1. 引言
随着金属基复合材料的发展,铝、镁、钛、铜、铁、金属间化合物及难熔金属基等多个金属基系都能够作为复合材料的基体,而铝基复合材料是金属基复合材料中应用最广的一种 [1]。目前,纤维增强和颗粒增强铝基复合材料发展迅速,有了许多的成果,而颗粒增强铝基复合材料相比较纤维增强铝基复合材料而言,具有突破性 [2] [3] [4];颗粒增强铝基复合材料的颗粒增强体成本较低,并且克服了制备过程中出现的纤维损伤、微观组织不均匀、纤维与原位纤维相互接触、反应带过大等影响复合材料性能和质量的问题 [5] [6] [7],由于颗粒增强铝基复合材料综合性能良好,有较高的比强度、比模量,用作高性能结构材料,可提高结构安全性,或优化结构设计已在国防与航空航天工业、汽车工业、电子领域、运动器材等方面得到广泛的应用 [8]。
2004年,日本宇航科学研究所的研究员北园等 [9] 在斋藤等的基础上,对工艺进行改进,首次将颗粒SiC置于Al板之间,并进行循环的叠轧–剪断处理–叠轧。经过诸多专家和研究员的探索可知,利用ARB法制备颗粒增强复合材料具有一定的可行性。
目前,颗粒增强铝基复合材料成为研究热点。碳化钛(TiC)是面心立方点阵,具有很高的化学热稳定性,用做金属陶瓷,具有高硬度,高模量,较高抗弯强度,耐腐蚀、热稳定性好等特点 [10] [11]。已有的研究表明,TiC和Al基体相容性好,能够对原基体材料的硬度等力学性能有显著提升,且耐磨耐蚀性能好,远高于基体金属的耐磨损耐蚀性能,对于铝或者铝合金是理想增强体材料。在此基础上,本论文采用颗粒增强铝基复合材料,增强相选择氮化钛(TiN)颗粒,TiN粉末为黄褐色,超细TiN粉末呈黑色,密度为5.43 g/cm3,熔点高,TiN是面心立方点阵,其中钛原子位于面心立方的顶角,晶体结构与TiC晶体结构相似,只是将C原子换成N原子,因此,TiN作为增强体,对基体材料具有与TiC相类似的增强功能,同样是一种理想增强材料 [12] [13] [14] [15],可得到具有优良的综合性能的复合材料。
2. 实验部分
2.1. 实验材料
以工业纯铝箔为原材料,其中铝的含量99.99%,尺寸为200 mm (L) × 100 mm (W) × 0.2 mm (T),以TiN颗粒为增强相,平均粒径为2微米。
2.2. 实验仪器
实验制备铝基复合材料轧机参数:电机转速为147 r/min,两辊轧制速度为15 m/min。
试样镶嵌机:XQ-1金相试样镶嵌机(220 V, 650 W)。
金相显微镜规格参数:WMJ-9638系列倒置金相显微镜。
2.3. 测试与表征
在ARB处理之前,采用600#SiC砂纸把实验用的铝箔表面研磨处理,排除其他条件的干扰和进行初步脱脂;之后将铝箔折叠,再分别用酒精和丙酮对铝箔进行脱脂,然后将铝箔放置在指定处干燥,对实验所使用的不锈钢封套,也同样用酒精和丙酮处理,再将光洁面折叠,用轧机压好制成不锈钢封套以备用。本次实验采用TiN体积分数分别为15%、20%、25%、30%。实验中TiN和Al的所选质量如表1。用天平分别称量好处理后铝箔的质量以及所需配比增强相TiN颗粒的质量,再把增强相均匀地洒在铝箔中间,并将含有TiN颗粒的铝箔的三个开边进行折叠,把含有TiN颗粒的铝箔夹在不锈钢封套内,便于ARB加工过程中的均匀变形。用精度为0.02 mm的游标卡尺,测量不锈钢封套和样品的总厚度,再将轧机两滚轮之间的间距调整好(即每道次的压下量),控制每道次的压下量大约为不锈钢钢套和样品总厚度的50%,将样品放入轧机两滚轮之间。然后将钢套取出,进行剪断–表面处理–叠轧循环的工艺,使材料不断叠轧焊合,进行大约20次的循环(轧制的次数根据实验目的可以有所变动),便可得到实验所需的样品。轧制完成后的TiN/Al复合材料样品,采用热镶法对样品镶嵌,分别按垂直轧制方向截取横截面试样,平行轧制方向截取纵截面试样。对相应的试样进行金相观察。
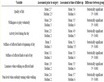
Table 1. Weight of TiN and Al in TiN/Al Composites with different volume fraction
表1. 不同TiN/Al复合材料中TiN和Al的成分
3. 结果与讨论
3.1. 微观组织
3.1.1. TiN/Al复合材料横纵截面的微观组织
图1显示了体积分数为15%、轧制道次为20道次,且在相同切割断面处截取的TiN/Al复合材料样品,其在横、纵截面上的金相图。从图中可以看出:a、c中的黑色块较少,b、d中的黑色块较多且分布有较大块的白色物质,黑色块为孔洞,横截面上有一定数量的孔洞分布,但可以清楚地看到,没有出现TiN和Al箔的层状复合材料,TiN颗粒已均匀地分布在铝基体中,形成了TiN颗粒增强Al基复合材料。
3.1.2. ARB工艺关于轧制次数对材料微观组织的影响
体积分数为30%的TiN/Al复合材料,分别截取不同截面样品金相如图2。
通过图2发现,随着轧制道次的增加,在金相下观察到白色块和黑色块慢慢减少,白色块和黑色块也从大团聚状慢慢的变为小团聚状,而在金相视图下存在有大块白色的物质,这一部分是未能和增强相颗粒充分结合的铝基体,也在变少;同样随着轧制道次的增加,在轧辊的作用下,通过压力和热能的作用,使得TiN颗粒和铝充分结合,团聚的TiN逐渐弥散分布在铝基体中,与铝紧密结合一起,形成颗粒分布均匀且细小的TiN/Al复合材料;但是,当轧制道次过多时,发现复合材料表面开始出现裂纹,最后导致崩碎成很小一块的复合材料。在图d中可以看到,复合材料组织细密,不存在微小孔洞和明显缺陷,增强相TiN分布均匀,团聚状少,TiN颗粒明显,与图2中a、b、c有明显区别。
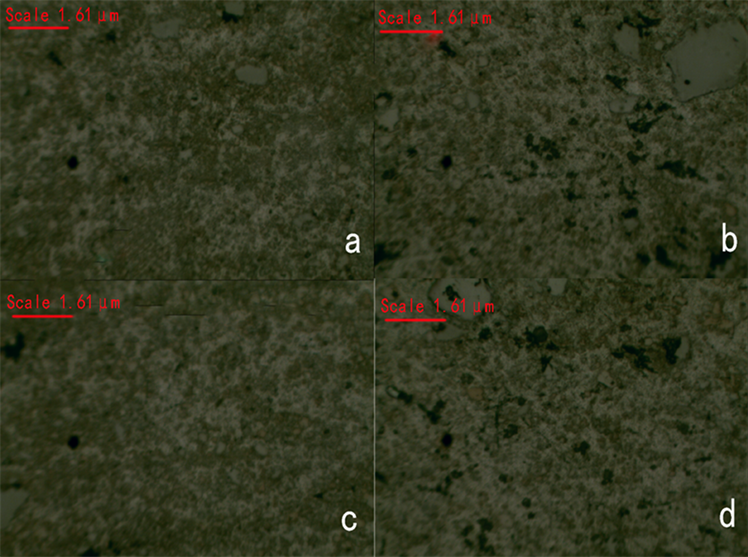
Figure 1. Metallographic micrographs of composites with volume fraction of 15% TiN/Al: longitudinal section a, c; cross section b, d
图1. 体积分数15%TiN/Al复合材料的金相显微图:纵截面a、c;横截面b、d
由此可以发现:ARB工艺制备的复合材料,在复合材料的轧制过程中,轧制道次不仅通过影响材料中TiN颗粒的分布进而影响其性能,并且对其组织的致密性,同样有着重要作用。在一定的成分许可轧制范围内,轧制道次越多,复合材料的增强相颗粒也会分布越均匀,增强相颗粒与金属基体结合程度也越紧密,在轧制过程中,细化晶粒效果也越明显,晶粒也越细,得到超细晶也越多,原有层状铝箔也会逐渐消失,从层状复合材料转变为颗粒增强复合材料。
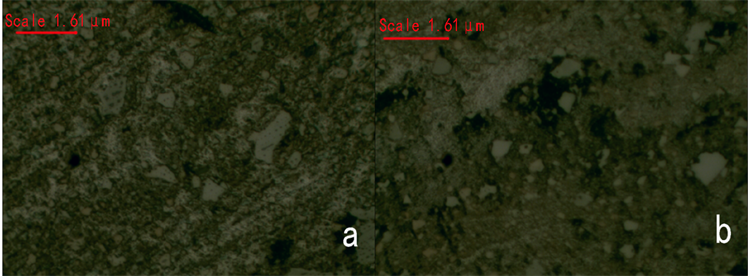
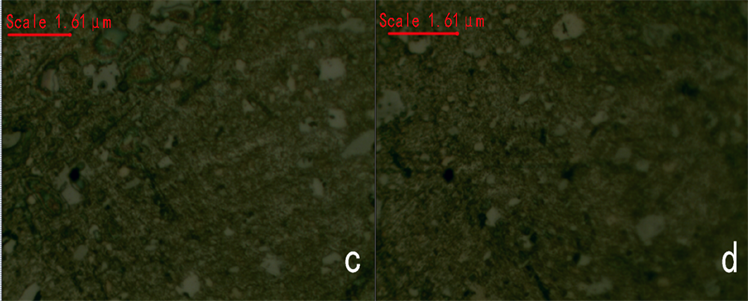
Figure 2. Micrograph of the TiN/Al composite: a Rolling 25 passes; b Rolling 30 passes; c Rolling 35 passes; d Rolling 40 passes
图2. TiN/Al复合材料的横截面金相显微图:a轧制25道次;b轧制30道次;c轧制35道次;d轧制40道次
3.1.3. 强化相TiN体积分数对材料微观组织的影响
在同样是20次的轧制次数下,图3,图4是不同体积分数的TiN/Al复合材料横、纵截面金相图。根据图3,图4,里面有四种相:大块的白色物质、具有一定规则的白色物质、黑色物质和棕色物质,分别为基体金属——铝、团聚TiN脱落后嵌入的镶嵌粉、团聚TiN脱落后的凹孔和被基体金属紧紧包裹的TiN颗粒(这也是复合材料主要的部分,其性能好坏的主要决定者);通过图3,图4可以发现:在体积分数为15%时,图a白色物质、黑色的较少,但有大块的铝基体,TiN颗粒明显且分布均匀;而体积分数为20%的图b中,开始出现大量的团聚物和凹孔,并且TiN颗粒不太明显,同样还存在少量的铝基体;在体积分数为25%的图c中,团聚物开始大量增多且凹孔开始变大,能明显看到增强相,而金属基体铝也大大减少;在体积分数为30%的图d中,白色物质增多,凹孔开始减少,金属基体铝基本不再出现。由此发现:基体金属与强化相的结合程度需要一定的轧制道次和一定的体积分数,体积分数越高,基体金属与增强相的结合机也会增多,分布也更均匀,但所需要的轧制道次也会相应增加,以保证复合材料的优良综合性能。
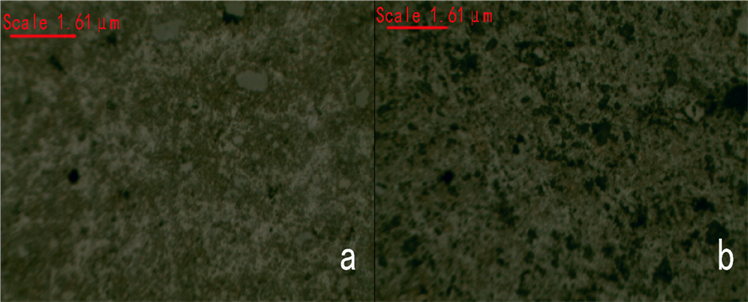
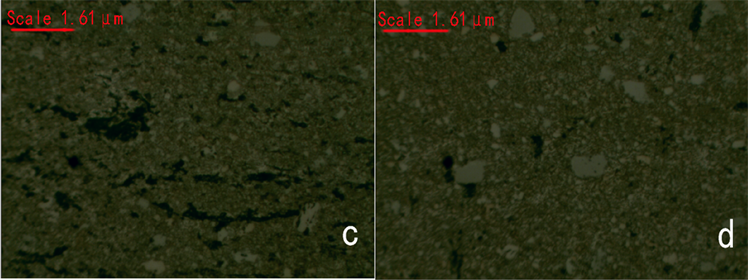
Figure 3. Metallographic micrograph of distribution ratio of TiN/Al composite cross section: volume ratio a 15%; b 20%; c 25%; d 30%
图3. TiN/Al复合材料横截面成分配比金相显微图:体积比a 15%;b 20%;c 25%;d 30%
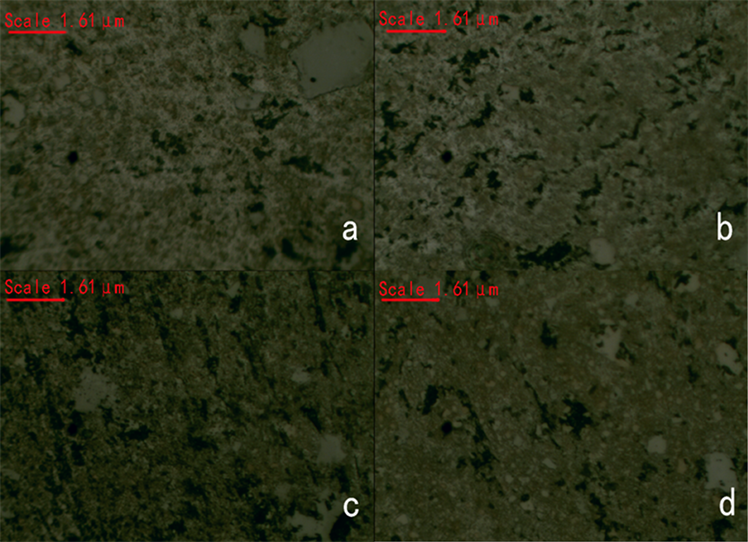
Figure 4. Metallographic micrograph of distribution ratio of TiN/Al composites: volume ratio a 15%; b 20%; c 25%; d 30%
图4. TiN/Al复合材料纵截面成分配比金相显微图:体积比a 15%;b 20%;c 25%;d 30%
3.2. 力学性能
3.2.1. TiN/Al复合材料的维氏硬度
其他条件均相同、轧制道次不同的体积分数为30%TiN/Al复合材料横、纵截面维氏硬度见图5。在图5中可以看到,两个截面的硬度值都比较接近,且硬度值都较高,而铝的维氏硬度为20 HV,体积分数为30%的TiN/Al复合材料,相对于原基体材料铝来说,TiN颗粒增强铝基体的效果显著,随着轧制道次的增加,TiN/Al复合材料的维氏硬度也在不断增加,从轧制道次为25次的5倍,30次的6倍,35次的7倍,最后40次约为基体材料铝的维氏硬度的9倍,可以看出少量的高硬度颗粒增强相,能够对原基体材料的硬度有很大的提升。
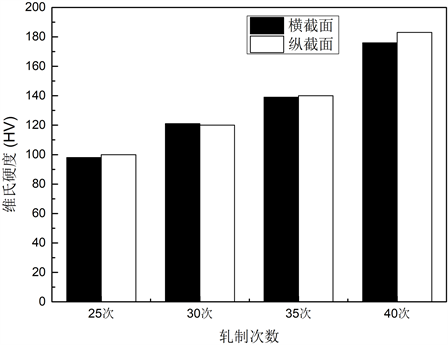
Figure 5. Vickers hardness of TiN/Al composites with different rolling rolling passes
图5. 轧制道次不同的30%TiN/Al复合材料横、纵截面维氏硬度
图6是在20次轧制道次下,体积分数分别为15%、20%、25%、30%的TiN/Al复合材料维氏硬度图。从图6中可看出,当体积分数分别为15%、20%、25%、30%时,其硬度值与纯铝相比较,分别增强376.5%、437.5%、491.25%、616.5%;且呈抛物线,并不是线性关系。随着成分配比的增加,轧制道次也应有一定的增加,而在这组实验控制的不变量是轧制道次,变量是成分配比,因此,成分配比为25%与30%的复合材料中的TiN颗粒与铝基体结合程度没有另两种的紧密,这也从侧面论证了上述的结论。同时,在成分配比为25%时,在金相下看到出现了许多的团聚状TiN,但“团聚”易引起颗粒分布不均匀,严重影响复合材料的性能,在实验原始数据中,成分配比为25%的波动较大;而在成分配比为30%的复合材料中,团聚较少;“团聚”状物质在一定的程度上对复合材料的硬度有一定的影响。
3.2.2. 强化机制
在金相显微镜下观察到的金相图也展示了随着轧制道次的增加,其微观结构也在逐渐变得清晰、颗粒分布逐渐均匀和其他相逐渐减少(其他相指的是在后续处理过程中嵌入的镶嵌粉和掉落的TiN颗粒),随着轧制道次的增加,一次次的轧制,会使得晶粒不断细化,TiN颗粒在之前轧制时,一些部位出现的弥散团聚现象,也会得到改善,逐渐消除团聚TiN。而ARB工艺也是一种使材料强烈塑性变形,改善材料性能的工艺,在晶粒不断细化的情况下,细化后的组织,生成更多的晶界,阻碍位错的运动,导致位错密度的增加,增大了塑性变形的流变应力。于是微观组织就变得清晰,也提高了材料的硬度。而在轧制道次足够多的条件时,内部缺陷逐渐消失,而ARB是强烈的塑性变形,能够细化晶粒,获得超细晶,在晶粒细小且分布均匀时,继续轧制会使晶粒继续伸长,晶粒就会变得特别细小,此时又在外力作用下,细长的晶粒会开始出现裂纹、细孔等缺陷,当足够多的晶粒出现缺陷时,而与轧辊接触部位的压力承受较大,从外而内的开始在表面出现缺陷,最后变成非常细小的块状复合材料。
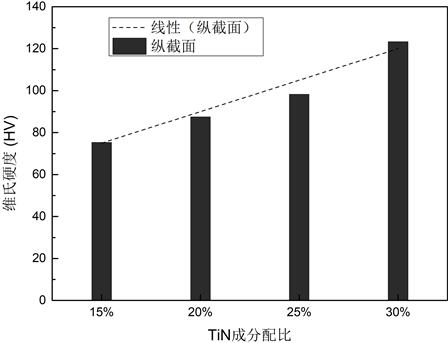
Figure 6. Vickers hardness of TiN/Al composites with volume fraction of 15%, 20%, 25%, 30%
图6. 体积分数为15%、20%、25%、30%的TiN/Al复合材料维氏硬度
除了轧制道次对样品性能会产生很大的影响外,增强相TiN颗粒的体积分数也会对样品的性能产生很大的影响。在除了体积分数不同、其他条件均相同的情况下,通过ARB制备出的TiN/Al复合材料样品中,样品的TiN颗粒体积分数增加,其硬度也相应有一定的提升,但是金相显微镜下观察到的微观组织分布变得暗沉,并且也会有一些团聚TiN增加。
如果体积分数增加时,对其轧制道次也相应增加,晶粒弥散分布得到改善,使得结合更紧密,晶粒也会不断地得到细化,显微组织和力学性能也会得到一定的改善。
4. 结论
本文以铝箔和TiN颗粒为原料,采用累积叠轧焊(ARB)的方法,制备了TiN颗粒增强的Al基体复合材料。对制备的TiN/Al复合材料微观结构和复合材料的力学性能进行分析,得出下述结论:
1) 通过ARB工艺成功地制备出体积分数为15%~30%的TiN/Al复合材料。
2) 通过ARB工艺制备的体积分数为15%的TiN/Al复合材料大约需要轧制20道次、体积分数为30%的TiN/Al复合材料大约需要轧制40次,最后得到增强相分布均匀、晶粒细小、具有性能良好复合材料,其余体积分数在两者之间的需要20~40道次不定,随着体积分数的增加,轧制道次也应该相应增加。
3) 制备出的TiN/Al复合材料硬度有很大的提升,随着TiN体积分数的增加而增加,当TiN体积分数为30%时,可提高至纯铝维氏硬度的9倍。
基金项目
本工作得到了武汉轻工大学大学生科研项目支持。