1. 前言
随着近年来国内石油生产一线的自动、信息化升级和更高安全生产要求的推进,二层台无人化和排管作业自动化的趋势愈来愈明显 [1] 。在石油天然气钻井和修井作业过程中,二层台自动化排管技术的应用已经成为一种标配,越来越多的排管机械手被用于替代二层台排管工作的人工作业,排管机械手的应用不仅降低了作业人员的劳动强度,改善了作业环境,也使排管工人的作业风险大大降低 [2] [3] [4] 。
随着机械手使用数量的增加,能够熟练操作排管机械的司钻人员也在紧锣密鼓的培训之中,在钻、修井作业过程也经常出现一些新手司钻作业的情况出现,由于一些新手司钻作业经验不足,偶有出现其操作机械手悬持管柱高度把控不准确的情况,造成管柱底部撞击钻台面的意外发生。并且,在司钻操作机械手停止运动后,由于电控系统和液压系统的滞后性,导致司钻发出机械手臂停止下放信号后,机械手臂机械向下运动过程中造成损伤管柱立根及钳牙的事故发生。
在钻修机进行修井作业时,由于使用的是油管,其管壁较薄,且是三根管柱的长立根,管柱刚性较差,发生管柱撞击钻台面时,可能出现机械手主动压弯油管立根,甚至压断油管立根的事故发生。在进行钻井作业过程中由于使用的是大直径钻杆,其刚度和强度较高,发生管柱撞击钻台面时,可能出现机械手夹钳与管柱发生相对上下滑动的现象,造成机械手夹钳钳牙损坏和管柱外壁磨损等意外发生。
2. 传统排管机械手存在的问题
为了避免上述使用机械手夹持管柱下放时,由于电控系统和液压系统的滞后性造成管柱撞击钻台面,同时由于机械手自身重量会压弯薄壁油管立根的情况发生,行业内均是增加监控设备,辅助司钻操作排管机械手,尽可能选用经验丰富的司钻操作排管机械手,经常对这些司钻进行培训,提高其对设备使用的安全意识,并且,严格执行安全责任制,使其收入与安全挂钩,以此来提醒司钻认真负责的操作排管机械手,达到降低管柱撞击钻台面的概率,以上做法确实降低了管柱撞击钻台面情况的发生,但不能完全避免施工事故的发生,因此,现阶段迫切需要一种在排管作业过程中可以避免管柱撞击钻台面同时实现机械手排管过程全自动化(自动停止下放管柱立根)的新技术。
3. 排管机管柱防撞与自动控制机构的结构组成及工作原理
为了解决上述因作业司钻由于操作经验欠缺及作业疏忽容易发生管柱撞击钻台面的问题,本文提出一种排管机管柱防撞与自动控制机构的结构,其利用机械结构与传感器自动控制功能完美的结合,在能够实现排管机械手作业过程全自动化的前提下还能使管柱与钻台平面的接触力在接触时抵消,到达防撞目的。
3.1. 排管机管柱防撞与自动控制机构的结构组成
排管机管柱防撞与自动控制机构是在钻修井起下钻作业过程中防止管柱撞击钻铤面的一种辅助装置,其主要包括:外壳支架、上螺母、下螺母、伸缩套、连接销、主芯轴、压缩弹簧及触发传感器等主要部件。排管机管柱防撞与自动控制机构装配完成后的外形如图1所示:
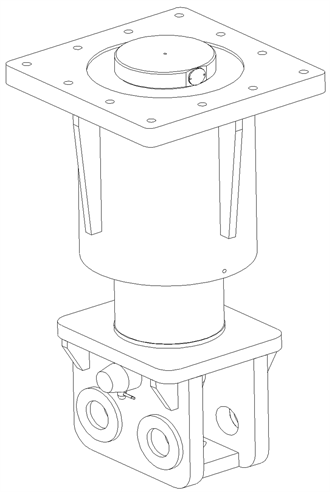
Figure 1. Schematic diagram of the external structure of the anti-collision and automatic control mechanism for the pipe string of the pipe arranging machine
图1. 排管机管柱防撞与自动控制机构的外形结构示意图
3.2. 排管机管柱防撞与自动控制机构的工作原理及功能
3.2.1. 排管机管柱防撞与自动控制机构的工作原理
图2中外壳支架为一中空圆筒结构,上部制作有方形法兰,方形法兰上加工有螺纹孔;外壳支架套装在伸缩套的上部,外壳支架的下端部装有下螺母,伸缩套插装在外壳支架内的部分装有压缩弹簧,压缩弹簧通过上螺母固定,伸缩套的中空部内装有主芯轴,主芯轴的上端通过T字头挂装在外壳支架的顶部,主芯轴的T字头端部上装有传感器,主芯轴的下端通过连接销与伸缩套的下部连接;伸缩套的上部通过下螺母与外壳支架下端固定,伸缩套能在下螺母内上下滑动,主芯轴的T字头端部通过螺纹与传感器连接;上螺母外壳支架的中空圆筒顶部形成一个缓冲运动空间,上螺母、伸缩套和主芯轴能在缓冲运动空间内一起上下移动,并通过上螺母使压缩弹簧压缩或复原。其结构组成原理图如图2所示:
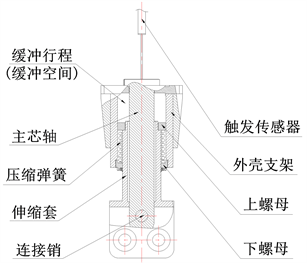
Figure 2. Schematic diagram of the structure and composition of the anti-collision and automatic control mechanism for the pipe string of the pipe arranging machine
图2. 排管机管柱防撞与自动控制机构的结构组成原理图
3.2.2. 排管机管柱防撞与自动控制机构的功能
排管机管柱防撞与自动控制机构是利用二层台自动排管机械手悬持管柱下放过程中,管柱底部接触钻台面时,依靠管柱防撞与自动控制机构的内部设置的空行程,外加压缩弹簧可克服管柱自身和夹钳自重,避免管柱提前发生弯曲变形,同时,在管柱接触钻台面的瞬间,触发传感器信号,控制系统自动判断管柱已经接触钻台面,控制电磁阀关闭液压缸动作,进而停止排管机械手继续下放管柱(不需司钻主动停止机械手下放管柱立根的动作),从而避免管柱大力撞击钻台面的原理。由于控制系统和液压系统均存在一定是滞后性,管柱防撞与自动控制机构内的压缩弹簧可最大化的吸收管柱接触钻台面的冲击力,可降低钻台面对油管反作用力,避免油管立根的弯曲或断裂,也可避免管柱立根与钻台面硬冲击力过大,使管柱立根与夹钳间发生锉动,造成钳牙磨损和管柱外壁损伤事故的发生。
4. 排管机管柱防撞与自动控制机构安装位置的选择
现阶段对于排管机管柱防撞与自动控制机构安装位置有三处可供选择:一是二层台排管机械手的上钳手与机械臂连接处;二是二层台排管机械手的下钳手与机械臂连接处;三是钻台机械手的夹钳与机械臂的连接处。现将排管机管柱防撞与自动控制机构安装上述三个位置的优缺性进行对比如表1:
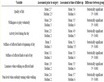
Table 1. Comparison of the advantages and disadvantages of anti-collision and automatic control mechanisms for the pipe string of the pipe laying machine at different installation positions
表1. 排管机管柱防撞与自动控制机构在不同安装位置优缺性的对比
通过三个方案的对比,方案二,将排管机管柱防撞与自动控制机构安装在二层台排管机械手下夹钳与机械臂连接处,该方案可使在较小的管柱弯曲变形,该管柱弯曲变形在系统运行允许的误差范围内,同时在系统运行过程中稳定性更高,故选择方案二为最优方案。最优方案如图3所示:
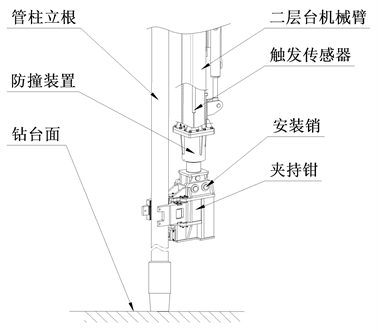
Figure 3. Schematic diagram of the relationship between anti-collision of pipe string and installation position of automatic control mechanism
图3. 管柱防撞与自动控制机构安装位置关系示意图
5. 压缩弹簧的选择
现阶段可以提供弹性力的主要机构有橡胶弹簧、机械弹簧及液气压弹簧等,现对以上三种弹簧在管柱防撞与自动控制机构上使用的优劣性作出如下分析,如表2所示:
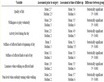
Table 2. Spring performance comparison
表2. 弹簧性能的对比
通过三个方案的对比,方案三,在排管机管柱防撞与自动控制机构上使用圆筒形状的机械式压缩弹簧,其结构形式不仅非常复合安装要求,在能提供大的弹性力行程的前提下,同时也能提供复合使用要求的弹性力,并且机械式的压缩弹簧,其弹性力受使用环境的温度影响较小,且其使用寿命也很高,需要维护保养的要求相对较低,非常符合在高空二层台排管机械手上使用,故选择方案三为最优方案。
6. 触发传感器的选择
在常用的带有触发功能的传感器有:行程开关、接近开关、电阻式电子尺、磁致伸缩位移传感器、激光位移传感器等,其中,行程开关和接近开关均为点位控制传感器,其触发信号均为一个点,没有全行程检测功能,故,在本次选择触发传感器应排除在选择范围之外,现电阻式电子尺、磁致伸缩位移传感器、激光位移传感器三种线性位移传感器的性能做如表3的对比:
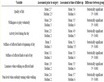
Table 3. Performance comparison of displacement sensors
表3. 位移传感器的性能对比
通过三个方案的对比,方案二,在排管机管柱防撞与自动控制机构上使用磁致伸缩位移传感器,其优良的防爆性能十分符合石油天然气行业内严格的防爆要求,可以有效增强作业的安全性,同时其优良的稳定运行性能也可以使排管机械手每次作业需要触发停止动作均能有效实现,可以大大的提高作业效率,故选择方案二为最优方案。
7. 结论
二层台排管机械手在悬持管柱下放过程中,当管柱立根底部接触到钻台面时,管柱立根相对于钻台面静止不动,机械手臂继续下行时,由于夹钳夹持住管柱立根,此时,夹钳相对于机械手臂向上运动,也带动自动控制机构的主芯轴相对向上运动,触发传感器停止信号,停止机械手臂的下放动作,起到了自动停止机械手下放管柱动作的功能。(不需司钻主动停止机械手下放管柱立根的动作)
由于自动控制机构内设置有缓冲运动空间,此缓冲运动空间可以解决由于电控系统和液压系统的滞后性,导致司钻发出机械手臂停止下放信号后,机械手臂机械向下运动过程中压弯薄壁管柱立根和损伤管柱立根及钳牙的事故发生。
由于自动控制机构内设置有压缩弹簧,管柱立根接触钻台面初期,夹钳和管柱立根自重由压缩弹簧弹力承担,不会出现由于夹钳和管柱立根自重将管柱立根压弯的情况,继续下放过程中能够带动排管机械手的夹钳上移,进而带动自动控制机构的主芯轴上移,触发传感器控制电磁阀关闭液压缸动作而停止排管机械手继续下放管柱,防止由于夹钳自重压弯管柱导致不能触发传感器,机械手不停止下放动作的问题发生,同时也解决了二层台机械手排管作业全自动化的问题。
基金项目
海洋模块钻机自动化管理及操作系统研究服务,2022-FW-GK-HYFZ-1930/01。
NOTES
*通讯作者。