块状试样检测凹痕2壁厚为2.0 mm,如图5(b)和图5(c)所示。断口附近大的沟状损伤如图6(a)所示。刮擦和切削损伤如图6(b)所示,变形形貌显示此处先被刮擦,又受到反方向切削。在邻近断口区域选取三个位置外表面圆弧检测轮廓,如图6(b)所示,结果显示圆弧2和圆弧3外径有明显变形,如图6(c)。
(a)
(b)
Figure 3. Fracture morphology of coiled tube. (a) Failure scene morphology; (b) Morphology in laboratory
图3. 失效连续油管断口形貌。(a) 失效现场形貌;(b) 实验室形貌
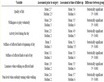
Table 3. Test results of outer diameter and wall thickness near the fracture (mm)
表3. 断口附近外径和壁厚检测结果(mm)
(a)
(b)
Figure 4. Indentation deformation near the fracture. (a) Two approximately parallel indentations; (b) A partial enlargement of dent 2
图4. 断口附近凹痕变形。(a) 两条近似平行凹痕;(b) 凹痕2局部放大图
(a)
(b)
(c)
Figure 5. Detection of dent tube thickness. (a) Detection of indentation 1; (b) The left side thickness of Indentation 2; (c) The right side thickness of indentation 2
图5. 凹痕壁厚检测。(a) 凹痕1壁厚检测;(b) 凹痕2断口左侧壁厚;(c) 凹痕2断口右侧壁厚
(a)
(b)
(c)
Figure 6. Obvious damage near the fracture. (a) Sulcus injury; (b) Scratch and cutting damage; (c) Outside diameter deformation
图6. 断口附近明显损伤。(a) 沟状损伤;(b) 刮擦和切削损伤;(c) 外径变形
4.2. 化学成分分析
在所送失效连续油管上取样,依据ASTM A751-14a [2],使用ARL4460直读光谱仪进行化学成分分析,结果见表4。样品化学成分分析结果符合API Spec 5ST-2010(R2015)对CT90的要求。
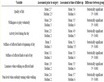
Table 4. Chemical composition analysis results (wt × 10−2)
表4. 化学成分分析结果(wt × 10−2)
4.3. 拉伸试验
在所送失效连续油管上截取全截面试样,依据ASTM A370-18 [2],使用SHT4106材料试验机进行试验,结果见表5。样品拉伸试验结果符合API Spec 5ST-2010(R2015)对CT90的要求。
注:屈服强度是按API Spec 5ST-2010(R2015)规定采用载荷作用下0.2%非比例伸长方法得到的。
4.4. 扩口试验
在所送失效连续油管上取样,依据API Spec 5ST-2010(R2015)规定方法,使用UH-F500KNI材料试验机进行扩口试验,结果见表6。样品扩口试验结果符合API Spec 5ST-2010(R2015)对CT90的要求。
注:扩口最小内径是依据委托方提供的连续油管规定外径38.1 mm (1.5 in)和规定壁厚3.2 mm (0.125 in)按API Spec 5ST-2010(R2015)规定计算得到的。
4.5. 压扁试验
在所送失效连续油管上取样,依据ASTM A370-18,使用UH-F500KNI材料试验机进行压扁试验,结果见表7。样品压扁试验结果符合API Spec 5ST-2010(R2015)对CT90的要求。
注:板间距离是依据委托方提供的连续油管规定外径38.1 mm (1.5 in)和规定壁厚3.2 mm (0.125 in)按API Spec 5ST-2010(R2015)规定计算得到的。
4.6. 洛氏硬度试验
在所送失效连续油管上取样,依据ASTM E18-19使用RB2002T洛氏硬度计进行洛氏硬度试验,结果见表8。样品洛氏硬度试验结果符合API Spec 5ST-2010(R2015)对CT90的要求。
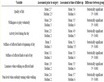
Table 8. Rockwell hardness test results
表8. 洛氏硬度试验结果
注:因为HRC硬度小于20,根据API Spec 5ST-2010(R2015)规定,改用HRB硬度进行试验。根据ASTM E-140,HRC22.0换算为HRB99.5。
4.7. 维氏硬度试验
在失效连续油管断口部位取1#、2#和3#试样,位置如图6所示,使用KB30BVZ-FA维氏硬度计在纵向剖面上进行维氏硬度试验,结果见表9。结果显示断口附近基体维氏硬度没有异常。
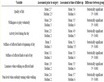
Table 9. Vickers hardness test results
表9. 维氏硬度试验结果
4.8. 金相分析
在所送失效连续油管断口部位取1#、2#、3#、4#、5#和6#试样,试样编号对应位置如图7所示,依据ASTM E3-11(2017)、ASTM E45-18a、ASTM E112-13,使用OLS 4100激光共聚焦显微镜对试样进行金相分析,结果见表10和图8~13。样品晶粒度分析结果符合API Spec 5ST-2010(R2015)对CT90的要求,焊缝未见宏观缺陷。

Figure 7. Schematic diagram of sample position
图7. 试样位置示意图
注:B-贝氏体,F-铁素体,P-珠光体。
图10~12右侧图为左侧图的局部放大。结果显示,1#、2#和3#试样断口附近组织明显有向外表面方向的弯曲变形;2#试样外表面有微裂纹;凹痕1 (图11)和凹痕2 (图12)处组织与管体其他部位表面组织无明显差异;6#试样距断口1 mm长度内组织有明显颈缩变形形貌,如图13所示,距断口更远处组织变形不明显。
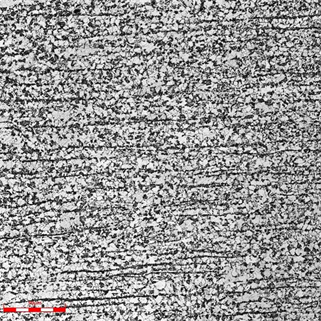
Figure 8. Metallographic morphology of pipe body (5#)
图8. 管体金相组织形貌(5#)
(a)
(b)
Figure 9. Weld morphology. (a) 1# morphologyaway from the fracture plate-plate weld; (b) 4# Longitudinal weld morphology
图9. 焊缝形貌。(a) 1#远离断口板–板焊缝形貌;(b) 4#纵向焊缝形貌
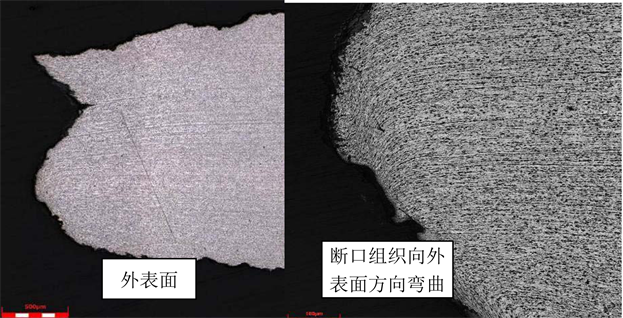
Figure 10. Microstructure morphology near fracture 1#
图10. 1#断口附近组织形貌

Figure 11. Microstructure morphology near fracture 2#
图11. 2#断口附近组织形貌

Figure 12. Microstructure morphology near fracture 3#
图12. 3#断口附近组织形貌

Figure 13. Microstructure morphology near fracture 6#
图13. 6#断口附近组织形貌
4.9. 微观分析
在所送失效连续油管断口部位取样1#、2#和3#,试样编号对应位置如图7所示。对截取的试样进行清洗,使用扫描电子显微镜对试样断口表面进行微观形貌观察,典型结果如图14。结果显示,断口
(a)
(b)
Figure 14. Typical morphology of fracture surface. (a) Fracture surface of sample 1#; (b) Fracture surface of sample 3#
图14. 断口表面典型形貌。(a) 1#试样断口表面;(b) 3#试样断口表面
表面锈蚀比较严重,已不能观察到原始形貌。对失效连续油管断口进行能谱分析,典型结果见图15~17,表11,表12。
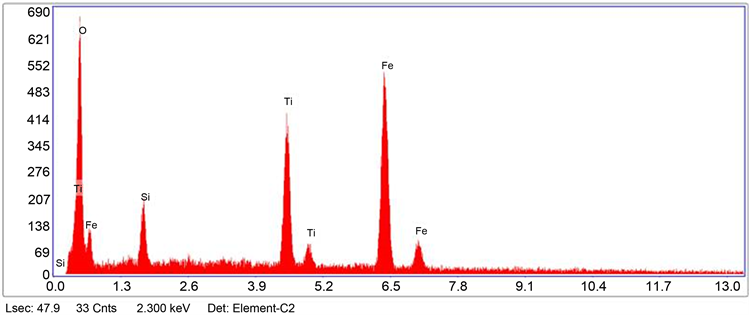
Figure 16. Typical energy spectrum analysis results of fracture site (region 1)
图16. 断口部位区域1典型能谱分析结果

Figure 17. Typical energy spectrum analysis results of fracture site (region 2)
图17. 断口部位区域2典型能谱分析结果
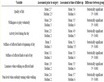
Table 11. Analysis results of region 2 energy spectrum
表11. 区域1能谱分析结果
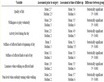
Table 12. Analysis results of region 2 energy spectrum
表12. 区域2能谱分析结果
5. 综合分析及结论
失效连续油管的化学成分分析结果符合API Spec 5ST-2010(R2015)对CT90的要求;拉伸试验、扩口试验、压扁试验和洛氏硬度试验结果均符合API Spec 5ST-2010(R2015)对CT90的要求;晶粒度分析结果符合API Spec 5ST-2010(R2015)对CT90的要求。
从宏观形貌分析和金相分析结果可以看出,失效连续油管断口部位局部存在弯曲变形。断口部位损伤较为集中,壁厚减少,最薄位置壁厚约1.5 mm。连续油管断裂原因分析如下:
1) 壁厚整体减少。失效连续油管无明显损伤部位实测壁厚为2.42~2.66 mm。根据现场提供信息,断口部位规定壁厚为3.2 mm。
2) 断口部位多处损伤。较严重损伤包括一条沟槽状损伤,两条凹痕,及一处切削。其中切削损伤处最小壁厚为1.5 mm左右,不到规定壁厚的一半,圆周方向宽约10 mm。凹痕2壁厚为2.0 mm,为规定壁厚(3.2 mm)的62%,总长度53 mm,约圆周长的44%。凹痕1可见长度30 mm,在断口另一侧连续油管上继续延伸,总长度未知。附近管体实测壁厚为2.4~2.6 mm,局部几何尺寸变化也会产生应力集中 [3]。
3) 局部弯曲变形。断口部位多处损伤,壁厚减少且分布不均匀,局部壁厚不到规定壁厚的一半,断口附近连续油管强度和刚度均降低,受压缩载荷作用时局部出现弯曲变形,再次受到拉伸和弯曲等复合载荷作用,应力分布不均匀。在连续油管弯曲变形位置容易产生应力集中,附加弯曲拉伸应力后总拉伸应力较高,超过材料强度而开裂,在压缩和拉伸交互应力作用下连续油管最终断裂。
综合以上分析,连续油管断裂的原因是壁厚整体减薄,外表面多处损伤且相距较近导致断口附近壁厚严重减薄和局部弯曲变形。