1. 引言
锰矿及其深加工产品被广泛应用于钢铁、有色冶金、化工、电子、电池以及农业等方面 [1],我国电解锰产业规模随着经济的发展而逐渐扩大,年产量达120万t/年 [2],成为全球最大的电解锰生产、出口和消费国 [1]。
电解锰阳极泥是生产电解锰时阳极板上产生的副产物,每生产1 t电解金属锰一般伴随50~150 kg阳极泥的产生 [3],由于阳极使用含铅阳极板,使得电解锰阳极泥含有一定量的铅 [4],给回收利用造成困难,除少量用于电解锰厂的锰矿浸取液除铁外,大部分阳极泥被堆积或以低价外卖,造成环境污染和资源浪费。
目前针对阳极泥的回收利用已有不少报道,还原法由于步骤简便,浸取率高且易于分离而被普遍利用。主要的还原方法有高温焚烧还原、湿法还原浸出、微生物还原浸出等。如蔡振勇 [5] 采用高温焙烧还原法,高温下加入还原剂使二氧化锰还原为氧化锰,再与硫酸反应得到硫酸锰。申永强 [6] 将电解锰阳极泥渣与氢氧化钠在高温下煅烧氧化,再经甲醛还原制备MnO2。还原焙烧法因能耗过高、产生氮氧化物以及硫氧化物等二次污染物,且渣中有煤渣的进入不利于铅的回收,已逐渐被淘汰。刘建本等 [7] [8] 以SO2尾气为还原剂浸取电解锰阳极泥,制得的硫酸锰可以达到工业级标准要求。但该方法存在副反应,产生连二硫酸盐,难以处理转化,不利于进一步利用,且SO2是气体不易贮运。黄齐茂等 [9] [10] [11] [12] 采用木屑、橘子皮、玉米秆等有机物作为还原剂,湿法浸出阳极泥中锰,实现锰铅高效分离。有机物木屑等虽廉价易得,但其自身不可作为还原剂,需先水解或酶解生成还原糖类等还原性物质,产生酸性废水较多,不易处理。微生物还原浸出法作为一种新兴方法,近年来研究也有所增加。Zhang [13] 利用混和自养培养法,在黄铁矿和硫的混合作用下从低品位软锰矿中浸出锰。生物浸取法虽然可行,但生物活性比较低,耗时长,同时消耗微生物生长所需营养物,难以实现工业化。因此,选择合适且廉价的还原剂成为研究的热点,本研究以湘西某工厂的阳极泥渣为原料,采用廉价易得的硫磺为还原剂,探讨温度、反应时间、酸矿比和硫酸浓度对锰浸取率的影响,从而实现阳极泥中锰的回收利用。
2. 材料与方法
2.1. 材料、试剂和仪器
电解锰阳极泥来自湖南湘西某工厂,呈黑色块状,含水率为5%。将锰渣洗矿处理后置于鼓风干燥箱中烘干至恒重,温度设置为105℃。经研磨粉碎过筛后,存放于干燥箱中备用。
实验试剂:硫酸锰、二氧化锰、硫酸、硫磺等均为分析纯。实验用水为去离子水。
实验主要仪器:D/max-γA型X-射线衍射仪(日本Rigaku公司);Magicube高压超声波微波协同组合工作站XH-200PE(北京祥鹄科技有限公司);ICAP6300型电感耦合等离子体发射光谱仪(ThermoFisherScientific.USA);FlexSEM1000型扫描电镜(日立高新公司)。
2.2. 实验方法
称取10 g干燥后的阳极泥渣于反应罐中,采用单因素实验法,探讨硫酸浓度(2、4、6、8、10、12、14和16 mol∙L−1)、反应时间(1、2、3、4和5 h)、反应温度(60、70、80、90、100、110和120℃)和酸矿比(1.5、2.0、2.5和3.0 mL/g)对锰浸出率的影响。其中主罐加入2 g硫磺粉末,对照组不添加硫磺,放置于高压超声波微波协同工作站中,于恒温条件下搅拌反应一定时间。反应完成后用150 mL去离子水分3次洗涤阳极泥渣,合并滤液和洗涤液并量取体积。准确移取少量滤液,采用ICP仪器测定锰浓度。滤渣烘干后称重,消解后采用ICP仪器测定其中Mn以及其他金属元素的含量。采用XRD测定阳极泥反应前后各主要成分的晶体结构。
2.3. 曲面响应优化设计
根据单因素实验结果,利用Design-Expert.V8.0.6.1软件中Optimal模块,选择温度、时间、酸矿比以及硫酸浓度4个条件作为实验因素,以阳极泥中Mn的浸取率为响应值,设计四因素四水平实验,筛选最佳浸取条件。实验因素水平设计及编码见表1。
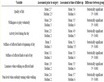
Table 1. Experimental factors and level coding
表1. 实验因素及水平编码
3. 结果与讨论
3.1. 反应前后阳极泥成分分析
阳极泥渣反应前后化学成分变化如表2所示,反应前阳极泥Mn含量高达54.952%,其次为Mg,有害物质Pb含量也较高,其他金属元素含量甚微。未加硫磺反应后的滤渣,Mn的质量分数为53.840%,其只被少量浸取。而加硫磺反应后滤渣Mn含量为2.694%,表明大部分Mn被浸取进入液相。
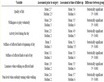
Table 2. Components of solid waste after the reduction (mass fraction/%)
表2. 阳极泥还原反应前后化学成分分析(质量分数/%)
图1为阳极泥和硫磺反应滤渣的XRD图谱,结合表2分析可知:电解锰阳级渣结晶度较差,图1(a)中有MnO2、Mn(OH)4等Mn化合物的衍射峰存在,说明Mn以多种化合物形式存在,同时Pb与Mn的氧化物络合。加入硫磺还原反应后,滤渣XRD图谱如图2(b)所示,主要成分为PbSO4和Na2-XMn8O16,说明Pb主要以PbSO4形式存在。MnO2和Mn(OH)4衍射峰消失,说明阳极泥中MnO2和Mn(OH)4基本反应完全。
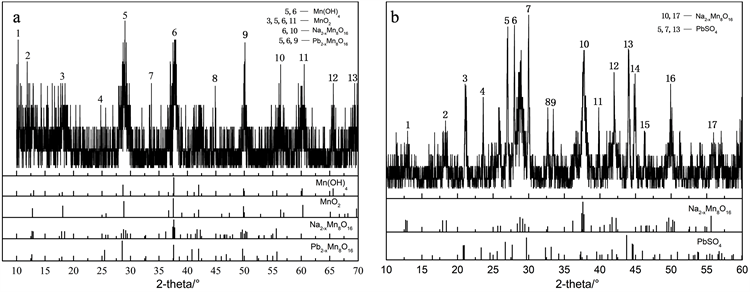
Figure 1. XRD patterns of Anode Slime (a) and sulfur reaction residue (b)
图1. 阳极泥(a)和硫磺反应滤渣(b)XRD图谱
浸取前后扫描电镜图如图2所示,可知反应后渣变小,且出现了明显的溶蚀痕迹,可推断在硫酸溶液的介质下,以硫磺为还原剂对Mn浸取效果较为明显。
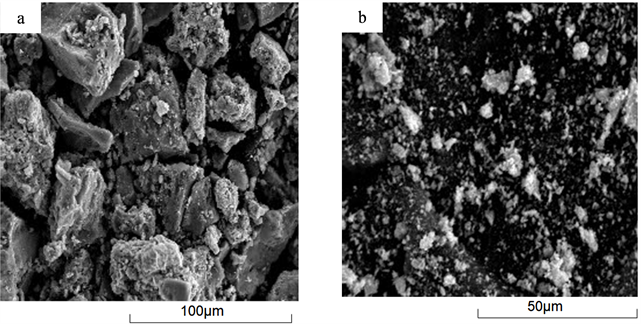
Figure 2. The SEM photographs of Anode Slime (a) and sulfur reaction residue (b)
图2. 阳极泥(a)和硫磺反应滤渣(b)扫描电镜图
3.2. 单因素实验结果与分析
单因素实验结果见图3,由图3(a)可知,在70℃~110℃范围内,Mn的浸取率随温度增加逐渐升高,到达120℃时降低,可能是粉末状的硫磺达到熔点(118℃)后呈熔融块状,与阳极泥接触面积变小,影响Mn的浸取率,故反应时间以110℃左右为宜。由图3(b)可知:Mn浸取率随硫酸浓度增加而升高,综合液固比和成产成本考虑,硫酸过多不利于后续回收。所以选择12 mol∙L−1左右为宜。由图3(c)可知:当酸矿比在1.5~2.5 (mL:g)时,Mn的浸取率随酸矿比增加而升高,原因可能是酸矿比低,溶液黏度大,浸取液易饱和,对传质过程不利。酸矿比增加到2.5 (mL:g)时,Mn的浸取率增加趋势趋于平缓。所以酸矿比选择2.5(mL:g)左右为宜。图3(d)可得:当时间在1~5 h内,Mn浸取率随时间增加而升高,浸取时间达到3.5 h时,浸取率增长趋势趋于平缓,应该是Mn基本上被浸出,再延长反应时间,Mn的浸取率保持不变,故反应时间选择3.5 h左右为宜。
注:(a) 温度,(b) 硫酸浓度,(c) 酸矿比,(d) 时间。
Figure 3. Effects of temperature, sulfuric acid concentration, acid ore ratio and time on leaching rate of manganese
图3. 环境条件对锰浸取率的影响
3.3. 响应实验结果分析
3.3.1. 响应曲面设计与结果
利用软件中Optimal模块响应面分析方法进行设计,实验设计及结果见表3。Mn的预测浸取率响应范围为23.09~99.96%,实际浸取率响应范围为22.17~99.57%,各组别预测浸取率与实际浸取率之间高度拟合。通过Design-Expert.V8.0.6.1软件进行多元回归拟合,得到的Mn浸取率(Y)与反应温度(A)、硫酸浓度(B)、酸矿比(C)和反应时间(D)之间的二次多项回归方程为:
通过回归方程可知,反应温度、硫酸浓度和酸矿比为模型显著项,而酸矿比对Mn浸取影响不显著。系数的正负可以反映因素对Mn的浸取率的正、负影响。因此可推断反应温度、硫酸浓度、酸矿比和反应时间对Mn浸取率都为正影响,即增加这4项因素用量,均可提高Mn的浸取率。
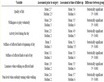
Table 3. Design list of response surface method and the test results
表3. 响应面法设计与实验结果
3.3.2. 建立模型方法与显著性分析
由表4可知,Mn的浸取率模型复相关系数为R2 = 96.97%,说明该模型与实验实际情况拟合较好。该模型F值为22.83,回归方程p < 0.0001,表明该模型高度显著,可以用来进行优化实验响应值的预测。另外,由表4中各实验影响因素的显著性检查可得:因素A (p < 0.05)、因素B (p < 0.05)以及因素D (p < 0.05)对Mn浸取率影响显著,因素C(p>0.1)影响不显著。根据均方越大,参数影响越大可知:四个因素对Mn的浸取率影响大小排序为:D (时间) > A (温度) > B (硫酸浓度) > C (酸矿比)。两因素交互影响从大到小排序为:AD > BC > AC > AB > CD > BD,即时间和温度的交互对Mn浸取影响最大。
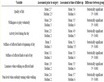
Table 4. Analysis of variance of manganese leaching rate model
表4. 锰浸取率模型方差分析
3.3.3. 曲面交互作用及结果分析
以Mn浸出率为响应值,将其与任意2个因素拟合为三维响应曲面图,如图4所示。
当反应时间为3.5 h,酸矿比为1.75(mL:g)时,考察反应温度和硫酸浓度及其交互作用对Mn浸取率的影响如图4(a)所示:反应温度对Mn浸取率的影响较硫酸浓度更显著。Mn浸取率随硫酸浓度的增高先升高后较为平缓,随着温度的增加,Mn浸取率先增加后减小,可能是温度升高,反应体系中粒子的热运动加强,有利于还原反应的进行,随着温度继续升高,硫磺达到熔点后呈熔融块状,与阳极泥接触面积变小,从而影响Mn的浸取率。硫酸浓度与温度交互影响,硫酸浓度为11 mol∙L−1,反应温度为105℃时,Mn的浸取率达最佳。
反应温度和酸矿比对阳极泥中Mn的浸取率交互影响如图4(b)所示。反应温度对Mn浸取率的影响较酸矿比更为显著。随着温度升高,Mn浸取率呈先上升后减小的趋势。随酸矿比增大,Mn浸取率呈先增加后趋于平衡并略有下降,可能是酸矿比较小时,浆液粘稠,浸取液易饱和,对传质过程不利,甚至部分阳极泥渣呈结块状,导致反应接触面积小,浸取率低。随着硫酸溶液增加,反应逐渐趋于平衡。
反应温度和反应时间对阳极泥中Mn的浸取率交互影响如图4(c)所示。温度较低时,Mn的浸取率随时间的延长逐渐上升后趋于平缓,说明反应基本完成。温度较高时,随着时间延长,Mn的浸取率变化不大,原因是温度影响硫磺物相状态,从而影响其与阳极泥的接触面积,不利于浸取反应。因此选择适当反应温度和反应时间可达到较高的Mn浸取率。
硫酸浓度与酸矿比对Mn的浸取率交互影响如图4(d)所示,可知:两者交互作用对Mn浸取率影响较大。硫酸浓度较低时,Mn浸取率随着液固比增加而缓缓上升。硫酸浓度较高时,Mn浸取率随着液固比增加而略有下降。
Mn浓度和反应时间对与阳极泥中Mn的浸取率交互影响如图4(e)所示。两者相互作用对Mn浸取率影响最不显著。Mn浸取率随时间延长先增加后趋于平缓,说明此时反应基本完成。Mn浸取率随浓度先增加后趋于平缓并略有下降趋势。
酸矿比与反应时间对阳极泥中Mn浸取率的交互影响如图4(f)所示。Mn浸取率随时间的延长先增加后趋于平缓,说明此时反应基本完成。Mn浸取率随液固比先增加后趋于平缓,两者交互影响,存在最佳浸取率。最佳值前,两者增加均有利于Mn浸取率增大。
利用Design-Expert软件进行数据的处理,筛选最佳反应条件为:反应温度105℃、反应时间3.5 h、酸矿比1.75 (mL:g)、硫酸浓度11 mol∙L−1,Mn的浸取率预测值为99.93%。在相同条件下进行多次实验验证,实测Mn浸取率平均值为98.57%,实测结果与预测值相差不大,说明曲面响应法优化阳极泥中Mn浸取条件合理可行。
注:(a) 温度与硫酸浓度,(b) 温度与酸矿比,(c) 温度与时间,(d) 硫酸浓度与酸矿比,(e) 硫酸浓度与时间,(f) 酸矿比与时间。
Figure 4. The three-dimension diagram of manganese reduction rate under the influence of different factors
图4. 不同条件下对阳极泥中锰浸取率交互影响的三维曲面图
4. 结论
a) 浸取Mn最佳反应条件为:反应温度105℃、反应时间3.5 h、酸矿比1.75 (mL:g)、硫酸浓度11 mol∙L−1,阳极泥中Mn的浸取率可达99.93%。
b) 各因素对Mn的浸取率影响从大到小的排序为:D (时间) > A (温度) > B (硫酸浓度) > C (酸矿比),两因素交互影响从大到小排序为:AD > BC > AC > AB > CD > BD。
c) 用硫磺做还原剂,硫酸为浸取剂,直接还原酸浸回收阳极泥中Mn,具有原料廉价易得,反应温度低,速率快,浸取率高的特点。
基金项目
吉首大学校级科研课题(JDCX2020328)。
NOTES
*通讯作者。