1. 引言
碎纸机的齿轮组在运行过程中主要的振动和噪声来源是齿轮在啮合时产生的 [1] 。齿轮啮合过程中可能会出现多种问题,导致噪声的产生,其中一些主要问题包括:齿轮制造误差,啮合不平滑,齿面磨损或损伤等等,这些问题会造成传动系统振动和噪声的增加,降低传动效率,同时也会缩短传动系统的使用寿命 [2] 。因此,对齿轮结构进行优化至关重要。合理的齿轮优化不仅可以减少齿轮啮合过程中的冲击和振动噪声,还能改善齿轮传动中载荷分布不均匀的情况,从而有效提升传动系统的可靠性和使用寿命。王文龙 [3] 等利用Romax并且结合遗传算法搜寻减速器齿轮最优修形参数,从而提高减速器整体的平稳性,降低振动和噪声。李宏坤 [4] 等利用ANSYS软件的优化求解器结合振速法原理,在齿轮箱箱体有限元振动响应计算的基础上,实现了齿轮箱箱体的减振、降噪优化求解。朱华 [5] 等将模态分析、多体动力学、有限元和边界元的计算方法有机地结合在一起,提出了一种高效,又能满足一定精度的噪声预测方法。王成 [6] 等则是提出了人字齿轮齿廓修形优化的理论和设计方法,以传动误差最小为目标函数,采用复形调优法进行优化,从而得到最佳修形齿面。
本文通过ROMAX软件建立斜齿圆柱齿轮组第一级传动副的模型,对其进行仿真分析轮齿所受到的载荷和传动误差,根据参数优化理论,利用Romax进行综合参数优化,最后对比分析齿轮修形前后传动误差峰值数据,验证修形效果。
2. 建立分析模型
在对齿轮组第一级传动副进行参数优化设计过程中,我们采用了Romax Designer软件进行建模和分析。主、从动轮的基本参数,如表1所示。其中,载荷谱功率流参数如表2所示。主动轮轴的输入功率为291.5瓦,其转速为4400转/分钟。首先,我们确定了输入轴和输出轴的布局,并在模型中施加了适当的荷载和设置了必要的边界条件,以确保模拟的真实性和准确性。通过Romax Designer软件提供的强大功能,我们能够对整个传动系统进行详细的分析,包括齿轮的啮合情况、传动效率、振动和噪音等方面的特性。这一系列的工作将为齿轮传动系统的优化设计提供有力的支持和指导,以确保其在实际应用中具备优异的性能和可靠性。具体的模型分析结果详见图1。
3. 修形前齿轮动态啮合性能分析
齿轮传动系统由于其具备弹性特性,因此在运转中可能出现一些挠曲和变形的情况。这种变形可能
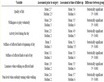
Table 1. Specific parameters of the driving and driven wheels
表1. 主动轮和从动轮的具体参数
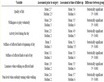
Table 2. Load spectrum power flow parameters
表2. 载荷谱功率流参数
会引起系统受到冲击载荷和振动的影响,进而影响系统的稳定性和承载能力。为了克服这些问题并优化系统的性能,必须进行深入的啮合性能分析,以了解齿轮之间的运动情况及其对系统的影响。通过这种分析,可以确定是否需要采取轮齿修形措施来改善系统的运行效果,确保其稳定性和可靠性。这样的优化举措将有助于提高齿轮传动系统的工作效率,并延长其使用寿命 [7] 。
3.1. 传动误差分析
传动误差(TE)是指在齿轮传动系统中,由于齿轮之间的啮合不完美或运动不平稳而引起的轴线间的角度变化。计算公式(1)、(2)如下:
(1)
(2)
在提到的公式(1)和(2)中,rb1和rb2分别表示主动轮和从动轮的节圆半径;θ1代表主动轮的理论转角,θ表示从动轮的实际转角,θ2则代表从动轮的理论转角;而Δθ则指传动误差所引起的从动轮实际转角与理论转角之间的偏差值。
通过Romax软件进行分析,可以获得小齿轮的传动误差曲线,详见图2。传动误差报告,详见表3。大齿轮的传动误差曲线和传动误差报告如图3和表4所示。从表3和表4我们知道大齿轮和小齿轮沿啮合线位移的距离是一样的,所以它们的传动误差一样,所以下面我们只分析小齿轮。
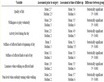
Table 3. Pinion gear transmission error analysis report
表3. 小齿轮传动误差分析报告
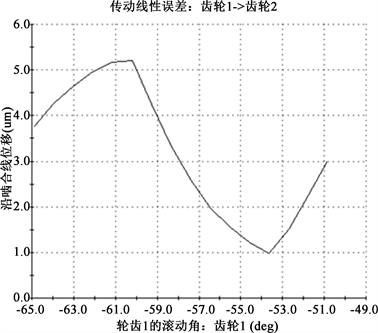
Figure 2. Transmission error curve before pinion gear shaping
图2. 小齿轮未修形前传动误差曲线
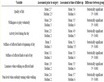
Table 4. Large gear transmission error analysis report
表4. 大齿轮传动误差分析报告
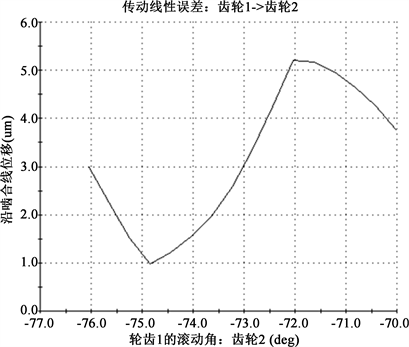
Figure 3. Transmission error curve of large gear before shaping
图3. 大齿轮未修形前传动误差曲线
3.2. 齿向载荷分析
单位长度法向载荷是指单位长度上所施加的垂直于齿轮齿面的力或载荷,用于描述齿轮传动系统中齿轮齿面受到的载荷的大小。这个载荷大小直接影响着齿轮的工作状态。如果单位长度法向载荷过大,从而齿轮受到的力太大,会导致齿轮的损伤。单位长度法向载荷计算公式(3)如下:
(3)
在公式(3)中,K代表载荷系数,Fn代表公称法向载荷,而L则表示齿面接触线的长度。
使用Romax软件的接触分析模块,在预先设定的工况条件下,能够生成齿面单位长度载荷的云图以及对应的3D示意图,具体的展示结果可参考图4。
单位长度载荷的不均匀分布是指在轮齿的宽度方向上,载荷不同位置的大小存在明显差异。从图4可知,最大载荷集中在轮齿的一端,并且达到了489.055 N/mm,这个值相比其他位置明显更高。这种不均匀分布可能导致一系列问题,包括局部点蚀、齿面胶合,甚至可能导致整个齿轮的折断。特别需要注意的是,齿面载荷的不均匀分布会使得传动系统的工作状态变得更加不稳定,容易出现传动失效的情况。

Figure 4. Load per unit length of pinion before trimming
图4. 未修形前小齿轮单位长度载荷
4. 齿轮修形
齿轮传动系统在运行过程中常常会遇到误差波动较大的情况,这可能导致动态载荷的增加,进而影响系统的稳定性和可靠性。这种误差波动不仅会引起系统的振动和噪音,还可能导致载荷分布不均匀以及齿面损坏等潜在问题的出现。为了应对这些问题,我们将对齿轮的齿廓和齿向进行修形。这种修形过程可以调整齿轮的几何形状,通过合理调整齿廓和齿向,可以有效降低冲击载荷的传递,并改善齿轮之间的啮合情况,从而减少系统振动和噪音的产生 [8] 。
4.1. 齿廓修形量的确定
根据GB /Z6413.1-2003,可以获得弹性变形量C的公式如式(4)所示 [9] :
(4)
在公式(4)中:KA为使用系数,1;Kmp为分支系数,1;b为齿宽,78 mm;αt为端面压力角,20˚;Cγ为综合啮合刚度,14.62 N/(mm·μm);Ft为切向力,N。如公式(5)所示:
(5)
(6)
在公式(5)中,T表示输入轴的转矩,其数值为632.641 N·m。而在公式(6)中,P代表了输入功率,其数值为291.5 W,而n则代表转速,为4400 r/min。通过对表6的数据进行计算,得到Ft的数值为132.108462 N。此外,根据公式(4)可以计算出弹性变形量C为12.3283 μm。
齿廓的最大修形量,通常由两个主要因素所决定,即弹性变形量和基节误差。弹性变形量指的是在齿轮传动系统中,由于材料的弹性特性,在受到载荷作用时齿轮发生的微小形变。而基节误差则是指齿轮在制造过程中可能出现的误差,如式(7)所示:
(7)
式中:Δ为齿廓最大修形量,μm;fb为基节偏差,12 μm;可得齿廓修形量为24.3283 μm。
Romax中齿廓修形如图5所示,左右齿面修形方式相同,齿顶修形起始点19.0909˚。
4.2. 齿向修形量的确定
齿向修形量计算公式(8)如下:
(8)
(9)
在公式(8)中:Fβy为齿向啮合误差,1.78 μm;Fm为分度圆柱上的平均端面力,132.108462 N。计算出Δc为12.4748 μm。
齿向修形选择齿端修形,修形长度取0.1b。Romax修形如图6所示。
4.3. 修形后齿轮动态啮合性能分析
我们在ROMAX中更改齿距的大小,完成对齿轮的修形。修形完成后的传动误差分析和齿向载荷分析如图7,图8所示。
修形完成后的传动误差报告如表5所示。
修形前后传动误差数据对比如表6所示。
修形后,传递误差曲线如图7显示,在轮齿1角度为−50.827˚时,沿啮合线的位移达到最大值,为
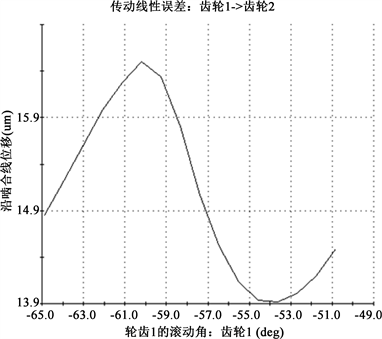
Figure 7. Transfer error curve after trimming completion
图7. 修形完成后的传递误差曲线
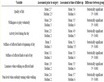
Table 5. Transmission error report after completion of trimming
表5. 修形完成后的传动误差报告
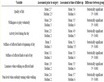
Table 6. Comparison of maximum peak transmission error data before and after shaping
表6. 修形前后传动误差最大峰值数据对比
16.50 μm;而当滚动角为−64.890˚时,达到最小值,为13.91 μm。经过修形处理,传递误差的峰值降至2.59μm,所以传递误差曲线更加平滑。与修形前相比,传递误差值从原先的4.23 μm降至2.59 μm,传动误差峰值减小了38.77%。单位长度载荷的分布图如图8显示,在齿轮修形完成后,载荷不再偏向一端,而是集中在齿轮中部。
5. 结论
经过Romax仿真后,齿轮的传动误差差值减少为2.59 μm,滚动角沿啮合线的位移曲线更加平滑。相比修形前,传动误差差值减少了38.77%。这样的改善有助于减少齿轮啮合时产生的冲击和振动,进而降低齿轮噪声,达到降噪目的。此外,齿轮修形后,单位长度载荷不再偏向啮合端,而是集中在齿轮中间位置,这表明齿轮的啮合更加平稳,震动减少,齿轮寿命延长,并促进了齿轮组的工作效率。