1. 引言
根据“碳中和”与“碳达峰”的发展目标,所有工业都面临着降低污染与排放的挑战,而对于我们汽车工业降低污染与排放就是我们主要的研发方向,对车辆的轻量化设计也是节能减排的路径之一。根据理论研究表明电动车质量减少10%,续航里程可增加6%~8%。本文采用20Cr作为钢管材料,在规则的条件下,在保证强度刚度的前提下,运用hypermeshoptistruct对钢管的壁厚进行一一优化。由于上赛季的后桥及传动定位有误差,造成车辆起步是发成了“打齿”现象,因此本赛季采用副车架的设计来保证定位的准确性。目前FSAE车架主要采用单体壳和钢管桁架式两种,但由于单体壳造价昂贵,因此更多车队采用造价更为便宜的钢管桁架式车架;但钢管桁架式车架有着质量较大,定位不准确的缺点,因此本文主要通过轻量化设计和副车架设计来改善这两点。
2. 建立车架有限元模型
2.1. 车架模型的建立
为建立精准的有限元模型是保准分析结果准确性的前提,本文使用hyperworks进行有限元分析,使用UG经行车架3D模型的建立,在钢管连接处进行剖口处理,如图1所示。
2.2. 材料及网格建立
将车架导入hypermesh,为了提高运算速度和提高计算精度,本文使用midsurfcae将钢管进行抽中面,经行2D的网格划分,网格大小为4 mm,对剖口处的进行网格检查,对破损网格进行优化;对副车架进行3D网格划分;使用rigids将钢管连接处进行刚性连接,如图2所示;并将材料的属性赋成20Cr,20Cr的材料属性如表1所示。
共生成178,046个节点,168,999个网格单元。
3. 载荷的分析与处理
车架在行驶过程中受到多种载荷的共同作用,主要有车架自身质量、车手质量、发动机总成质量、后桥质量。本文中车手的质量为70 KG,发动机总成的质量为60 KG,后桥总成的质量为20 KG,均均匀地分布在车架连接节点钢管上,自身重量使用hypermesh中的重力场添加。
4. 工况分析
4.1. 满载弯曲工况
在满载弯曲工况下,取动载因数为2。在发动机舱添加1200N向z轴负方向的力,后桥总成添加400N向z轴负方向的力,在驾驶舱添加1400N向z轴负方向的力。在轮胎中心添加约束条件:限制四个支撑点Z方向平动,右前方Y方向平动,左后方X方向平动,右后方Y方向平动。
结果分析可得,如图3所示最大应力发生在后悬与钢管的连接处,应力大小为125.5 Mpa,远小于20Cr的屈服强度,主要承受后悬的力;如图4所示位移最大处为前悬与车架连接的横杆处,位移量为1.716 mm;如图5所示副车架的最大位移为1.06 mm,发生在副车架与减震器的连接处,符合设计要求。
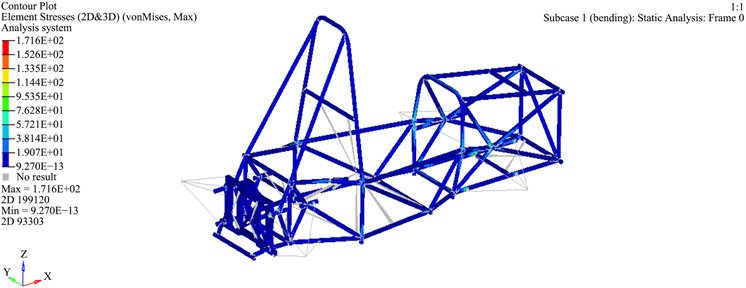
Figure 3. Cloud map of full load condition
图3. 满载工况等效应力云图
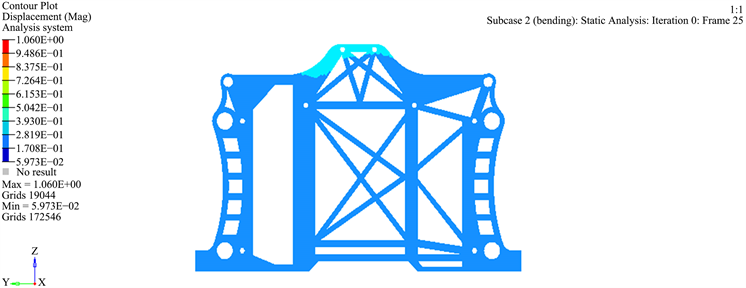
Figure 5. Cloud map of full load condition
图5. 满载工况等效应力云图
4.2. 紧急制动工况
当比赛过程中赛车在紧急制动的过程中会受到一个惯性力,计算公式如下:
上式中a为制动减速度,v为制动初速度25 m/s,s为制动距离为30 m,计算得制动减速度为1.04 g [1]。
紧急制动工况中,给模型添加一个向x轴负方向的大小为1 g的制动减速度,约束条件下考虑前轮完全抱死:对前轮XYZ平动约束,后轮XZ方向平动约束 [2]。
结果分析可得,如图6所示最大应力发生在前悬与钢管的连接处,应力大小为106.2 Mpa,远小于20Cr的屈服强度,主要承受后悬的力;如图7所示位移最大处为座椅连接点处,位移量为0.425 mm;如图8所示副车架的最大位移为0.39 mm,主要受力部位为与减速器支撑架连接处,位移量与应力量都符合设计要求。
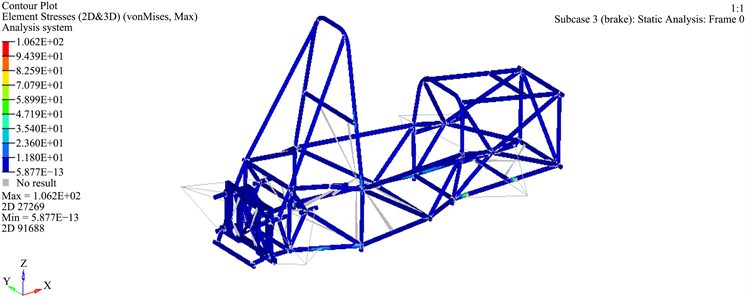
Figure 6. Cloud diagram of the other effect force of braking condition
图6. 制动工况等效应力云图
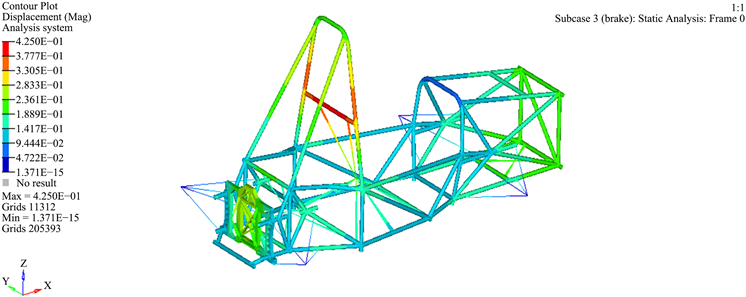
Figure 7. Equivalent cloud shift diagram of brake working condition
图7. 制动工况等效位移云图
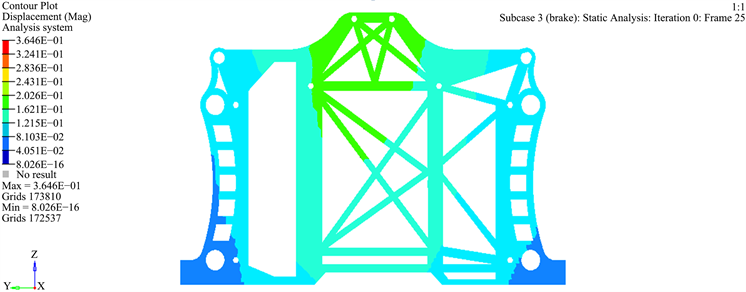
Figure 8. Cloud diagram of the other effect force of braking condition
图8. 制动工况等效应力云图
4.3. 高速过弯工况
大学生方程式汽车大赛通过八字绕环来检验车辆的过弯工况,过弯时除了会受到垂直方向的载荷,还会因为紧急转弯而受到向心加速度,向心加速度a的计算公式如下:
其中上式r为八字赛道半径取15.25 m,t为八字绕环单圈时间取6 s,带入上式算得a = 1.02 g。
因此高速转弯工况下,考虑汽车向左转弯,在模型上添加一个向右的,大小为1.02 g的加速度,约束条件保证车辆向左过弯:约束左前轮XYZ方向所有自由度,右前轮XZ方向所有自由度,后轮Z方向平动。
由分析结果可得,如图9所示受应力最大部位在前悬上支撑吊耳和前环与上侧防撞杆的连接处,最大应力为59.42 Mpa,远小于20Cr的屈服强度;如图10所示车架主要变形部位在主环与主环斜撑的连接处,最大变形量为0.572 mm。符合设计要求。
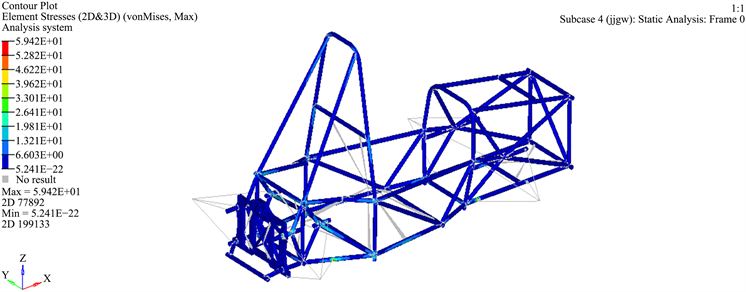
Figure 9. Cloud diagram of the effect force under overbending condition
图9. 过弯工况等效应力云图
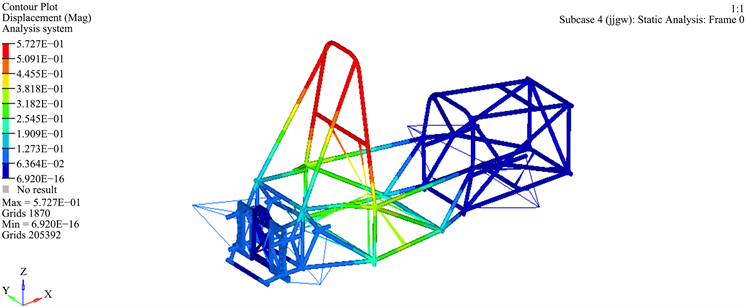
Figure 10. Overbend equivalent displacement amount
图10. 过弯等效位移量
4.4. 扭转刚度分析计算
扭转刚度是衡量车架力学性能的指标,通过模拟车辆在通过不平整路面的时,左右两前轮受到不同方向的力来计算车架的扭转刚度。轮载荷条件:在前轮两轮心各添加一个大小相同的Z向作用力,大小为1000N。约束条件:约束后悬的XYZ的平动自由度,以及前隔板下横杆中间Z轴的自由度 [3]。刚度的计算公式如下:
如图11所示分析结果得两个轮心等效点的位移量为8.637 mm,前轮轮距为1220 mm,计算得车架扭转刚度为1503.06 N∙M/(˚)。根据国内外车架设计经验,扭转刚度一般在1000 N∙M/(˚)~2000 N∙M/(˚),因此符合设计要求。
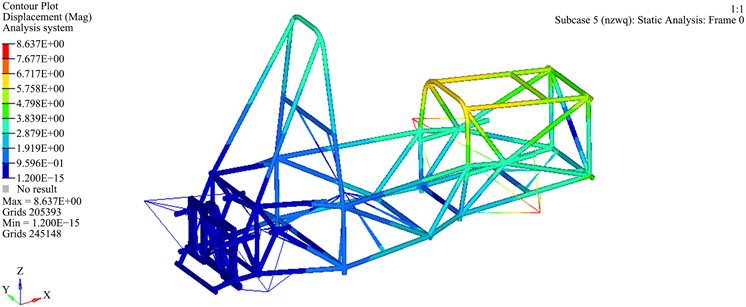
Figure 11. Torsional stiffness displacement diagram
图11. 扭转刚度位移图
5. 自由模态分析
车架在汽车行驶过程中受到外部激励主要有两种:一种不平整的路面产生的随机振动,频率一般在20 Hz左右,另一种是发动机工作时,燃烧产生的压力和活塞往复运动产生的惯性力引起的简谐振动,如果当这些激励的频率和车架的某一固有频率相吻合时,车架就会产生共振,甚至可能造成车架被破坏的危险 [4]。本赛季依然使用四冲程的春风650NK发动机,发动机怠速时的转速为2000 r/min;一般驾驶情况下发动机转速在5000 r/min~8000 r/min区间,发动机频率的计算公式如下:
式中:z为发动机缸数;n为发动机转速(r/min);τ为发动机的冲程数。计算得发动机怠速时发动机得频率为33.3 Hz,一般工况下发动机得频率为83.3 Hz~133.3 Hz。前十阶车架的固有频率为如下表2所示。可得出前六阶频率避开了地面激励,后四阶频率避开了发动机激励。
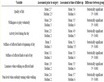
Table 2. Top 10-order free-mode frequency
表2. 前10阶自由模态频率
6. 车架轻量化设计
根据各种工况的分析结果可以得出,车架钢管的管径仍然有进一步优化的空间,并且车架的刚度也仍然需要进一步的优化。因此文本中采用Hypermesh Optimization size进行钢管的尺寸优化。
6.1. 建立优化数学模型
Minimize:
Subjectt:
式中:
为设计变量,本文中为钢管的壁厚,
为目标函数,本文中为钢管体积的最小值;
为约束条件,本文中为满载弯曲工况、紧急制动工况、第10阶模态频率 [5] [6]。
为了能加快计算速度,本文中将对称的钢管列为同一个优化组,最终将钢管按分成23组,如图12所示,每一组的壁厚为2 mm,钢管壁厚的设计范围为1.5 mm~2.5 mm。
6.2. 建立设计目标、约束条件
约束条件:在满载弯曲、紧急制动、高速过弯三种工况下最大应力不超过350 Mpa,第十阶模态频率低于83.3 Hz,工况的比重系数为1。
设计目标;车架钢管的体积最小值。
6.3. 数据优化
根据优化数学模型,运用optistruct在不影响车架性能的前提下对钢管壁厚进行优化。目标函数为车架体积最小,约束条件为各种工况下最大应力值小于350 Mpa,第十阶模态频率低于83.3 Hz。优化时钢管的壁厚变化式连续的,还有多位小数而在实际情况下并不能采购到相应的管件,因此需要对优化数值进行处理。分析结果如下图13所示,车架受力较大的为前悬架上横杆、前换以及侧面防撞杆,其余的杆件的优化值均为1.5 mm,如表3所示,均为我们所设置的最低值,因此可以在规则允许的前提下,将这些管件使用壁厚更加薄的管件替换。
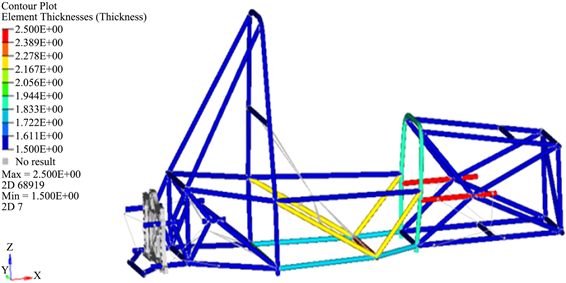
Figure 13. Numerical drawing of steel pipe wall thickness after optimization
图13. 优化后钢管壁厚数值图
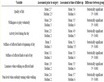
Table 3. Optimize the rear wall thickness parameters
表3. 优化后壁厚参数
5、前悬固定杆2.423 mm;10、主环下横杆1.956 mm;11、驾驶舱横杆2.500 mm;13、侧边防撞杆2.202 mm;14、发动机舱后杆1.739 mm;19、后悬固定杆1.56 mm。
7. 优化数据校核与统计
7.1. 模型修改
如图14,图15所示中由原来的蓝色1.65 mm壁厚的改为黑色1.5 mm壁厚 [7],修改之后车架的质量由原来的31.97 KG降低到了30.56 KG,减少了4.4%的质量。
7.2. 工况分析统计
经过钢管壁厚的修改,在软件继续分析生成相应工况下得到应力以及位移数据如下:
管件修改前后的分析结果对比图如表4所示,虽然最大位移量、最大应力大小值都有所增加但都是设计范围之内,如表5所示,车架第7阶到第10阶的固有模态频率也避开了与发动机的共振,车架刚度由原来的1503.08 N∙M/(˚)降低到了1339.98 N∙M/(˚),但仍然符合设计要求。
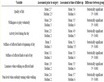
Table 4. Analysis and comparison diagram
表4. 分析对比图
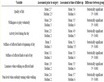
Table 5. Modified order 7 to 10th modes
表5. 修改后第7阶到第10阶模态
8. 结论
本文工况hypermeshoptistruct对车架的尺寸进行了优化处理,并且在最终降低了4.4%的质量,并且车架的安全性仍然能够得到保障。但是车架的安全性能仍然要进行车架的碰撞分析,为接下来设计新一代车架提供了设计方向。