1. 引言
MOX燃料(钚铀氧化物混合燃料)芯块是MOX燃料组件的重要部件,目前在钠冷快堆中使用氧化物型的燃料,为贫氧化铀(UO2)与氧化钚(PuO2)的混合氧化铀钚陶瓷燃料,是我国核工业发展的重要核燃料之一 [1] 。目前我国对MOX燃料芯块的研究日益增多。
目前国内外对于工件磨削大部分采用湿磨法,在磨削过程中充分加入冷却液,降低磨削温度,带走磨削渣,改善磨削条件。由于MOX燃料芯块采用湿磨法存在临界安全控制、废液处理等问题,因此不能像普通材料一样采用湿磨法加工。现在我国首次采用无心干磨法对模拟MOX燃料芯块进行磨削加工试验,采用树脂金刚石砂轮磨削硬脆难加工的陶瓷材料是目前最适宜的加工手段。无心磨床采用连续加工,无需退刀,装夹工件等复制时间短,生产率高。MOX燃料芯块属于核燃料,具有强烈的放射性,因此磨削后的粉尘更不能有任何泄露,对除尘效率,粉尘收集等方面有特殊要求。由于目前我国没有在MOX燃料芯块磨削除尘方面的试验应用,为此,设计出一种脉冲反吹工业集尘器,应用于模拟MOX燃料芯块干磨实验室的除尘中,可以将生产线0.3 μm以上的颗粒物吸收达到99%。普通滤布为介质的布袋式除尘器易发生形变,清灰死角大,吸尘效率低。该除尘器过滤介质采用进口材料,变形性小,利用反吹技术,对滤筒灰尘可无死角清除,根据材料特性,可以针对不同粒径的粉尘进行有效过滤。整个实验室二次密封,所有设备没有特殊情况可以连续工作数年,减少工作人员的辐射损伤,原理简单易行成本低,对核燃料生产线的除尘有巨大意义。
2. MOX芯块粉尘特性分析
除尘器选型和除尘系统设计主要依据粉尘的物化性质,粉尘粒度分布,气流的特性,以及对除尘系统的要求。对除尘系统的要求主要有尘源特征、管道及除尘设备布置要求、设备维护要求、经济性指标等诸方面。
MOX陶瓷燃料熔点高、热稳定性好。但是密度低,质硬而脆,不易加工,热导率小。快堆MOX燃料与水堆MOX燃料在性质上是截然不同的,主要反映在快堆MOX燃料芯块的钚含量远远高于水堆,芯块尺寸十分小并且可能存在中心孔,此外在杂质含量、密度等方面的要求也与水堆不同 [2] 。
本次生产线磨削的是快堆的模拟MOX燃料芯块,国外调研的MOX燃料芯块粉尘各项参数如下:
粉尘外观:呈颗粒状;
粉尘热导率:λ = 1/(3.13 + 0.026·T);
粉尘熔点:2976 K;
粉尘线膨胀系数:8.3 × 10−6/K (25℃~600℃);11.0 × 10−6/K (600℃~900℃);
放射性:强;
化学性质:氧化物,性质较稳定,难以燃烧和爆炸。
粉尘与除尘工程密切相关的属性还包括悬浮性,扩散性,粘附性,燃烧性,爆炸性,粉尘的浓度,粒度等。一般机械加工过程中的粉尘浓度分布,受不同加工条件下产生的粉尘数量和质量、室内换气率、房间容积、通风装置、气流状态等因素影响。切削运动引起的气流运动模式主要影响粉尘浓度的空间分布模式,机械加工产生的粉尘总量影响浓度分布的大小。切削速度是影响粉尘浓度分布的重要因素,随着切削速度的增大,粉尘浓度空间分布的变异系数减小。
从微观的角度来看,切削产生细微粉尘由以下几个部分组成(图1):① 剪切带内的剪切活动对材料的挤压引发塑性变形产生一部分粉尘(P1);② 在切屑的成形过程中,切屑的变形产生另外一部分粉尘(P2);③ 切屑在前刀面的滑移将经历第二次变形和摩擦,导致一部分粉尘的产生(P3);④ 磨粒在新切表面的擦动产生的更多粉尘(P4),并且在磨削开始时和磨粒发生磨损时粉尘量会增加。如果有积屑瘤产生,积屑瘤破裂排出时会产生第二次摩擦损耗,因此产生更多的粉尘 [3] 。
3. 除尘器选型
除尘技术基本类型分为机械式除尘技术、电除尘技术、湿式除尘技术和过滤除尘技术,现在逐渐发展起来的还有电袋复合式除尘器,电旋风除尘器等复合式除尘技术。
过滤除尘技术利用多孔介质,当含尘气流通过多孔介质时,粒子黏附在介质上,而与气体分离。过滤式除尘器,又称空气过滤器,是使含尘气流通过过滤材料将粉尘分离捕集的装置。在过滤式除尘器中,袋式除尘器的除尘效率最高,捕集粒径范围最大,能适应高温、高湿、高浓度、微细粉尘、吸湿性粉尘、易燃易爆粉尘等不利工况条件。因此,它的应用范围最为广泛。但是它需要定期更换滤袋,由于滤料的品种少,质量欠佳,缝袋技术不太过关。在高温,烟气腐蚀性强的工况条件下,滤袋寿命短,增加了运转费用和维护工作量 [4] 。
脉冲反吹工业集尘器主要利用过滤除尘技术,具有风量大、脉冲反吹、稳定可靠、整体体积小,移动灵活等特点,它采用三级过滤除尘,除尘效率高。本机器可适用于粉尘量很大的漂浮、悬浮粉尘收集与处理。集尘器使粒度细、密度小的尘粒则在气流通过滤筒时被过滤效果高达99%的滤筒过滤,截留在滤筒表面,并被脉冲反吹结构反吹落入灰斗内,净化后的气体进入净气室由集尘器右侧风机室的排风口重新排放到车间里。原理如图2所示。
3.1. 一级扰流沉降
工程上常用重力,惯性力,离心力等机械力来捕集分离粉尘颗粒。最早用来捕集分离粉尘颗粒的机械力是重力,对于某特定粒径d的粉尘颗粒,其除尘作用的重力,即捕集分离的作用力与重力加速度成正比,但是打算改变g实现增大fg显然不可取。随着人们生产实践和对科学理论的深入,人们使含尘气流绕障碍物做旋转运动可以产生另外一种机械力,即以离心力形式表现出来的惯性力,这种惯性离心力比重力大100倍到1000倍 [5] 。若气流绕障碍物的圆周切向分速度为u,则离心加速度
,r为回
转流线的曲率半径,这样粉尘颗粒得到的除尘作用力
。使气流绕障碍物旋转运动,实际上就是利用了含尘气流速度矢量方向的改变。
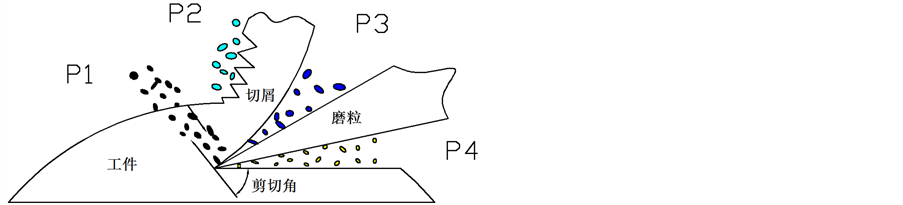
Figure 1. Composition diagram of cutting dust
图1. 切削粉尘组成图
一级过滤在进风口处加装扰流板,使进入过滤单元的大颗粒粉尘直接掉入灰斗内,粉尘通过吸入口捕集进入集尘器后,含尘空气从集尘器的进风均流装置进入过滤室,首先碰到进风口中间的扰流板,由于气流断面突然扩大及在扰流板的作用下,气流中一部分粗大颗粒直接沉降至灰斗,起到预除尘效果,无须再加前置旋风装置等大颗粒飞溅火花捕集器,降低整套设备的投资和运行费用,且使到达滤筒表面的过滤风速降低,增加过滤效果。过滤室结构如图3所示。
3.2. 二级反吹过滤
3.2.1. 滤筒选型
二级过滤要求可以吸收过滤99%以上直径在0.5~1 μm的粉尘颗粒。采用高效抗静电镀铝型过滤筒,圆筒利NION无纺布过滤材料,采用进口基布,有良好的机械耐受性能和抗磨损能力,经过环保局严格检测,对0.3 μm颗粒过滤效率为99.10%,0.5 μm颗粒过滤效率为99.51%,1 μm以上颗粒过滤效率为100%,经过专业检测,具体参数如表1所示。圆筒褶皱式设计增大了滤筒过滤面积,在保证安全防静电的基础上,提高过滤效果,对1 µm以上的粉尘过滤效率达99%以上。单个滤筒过滤面积为11 m²,在保证过滤面积的基础上,大大减少了机器占地面积,且采用立式安装可有效避免粉尘堆积导致的滤筒面积损失及危险系数的提高。
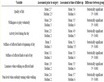
Table 1. Performance parameters of base cloth
表1. 基布材料性能参数
3.2.2. 脉冲反吹结构
滤筒的清灰方式可以采用脉冲电磁阀连接螺旋喷嘴脉冲反吹,工作压力为0.4~0.6 MPa,连接气源即可使用。防爆脉冲电磁阀由脉冲控制仪自动控制,可自由调整脉冲宽度和时间间隔,使清灰效率更高、更彻底,以保护滤筒的使用寿命。电磁脉冲阀采用双膜片结构,控制灵敏,效率高。
常规的直通喷嘴在进行脉冲反吹清灰的基本过程中,只有靠近滤筒底部的粉尘被清理,上面2/3区域是没有被清理干净的,经过多次喷吹靠近滤筒上部1/3区域仍是清理盲区。为了解决清灰盲区,根据专利“集尘器自动清灰系统的脉冲式反吹装置”和“一种旋转式脉冲反吹装置”,最终采用90度螺旋喷嘴来取代市面常见的直通喷嘴,在进行一次清灰过程后,整个滤筒粉尘都被一定程度的清理,其清灰面积基本可以覆盖整个滤筒,且清灰效率也更高。脉冲反吹结构如图4所示。
连接至气缸的压缩空气需经油水分离器预过滤,以保证喷吹到滤筒上的气流干燥无杂质,同时在气
缸上设安全排气阀,必要时及时排空气缸中压缩空气,在保证安全的基础上,增加滤筒的使用寿命。防静电镀铝型滤筒上外接引出一条导线,用于将静电引出接地,且滤筒的安装方式采用垂直立式,避免粉尘堆积导致的滤筒面积损失及危险系数的提高。
脉冲反吹系统由气缸、电磁脉冲阀、脉冲反吹控制仪、压缩空气组成。工作时,脉冲阀的一端连接压缩空气储气缸,另一端连接电磁脉冲阀。排气阀由脉冲反吹控制仪控制。当脉冲反吹控制仪无信号发出时,排气阀的活动挡板处于封闭排气孔的位置;当程序控制仪发出信号时,活动挡板打开,储气缸的压缩空气迅速泄压,于是排气阀内部的波纹膜被压向相反方向,喷气口打开,压缩空气经脉冲阀进入滤筒进行喷吹清灰。当信号消失后活动挡板恢复至原来封闭排气阀的位置,波纹膜重新封闭喷气口,喷吹自动停止。每次喷吹清灰在0.1~0.2 S左右完成,就是这一瞬间喷出的高压空气起到良好的清灰效果,使附在过滤筒的粉尘被抖落,滤料表面吸附的微尘在气流作用下被抖落至集尘斗中。脉冲喷吹气压为0.4~0.6 Mpa,且运行中须保持恒定不变的供气量。反吹原理如图5所示。
3.2.3. 粉尘收集结构
在灰斗下的自动卸料阀可满足粉尘料大、净化器需连续运行的工况,其工作平稳可靠、卸料均匀准确、体积小、密封性能好、维护方便、使用寿命长。其转速为24 r/min,每转4 L,卸料能力96 L/min,卸灰阀需定期加机油保养,确保卸料阀正常工作,周期为半年至一年。
粉尘收集采用独特的连续套袋结构,独特的连续套袋装卸方便,套袋由管状塑料袋折叠,可以连续拉扯,每一套粉尘收集袋的长度是22米,约可以连续使用25次。粉尘收集袋的材质为聚乙烯(PE),聚乙烯薄膜,轻盈透明,具有防潮、抗氧、耐酸、耐碱、热封性优异等性能。关于设备的检维护,为了防止放射性材料的粉尘外溢,对人体造成伤害,同时避免检维护时破坏其他零部件,我们在设备箱体部分设置了手套箱,并提供足够空间供工作人员修整。
3.3. 三级小粒子过滤
三级高效过滤器放置于机器顶部,主要用于捕集0.5 um以下的颗粒灰尘及各种悬浮物,作为各种过滤系统的末端过滤。采用超细玻璃纤维纸作滤料,胶板纸、铝箔板等材料折叠作分割板,新型聚氨酯密封胶密封,铝合金型材为外框制成。当经过滤筒一次过滤后的洁净气体再次通过高效过滤器时,气体中的那些杂质就会被过滤掉,从而达到保证过滤效果的作用。实物如图6所示。
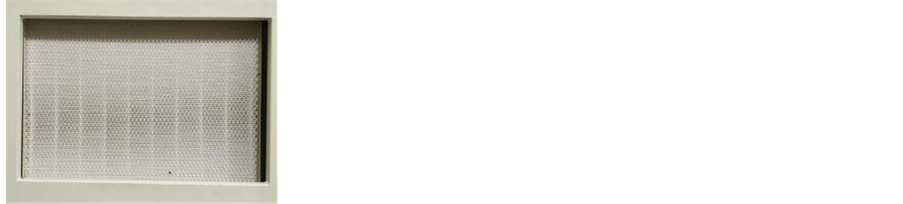
(a) (b)
Figure 6. Level-three high efficiency filter plate front (a) and back (b)
图6. 三级高效过滤板正面(a)和反面(b)
4. 磨床配套除尘方案设计
一套除尘净化系统,通常由粉尘捕集装置(吸尘罩口),管道系统,除尘器,风机及控制测试辅助装置等组成 [6] 。
4.1. 排风量选择
根据MOX物料特性,磨削过程中物料及磨削粉尘应围封在密封箱室内。密封箱室换气次数参考《核燃料后处理厂辐射安全设计规定》(EJ 849-1994),对于容器5~10 m3的小室,每小时换气次数15~20次。初步估算,磨削和后续工序密封箱室容积约为6 m3 (双面操作四工位箱室+单面操作六工位箱室),排风量Q1 = 6 m3 × 20 次/h=120 m3/h。
根据伯努利原理,流动中速度增大,压强就减小;速度减小,压强就增大;速度降为零,压强就达到最大(理论上应等于总压)。因此,吸尘系统在给定一定的流速的管道空气后会在管道处产生负压,使磨削处的粉尘产生一个吸引力。被切削出来的粉尘也会受到两个力,有法向应力和切向应力。通过粉尘自身的切向力并结合吸尘系统负压产生的吸力,可容易地将粉尘引进吸尘口内,通过管道系统从而将粉尘从源头上消除掉。
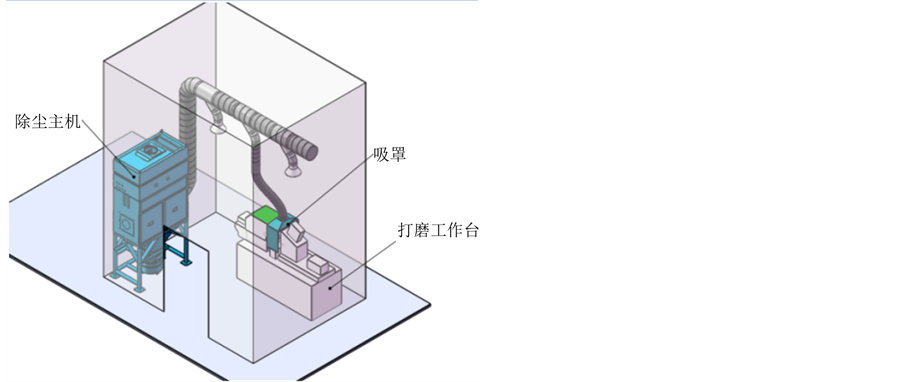
Figure 7. Dust removal system simulation diagram
图7. 除尘系统模拟示意图
根据磨削处实际尺寸,设计一内径为200 mm的吸尘口,设计管口风速为1.5 m/s,计算风量需求。根据体积流量计算公式:
(1)
其中Q——气体流量,m3/h;
D——圆形管道的内径,m;
v——管道内的气体流速,m/s。
通过计算可得风量需求为Q2 = 170 m3/h。同时,吸尘口后接管处设计一风阀以便调节风速和控制风量。则总风量Q = Q1 + Q2 = 290 m3/h。根据工况,设计工业集尘器,功率为3.0 kW,最大风量500 m3/h,最高负压1500 Pa。
4.2. 管道的布置
根据生产要求,设计两处吸尘口,一处为磨削处,一处为磨削完成表面除尘,配套管道直径的设计全部按风速合理布局,支管和弯头位置采用45˚斜角弯头分流。对于车间管路的材质选取,考虑到输送压力的大小(最大不超过5000 Pa),无需选择耐压比较高的钢管,可采用强度高、阻力小、密封性能好、外形美观、安装简单的镀锌螺旋风管布置,其内外壁光滑,风道阻力小。
MOX物料具有强烈的放射性和极毒的化学毒性,其物料接触必须是具有严格密封特性,要防止老化、腐蚀,寿命尽量长。选择安装不锈钢焊接管道。
4.3. 除尘系统总体设计
根据生产要求,除尘系统主要由除尘器,除尘管道,排风机等组成,为了保证产生的粉尘不泄露,从磨床生产线到工作车间设计了多层密封罩,实际使用中,除尘系统外壳就是一个密封箱室或手套箱。实际生产需考虑辐射屏蔽。除尘系统模拟示意图如图7所示。
5. 总结
随着空气质量问题越来越受关注,工厂生产加工过程中产生的粉尘处理问题不容忽视。我国首次用无心干磨法进行模拟MOX燃料芯块磨削试验,产生的粉尘具有强烈的放射性和化学毒性,会对人员和环境产生严重伤害,因此绝对不能有任何泄露。
MOX燃料芯块磨床的整体除尘要求坚持安全、可靠、适用的设计原则,选择工艺先进成熟、系统稳定安全可靠、管理方便的治理技术。本文在我国现有的多种除尘技术中选择利用过滤除尘技术,设计出一种经济适用,简单易行的除尘方案并进行试验验证,对0.3~1 μm粒度的粒子吸收率能达到99%。该方案可适用于大多数工业生产,且效果显著。这一套除尘方案包括送风量计算,除尘口设计,管道布置,二次密封等,还研置出一种除尘效率高达99%的工业除尘器,它利用扰流,脉冲反吹等原理用三次过滤方式进行粉尘过滤,确保粉尘的吸收率。
该方案首次应用于MOX燃料芯块干磨试验生产线中,经过实践验证,可以达到很好的除尘效果,后期将扩大对其应用。该设备和方案简单易行,经济效益高,具有很大的市场潜力,值得推广。