1. 引言
基于模型定义(Model-Based Definition, MBD)技术是数字化设计的发展趋势,是工程设计语言表达方式的一次技术革新。其核心思想是:全三维基于特征的表述方法,通过三维主模型驱动,融入知识工程和产品标准规范。它用一个集成的三维实体模型来完整的表达产品信息,将制造信息和设计信息共同定义到产品的三维数字化模型中,从而取消二维工程图纸,保证设计和制造流程中数据的唯一性 [1] [2] [3]。当前,MBD技术在国外已经得到了深入的推广应用,但在国内起步较晚,仍处于探索和研究阶段,主要是因为对MBD技术如何适应国内的研发模式缺少研究,在MBD技术实践应用过程中缺乏设计工艺一体化的意识,特别是在重用MBD设计模型快速构建MBD工艺模型的关键技术上少有文献报道 [4] [5]。现由于大部分有能力推广MBD技术的企业研发部门和工艺部门相互独立,模型数据传递的连续性受到破坏,工艺部门常常需要重新构建工艺模型,工作量大,且重新建模容易出现人为错误 [6] [7] [8]。本文在企业数字化科研体系建设过程中,对MBD技术的设计工艺一体化实践应用进行深入研究,结合企业实际需求,对三维设计软件进行定制化开发,通过智能化工艺扣镀层、中差模型转换、尺寸标号等功能,快速实现MBD工艺模型构建,大大提升工艺设计效率,打破设计工艺壁垒,并最终以三维可视化作业指导书的形式传递至下游。从而打通基于MBD的产品研发、生产制造、检测全流程,为数字化企业的实现奠定坚实的基础。
2. MBD设计工艺一体化技术路径
基于MBD的设计工艺一体化技术路径如图1所示。设计部门采用全三维的设计模式,MBD设计模型应包括能够完整描述产品生产制造的属性、尺寸及公差、形位公差、镀覆要求、粗糙度、特殊要求等制造信息PMI (Product manufacturing Informationg,产品制造信息),设计发布前要经工艺部门审查,设计发布后由工艺路线工程师以结构化工艺的形式附带设计模型发送至具体工艺负责人;工艺部门直接重用MBD设计模型,继承全部PMI信息,然后先后利用“扣镀层工具”、“中差模型转换工具”、“尺寸标号工具”等快速完成模型的镀层扣除,中差模型转换,尺寸自动标号,从而得到MBD工艺模型,MBD工艺模型嵌入结构化工艺中进行归档发布;制造部门在接到生产计划后直接利用发布的MBD工艺模型,由于MBD工艺模型为中差工艺模型,名义尺寸即模型实际尺寸值,可直接将模型放入仿真软件,快速完成CAM编程,仿真加工的程序经过适当校正后传至机床进行生产制造;生产制造的零件可通过基于Web在线作业指导书检验流转,先进的设备甚至能够实现根据模型信息在线检测。
3. MBD设计模型的构建
一个完成的MBD设计模型应该包含三维模型、三维标注和必要的属性。三维建模技术现已较为成熟,关于三维标注,在两百多年二维工程图思维主导下,设计师们习惯的尺寸标注方式为基轴基孔制,便于直观观察尺寸配合关系。在企业实施MBD技术时,仍然可以采用名义尺寸、非对称公差的方式进行三维标注。但是基于MBD的设计工艺一体化的实现源头是设计,在MBD技术实施时,需充分考虑模型最大化快速重用方案,工艺部门要充分参与方案的讨论和验证。本企业采用NX三维软件作为设计工具,不同于其他三维软件的标注方法,在NX中进行草图绘制的同时,可以在草图尺寸中添加公差,
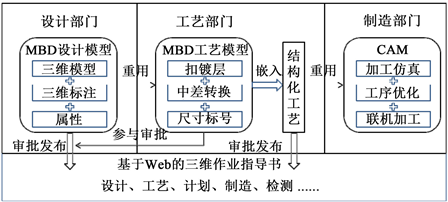
Figure 1. Technical path of integration of design process based on MBD
图1. 基于MBD的设计工艺一体化技术路径
并将添加公差后的草图尺寸转化成PMI尺寸标注,这样转换得到的尺寸信息自然建立了和草图尺寸的关联,这种关联关系便于下游部门开展PMI尺寸信息重用驱动模型转换,草图尺寸必须全约束以保障模型的稳定性。采用草图尺寸转换为PMI的方式可以完成大部分三维尺寸标注的工作,相对于传统三维完成后再重新标注尺寸的方法,极大地提升了三维标注效率,再添加形位公差、表面粗糙度、特殊技术要求信息及其他属性信息得到完整的MBD设计模型。MBD设计模型需按照企业标准规范的要求进行模型规范性检查,以保证草图尺寸全约束、三维标注规范、建模规范等,如图2所示。
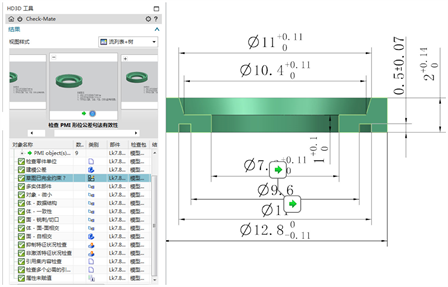
Figure 2. Normative inspection of MBD design model
图2. MBD设计模型规范性检查
4. MBD工艺模型的转换
目前,很多企业在推广MBD技术应用过程中感觉困难重重,主要原因就是工艺部门人员需要花费大量的时间和精力重建MBD工艺模型,原工艺人员资源配置难以满足要求,且出错概率较大,风险较高。因此,要实现基于MBD的设计工艺一体化,MBD工艺模型快速、准确、规范的构建显得非常重要 [9]。本企业结合工艺部门MBD工艺模型构建的主要工作内容,在NX三维设计软件基础上,使用VS2012作为开发工具,采用UGOPEN/API、NXOPEN的开发方式进行二次开发,实现了智能化扣除镀层、一键转换中差模型、PMI尺寸自动标号等功能。工艺人员最大化重用MBD设计模型,快速转换成工艺需要的MBD工艺模型,极大的减轻了工艺工作量,使得MBD技术在企业顺利推广使用。MBD工艺模型转换步骤如图3所示。
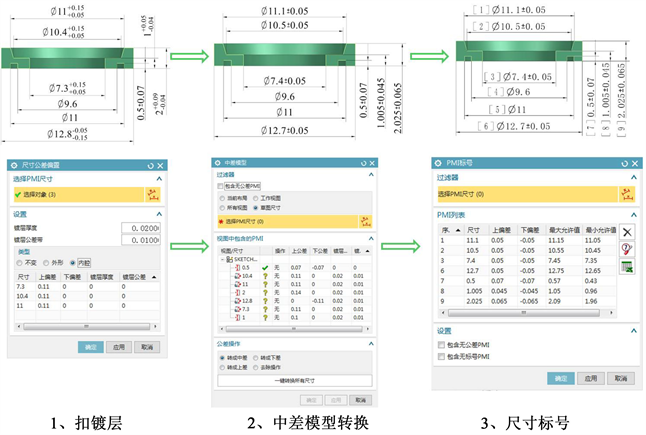
Figure 3. Legend of MBD process model conversion steps
图3. MBD工艺模型转换步骤图例
设计图纸尺寸通常为产品镀覆后的尺寸,因此,扣除镀层尺寸是工艺设计师开展工艺工作的重要内容。公司以前的方法是通过工艺工程师逐步遍历所有的设计尺寸,并根据产品结构设计依次判断该尺寸公差放大或缩小的类型,然后通过手工计算,得到扣除镀层厚度及公差余量后的公差值,再改变设计尺寸公差,得到工艺图纸,该方法计算繁琐、容易出错、工作量大。采用自动扣镀层工具后,系统自动搜索工作部件中所有PMI尺寸,读取PMI尺寸值、上、下公差值,工艺人员指定PMI尺寸类型及镀覆种类后运行程序,程序便会自动计算并修改公差值,最终实现在PMI尺寸公差上扣除镀层厚度及公差余量,得到扣除镀层后的MBD工艺模型,极大的提高了工艺处理效率和准确性,如图3中的步骤1所示。
扣除镀层后的MBD工艺模型仍然无法进行机加仿真编程,需转换成中差模型,中差模型是指尺寸公差均为对称公差的三维模型,三维模型实体名义尺寸即为理想化实体尺寸值,名义尺寸可直接作为机加工艺人员CAM编程的输入值。要真正意义提升设计、工艺协同研发效率,中差工艺模型的转换和利用至关重要。采用中差模型转换工具后,系统自动提取工作部件中所有带有公差的PMI尺寸,然后计算上、下公差值,并改变名义尺寸,同步驱动模型更改,极大地提高了中差模型的转换效率,如图3中的步骤2所示。MBD中差工艺模型作为三维工艺设计的源头,可以提升工序模型的构建效率和CAM编程效率,从而整体上提升三维工艺的编制效率。
关于尺寸标号,公司原有的方式是手动一个个对尺寸进行标号,然后检验人员根据尺寸标号手工填写尺寸检查表,效率低,还存在尺寸写错的风险。采用尺寸自动标号工具后,软件可以对PMI尺寸自动标号,并根据标号一键生成尺寸检测表,作为零件检验控制卡,如图3中的步骤3所示。同时,具有标号的MBD工艺模型能够为生产、检测各环节提供友好的显示,方便线下线上尺寸的一一对应。
5. 基于Web的在线三维作业指导书
基于MBD的作业指导书是整个MBD技术推广应用的重要一环,是连接器虚拟世界和物理世界的纽带和媒介。有了三维设计模型,如何将三维设计模型应用到现场,是很多制造企业头疼的问题。有些企业将三维设计模型直接搬到车间的大屏幕作为展示,更有些企业将三维转换成二维工程图再下发到现场。本企业采用基于Web的在线三维作业指导模式,通过Web端输入生产制造的零部件信息,便可直接从管理平台Teamcenter服务器获取结构化工艺,包括工序流程图、操作描述、工艺资源和三维模型等,如图4所示。采用Web的在线三维作业指导模式打通了基于MBD技术的最后一道屏障,是一种轻量化模型展示方法,普通电脑即可支持使用,使得现场不用像设计部门一样配备高性能计算机,从而降低了推广使用成本。相对于传统二维工程图,三维工艺可以通过放大、缩小、旋转、移动、剖切、测量等各种手段直观、灵活的展示设计意图,缩短了原来的读图、理解消化时间,降低出错率。且设计工艺完成更改后,Web端的信息自动更新,消除了现场图纸更新不及时可能存在隐患。
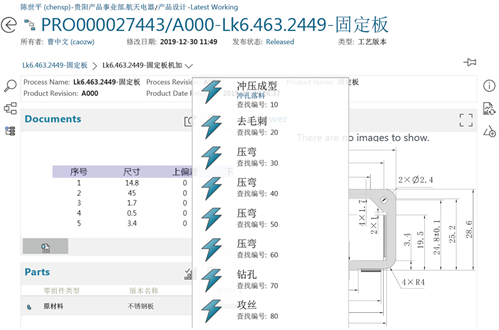
Figure 4. 3d work instruction based on Web
图4. 基于Web的三维作业指导书
6. 结论
在推广基于MBD技术应用的过程中,对设计工艺一体化关键技术进行了深入研究和实践应用。结合企业实际需求,对三维设计软件进行定制化开发,实现了基于MBD设计模型的智能化工艺扣镀层、一键中差模型转换、PMI尺寸自动标号等功能,从而快速实现MBD工艺模型的转换,大大提升工艺设计效率,打破设计工艺壁垒,最终以基于Web在线三维作业指导书的形式传递至下游环节,打通了基于MBD的产品研发、生产制造、检测全流程,为基于模型的数字化企业建设奠定了基石。