1. 引言
在各个行业中,螺纹零件都是扮演着紧固与连接的重要角色,而在机械加工领域中,孔加工占总工作量的30%左右,其中,内螺纹加工占孔加工总量的14%。随着21世纪机械行业不断向前发展,机械行业对螺纹加工工艺要求也同样随之增高,传统的小螺距螺纹,可以通过攻丝来进行加工,而针对大直径的内、外螺纹则可以采用螺纹铣削加工 [1]。螺纹铣刀相对于攻丝来说,不仅强度高而且不易损坏,还在加工过程中还可以通过插补程序来保证螺距。如果通过攻丝加工螺纹,会存在丝锥因切削力过大而折断、堵塞螺纹孔等问题,从而导致零件的报废 [2]。随着新型被加工材料及其自身物理性能的不断提高,丝锥攻丝等传统加工方式已经不再适合螺纹的加工,内螺纹的加工方式从主流的攻丝逐渐过渡到铣削加工,所以研究针对内螺纹的加工工艺,特别是对难加工材料的研究就显得尤为重要。
朱冰等 [3] 根据正交试验方法研究了切削线速度、每齿进给量和背吃刀量对于加工发动机主轴承螺栓孔的影响,表明了每齿进给量、背吃刀量、切削线速度的影响依次递减。张宏基等 [4] 通过建立铣削参数和表面粗糙度的数学预测模型,得到了AZ91D镁合金的铣削参数和表面质量的关系。刘贞等 [5] 开展了对内螺纹铣削与攻丝工艺的研究,通过大量的切削试验与数据分析,实现了钛合金材料精密小尺寸螺纹的高效率与高加工精度切削加工,从而使小尺寸钛合金内螺纹产品的表面质量和加工效率得到显著提高。林法振等 [6] 根据螺纹铣削原理,通过系统地分析了螺纹铣刀的选用、铣削参数的选择、加工工艺的选择以及数控程序的编写对于内螺纹铣削工艺的影响,总结出一套合理针对数控铣削大直径内螺纹的方案。Zdenka Rysava [7] 等人开发了一种特定的测量程序来量化孔加工时最具代表性的几何特征:直径、垂直度和毛刺。通过选择合适的孔加工切削参数,确保后续螺纹加工时的精度与被加工工件表面质量。Guillaume Fromentin [8] 等人提出了一种迭代方法来分析由螺纹铣刀轨迹包络线所产生的螺纹轮廓。结果表明:螺纹铣削产生干涉,即加工中螺纹受到过切的影响,通过改变螺旋插补半径与切削参数来减少过切,以便生产高精度螺纹。S. W. Lee [9] 等人通过调整每齿进给量等切削参数,对在单位时间的切削的切屑进行了分析,对提高生产率进行了研究,达到了提高生产率的效果。Anna Carla Araujo [10] 等对螺纹铣削参数进行了全面分析,试验结果表明:随着每齿进给量减小,切屑厚度减小、切削刃上的切削力降低。
在金属加工的过程中,对于加工精度的影响首先是加工设备的影响,其次刀具的合理选择对于提高加工精度也有很大的作用。但由于每种材料具有各自不同的加工特性,不同的材料不同因素的影响都是不一样的,所以本文得出的结论对于其他金属加工具有一定的参考价值。
本文通过对材料进行正交试验,采用三因素(切削速度v、每齿进给量fz、铣刀悬伸量s)三水平正交试验。通过对试验数据进行极差分析,可以得出在相同的实验范围,不同的实验指标下随着试验因素的变动而产生的实验数据的变动;各个因素对于实验的影响程度;从而得出最适合的因素搭配方案。
2. 试验设备
2.1. 工件材料
工件选择材料为45钢的无缝钢管,其具体几何参数:孔外壁直径φ1 = 125 mm、孔内壁直径φ2 = 96.75 mm、轴向高度H = 150 mm。被加工材料相关参数如表1所示。
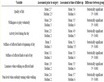
Table 1. Mechanical properties and chemical composition of 45 steel (wt. %)
表1. 45钢力学性能和化学成分组成(wt.%)
2.2. 加工设备以及加工刀具
试验选用的设备为德国德玛吉公司生产的DMU50五轴联动加工中心。螺纹的铣削加工通常采用整体式螺纹铣刀或刀片式螺纹铣刀,整体式螺纹铣刀受限于其自身尺寸与螺纹尺寸,往往应用于中、小孔径的螺纹加工。而刀片式螺纹铣刀的铣刀盘直径则可以更大程度的根据要加工内孔尺寸进行适当选择,刀片也可以根据加工不同螺距的螺纹进行灵活选择,而且在可转位刀片发生较严重磨损时也可以快速转换,极大节省时间和经济成本。
2.3. 加工精度测量设备
螺纹加工精度测量设备选用德国Optacom公司生产的VC10螺纹综合扫描仪。该仪器可以全自动测量螺纹的几何尺寸,包括大径D、中径D2、小径D1、螺距P、牙型左半角βl、牙型右半角βr。该仪器可以满足试验所需测量精度要求。
3. 试验方案和结果分析
3.1. 试验方案
正交试验设计是通过正交表来合理安排与分析多因素、多水平试验的设计方法。由于正交试验的原理是从全面试验中选择出最具有代表性的组别进行试验,因此,在试验因素、水平数较多的情况下,正交试验法的优势在于极大程度的减少试验次数、减低研究人员的时间成本。
本文的正交试验采用三因素(切削速度v、每齿进给量fz、铣刀悬伸量s)三水平正交试验。切削速度v的选取区间为70~90 m/min、每齿进给量fz的选取区间为0.04~0.08 mm/z、铣刀悬伸量s的选取区间为35~100 mm。根据选定的试验因素及水平数,选择L9(34)正交实验表,如表2所示。试验过程中保证切削深度ap = 1.625 mm不变。
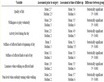
Table 2. Orthogonal test table of 45 steel for internal thread milling
表2. 内螺纹铣削45钢正交试验表
3.2. 试验结果与分析
根据正交试验表2,建立L9(34)三因素三水平正交试验表,并且按照正交表进行内螺纹铣削试验。试验结束后对被加工材料的几何尺寸进行测量,将测量数据(中径偏差、螺距偏差、螺纹牙型左半角偏差、螺纹牙型右半角偏差)进行整理结果如表3、表4所示。
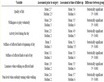
Table 3. Orthogonal test results of machining accuracy of 45 steel for internal thread milling
表3. 内螺纹铣削45钢加工精度正交试验结果
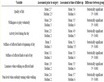
Table 4. Range analysis of internal thread milling 45 steel test results table
表4. 内螺纹铣削45钢试验结果极差分析表
1) 切削速度对尺寸精度偏差的影响
如图1所示,图1(a)、图1(b)分别为中径偏差、螺距偏差和螺纹牙型左、右半角偏差随切削速度的变化规律折线图。
可以看出中径偏差和螺距偏差随切削速度进一步增大而降低,但变化趋势较弱。牙型左半角偏差随切削速度进一步增大而降低,且变化趋势明显,而牙型右半角偏差随切削速度进一步增大而降低,且变化趋势一般。这是由于当切削速度从v = 70 m/min增大至v = 90 m/min时,一方面残留面积高度减小,理论粗糙度降低;另一方面,随着切削速度增大,切削力减小,刀具切削刃处磨损减弱,且被加工材料表面受力减小,表层金属塑性变形范围缩小,尺寸精度误差降低。
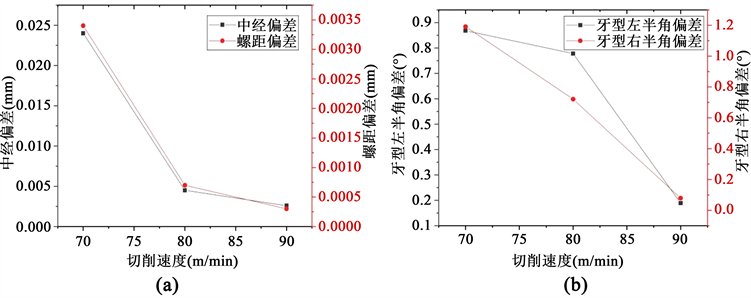
Figure 1. Influence of cutting speed on dimensional deviation
图1. 切削速度对尺寸偏差影响
2) 每齿进给量对尺寸精度偏差的影响
如图2所示,图2(a)、图2(b)分别为中径偏差、螺距偏差和螺纹牙型左、右半角偏差随每齿进给量的变化规律折线图。可以看出中径偏差和螺距偏差随每齿进给量进一步增大而增大,且变化趋势明显。牙型左半角偏差随每齿进给量进一步增大而增大,且变化趋势明显,而牙型右半角偏差随每齿进给量进一步增大而增大,且变化趋势较弱。
这是由于当每齿进给量从fz = 0.04 mm/z增大至fz = 0.08 mm/z时,一方面残留面积增大,理论粗糙度增大;另一方面,随着每齿进给量增大,切削力增大,刀具切削刃的磨损加剧,伴随着工件表面受力的逐渐增大和切削温度的升高,从而引起被加工材料表层的热应力增大,塑性变形加剧,引起被加工材料表层体积产生变化,从而引起尺寸精度下降。
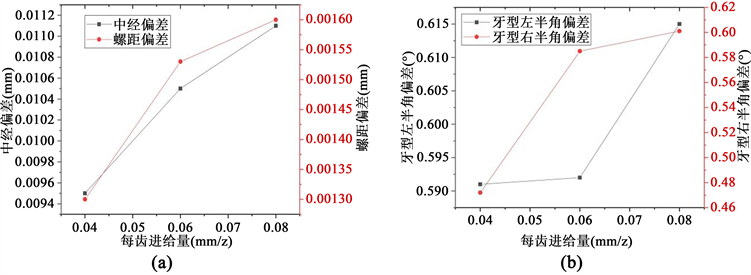
Figure 2. Influence of feed per tooth on dimensional deviation
图2.每齿进给量对尺寸偏差影响
3) 铣刀悬伸量对尺寸精度偏差的影响
如图3所示,图3(a)、图3(b)分别为中径偏差、螺距偏差和螺纹牙型左、右半角偏差随铣刀悬伸量的变化规律折线图。
可以看出中径偏差和螺距偏差随铣刀悬伸量进一步增大而增大,且变化趋势明显。牙型左半角偏差随铣刀悬伸量进一步增大而增大,且变化趋势一般,而牙型右半角偏差随铣刀悬伸量进一步增大而增大,且变化趋势较弱。这是由于当铣刀悬伸量增大从s = 35 mm增大至s = 100 mm时,铣刀整体刚度降低,一方面引起铣刀径向振动幅值增加,增强了切削过程中所产生的过切与残留现象,另一方面引起切削力大幅增大,引起刀具磨损加剧,被加工材料表面塑性变形加剧,从而导致尺寸精度大幅降低。
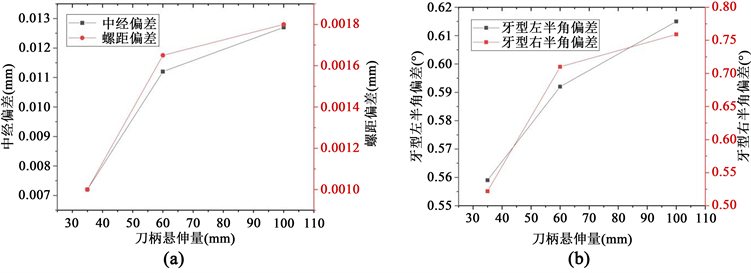
Figure 3. Influence of milling cutter suspension on dimensional deviation
图3. 铣刀悬伸量对尺寸偏差影响
4. 结论
铣削加工后内螺纹的中径偏差、螺距偏差、牙型左半角偏差和牙型右半角偏差随着切削速度增大而降低,随着每齿进给量和铣刀悬伸量的增大而增大。
影响铣削加工内螺纹尺寸精度的顺序依次为:切削速度、铣刀悬伸量和每齿进给量。因此,欲降低铣削内螺纹尺寸精度偏差,应适当增大切削速度,其次考虑减小每齿进给量和铣刀悬伸量。
NOTES
*第一作者。
#通讯作者。