1. 引言
电子束选区熔化(Electron beam selective melting, EBSM)是一种先进的增材制造技术,融合了计算机辅助设计,材料加工与成形技术,通过自下而上的材料累加实现三维零部件的成形制造 [1] [2] 。EBSM技术具有能量密度高、吸收率高、真空制造环境无污染、成形热应力小的特点,能够实现高熔点和脆性材料的成形,应用前景非常广阔 [3] [4] 。传统的基于光学的监测系统,对于EBSM过程中孔隙、球化、表面翘曲变形等缺陷的长期监测很困难 [5] [6] ,成像清晰度、工作时间都不能满足电子束选区熔化过程 [7] [8] [9] 。
针对电子束选区加工过程中实时监测的需求,本课题组已经设计出了一套包括高频偏转扫描系统,背散射电子接收传感器,背散射电子信号处理系统以及图像处理软件的监测系统,实现了150 × 150 mm范围高速成像,分辨率可达1000 × 1000像素,成像速度可达1帧/秒。目前已经可以应用于电子束选区熔化过程的实时在线监测。但是在后续实验中发现,有许多因素仍然会影响最终的成像效果。传感器单极板有效采集面积过小,不利于形貌信息的采集,甚至有效信息完全被噪声覆盖,得不到图像 [10] [11] 。传感器极板个数设计不合理,会导致表面形貌信息采集不完整,出现信息丢失的情况 [12] [13] 。RC滤波电路中的电容容值过大会导致系统的截止频率降低,高频成像信号被滤除,成像细节缺失,分辨率和清晰度严重降低。容值过大时,系统对于高频成像信号的处理不灵敏,成像效果变差 [14] 。
使用课题组研制的背散射电子成像的在线监测系统,在EBSM过程中加以应用。通过小功率电子束流扫描成形表面,采集反射的背散射电子,还原扫描点对应的背散射电子信号携带的表面形貌信息。进行了背散射极板个数、单极板面积与滤波电容容值的优化,并实验得到优化后成形表面的背散射灰度图像,实现了清晰度明显提高的在线监测。该技术过程对高温、强光及金属蒸气不敏感,克服了传统光学监测技术的不足,并满足了电子束加工过程中清晰成像的要求,为电子束选区熔化过程实时清晰监测带来新的解决方案。
2. 背散射电子成像原理与系统设计
基于背散射电子成像原理,所设计的背散射电子成像系统主要包括高频偏转扫描系统、背散射电子传感与放大系统、图像处理软件,各模块原理图如图1所示。
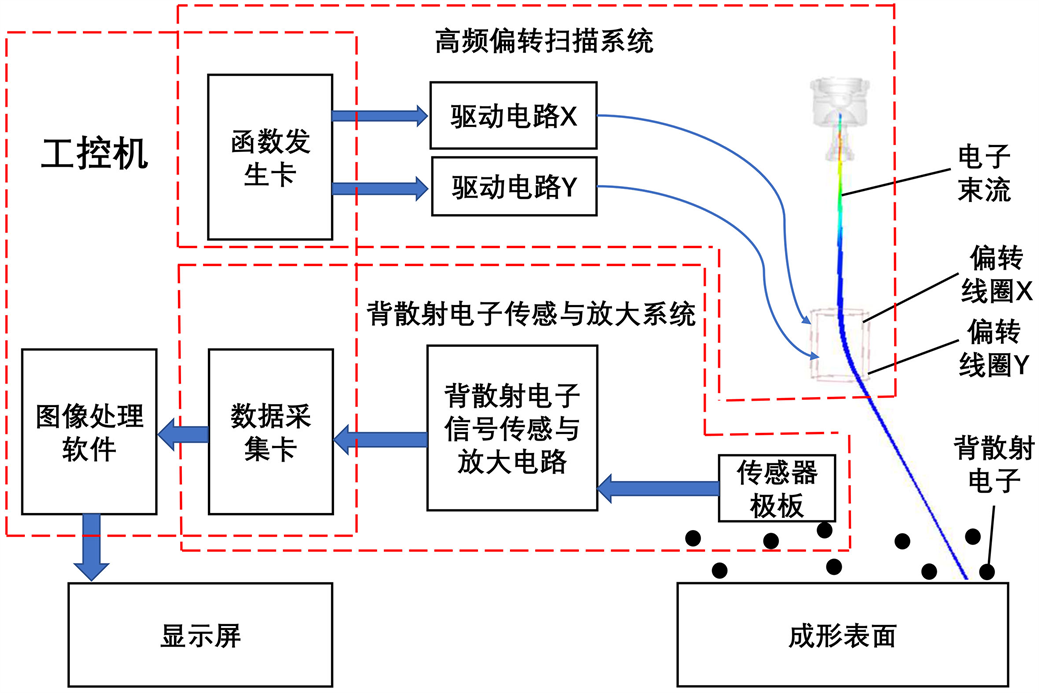
Figure 1. Block diagram of an online monitoring system based on backscattered electron imaging in the EBSM process
图1. EBSM过程中基于背散射电子成像的在线监测系统框图
高频偏转扫描系统控制电子束流的高速精确偏转过程,包括函数发生卡、高频偏转扫描驱动电路、偏转扫描驱动线圈。函数发生卡用于输出预定的偏转扫描信号;高频偏转扫描驱动电路对偏转扫描信号进行功率放大;驱动偏转扫线圈产生能够快速变化的磁场,控制电子束流的任意点偏转。
背散射电子传感与放大系统用于背散射电子信号的传感与放大,包括四极板背散射电子接收传感器、四路背散射电子信号传感与放大电路、数据采集卡。四极板背散射电子接收传感器用于背散射电子信号的采集;四路背散射电子信号传感与放大电路用于接收极板采集到的背散射电子信号,转化为电压信号并放大输出给数据采集卡;数据采集卡分别接收四路放大后的背散射电子信号,完成模数转换并存储原始数据。
图像处理软件基于C++可视化开发平台Qt Creator开发,包含人机交互界面、函数发生卡与数据采集卡的驱动模块、数据处理模块、图像生成与处理模块。人机交互界面主要用于输入参数、显示图像;板卡驱动模块主要用于配置函数发生卡及数据采集卡的参数;数据处理模块主要对数据采集卡采集到的原始数据进行分离和归一化,对应到0~255的像素灰度值;图像生成及处理模块将分离并归一化后的四极板数据处理为四幅单极板图像,再进行融合与滤波,输出清晰的形貌灰度图。
3. 系统成像能力测试与影响因素分析
3.1. 系统成像能力测试
实验依托中国航空制造技术研究院自主研发的大尺寸EBSM设备,将背散射电子接收传感器布置在成形平台上方并于电子枪同轴。实验时,选择EBSM过程真实的成形层表面作为扫描观察对象。
扫描范围设置为360 × 360 mm,选择S型扫描策略、点扫描方式,扫描点间隔设置为0.3 mm,扫描频率为100 kHz,这样采集到的像素数据为1200 × 1200个,即成像分辨率为1200 × 1200像素。高压加速电压为−60 kV,电子束流为2 mA,聚焦电流487 mA。灰度值的范围为0~255,0代表黑色,255代表白色。
成像效果如图2所示,成像范围能够实现360 × 360 mm,分辨率能够达到1200 × 1200像素,验证了所研制系统实现大范围成像的可行性以及应用于EBSM过程监测的潜力。图2(a)表面形貌图像对比度较弱,虽然能够分辨出轮廓,但细节丢失严重。图2(b)成像整体过于灰暗,无法看清表面细节。由此可知,本系统虽然可以成像,但成像过于粗糙,不能满足在线监测的需要,系统还需要进一步优化。
3.2. 影响系统成像能力的主要因素分析
对于电子束选区熔化设备,一般传感器极板的布置位置在成形平台上方,且不能遮挡束流通路,如图3所示。传感器极板的个数以及面积大小,将直接影响背散射电子信号的采集完整度,决定了系统成像正确性。传感器极板个数设计不合理或者有效采集面积过小,不利于形貌信息的采集,甚至有效信息完全被噪声覆盖,得不到图像。
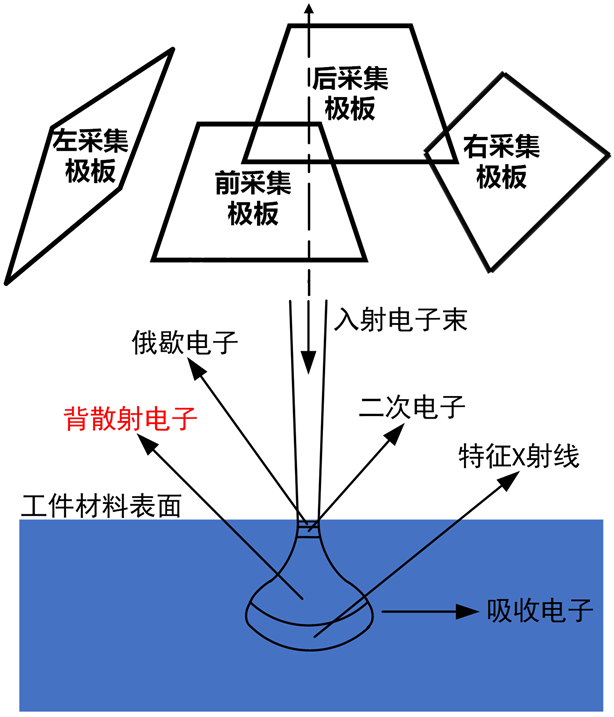
Figure 3. Arrangement position of the sensor plate
图3. 传感器极板的布置位置
背散射电子信号放大电路如图4所示,其中C4、C5为去耦电容,其余都为滤波电容,分别与电阻组成RC滤波电路,主要作用是滤除信号传输中的噪声,其截止频率公式如(1)所示:
(1)
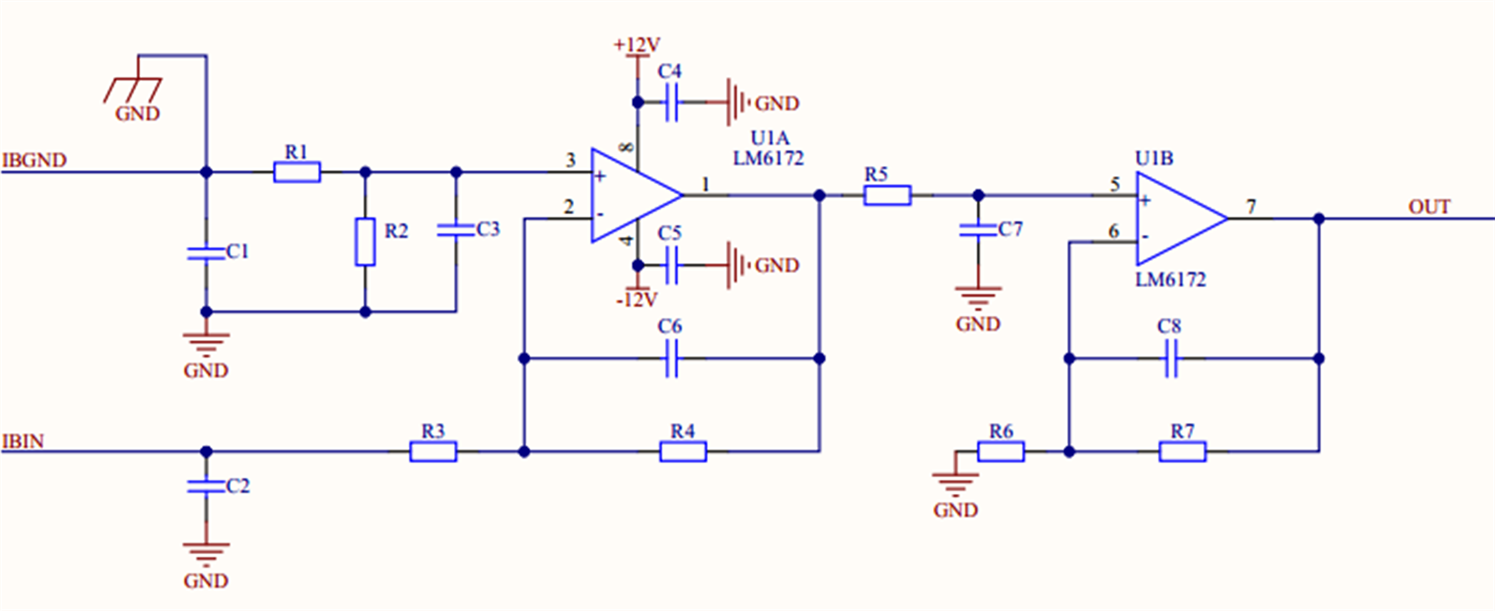
Figure 4. Backscattered electronic signal amplification circuit
图4. 背散射电子信号放大电路
由此可知,RC滤波电路中的电容容值过大时,系统的截止频率低,会导致高频成像信号被滤除,成像细节缺失,严重影响分辨率和清晰度。
使用函数发生器和示波器进行输出波形模拟测试,函数发生器给定脉冲信号的幅值为200 mV,占空比50%,频率为1~10 kHz可调,放大电路的放大倍数为10倍。输出波形如图5所示。可知随着频率的增大,输出波形逐渐失真。由方波逐渐变为近似正弦波。10 kHz时的峰值明显降低,为了更加直观读取波形,脉宽相较于其他波形降为了一半。由此可知,当前系统确实对高频扫描的输出信号处理失真严重,需要进一步优化。
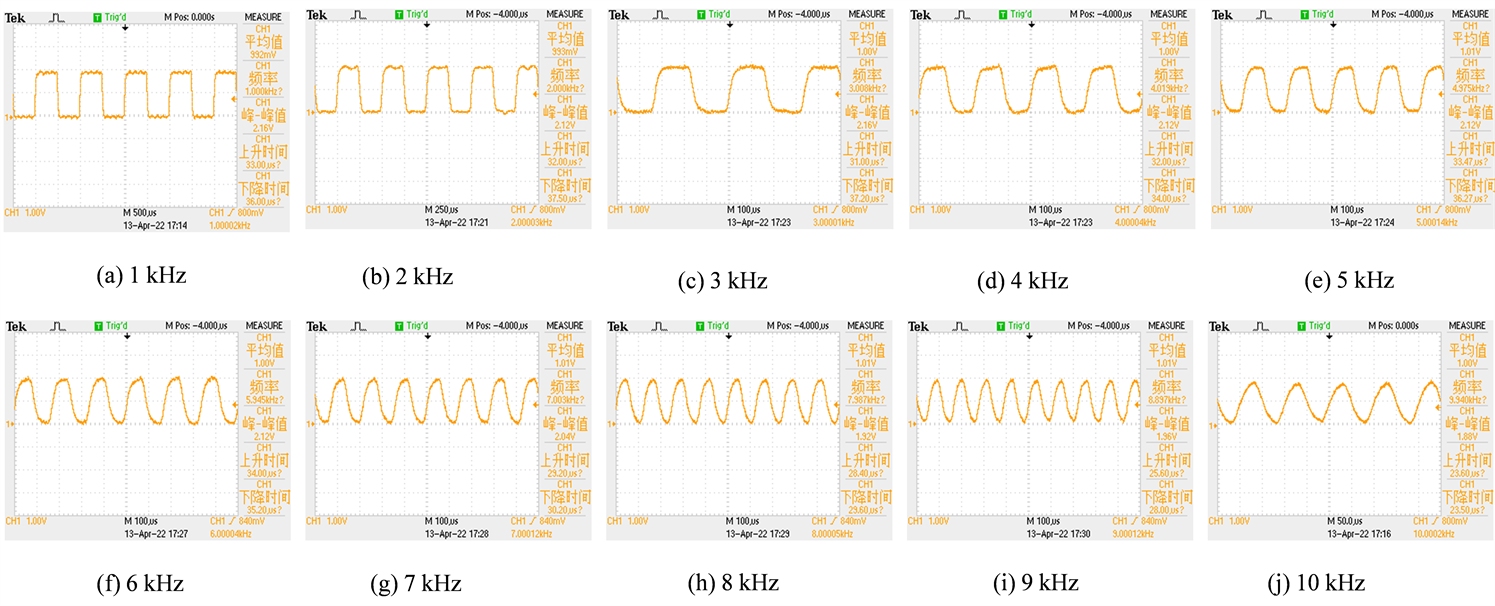
Figure 5. Waveform output at different frequencies
图5.不同频率下波形输出
4. 系统优化
本文主要对背散射电子信号采集与处理系统进行优化探索,主要包括传感器极板面积和个数优化,背散射电子信号放大电路的参数优化。
4.1. 极板个数优化
选取单极板面积为0.09 m2的传感器进行极板个数优化实验,选取图2(a)的实物为测试样品。传感器极板相对观察对象的位置布置和通过极板获得的背散射信号如图6所示。
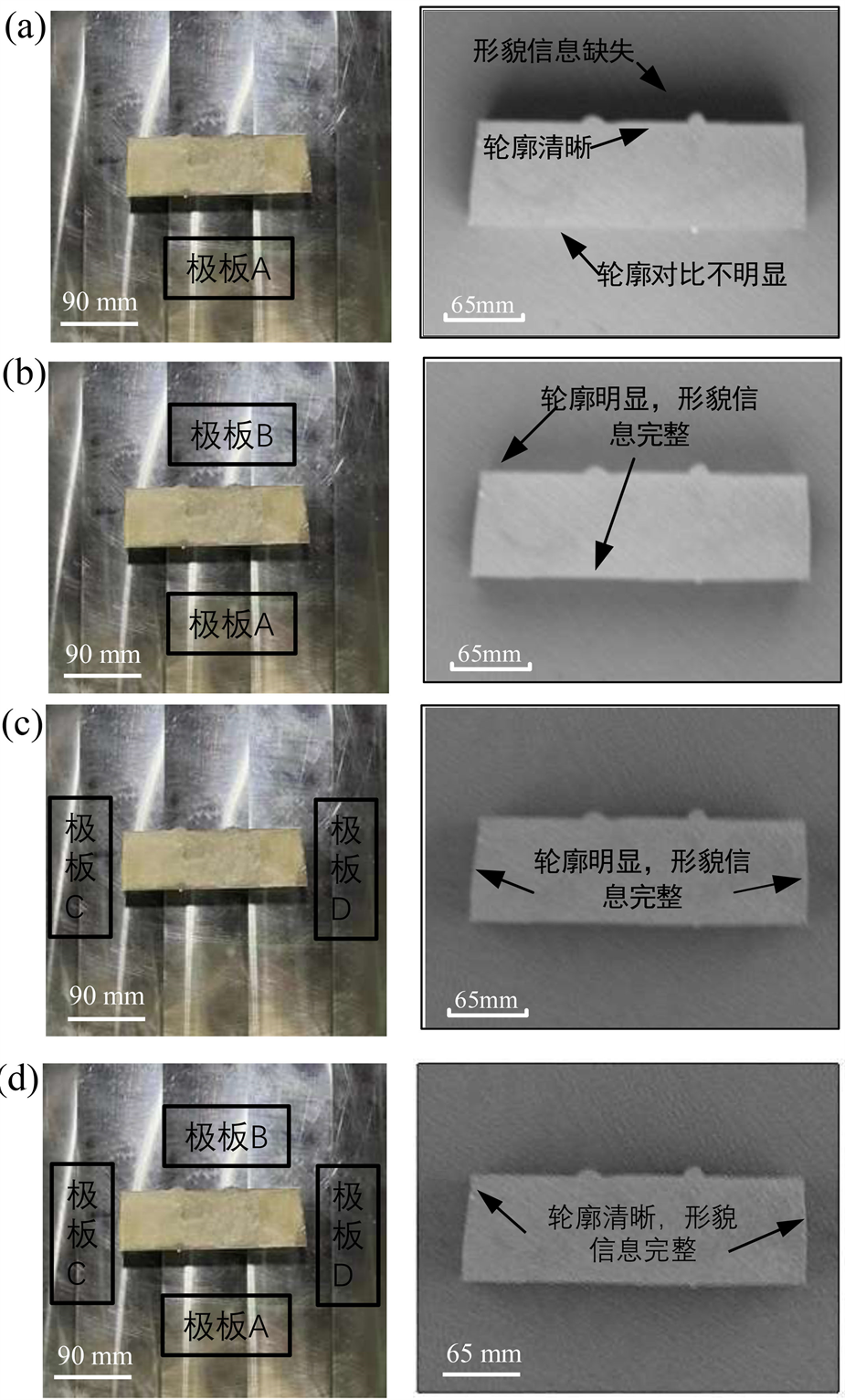
Figure 6. Position arrangement and backscattering morphology of sensor plates, (a) unipolar plate; (b) AB plate; (c) CD plate; (d) quadrupole plate
图6. 传感器极板的位置布置和背散射形貌,(a) 单极板;(b) AB极板;(c) CD极板;(d) 四极板
由图6(a)所示,单一方向布置的传感器极板A接收到的图像信息不完整,距离传感器极板较远部位成像信息会因为距离传感器较近的表面突起遮挡而丢失,但由此产生的遮挡部位与被遮挡部位之间明显的信号差会使得该部位轮廓信息加强,能够得到较清晰的轮廓信息。与传感器极板较近位置,接收到的背散射信号普遍较强,相对极板的物体轮廓及其周围信息能够被极板完全接收,且对比不明显,轮廓不清晰。
采用双极板传感器时,极板A、B相对观察对象布置如图6(b)所示。可见B极板得到的形貌信息,正好可以弥补观察对象距离A极板较远位置形貌信息的缺失,以及距离A极板较近位置轮廓对比不明显的问题。同理极板C、D按如图6(c)布置,通过融合C、D极板获得的单极板图像形貌信息同样优于单极板布置的图像。
通过四极板背散射电子传感器得到的四个方向上面的形貌信息,进行融合进而得到完整的四个方向上图像形貌信息,如图6(d)所示。可知四极板背散射传感器经过图像融合的图像四个边缘都很清晰,轮廓对比也很明显。得到的图像形貌信息明显优于单极板和双极板布置的形貌信息。
由上述试验结果可见,传感器极板的布置与数量会影响观察对象形貌信息的收集。单极板传感器只对背散射电子出射方向相对于该极板空间方位角大的方向形貌信息敏感,而其他方向,特别是被观察对象表面突起遮挡的部位,形貌信息会丢失。双极板传感器相对于单极板的形貌有明显改善,但边缘轮廓依然有些模糊。选择四极板背散射电子采集传感器可以完整采集观察对象表面形貌信息,通过图像融合处理可以得到完整的表面形貌图像。
4.2. 极板面积优化
对原有传感器极板进行改进,保持原有结构不变,使用4极板背散射电子传感器。增大传感器极板尺寸,使改进后的传感器极板采集面积增大为原来的两倍左右且正好能够完全“包裹”EBSM设备成形平台表面,如图7所示。优化前,单极板面积大约为0.03 m2,优化后单极板面积大约为0.09 m2,增大了两倍。
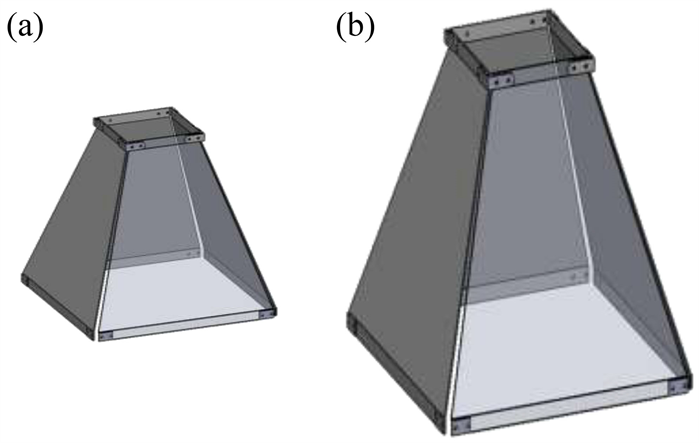
Figure 7. Sensor plate (a) before, (b) after optimization
图7. 传感器极板 (a) 优化前,(b) 优化后
选取图2(b)的实物为测试样品,优化前后得到的成形表面形貌图像如图8所示。优化前传感器极板得到的形貌图像整体偏暗,对比度小,细节丢失较多,优化后得到的图像细节明显,整体效果明显优于前者。由此可见,传感器极板面积对成像效果影响较大,传感器极板面积较小,对背散射电子信号的敏感度降低,生成的图像基本不能识别出表面纹理信息。大面积极板传感器对于背散射信号的采集能力较强,进而可以得到质量较高的图像。
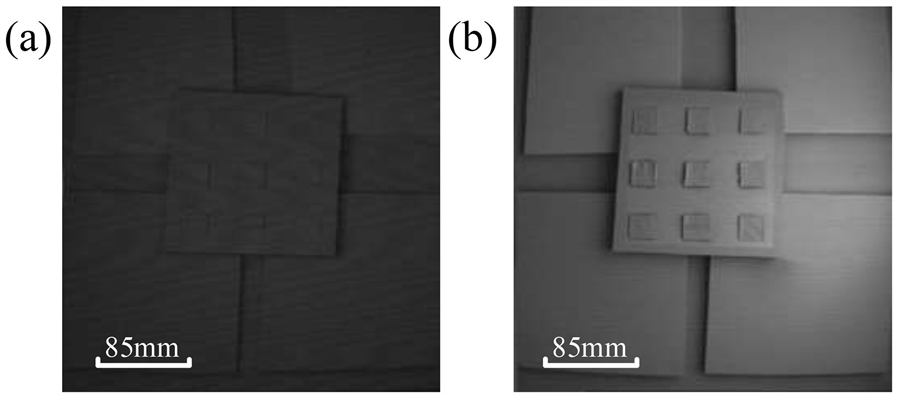
Figure 8. Backscatter imaging (a) before, (b) after optimization
图8. 背散射成像图 (a) 优化前,(b) 优化后
4.3. 背散射电子信号传感与放大电路优化
背散射信号采集电路的带宽由时间常数确定。实验时更改电路中的滤波电容,使时间常数减小,进而提高电路带宽。对原有背散射电子信号采集与传输电路进行改进,使优化后的电路带宽增大,并分别比较优化前后的成像效果。使用优化后的较大面积的四极板背散射传感器进行实验。
将图4所示放大电路中的滤波电容C1、C2、C3、C6、C7和C8由100 pF减小为的15 pF,电阻值保持不变,实验时选取图2(b)的实物为测试样品。使用优化前后背散射电子信号采集与传输电路,分别在不同扫描频率下进行成像实验。优化前所成图像如图9所示,扫描频率大于300 kHz时图像已经明显模糊,并在边缘出现畸变。优化后所成图像如图10所示,扫描频率大于300 kHz时,图像依然清晰。特别在扫描频率500 kHz时,前者已经完全模糊,后者仍能观察到细节。
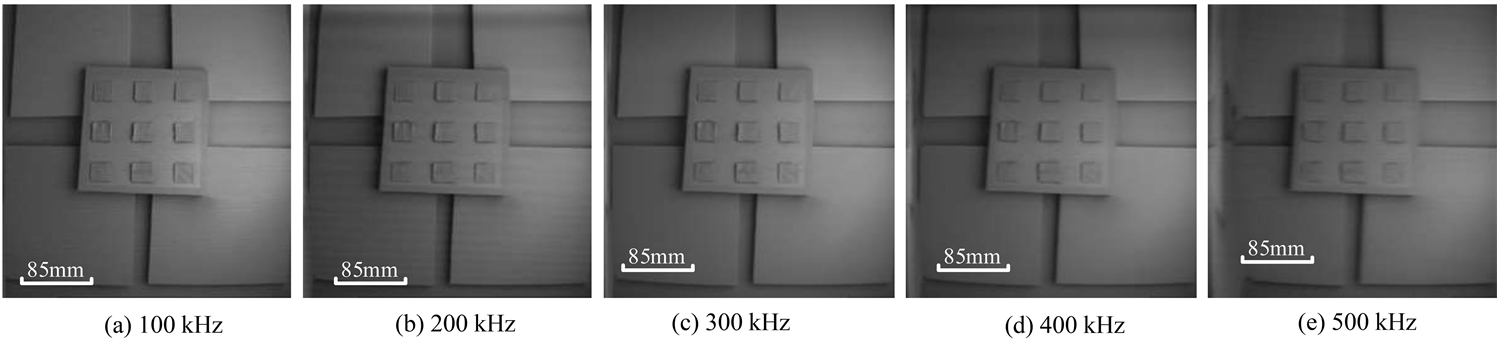
Figure 9. Scanning imaging at different frequencies before optimization
图9. 优化前不同频率下的扫描成像
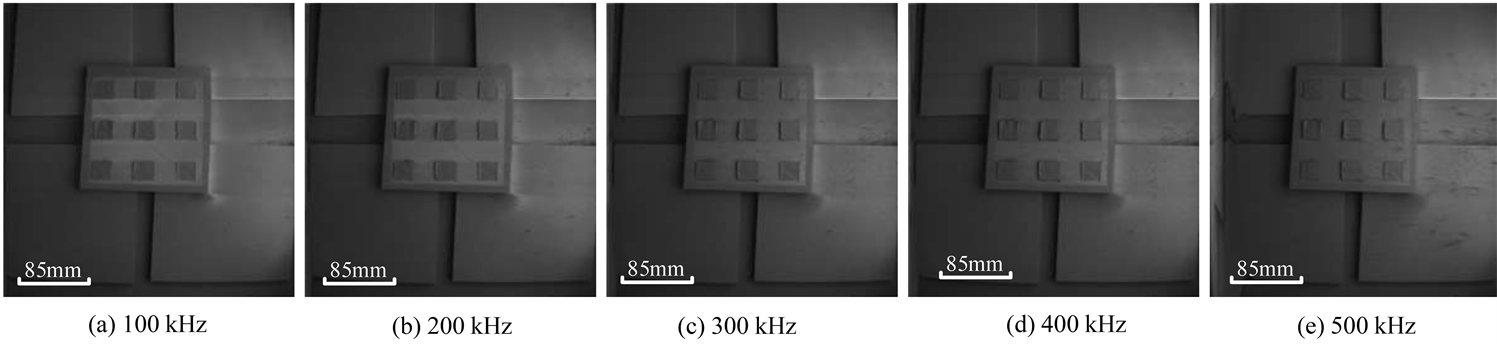
Figure 10. Scanning imaging at different frequencies after optimization
图10. 优化后不同频率下的扫描成像
由此可见,滤波电容的容值确实对背散射电子成像有较大影响。容值减小时,系统对于高频成像信号的处理更加灵敏,成像效果更好,扫描速度可以更快,分辨率和清晰度也更高。
5. 结论
本文基于背散射电子成像原理与背散射电子成像的在线监测系统,进行了背散射极板个数、单极板面积与滤波电容容值的优化,并实验得到优化后成形表面的背散射灰度图像,实现了清晰度明显提高的在线监测。最终确定为单极板面积0.09 m2的四极板对称布置背散射电子传感器,滤波电容为15 pF的优化系统。经过优化后系统成像的清晰度显著提高,扫描频率为500 kHz时依然可以清晰地成像。最终得到的监测系统可以实现360 × 360 mm的大范围监测,1200 × 1200像素的高分辨率成像,满足实际EBSM过程中在线监测的需求。
基金项目
广东省重点研发计划(2018B090904004),国家自然科学基金项目(51975036)。
NOTES
*通讯作者。