1. 引言
随着科学技术的不断发展,传统钻眼爆破隧道掘进方式逐渐被机械掘进方式所取代。全断面岩石掘进机(简写为TBM)便是的这类设备中的典型代表,已经被广泛应用于公路隧道工程、水利隧道工程和地铁隧道工程等岩石工程领域。在TBM的刀盘上,按照某种规律布置有多个破岩滚刀。TBM的掘进速度受滚刀的几何形状、TBM的推力和岩石的物理力学性质以及岩体的裂隙分布特性的影响。掘进机刀盘上的盘形滚刀在岩石表面上将岩石切碎来达到破岩的目的,将岩石以岩石碎片的形式分离出来。盘形滚刀随着刀盘旋转,同时又绕着自身轴线进行旋转,在掘进机推力的作用下,使刀盘上的盘形滚刀紧紧贴在岩岩石表面,盘形滚刀在推力和扭转等复杂的作用下,达到岩石的破坏强度后,岩石开始破碎,形成岩石破碎区,破碎区将压力继续传递给周围的岩石,形成一些微裂纹,出现裂纹区域,当裂纹逐渐扩展,与另一条裂纹贯通时,岩石就会形成岩石碎片而脱落。为了研究滚刀的破岩机理和过程,国内外进行了广泛深入的一系列研究。Entachera基于线性切割破岩实验,提出了滚刀破岩性能的预测模型 [1]。Gertsch在花岗岩上进行了滚刀破岩实验,提出了TBM掘进性能预测模型 [2]。Rostami研究了滚刀与岩石之间的相互作用以及压力分布特性 [3]。Tumac研究了滚刀破岩特性,并且将理论值、经验值与实验值进行了对比分析 [4]。姜兴宇以库仑莫尔理论为基础,提出了盘形滚刀破岩力预测模型 [5]。刘泉声推导了常截面盘形滚刀的法向推力与滚动力计算公式,并利用多种不同强度岩石的线性切割试验结果进行验证 [6];李刚分析了全断面岩石掘进机滚刀的破岩机理,并基于实际的施工过程,对滚刀进行了受力分析 [7];宋克志讨论了影响盘形滚刀与岩石相互作用的主要机械因素和地质因素 [8];孙斌通过对原有CSM受力模型分析的基础上,基于盘形滚刀切割岩石实际情况提出了改进的CSM模型 [9]。Geng实验研究了盘形滚刀的破岩过程,并且将理论值与经验值和实验值进行了对比分析 [10]。刘立鹏等应用颗粒流程序理论方法对单刀破岩过程进行有限元建模,发现了岩石破坏分为几个阶段形式的破坏,前中期为挤压剪切破坏,后期为挤压张拉破坏 [11]。梁正召等应用RFPA软件对单个盘形滚刀作用下的破岩机理进行了数值模拟,结果表明岩石破坏的过程大致可以分为出现岩石粉末、粉核体、裂纹、岩石碎块这四个阶段,破坏的形式主要为张拉破坏,同时也存在挤压和剪切破坏,岩石的碎裂主要是由拉力导致 [12]。肖南等应用三维有限元法(FEM)结合光滑粒子流体动力学方法(SPH)模拟了单个盘形滚刀的破岩过程,发现岩石破坏主要有压碎区、微裂纹的形成以及主裂纹扩展三个阶段 [13]。从以上文献中的研究结果可以看出,不同的研究者所得到的预测力模型差异较大。本文的目的在于总结现有的预测模型,结合工程具体实例,分析讨论各种滚刀力预测模型的差异。
2. 几种典型的TBM滚刀破岩贯入力预测模型
盘形滚刀在侵入岩石的过程中,主要受到三个方向的作用力:法向力、滚动力和侧向力,受力模型如图1所示。基于滚刀破岩机理模型、实验研究和经验公式,前人提出了许多不同的滚刀受力预测模型,目前被普遍认可的受力模型大致可以分为三种类型:基于理论分析的受力模型、基于实验结果的受力模型和基于理论分析和实验数据的半理论半实验受力模型。比较常用的基于理论的受力模型有伊万斯预测公式、秋三藤三郎预测公式、罗克斯巴勒预测公式以及科罗拉多矿业学院预测公式等;而基于实验数据拟合的受力模型有Rostami预测公式等;理论分析和相结合的半理论半实验受力模型,包括上海交通大学预测公式、CSM模型等。
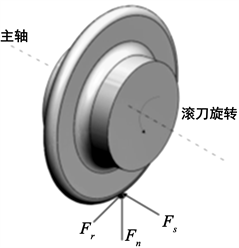
Figure 1. Mechanical analysis for disc cutter during cutting rock
图1. 滚刀破岩时的受力分析模型
滚刀在破岩过程中,作用在滚刀上的岩石反力包括法向力、滚动力和侧向力。荷载的大小与岩石的力学性能、滚刀的几何尺寸和贯入度有关。在众多的预测作用在滚刀上荷载的解析模型中,科罗拉多矿业学院预测模型(简写为CSM模型)是一种半理论半经验的解析模型,CSM预测模型的盘形滚刀破岩法向力与岩石强度、贯入深度和滚刀形状参数之间的关系为 [5]
(1)
式中FN为作用在滚刀上的法向力,R为滚刀半径,S为滚刀间距,T为滚刀刃宽,sc为岩石的抗压强度,st为岩石的抗拉强度,l为常数,它随着滚刀刃宽的增加而减少,l = −0.2 − 0.2;a为滚刀与岩石之间的接触角,x为常数,近似取x = 2.12。
(2)
式中P为滚刀侵入岩石的深度,简称贯入度或者切深。盘形滚刀破岩滚动力与法向力之间的关系为
(3)
式中FR为作用在滚刀上的滚动力。CSM预测模型是目前比较公认的半理论半经验的解预测模型,该模型分别考虑了岩石的抗压强度和抗拉强度、滚刀间距、贯入深度和滚刀刃宽等参数。科罗拉多矿业学院的Ozdemir和Miller针对V形截面滚刀,假设盘形滚刀与岩石的接触面为三角形,建立了滚刀作用力的解析计算模型 [14],其表达式为:
(4)
式中D为滚刀的直径,st为岩石的抗剪强度,q为滚刀的刀刃角。该模型分别考虑了岩石的抗压强度和抗剪强度、滚刀的刀刃角、贯入深度等因素的影响,是一种基于原型实验数据经过统计分析得到的模型。
(5)
Evans假设盘形滚刀法向力与滚刀压入岩石区域在岩石表面的投影面积成正比,提出的滚刀法向力计算模型为 [15]
(6)
式中sc为岩石的抗压强度,该预测模型预测的法向力与岩石的抗压强度和贯入深度近似成正比。Roxborough提出的滚刀荷载计算模型为 [16]
(7)
(8)
Roxborough预测模型的法向力与岩石的抗压强度近似成正比,与Evans预测模型的表达式相近,Evans预测模型预测的法向应力仅仅是Roxborough预测的法向三分之一左右。当滚刀的几何参数和岩石的基本力学参数已知时,基于以上预测模型就可以计算在给定贯入度下滚刀的法向力和滚动力,为TBM掘进机掘进性能预测提供参考。
3. 数值算例
为了对比研究滚刀破岩法向力、滚动力与滚刀贯入度的关系,以普遍采用的19英寸滚刀为例,盘形滚刀半径R = 254 mm;滚刀刀尖宽度T = 8 mm;滚刀刀刃角q = 30˚。岩石为变质花岗岩,其主要基本力学特性参数如表1所示。图2给出了不同模型预测滚刀法向力随贯入度的变化。
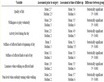
Table 1. Basic mechanical properties of some metamorphic granite
表1. 某变质花岗岩的基本力学特性
表2为不同模型预测滚刀法向力随贯入度的变化,表3给出了不同模型预测的滚刀滚动力随贯入度的变化。从表2中可以看出,四种预测模型在相同贯入度时预测的法向力差异较大,CSM模型预测的法向力最大,Evans模型预测的法向力最小。
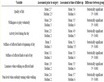
Table 2. Variation of normal force versus penetration depth for different prediction models
表2. 不同模型预测滚刀法向力随贯入度的变化
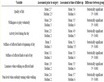
Table 3. Variation of rotating force versus penetration depth for different prediction models
表3. 不同模型预测的滚刀滚动力随贯入度的变化
从表3中看出,SM模型预测的滚动力最大,Ozdemir模型预测的滚动力最小。从图2和图3中可以发现,滚刀法向力和滚动力近似与贯入深度成正比。滚动力比法向力小了近似一个数量级。从图4中可以看出,滚刀法向力与滚动力近似成线性关系。CSM模型预测的滚刀法向力与滚动力关系可以近似表示为:
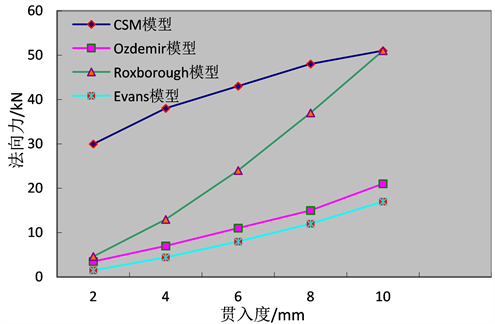
Figure 2. Variation of normal force versus penetration depth for different prediction models
图2. 不同模型预测滚刀法向力随贯入度的变化
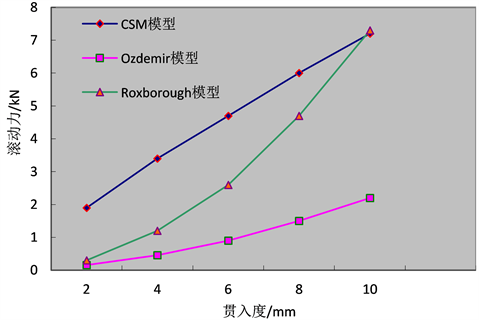
Figure 3. Variation of rotating force versus penetration depth for different prediction models
图3. 不同模型预测的滚刀滚动力随贯入度的变化
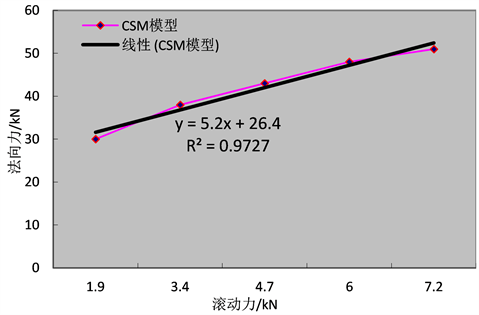
Figure 4. Variation of normal force versus rotating force for CSM prediction models
图4. CSM模型预测的滚刀法向力与滚动力关系
从表3中看出,SM模型预测的滚动力最大,Ozdemir模型预测的滚动力最小。从图2和图3中可以发现,滚刀法向力和滚动力近似与贯入深度成正比。滚动力比法向力小了近似一个数量级。从图4中可以看出,滚刀法向力与滚动力近似成线性关系。CSM模型预测的滚刀法向力与滚动力关系可以近似表示为:
(9)
4. 结论
在给定岩石力学参数和滚刀几何参数条件下,滚刀法向力随贯入度的增加近似线性增加,在4个法向力预测模型中,CSM模型预测的法向力值最大,Evans模型预测法向力最小,最大值与最小值之间比例达到三倍以上。在给定岩石力学参数和滚刀几何参数条件下,CSM模型预测的滚刀滚动力近似为法向力的1/7~1/10;滚刀法向力与滚动力近似为线性关系。
基金项目
国家重点基础研究发展计划“973”项目(2015CB057804);国家自然科学基金资助项目(11572079)。
参考文献