1. 介绍
由于蜂巢结构在轻质的同时还能保持良好的机械性能,因此被广泛应用于航空、船舶、车辆等各个领域。但蜂巢结构也是一种相对复杂的蜂巢结构。近年来,随着3D打印技术的发展,其成本逐渐降低,在制造复杂结构方面的优势也逐渐显现,并被广泛应用于蜂巢结构等复杂结构的制造。在3D打印技术中,FDM (熔融沉积成型)技术因其工艺简单、成本低廉而成为应用最广泛的3D打印技术。然而,在使用FDM制造蜂巢结构时,其工作流程与波纹法等传统方法有很大不同,虽然制造出的工件在宏观上相似,但由于3D打印的逐层打印过程和材料的熔融挤出凝固过程,会使工件在微观上产生波浪缺陷等微观结构缺陷 [1] ,从而改变蜂巢结构的力学性能,这些效应会改变蜂巢结构原本以拉伸为主的行为,使其也具有弯曲行为,成为拉伸和弯曲的结合体,并对其能量吸收功能产生不利影响 [2] 。
2. FDM 3D打印工件与传统工件的区别
FDM或DIW等挤出式3D打印技术获得的工件在宏观上一般都能满足精度要求,但由于3D打印的逐层打印过程,其制造的工件在微观上与传统方法制造的工件有很大不同,从而导致其机械性能的差异。影响因素主要包括材料和工艺 [3] 。
2.1. 过程因素
首先,在材料熔化过程中,固态材料受热成为流体,如果喷嘴温度过高,挤出后材料的状态多为液态,流动性强,粘度系数低,成型性差,精度控制不好,还可能造成两层印刷材料过度粘结、重叠 [3] ,影响印刷工艺。如果喷嘴温度过低,线材不易挤出,层间结合强度降低,容易造成分层、喷嘴堵塞等现象。因此,为了保证工件的宏观精度,喷嘴的加热温度会取一个中间值,但在微观上,中间加热温度会导致工件上同时存在温度过高和过低引起的问题。
1) 流变学
材料从加热成流体到凝固期间,具有流体流变性,流动无法控制,形成不规则的微观结构,会形成类似图1的结构 [4] 。
2) 层与层之间的附着力
同时,材料向流体的转化不完全,会导致层间粘附力不够,产生细小裂纹,影响工件的机械性能。此外,温度不够高,冷却速度过快,也会导致工件热应力增大,产生翘曲和变形 [4] 。
3) 冷却收缩
在熔融材料的冷却过程中,工件会出现收缩现象。材料的热膨胀是产生这种收缩的根本原因,在收缩过程中,由于材料植入和温度条件等复杂条件的影响,材料会产生不均匀的收缩。这种收缩使得每层印刷的材料分布不均匀。
多层印刷后,熔化的长丝不能同时叠加,这就会造成层间收缩率的差异,先印刷的层提前固化收缩,而后印刷的层没有完全固化收缩,这就会造成误差。如果印刷层数足够多,收缩率差异造成的误差就会叠加,从而导致微观结构缺陷。而且层与层之间会产生不同的内应力,进一步导致工件变形。
2.2. 材料因素
就材料而言,材料熔化后流体的粘度也会在很大程度上影响工件的微观结构。熔化后粘度高的材料在打印中更受欢迎,因为粘度高的聚合物具有更好的形状保持性,这意味着上述材料熔化成流体时的不可控流动性将得到改善。与其他AM技术相比,像FDM这样的喷嘴分配系统适用于从低粘度液体到粘稠糊状物(粘度高达6 × 107 mPa∙s),非常适合各种流体的沉积。因此,在FDM打印中,大多数材料在熔化后都具有高粘度。高粘度流体可以在固化过程中保持形状,但由于这种高形状保持能力,高粘度材料在打印时会在横截面上产生如图1所示的“木桩”形状,影响分辨率和光滑度,还会造成缺陷和空洞,这些缺陷和空洞是影响工件强度的关键因素。
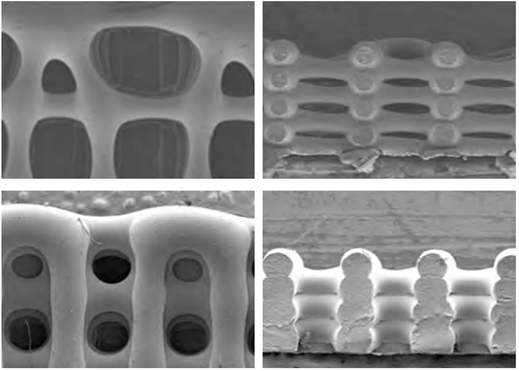
Figure 1. Features caused by fluid flow (upper left); features caused by insufficient adhesion (upper right); features caused by shrinkage (lower left); “log pile” shape on the cross section (lower right)
图1. 流体流动造成的特征(左上);粘合力不足导致的特征(右上);收缩造成的特征(左下);横截面上的“原木桩”形状(右下)
受上述因素的综合影响,与传统方法制造的结构相比,FDM 3D打印工件具有以下微观差异:
1) 由于收缩和凝固过程中流体材料的流动,每层平面上会产生不规则的波形边缘,而传统方法是规则的。
2) 由于材料流体状态的高粘度和固化收缩的影响,印刷层之间会有明显的界限,横截面形状如图2为不规则的椭圆形(“原木桩”)。传统方法不会出现分层现象,横截面也是规则的 [1] 。
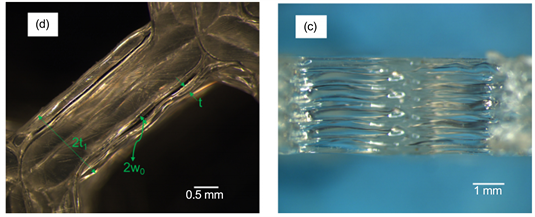
Figure 2. Wave defects and defects between layers
图2. 波浪缺陷和层间缺陷
3. 不同的微观结构导致的不同机械性能
对于蜂巢结构,我们有以下两个公式来计算其强度和模量,对于蜂巢结构,我们认为其行为以拉伸为主,因此比例指数b和c等于1,另一方面,对于行为以弯曲为主的结构,比例指数b和c大于1,至于比例系数B和C则取决于蜂巢结构的几何形状 [5] 。
(1)
(2)
上一节中提到的细胞壁波浪形变形将影响细胞结构的模量,具体来说,将在上式中加入一个击穿因子将被添加到上式中 [5] 。因此我们得到:
(3)
其中,波状度的非维度测量值
,波浪的振幅为而t是波浪的厚度。因此,我们可以通过测量波浪
的厚度t和波浪度的振幅,得到单位晶胞的胞壁波浪度
。
3.1. 单轴拉伸与弯曲载荷实验 [1]
下面使用FDM打印的蜂巢结构的单轴拉伸实验为例说明这些微结构对FDM印刷蜂巢结构机械性能的影响。以下六边形蜂巢结构使用的是Filaments.ca公司的PLA材料。材料的直径为1.75 mm,密度为1.23 g/cm3,使用的打印机为RepRap 3D。其尺寸为127 mm × 12.7 mm × 3.2 mm。
图3显示了六边形蜂巢结构的相对模量和抗拉强度,这是细胞结构相对密度函数的典型图像。
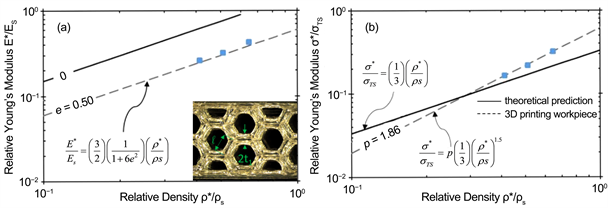
Figure 3. Hexagon honeycomb’s curve of Young’s modulus and strength to relative density under tensile conditions [1]
图3. 六角蜂巢在拉伸条件下的杨氏模量和强度相对密度曲线 [1]
实线表示理想拉伸主导型六边形结构的模量和拉伸强度的理论预测值。3D打印工件的相对模量与相对密度成线性比例,但相对模量低于理想拉伸主导型六边形填充结构模量的理论预测值。
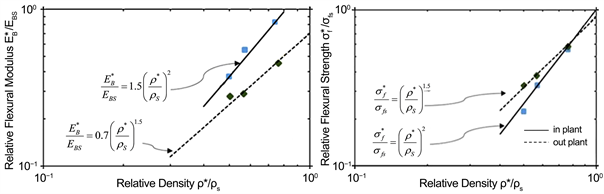
Figure 4. Hexagon honeycomb’s curve of Young’s modulus and strength to relative density for bending [1]
图4. 弯曲时六角形蜂窝材料的杨氏模量和强度与相对密度的关系曲线 [1]
图4中对于平面外荷载,结构的相对模量与相对密度成线性比例就强度而言,它与相对模量的比例指数为1.5。对于平面内荷载,结构相对模量与相对密度的比例指数为1.5,结构强度与相对密度之间呈二次关系。
3.2. 实验结果分析
图3中的现象可以通过波形缺陷得到很好的解释。对于图2所示的波浪变形,波浪度的非维度测量值e = 0.5,当对这种波浪形缺陷应用击穿因子(如公式(3)所述)时,它能正确描述六边形结构的相对模量。另一方面,3D打印工件的相对强度高于理论预测值,但强度与相对密度呈1.5的幂次关系,而对于拉伸为主的结构,强度应与相对密度成线性关系,相对密度与强度之间的比例指数差异以及相对模量低于预期值的现象是由于上一节提到的波形缺陷和微结构缺陷造成的,原因为波形缺陷增加了破坏机制中弯曲的贡献,因此这种蜂巢结构不具有拉伸为主的行为,但弯曲和拉伸行为的结合导致脆性断裂裂纹突然扩展,相对模量下降,也导致强度与相对密度的比例指数从1增加到1.5。
图4中的现象对于平面外荷载,结构的相对模量与相对密度成线性比例,这表明该荷载下的结构行为仍以拉伸为主。强度方面,它与相对模量的比例指数为1.5,这表明在平面外荷载作用下,结构行为已从拉伸为主转变为拉伸与弯曲相结合的行为。对于平面内荷载,结构相对模量与相对密度的比例指数为1.5,结构强度与相对密度之间呈二次关系。这表明在平面内荷载作用下,结构行为以弯曲为主。
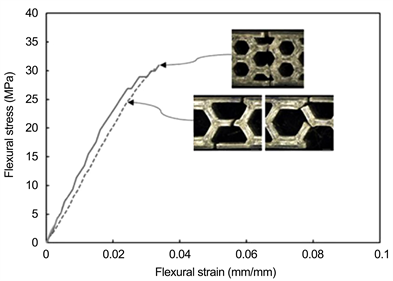
Figure 5. Strain-stress curve of hexagon honeycomb under bending [1]
图5. 六角形蜂窝材料弯曲时的应变–应力曲线 [1]
应变–应力曲线和光学图像也证实了结构行为的变化:在平面外载荷下,应变–应力曲线呈阶梯状,这是由于各印刷层逐渐破碎所致。而光学图像显示,在两种载荷下,结构的破坏都是由于拉伸–弯曲共同作用造成的。
4. 能量吸收性能
蜂巢结构的一个非常普遍的应用是能量吸收,上文提到的微观结构也会影响能量吸收性能。蜂巢结构在平面外方向受力时因其平坦的应变–应力曲线,最适用于能量吸收用途。图6显示了用传统方法制造的典型蜂巢结构在平面外方向受压时的应变应力曲线 [6] [7] 。
如图6,几种不同参数的FDM 3D打印蜂巢结构,由于微结构缺陷,其应变应力曲线并不平坦 [6] 。因此,在能量吸收方面FDM方法制造的普通蜂巢结构丧失了优势。
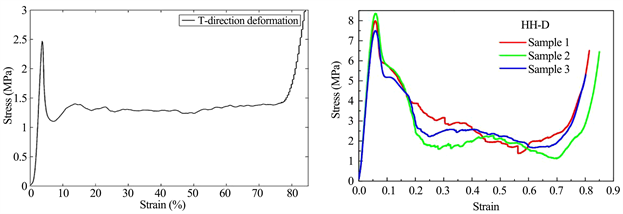
Figure 6. Energy absorption performance of traditional honeycomb FDM 3D printed honeycomb
图6. 传统蜂巢与FDM 3D打印蜂巢的能量吸收性能
虽然3D打印的普通蜂巢结构在吸能方面效果不佳,但我们可以充分发挥3D打印在制作复杂结构方面的优势,制造具有更好吸能性能的蜂巢结构。图7是一种被称为“折纸”的蜂巢结构 [2] 。与普通矩形蜂巢相比,“折纸”蜂巢结构的几何图案单元由四个具有一定长宽比e的矩形组成,且侧壁具有褶皱。它是用TPU进行FDM 3D打印的,TPU是一种常见的高分子材料,具有与PLA相似的机械性能。
如图7所示(e代表长宽比,n代表褶皱数),与长宽比e = 1且没有褶皱的普通蜂巢相比,“折纸”蜂巢具有更平整的能量吸收区域,甚至优于传统制造的蜂巢 [2] 。而这种结构对于传统制造方法来说非常复杂,但对于3D打印来说,复杂性不是问题。因此,要提高3D打印蜂巢结构的机械性能,设计更复杂、更合理的结构不失为一条出路。
5. 结论和未来工作
综上所述,蜂巢结构的行为都会受到3D打印工艺产生的微观结构的影响,主要表现在模量和强度的比例指数和比例系数的变化,导致力学性能的变化;在能量吸收方面,能量吸收区的应变应力曲线不再平坦,导致FDM 3D打印的普通蜂巢结构不像传统方法制作的蜂巢那样适合吸收能量。但FDM可以轻松打印出具有高能量吸收性能的复杂变体蜂巢,就像“折纸”蜂巢一样。
至于今后的工作,一方面可以着重改进三维打印工艺,比如调整材料配方,减少材料的收缩率就是提高打印精度的措施之一。最有效的补偿方法是在设计三维模型时提前考虑收缩率,调整零件尺寸,最大程度地抵消成型零件收缩率带来的精度误差。在设计时,根据工件的不同结构和形状,采用适量的补偿,使成型工件的实际尺寸略大于CAD模型的尺寸;在冷却过程中,尺寸会按照预定的收缩设计量进行调整,最终达到预期尺寸,满足精度要求。另一方面,三维打印工艺可用于改善某些具有特定几何图案的蜂窝结构的机械性能。例如,对于三角形和矩形蜂窝结构,可以部分改善蜂窝结构的力学性能。或者充分利用三维打印技术在制作复杂结构方面的优势,制作出更多具有设计感、吸能性能更好的蜂窝。