1. 背景
目前,餐厨垃圾在处置时,大多数采用厌氧发酵处理技术 [1] ,经厌氧发酵后的污水可生化性较差,B/C比一般不足0.1,后续需配套膜法进行污水处理。而老旧填埋场渗滤液则面临着碳源严重不足,需采购甲醇或葡萄糖等进行碳源补充。
主流的餐厨垃圾厌氧处置工艺采用全混合湿式厌氧发酵。由于餐厨垃圾中含有大量的油脂,厌氧发酵系统中的微生物会被油脂包裹并被其带到发酵系统上层,降低发酵系统中微生物量,此外油脂的水解产物长链脂肪酸(LCFA)会吸附在产甲烷菌细胞膜上,干扰微生物对有机质的吸收,油脂的存在对厌氧发酵产甲烷抑制明显。同时,由于厌氧发酵过程中,氨氮浓度不断积累,容易造成整个厌氧系统的氨中毒,抑制甲烷菌的生长,从而影响厌氧消化的产气效率。实际运营中,厌氧系统运营要求较高,需定期进行污泥补充 [2] [3] 。
杭州市某产业园内运行老龄化填埋场一座、餐厨垃圾处理项目(200吨\天)一座以及配套填埋渗滤液处理厂。本工艺的技术核心为水解产酸,通过将传统的厌氧发酵停留在水解酸化阶段,将餐厨垃圾低成本的转化为高浓度、易生物降解的有机酸化液。该酸化液具有极佳的可生化性,没有毒害作用,从而可以有效地替代价格昂贵的商品碳源 [4] [5] [6] 。国内外研究中,酸化液可作为养殖废水、生活污水、化工废水的碳源应用于生物脱氮除磷,而在渗滤液处理的实际工程应用中,相关研究较少。本文通过餐厨垃圾厌氧发酵罐附加酸化改造工程的实施,将餐厨垃圾所产生的污水供给渗滤液处理厂进行碳源补充,探究园区化建设过程中的产业协同之路,实现生态效益、经济效益双赢 [7] [8] 。
2. 试验方法
2.1. 酸化液稳定产出测定方法
本次试验以工程化实施为最终目的,在实验室内模拟产酸过程,通过对酸化液TS、COD、NH3-N、TN、C/N、VFAs的指标的监测,最终确定适宜的pH、温度、停留时间,从而产出稳定、优质的酸化液。完成实验室小试后,将餐厨处理项目原有厌氧系统进行改造,进行产酸工程化实践。
TS:将瓷坩埚洗涤后在600℃马弗炉灼烧1 h,待炉温降到100℃后,取出瓷坩埚并于干燥皿中冷却称重。记作a g;取V ml样品,置于坩埚内,称重,记作b g。然后放入干燥箱,在105℃ ± 2℃下干燥至恒重,重量记作c g;将含干燥后样品的坩埚放入马弗炉,在600℃下灼烧2 h,待炉温降到100℃后,取出瓷坩埚并于干燥皿中冷却后称重,记作d g。TS = [(c − a)/(b − a)]*100%
COD:先对样品进行匀质化处理,并根据量程稀释一定倍数;打开DRB200反应器,预热到150℃;取两支COD TNT试剂管放试管架,除去试剂管上的盖子;用清洁的移液管吸取2.00 mL去离子水添加到第一支20~1500 mg/L试剂管中为空白样;用清洁的移液管吸取2.00 mL样品添加到第二支20~1500 mg/L 试剂管中为测定样品;拧紧管盖,用清洁的纸巾擦干试剂管外壁;在水池上方拿住管盖的一端,上下颠倒几次混匀,将试剂管插入预热的DRB200反应器中,盖上保护盖;加热2试剂时;关闭反应器,等待大约15分钟,使试剂管冷却到120℃或更低的温度;将试剂管放到试管架上,使其冷却到室温;在DR3900分光光度仪上选择COD测试程序;先用湿布擦拭试剂管外壁,再用干布擦净;将空白管和样品管先后插入到仪器圆形样品隔室中,按零校准后读数;使用高量程COD消解试剂管,将所得的结果乘以稀释倍数,即得最终结果。
注:氯离子含量过高会对实验精确度产生影响,可在添加样品前,在各COD小瓶中添加0.5 g硫酸汞以屏蔽氯离子的干扰。
NH3-N:在DR3900分光光度仪上启动氨氮测试程序;先对样品进行抽滤处理,并根据量程稀释一定倍数;取两支NH3-N管放试管架,除去试剂管上的盖子;用清洁的移液管向第一支试剂管中加入0.1 mL无氨水为空白样;用清洁的移液管向第二支试剂管中加入0.1 mL样品为测定样品;分别向两支试剂管中各加入一包水杨酸盐试剂粉枕包;再分别向两支试剂管中各加入一包氰尿酸盐试剂粉枕包;盖紧盖子,上下摇晃试剂管时粉末溶解;计时反应20分钟后,将空白值的试剂管擦拭干净进行校准;将样品管擦拭干净放入隔室中,读取氨氮结果;将所得的结果乘以稀释倍数,即得最终结果。
TN:打开DRB200反应器,预热到105℃;先对样品进行抽滤处理,并根据量程稀释一定倍数;取两支Total-N试剂管放试管架,除去试剂管上的盖子;用清洁的移液管向第一支试剂管中加入0.5 mL去离子水为空白样;用清洁的移液管向第二支试剂管中加入0.5 mL样品为测定样;分别向两支试剂管中各加入一包总氮过硫酸盐试剂粉枕包;将两支试剂管盖上盖子,猛烈摇晃30秒以混合;将试剂管插入消解器,盖上保护盖,加热消解30分钟;结束后,将热的试剂管从消解器中取出,放在试剂管冷却架上冷却至室温;分别向两个试剂管中个加入一包总氮A试剂粉枕包,盖上盖子,上下摇晃试剂管15秒,计时反应3分钟;再打开瓶盖,分别向两个试剂管中各加入一包总氮B试剂粉枕包,盖上盖子,上下摇晃试剂管15秒,此时溶液开始变成黄色,计时反应2分钟;计时结束后,打开两个TN C总氮C试剂管,将2 mL空白值的消解液加入到第一支TN C总氮C试剂管中,将2 mL样品的消解液加入到第二支TN C总氮C试剂管中;盖上盖子并倒转试剂管10次以上以混合均匀,缓慢的小心的倒转试剂管,计时反应5分钟,此时溶液的黄色应该变深;计时反应结束后,将空白值的试剂管擦拭干净进行校准;将样品管擦拭干净放入隔室中,读取TN结果;将所得的结果乘以稀释倍数,即得最终结果。
VFA:在DR3900分光光度仪上启动挥发酸测试程序;对样品进行抽滤处理,并根据量程稀释一定倍数;取两只比色管,制备空白样与测定样与TN一致;分别向两支比色管中各加入1.5 mL乙二醇溶液,混合均匀;分别向两支比色管中各加入0.2 mL稀硫酸溶液,混合均匀;水浴加热3分钟;分别向两支比色管中各加入0.5 mL盐酸羟胺溶液,混合均匀;分别向两支比色管中各加入2.0 mL氢氧化钠溶液,混合均匀;分别向两支比色管中各加入10 mL酸性氯化铁溶液,混合均匀;分别向两支比色管中各加入10 mL去离子水,混合均匀,计时反应三分钟;取两只干净的比色皿,从两支比色管中分别移取10 mL溶液到比色皿中;将空白值的比色皿擦拭干净进行校准;将样品比色皿擦拭干净放入比色皿隔室中,读取VFA结果;将所得的结果乘以稀释倍数,即得最终结果。
2.2. 酸化液代替商品碳源可行性测定
通过碳当量核算渗滤液厂每日酸化液需求量,逐步提升每日酸化液代替商品碳源的使用量,监测渗滤液厂生化出水段COD、NH3-N、TN变化情况,测定酸化液代替商品碳源的可行性。
驯化阶段:第一天至第四天启动驯化,向产酸池内投加15方厌氧污泥及45方的餐厨液相,停留4天,完成酸化液的前期驯化。
如表1,稳步提升负荷阶段:第五天起,逐步提升渗滤液厂酸化液使用量,直至全部替代,每日监测酸化液与渗滤液的混合液对渗滤液处理厂生化段出水指标的影响情况,确定酸化液使用量提升。
稳定运营阶段:待酸化液使用量增加到全部替代(60吨\天)后,稳定、连续供应,每日监测酸化液与渗滤液的混合液对渗滤液处理厂生化段出水指标的影响情况,确定后续连续投加酸化液是否可行。
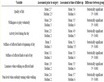
Table 1. Consumption of acidizing fluid used in leachate treatment plant
表1. 渗滤液处理厂酸化液使用情况
3. 结果分析与讨论
通过实验室小试,确定餐厨垃圾预处理出水水质研究最佳的工艺条件为:反应温度为35℃、pH为6、停留时间4天、选用餐厨垃圾预处理新鲜出水为原料进行酸化试验。
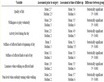
Table 2. Indicators of acidizing fluid
表2. 酸化液各类指标
通过上述表2数据可看出,在PH = 6 [9] 、35℃的酸化环境中,停留4天,酸化液的VAFs维持在15,000 mg/L,COD为150,000 mg/L左右 [10] ,酸化液各项指标稳定。通过碳当量核算,渗滤液处理厂每日需酸化液60吨。将该酸化液投加至渗滤液厂生化段,通过逐步提升酸化液使用量直至60吨\天(根据碳当量核算的酸化液需求量) [11] 。待酸化液提升至60吨后,渗滤液厂停止了原碳源补充剂——葡萄糖的添加,随后对渗滤液厂生化段出水COD、NH3-N、TN进行监测。
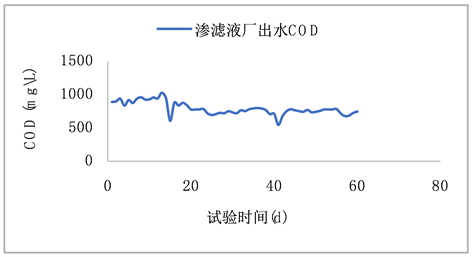
Figure 1. COD of effluent from biochemical section of leachate plant after using acidification liquid
图1. 使用酸化液后渗滤液厂生化段出水COD情况
如图1所示,渗滤液厂生化段出水COD浓度在稳步提升负荷阶段(第5天~第35天)保持在606 mg/L~1028 mg/L,COD浓度较高且在15天内呈上升趋势,这是因为由于餐厨垃圾水解酸化液成分比较复杂,存在很多难降解有机物,使得出水COD的浓度有一定升高 [12] ,同时高VAFs的酸化液也会影响生化段菌种活性;而在稳定运营阶段(第35天以后),渗滤液厂生化段出水COD浓度保持在584 mg/L~800 mg/L范围内,这说明酸化液中的难降解有机物已被微生物逐渐降解,也可能是因为生化段菌种对酸化液高VAFs的耐受性加强,COD降解率大大提高 [13] 。综上所述,稳定运营阶段每日投加的酸化液可以作为碳源完全代替相同碳当量的葡萄糖,并且满足污水厂生化段出水COD标准要求COD < 800 mg/L。
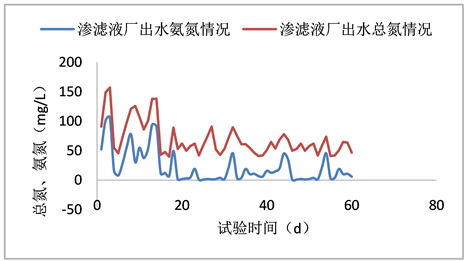
Figure 2. Total nitrogen and ammonia nitrogen in effluent of biochemical section of leachate plant after using acidification liquid
图2. 使用酸化液后渗滤液厂生化段出水总氮、氨氮情况
如图2所示,在酸化液作为碳源代替葡萄糖的条件下,酸化液投加18天后,出水NH3-N含量小于100 mg/L,满足排放标准;投加34天后,出水TN含量小于50 mg/L,满足排放标准。
通过对于餐厨垃圾项目原厌氧系统进行改造,实现餐厨垃圾出水定向产酸,通过对于PH、温度、停留时间等多个指标对产酸环境进行控制,酸化液指标稳定,达到实验室小试预期。
将该酸化液投加至渗滤液厂生化段,通过逐步提升酸化液使用量直至60吨\天(根据碳当量核算的酸化液需求量)。待酸化液提升至60吨后,渗滤液厂停止了原碳源补充剂——葡萄糖的添加,渗滤液处理厂生化段工艺仍可满足原控制要求(COD < 800 mg/L; NH3-N < 50 mg/L; TN < 100 mg/L)。
4. 结论
餐厨垃圾预处理出水经水解产酸后形成的酸化液对商品碳源有着显著的代替作用 [14] 。在园区化的建设模式下,通过厌氧发酵工艺的产氢改造,减少了厌氧发酵后难降解污水的产生量,将其变为有价值的副产物;而渗滤液厂则得到了更加安全、廉价的碳源。伴随着垃圾处置行业的蓬勃发展,可以预见,在不久的未来,园区化的垃圾处置模式将成为焦点。通过垃圾处置各环节的紧密协同,形成项目合力,实现环保项目在经济效益上的自我造血 [15] [16] 。