1. 前言
随着新能源汽车行业的高速发展,低风阻、低风噪成为乘用车节能与提高续航里程的新热点 [1] 。汽车风洞是测试新开发车型风阻系数和气动噪声最可靠的试验设备 [2] 。对于由汽车风洞与测力天平组成的试验系统,汽车风洞流场品质是影响试验数据质量的重要因素 [3] 。具有高品质流场的汽车风洞在满足新车型气动特性评估试验的同时,还具备开展流动机理研究的基础条件,是能够兼顾新产品工程验证和新技术研发的试验平台 [4] 。
最早的汽车风洞源于航空风洞,从结构形式上划分有直流式风洞和回流式风洞;从试验段尺寸划分有模型风洞和实车风洞 [5] 。汽车风洞的发展是随着汽车产品对气动试验能力需求的持续提升而逐步完善的。当3/4开口试验段回流结构成为汽车风洞的基本结构形式的情况下,行业内技术人员开始关注该气动构型的气动特性。其中,低频压力脉动是最典型的气动问题 [6] 。1928年,Jacobs风洞设计团队在开口试验段风洞的试验中发现压力脉动现象,提出该现象与风洞尺寸、喷口结构、收集口结构有关 [6] 。1977年,欧洲最大的低速风洞DNW在建成后的首次调试中,发现在60 m/s风速时出现压力脉动现象,在84 m/s风速时出现部分结构损坏的情况 [6] ,直接导致该风洞的最大风速就被限制在80 m/s。我国的汽车风洞发展起步较晚,2003年,吉林大学建成了汽车试验风洞实验室。2009年,同济大学全尺寸汽车风洞实验室建成并投入使用。2019年,中国汽研在重庆建成了国际一流水平的汽车风洞实验室。国内建设的全尺寸汽车风洞气动构型一致,试验段喷口尺寸相当,低频压力脉动的弱化方法都是使用亥姆霍兹谐振腔 [6] 。2011年,湖南大学仇健和谷正气研究了汽车风洞收缩段对流场品质的影响 [7] ;2014年,湖南大学鲍欢欢和谷正气研究了汽车风洞主要结构参数对风洞噪声影响 [8] 。本文提出汽车风洞高品质流场气动设计方法研究,尝试在系统梳理汽车风洞高品质流场影响要素的基础上,通过总统方案设计、风洞洞体各部段设计以及风洞高品质流场控制措施设计,给出汽车风洞高品质流场气动设计的基本流程与技术路线,初步形成一套工程设计方法。
2. 风洞高品质流场总体方案设计
汽车风洞的高品质流场评价参数包括参考点动压修正系数、动压稳定性、动压均匀性、局部气流偏角、轴向静压梯度、湍流度、背景噪声、低频压力脉动、边界层厚度、气流温度 [9] 。其中,动压参考点修正系数是为试验提供准确动压的根本保证;动压稳定性、动压均匀性、气流偏角是试验数据不确定度的影响因素;湍流度会影响边界层转捩位置从而影响试验结果;低频压力脉动存在使风洞产生低频共振的风险,同时会对相关流场参数产生影响 [10] 。
开展汽车风洞高品质流场总体方案设计,就是在常规风洞设计的基础上进一步研究提升流场品质的方法,制定一条科学合理的技术路线 [11] 。把28 m2汽车风洞试验段喷口面积和最大风速250 km/h作为基本设计条件,参考以往工程案例,喷口截面水力直径约为5左右,初步确定试验段喷口截面尺寸为7 m × 4 m。
首先,初步确定风洞洞体气动轮廓为3/4开口试验段回流型式。整个风洞洞体回路包括收缩段、试验段、多级扩散段、拐角段、动力段、圆变方过渡段、换热器段和稳定段,风洞气动轮廓图如图1所示。基于3/4开口试验段的气动构型,即下洞壁为固壁,没有上洞壁和侧洞壁。对于这样的气动构型,因喷口射流剪切层作用产生的涡脱频率与风洞固有模态声振频率重叠时,就会在某个特定风速下产生风洞结构低频振动。为此,汽车风洞总体方案设计中需要将弱化低频压力脉动作为主体内容。

Figure 1. Aerodynamic profile of wind tunnel
图1. 风洞气动轮廓图
其次,合理选择收缩比并匹配风洞各部段面积。风洞收缩比是低速风洞最关键的参数之一,需要与稳定段整流装置参数合理匹配,使风洞具有较低的湍流度、较高的能量比和合理的工程造价。依据工程经验,较大的收缩比有利于在试验段获得较低的湍流度。但是国外气动声学风洞最新研究表明,采用大收缩比获得的较低的试验段湍流度的频谱特性与真实情况有较大差异 [12] ,一些研究报告推荐声学风洞使用收缩比在3~12范围内,本设计将收缩比定为6。风洞收缩比确定后,需要优化匹配风洞各主要部段的面积比例(与试验段面积之比)。这些部段包括扩散段、风扇段和换热器部段等。其主要目标是提高风洞流场品质,降低风洞回路损失。具体表现为:控制风洞回路中不出现流动分离,有利于提高风扇效率并降低换热器损失。根据已有低速风洞设计经验,风扇段与试验段面积比例一般为2~3范围内,这样有利于提高风扇效率。
第三是湍流与噪声控制。为了在风洞试验段获得较低的气流湍流度,通常在稳定段整流采用多层阻尼网。阻尼网和收缩段对湍流度的衰减效果可从阻力手册中查询。低速风洞有两个主要噪声源,即风扇噪声和射流噪声,此噪声将沿回路传播。为降低试验段的背景噪声,气动总体设计中通常采取降低风扇噪声、在风洞回路中采用吸声衬里和片式消声器、对拐角导流片作吸声处理、将消声室所包围的试验段、收缩段、收集器、第一扩散段表面作吸声处理。对于扩散段面积比的选择:低速风洞首要要求是较好的流场品质,如此要求扩散段面积比和扩散角具有严格限制,一般要求第一扩散段面积比不大于2 [13] 。换热器部段布置在第三拐角段和第四拐角段之间,其理由是换热器部段是整个风洞回路中面积最大的部段,目的是尽量减小来流速度,控制流动损失。
第四是动压稳定性、动压均匀性、气流偏角和轴向静压梯度控制。气流在风洞回路中稳定运行,其决定性因素是轴流风扇转速的稳定性。为此,需要对电机和变频器做精细化筛选,严格限制电机转速控制精度。动压均匀性和气流偏角由风洞洞体气动轮廓决定。其设计理念是控制风洞回路中不出现流动分离。轴向静压梯度的决定性因素是喷口和收集口,设计中需要对比优选喷口和收集口的匹配关系。
第五是低频压力脉动控制。为弱化低频压力脉动,低频压力脉动成为流场品质影响因素中需要重点考虑的问题。为此,在开展汽车风洞总体设计阶段需要在不同参数条件下,循环迭代试验段喷口剪切层涡脱频率与风洞及驻室声振频率之间的耦合关系,通过使用亥姆霍兹谐振腔弱化低频压力脉动 [14] 。
3. 风洞洞体各部段气动设计
3.1. 收缩段
在风洞收缩比确定的基础上,需要进一步选择收缩曲线。依据工程经验,工程上常用的收缩曲线有三种,分别是维氏曲线、双三次方曲线和五次方曲线(如图2所示)。为保证声学及开口试验段流场品质,对收缩段的内部型面有很高的要求,数值研究结果表明,维辛斯基曲线进口处收缩快,逆压梯度明显,容易导致气流分离,因此采用五次曲线设计收缩型面较多,双三次曲线的也比较常用。本设计中收缩段型面选择五次方曲线,如图3所示。
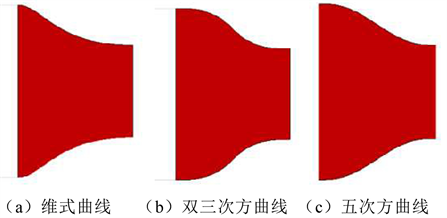
Figure 2. Contraction curve of contraction section
图2. 收缩段收缩曲线
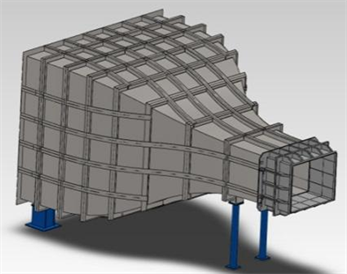
Figure 3. Outline structure of contraction section
图3. 收缩段外形结构图
3.2. 试验段
对于3/4开口试验段,在喷口截面尺寸确定的条件下,需要在开口试验段下游匹配设置一矩形截面收集器,其作用主要是汇集射流气体进入下游第一扩散段。收集器相关的设计要点是调整收集器入口面积使其收集的气体流量与喷口出口流量匹配。试验段喷口与收集口及试验段驻室区域如图4所示。
3.3. 扩散段
扩散段的作用是使气流在面积逐渐增加的流动通道内逐渐减速升压(如图5所示)。它的设计要点是避免流动分离,并尽量减少扩散段损失。其设计参数主要包括当量扩散角和面积比。研究表明最佳扩散角θ < 5˚。当扩散角θ < 5˚时,如果面积比过大或入口速度剖面分布不均匀时也同样有分离的危险 [15] 。本设计选择三级扩散,使每段当量扩散角相等,这样可显著减小过渡扩散段的压力损失,而且过渡段的初始部分不易发生流动分离。
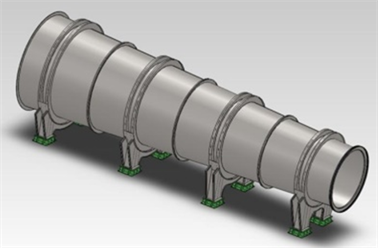
Figure 5. A diagram of diffusion section
图5. 扩散段示意图
3.4. 圆变方过渡段
圆方过渡段连接低速扩散段和第三拐角段,管道内部要求等面积过渡(如图6所示)。
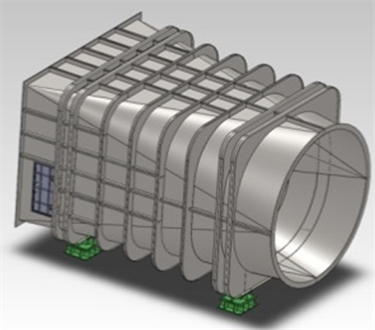
Figure 6. A diagram of circular to rectangular transition section
图6. 圆变方过渡段示意图
3.5. 拐角段
风洞通过四个90˚拐角段来实现气流转向在洞体内循环,四个拐角段内均布置有拐角导流片,同时可实现以下两个作用:一是抑制拐角流动分离,减小压力损失;二是改善出口气流流动品质。拐角导流片按剖面形状不同可分为圆弧型、薄片圆弧弯板型以及翼剖面型等不同型式。翼型剖面导流片对来流有较好的适应性,并且出口流场有较好的均匀度。拐角导流片气动轮廓如图7所示。
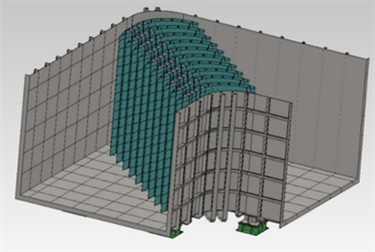
Figure 7. A diagram of corner deflector
图7. 拐角导流片示意图
3.6. 换热器段
为保证试验过程中气流温度恒定,在风洞内需要布置换热器系统(如图8所示),换热器型式采用圆管翅式,换热器表面换热元材料选用不锈钢或铜,换热器壳体与风洞洞体一致 [16] 。换热器系统采用闭式循环水冷却,冷却介质为软化水。
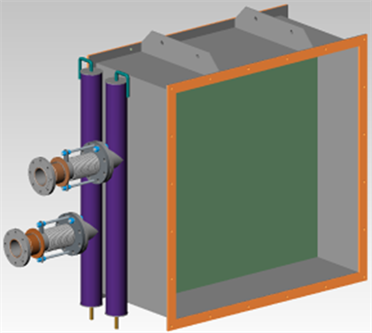
Figure 8. A diagram of heat exchange section
图8. 换热器段示意图
3.7. 稳定段
稳定段位于收缩段上游,内部设置整流装置,主要作用是为风洞收缩段提供均匀、方向性好以及湍流脉动衰减的气流。稳定段设计综合考虑以下因素:一是保证风洞试验段具有良好的入口气流品质;二是风洞回路具有较小的压力损失;三是风洞回路具有较小的洞体容积。稳定段其设计目标是为收缩段提供均匀稳定的来流(如图9所示)。稳定段内布置有蜂窝器和多层阻尼网等整流装置(如图10所示)。蜂窝器主要作用是导向和分割来流大旋涡,同时由于壁面对气流的摩擦作用,也有利于改善气流的截面速度分布。该蜂窝器截面为六角形,蜂窝器的长径比取值L/D = 20,孔眼对边距离为10 mm,轴向长度为200 mm,保证低温下蜂窝器内气流流动为完全发展湍流,可消除气流湍流的横向分量。阻尼网主要用于降低气流的轴向湍流度,同时由于气流通过阻尼网时产生的压降与速度的平方成正比,其轴向速度的均匀性也会得到改善。阻尼网设计参数包括网的阻力系数k值、通气率f值、层数、网丝直径及网间距等。阻尼网选用规格为20目/英寸、网丝为直径0.25 mm的不锈钢丝,通气率约为64%。
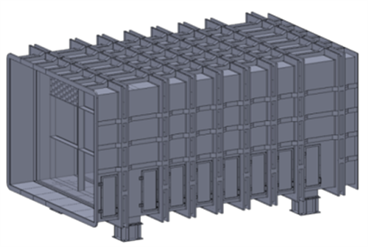
Figure 9. A diagram of control airflow section
图9. 稳定段示意图
3.8. 能量损失估算
在风洞各部段设计完成后,参考流体力学阻力手册中的经验公式计算风洞各部段总压损失系数:
开口试验段损失系数如(1)式所示。
(1)
式中L为试验段长度,DN为试验段喷口水力直径。
扩散段损失系数如(2)式所示。
(2)
式中λ为摩擦阻力系数,θ为扩散角,D1为扩散段入口直径,D2为扩散段出口直径。
拐角段损失系数如(3)式所示。
(3)
式中Re为拐角导流片特征雷诺数。
风扇段损失系数如(4)式所示。
(4)
式中λ为壁面摩擦阻力系数,L为风扇段长度,D为风扇段直径,η为整流体尾罩扩散效率,通常取值0.8,rb为整流体最大截面半径与风扇段半径之比,
静叶相对厚度。
蜂窝器损失系数如(5)式所示。
(5)
式中
为蜂窝器阻塞度,L为蜂窝器长度,D为蜂窝器孔水力直径。
阻尼网损失系数如(6)式所示。
(6)
式中
为阻尼网阻塞度。
收缩段损失系数ξ值经验公式(7)计算:
(7)
式中:L——收缩段的长度;
Dτ——收缩段出口截面的当量直径;
λ——单位长度阻力系数。
风洞各部段总压损失系数计算结果如表1所示。
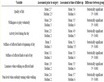
Table 1. Total pressure loss coefficient of each section of wind tunnel
表1. 风洞各部段总压损失系数表
由表1中数据可知,气动轮廓及整流装置优化后汽车风洞总阻力损失系数约为0.61,风洞能量比约为1.64,动力系统驱动电机轴功率约为4 MW。
计算风洞最大体积流量,算法见表达式(8)。
(8)
部段设计的主要工作是总压损失估算。依据工程经验,汽车风洞能量比通常为2左右,由此估算轴流风扇压升,见表达式(9)。
(9)
得
。
通过流量和压升两个基本参数可以明确该风扇属于低压大流量产品。这部分设计内容需要将风扇直径、电机、整流罩等产品和动力段气动轮廓关联在一起,这必然存在扩散段与试验段的匹配与优化问题。根据已有低速风洞设计经验,严格控制风扇段面积比和该扩散段的扩散角以提高风扇效率 [15] 。
轴流风扇气动设计的指导思想是较低的旋转噪声和较高的气动效率 [15] 。轴流风扇段为风洞内气流运行克服阻力提供动力,位于第二拐角段下游。风扇段的设计需要兼顾不同运行工况的高气动效率,同时还要尽可能地降低转速来抑制风扇的气动噪声。基于风洞总体方案和回路损失,采用基于流线曲率的气动设计方法,通过反复调整风扇设计参数(风扇直径、桨毂比、桨叶弦长、安装角等),给出初步的设计结果,风扇段的气动轮廓和结构三维示意图如图11所示。其中,桨毂比为xb = 0.55,风扇桨叶直径选择9 m,桨毂直径4.95 m。依据工程经验,风扇转速应与风扇轴向气流速度相配合,对于桨毂比介于0.5到0.7之间的风扇,通常叶片的尖部前进比取值0.20~0.40时风扇有高的叶片效率。为弱化噪声与气流脉动,风扇额定转速控制在200 rpm以内。为了提高风扇效率,采用具有较高的升阻比(翼型最大升阻比达60~80)的翼型。因为该风洞运转速度范围较宽(7 m/s~70 m/s),因而风扇叶片需要有较宽的迎角使用范围是有利的,适合于选择厚度较大、失速角大的翼型。对于给定的风扇压升、风扇转速,叶片数与叶片弦长的乘积是确定的,叶片数与弦长成反比关系。若叶片数目过多,则弦长过小,会使运转Re数降低,阻力增大,影响风扇效率,桨叶数目太少,可能会引起气流的脉动。综合以上因素,该风扇转子叶片数为20片。风扇段直径为9 m,叶尖间隙平均小于5 mm。由于风扇入口前是第二拐角,拐角出口气流不均匀,会恶化风扇入口气流环境,在这里前导流片主要起导流和支撑的作用,使风扇入口气流与轴线平行。为了避免共振,通常前导流片的数目与风扇叶片数目互质。由于风扇入口离拐角近,气流速度剖面不均匀,取较多的片数共17片,采用对称的NACA015翼剖面。止旋片的作用一方面是为了支撑电机,一方面是为了克服气流中剩余的旋转,将气流旋转动能转化为压力能。止旋片的数目以避免共振为前提,共17片。为了使气流流过风扇时有较好的流动状态,需要布置整流罩,防止气流分离,提升风扇入口流动品质并降低风扇出口流动损失。
4. 风洞高品质流场控制措施设计
4.1. 流场均匀性
流场均匀性的首要决定因素是风洞洞体的气动轮廓。对称、平顺是洞体流道匹配流场均匀性的基本条件。流场均匀性的次要决定因素是整流装置的布局。其中拐角导流片满足型面平滑、间距相等。蜂窝器模块组合满足对称条件,蜂窝器与洞体安装接口保证四周一致。
流场均匀性评价参数是动压场系,参数表达式如(10)式所示。
(10)
式中,
为流场中测量点动压系数,
为测量点动压,
为所有测量点平均动压。在气动轮廓确定的条件下,计算了三种收缩段收缩曲线的流场均匀性,结果如表2所示,结果表明五次方收缩曲线结果最好,本设计选择五次方曲线。
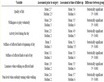
Table 2. 50 m/s, uniformity of dynamic pressure field in test section under different contraction curves
表2. 50 m/s,不同收缩曲线试验段动压场均匀性
4.2. 流场稳定性
流场稳定性的首要决定因素是风扇动叶旋转速度均匀,这需要依靠领先的动力与控制系统。本设计采用大功率交流变频器和电机组成的交流变频驱动系统作为动力设备。为实现风扇电机调速的要求,动力设备采用变频器矢量反馈控制或者直接转矩控制方式,通过风扇同轴的速度编码器反馈电机转速,实现电机转速闭环控制。
4.3. 低湍流度
汽车风洞湍流源包括壁湍流、分离流、旋转机械扰流。对于不同的湍流源,需要应用不同的控制方法。稳定段的湍流综合整治和收缩段的湍流减小控制是低湍流度控制的重要措施。
对于壁湍流,需要在气动设计方案中对洞壁内表面粗糙元尺度及与粗糙元尺度对应的流动特性开展计算研究,壁湍流的产生源于洞壁粗糙元,粗糙元周围的湍流结构以及不同尺度粗糙元的速度型如图12所示。
对于分离流,汽车风洞的流动分离包括扩散分离和转角分离。通常情况下,洞体拐角段会出现拐角区域外壁分离和拐角后内壁分离,流动分离会产生多尺度旋涡,这会使拐角段之后的流动不均匀而产生速度脉动。转角分离使用拐角导流片控制,依据工程经验,导流片有多种不同构型,不同类型导流片特性如图13所示。对于汽车风洞,双圆弧翼型结构导流片(如图14所示)是工程上的最佳选择。
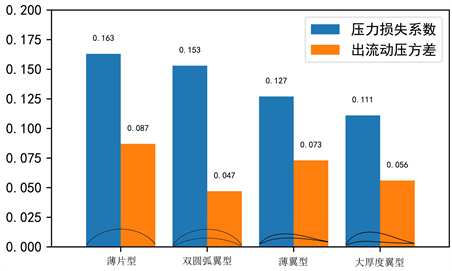
Figure 13. Characteristics of different types of deflectors
图13. 不同类型导流片特性
对于稳定段综合整流,主要使用蜂窝器和阻尼网对气流的湍流做综合整治。蜂窝器能够切碎大涡并导直气流;阻尼网进一步切碎小尺度旋涡并使流动均匀。收缩段将稳定段综合整治的湍流平稳加速并保持湍流脉动不会发散。
对于旋转机械扰流,使用止旋片控制湍流度,控制效果如图15所示。

Figure 15. Effect of reverse rotatin control vane
图15. 止旋叶片控制效果
4.4. 低噪声
风洞声学设计中为降低风洞背景噪声采用的主要降噪措施如下:
采用专门的低噪声风扇系统、并将驱动电机安装于风扇中心体内直接驱动,以减小传动机构的机械噪声;对拐角导流片作吸声处理。其表面贴附有吸声材料,主要作用是降低风扇及回路产生的高频噪声。导流片选用较大弦长以提高其低频降噪能力;将试验段、收缩段出口端和收集器置于消声室内;拐角段、风扇段和第一扩散段的内壁做吸声处理;在开口试验段进行声学试验的情况下,在收缩段出口采取扰流体或柔性材料等射流降噪措施,降低射流噪声。总的来讲,通过风洞回路中的降噪装置,保证风扇噪声传播至噪声监测点时噪声水平;通过射流降噪措施降低射流噪声。
4.5. 低轴向静压梯度
轴向静压梯度的决定性因素是试验段喷口与收集口的截面匹配关系。设计过程中选择了四种不同收集口与喷口的面积比,仿真结果如图16、图17所示,其结果表明面积比1.48为最佳,其轴向静压梯度值最小(小于0.001)。
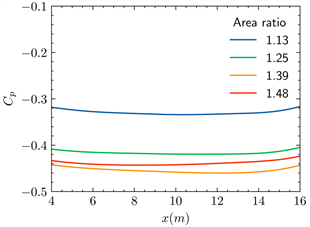
Figure 16. Axial static pressure distribution with different area ratio
图16. 不同面积比轴向静压分布
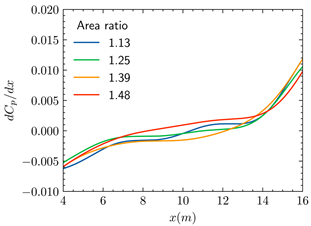
Figure 17. Axial static pressure gradient distribution with different area ratio
图17. 不同面积比轴向静压梯度分布
4.6. 无低频颤振
开口试验段喷口位置的涡脱落是低频压力脉动源,这种剪切涡脱落的频率可根据斯特罗哈数Sr计算,对于3⁄4开口式汽车风洞来说Sr的取值为0.34。剪切层涡脱落扰动频率按公式(11)计算:
(11)
其中
代表激励频率,V为来流风速,
表示喷口水力直径,不同风速下剪切层涡脱落扰动频率的计算结果如表3所示。
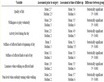
Table 3. Calculation data of vortex shedding frequency of nozzle shear layer under different wind speed
表3. 不同风速下喷口剪切层涡脱落频率计算数据表
另一个低频压力脉动源是喷口到收集口的自激励反馈。从喷口后缘脱落的旋涡随主流向下游移动,其移动速度约为中心主流速度的0.65倍。到达收集口后缘时旋涡与收集口发生碰撞并破碎,碰撞和破碎过程中产生的压力扰动又继续以
的速度向上游传递,会在喷口作为一种激励或扰动诱导新剪切涡的产生。如此在喷口与收集口之间形成一种自激励反馈循环,进一步加剧了测试段内压力扰动。因此,喷口与收集口之间的这种自激励反馈机制也会产生新的压力扰动。旋涡从喷口脱落,随主流到达收集口的时间计算公式为(12)、(13)、(14),计算结果如表4所示:
(12)
涡流与收集口碰撞并破碎后产生的压力扰动回向传播时间的表达式为
(13)
因此,自激励反馈所需要的总时间为
,得到自激励反馈循环频率为
(14)
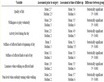
Table 4. Self-excited feedback cycle frequency of nozzle and collector under different wind speed
表4. 不同风速下喷口与收集口自激励反馈循环频率
3/4开口试验段汽车风洞存在三种声振模态,一是洞体流道等效的声学吹管声振模态;二是驻室腔体声振模态;三是喷口–驻室亥姆霍兹声振模态。三种声振频率的估算方如下:
等效声学吹管声振模态频率计算见式15,不同模态下具体结果见表5。
(15)
式中
为等效声学吹管的声振频率,n为模态阶数,a为声波速度,L为风洞流道长度。
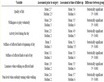
Table 5. Frequency of sound vibration under different modes of acoustic blowpipe
表5. 声学吹管不同模态下声振频率
对驻室设计尺寸进行验证计算,确保驻室内声学振动模态与风洞洞体回路不发生耦合,或者其耦合模态对应的频率在开口射流主要激励频率范围以外;收集器入口面积比自由射流等质量流量边界大一些,如此有利于减小低频压力脉动幅度;收集器开度可调,其基本开度及可调范围结合试验研究结果给出;最终用于风洞运行的最优开度在声学回路建成后调试过程中确定。驻室腔体的声学振动模态可用一个给定容积内的气柱振动模态简化。矩形容积内的不同振动模态对应的频率可用16式计算,不同模态下具体结果见表6。
(16)
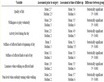
Table 6. Frequency of sound vibration under different modes in anechoic chamber
表6. 消声室不同模态下声振频率
喷口–驻室亥姆霍兹声振模态计算见式17。
(17)
喷口–驻室亥姆霍兹声振模态下声振频率约为1.3 Hz。
将风洞喷口涡脱频率、喷口–收集口自激励反馈循环频率以及声学吹管、驻室和喷口–驻室声振频率结果绘制曲线,结果如图18所示。
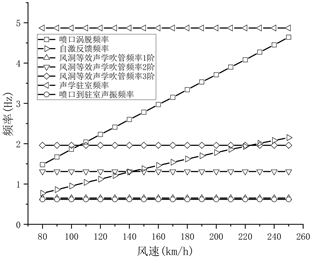
Figure 18. Curves of test section nozzle vortex frequency and wind tunnel different acoustic vibration mode frequency
图18. 试验段喷口涡脱落频率与风洞不同声振模态频率曲线
结合表3~6数据和图18,可以分析得出:声学驻室各阶频率避开了其余频率,声学驻室尺寸参数选择合理。喷口涡脱频率与风洞等效声学吹管三阶模态声振频率存在耦合,对应风速约为105 km/h;喷口–收集口自激励反馈频率与风洞等效声学吹管的二阶模态和三阶模态频率发生耦合,对应风速分别为150 km/h和230 km/h。
针对上述情况,需要开展低频压力脉动抑制设计。可借鉴且实效性强的工程方法是亥姆霍兹谐振腔(如图19所示)。其中,105 km/h是试验常用风速,在亥姆霍兹谐振腔设计条件匹配阶段需要重点关注。
5. 结论
本文基于新能源汽车低风阻车型开发对风洞高品质流场的试验需求,在系统梳理流场参数影响因素的基础上,提出了汽车风洞高品质流场设计的基本流程与技术路线,初步建立了一套工程设计方法。
总体设计方案中明确了风洞的气动轮廓,匹配了主要部段面积比,给出了湍流度、背景噪声、低频压力脉动的设计思路。
风洞洞体各部段设计中优化了各部段的具体参数,对流场均匀性、气流偏角、总压损失都做了工程估算。
风洞高品质流场控制措施设计中围绕流场均匀性、流场稳定性、低湍流度、低噪声、低轴向静压梯度、无低频颤振等高品质流场需求,给出了控制措施。