1. 引言
作为磁控溅射的阴极材料,ITO靶材的密度和微观结构是衡量靶材的重要指标 [1] [2] ,高密度可以增强靶材的抗刻蚀能力和溅射的稳定进行,有助于提高靶材利用率和溅射薄膜的性能,而均匀的显微组织和相结构可以改善溅射薄膜各区域的均一性 [3] [4] 。为了获得高致密、显微组织均匀的ITO靶材,研究者尝试采用热压烧结、热等静压烧结、微波烧结等致密化技术,已经制备出相对密度超过99.5%的烧结体,但这些技术无一例外的受设备尺寸、生产成本、产品性能等因素制约难以满足TFT-LCD用高性能溅射靶材的技术要求 [5] [6] 。氧气氛烧结法与上述技术相比具有工艺简单、烧结气氛可控、成本较低、可制备大尺寸靶材等优势,因此而受到研究者的广泛关注 [7] 。
采用氧气氛无压烧结法制备ITO靶材,其致密化程度主要受原料性能、成型工艺及烧结条件等因素的影响。纳米粉体由于具有大的比表面积,可以显著降低烧结温度、提高烧结活性;成型坯体密度的提高可以减少烧结过程中的收缩变形;氧气氛无压烧结可以有效抑制高温下In2O3和SnO2的分解,有利于获得高致密度ITO烧结体。王玥等 [8] 以粒径30 nm左右的ITO粉为原料,在400 MPa下模压成型,在氧气氛下1550℃烧结5 h得到相对密度在99%以上的烧结体。
研究表明:以ITO粉或In2O3和SnO2混合粉为原料,采用烧结法制备ITO靶材,当SnO2含量超过6.48 wt%后高温下会有In4Sn3O12第二相出现 [9] ,但目前关于含10 wt% SnO2的ITO靶材微观组织的研究主要集中在晶粒尺寸及断口形貌的分析,而对烧结过程中第二相的特征及分布规律少有报道。因此,深入研究烧结法ITO靶材的微观组织及各物相的分布规律具有重要意义。
本研究采用氧气氛烧结技术制备ITO靶材,对ITO靶材的烧结行为进行了研究,分析了不同烧结条件下ITO靶材的微观组织,探讨了ITO纳米粉体的烧结致密化机制。
2. 实验
粉末处理:ln2O3 (4N5)粉末、SnO2 (4N)粉末,按照ln2O3:SnO2为90:10 (wt%)两种组成比例进行称量配料,加入定量去离子水(电阻率 > 10 MΩ∙cm)和分散剂,配成水性料浆,以氧化锆球为研磨球,在高能球磨机中进行化学分散和机械研磨2~4 hr,控制混合粉体的比表面积8~10 m2/g,随后进行喷雾造粒预处理。氧化铟和氧化锡单体粉以及预处理后的ITO粉体形貌见图1。
ITO分散料浆雾化造粒,得到具有良好流动性的ITO粉末,装入钢制模具,以60~80 MPa模压成型,再经280 MPa冷等静压进行二次压制,得到Ф105 × 10.5 mm、相对密度60%~65% ITO素坯(理论密度:7.155 g/cm3)。坯体经脱水脱脂,在不同温度和气氛条件下,研究烧结工艺对靶材烧结行为的影响。
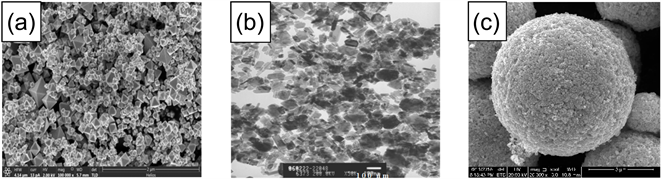
Figure 1. Morphology of monomer powder and ITO powder (a) In2O3 powder; (b) SnO2 powder; (c) ITO powder
图1. 单体粉和ITO粉体形貌(a) In2O3粉末;(b) SnO2粉末;(c) ITO粉末
ITO粉末的形貌、腐蚀之后的靶材晶粒和断口形貌通过美国FEI公司生产的Quanta250FEG型扫描电子显微镜(SEM)来观察。ITO粉末及ITO靶材的相结构使用Lab XRD-6100型X射线衍射仪(XRD)来表征。靶材的实际密度通过阿基米德原理测量,相对密度通过实际密度和理论密度(7.155 g/cm3)之比确定。在对靶材样品研磨和抛光后,分别在1200℃空气中热蚀1 h及在HCL和HNO3混合酸溶液中腐蚀8 min。对于每个靶材样品,通过统计法得到平均晶粒尺寸。通过能谱仪(EDS)测量靶材中各点的元素含量。通过EPMA-1720 Series型电子探针测试靶材的元素分布情况。
3. 结果与讨论
3.1. ITO靶材坯体的烧结致密化过程
图2为ITO生坯在其它烧结条件相同时,不同烧结温度下烧结所得ITO靶材的相对密度。从图中可以看出ITO生坯有两个明显的致密化阶段,第一阶段是1200℃~1300℃的快速致密化过程,此阶段靶材的相对密度从69.28%增加到83.19%,第二阶段是1300℃~1600℃的缓慢致密化过程,此阶段靶材的相对密度从83.19%增加到99.05%左右,增长幅度较第一个阶段大幅下降。
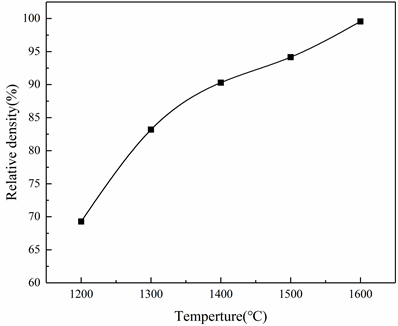
Figure 2. Relative density of ITO targets at different sintering temperatures
图2. 不同烧结温度下ITO靶材的相对密度
图3是不同烧结温度下所得ITO靶材经过磨抛且热腐蚀后的表面微观形貌,从图3(a)可以看出烧结温度在1200℃时,靶材内已经明显出现由晶粒孔洞形成的网络状结构,并且部分孔洞已出现闭合现象,此时晶粒尺寸只有0.6~0.8 μm。随着烧结温度的升高,靶材中的孔洞开始闭合并且逐渐消失,如图3(d)所示烧结温度为1500℃时靶材内部只有部分孤立的孔洞存在,此时靶材内晶粒按尺寸大小可分为两类,大晶粒平均尺寸约为5 μm左右,小晶粒平均尺寸1.5 μm左右,小晶粒一般位于多个大晶粒的交界处。如图3(e)所示当烧结温度升高到1600℃时,在靶材表面已经基本没有孔洞出现,且可以明显看出晶粒尺寸进一步长大,晶粒表面完整无裂痕,晶粒间角度约120˚,这表明晶粒完全长大。ITO粉末在烧结过程中在1200℃以下时粉末颗粒之间已经开始接触形成烧结颈,此阶段由于主要是粉末颗粒开始接触形成烧结颈,对密度的提高不明显,随着烧结温度上升,颗粒之间形成连通的网格结构且烧结颈扩大,烧结过程处于中期阶段,该阶段起主要作用的传质机制是最易发生的表面扩散,致密化程度大幅增加。当烧结温度高于1400℃时烧结过程进入后期阶段,该阶段的主要传质机制是晶界扩散和体积扩散,其主要通过消除孤立孔隙来促进致密化,此时,烧结体缓慢收缩致密化速度变缓,晶粒生长速率相对增加,靶材中的孔洞数量减少且主要分布于三晶或多晶交界处。
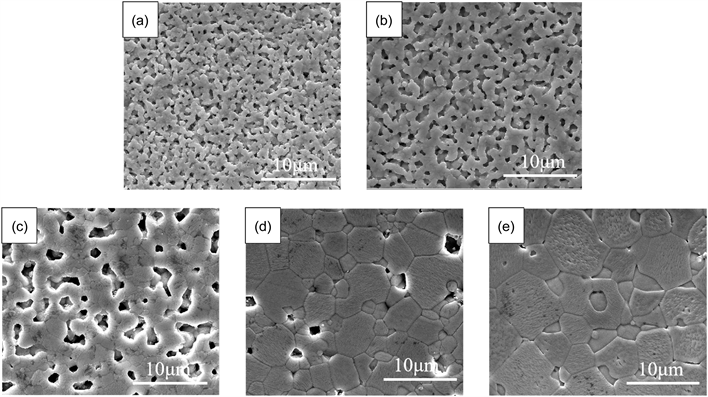
Figure 3. Surface topography of ITO target at different sintering temperatures (a) 1200℃; (b) 1300℃; (c) 1400℃; (d) 1500℃; (e) 1600℃
图3. 不同烧结温度下ITO靶材的表面微观形貌(a) 1200℃;(b) 1300℃;(c) 1400℃;(d) 1500℃;(e) 1600℃
图4是不同烧结温度下ITO靶材断口的微观形貌。从图4(a)、图4(b)可以明显看出当烧结温度较低时,ITO靶材内部存在大量连通和封闭的孔洞,当温度升高到1400℃时,孔洞的数量急剧减少。随着烧结温度进一步升高到1500℃时,开孔全部消失,只剩下少量的闭孔存在且孔径尺寸明显变小,说明提高烧结温度可以促进靶材孔洞收缩。当温度升高到1600℃时,在靶材断面基本看不到孔洞且发生明显的穿晶断裂。当烧结过程进入后期时,靶材中的连通孔隙逐渐形成独立的闭孔,孔洞收缩并通过体积或者晶界扩散的方式排出。根据粉末烧结理论 [10] 可知,在烧结后期,孔洞是否能够排出取决于和晶界之间的相对运动速度,当晶界运动速度较快时,会发生孔洞和晶界脱钩现象,此时,孔洞将会一直留在烧结体的内部无法排出,将对靶材的致密化产生较大的影响。
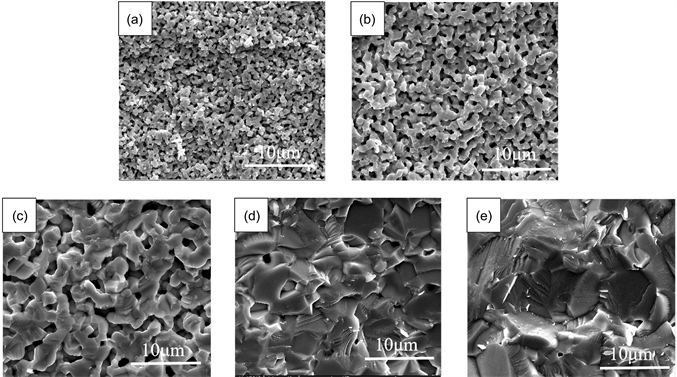
Figure 4. Fracture microscopic morphology of ITO target at different sintering temperatures (a) 1200℃; (b) 1300℃; (c) 1400℃; (d) 1500℃; (e) 1600℃
图4. 不同烧结温度下ITO靶材的断口微观形貌(a) 1200℃;(b) 1300℃;(c) 1400℃;(d) 1500℃;(e) 1600℃
3.2. ITO靶材相组成的研究
图5为不同烧结温度下ITO靶材的X射线衍射图。从图可以看出当烧结温度为1200℃和1300℃时,ITO靶材中还存在明显的SnO2衍射峰,说明此时SnO2还没有与In2O3发生固溶反应;当烧结温度达到1400℃后,ITO靶材中除了立方In2O3相,还发现了二次相的衍射峰。
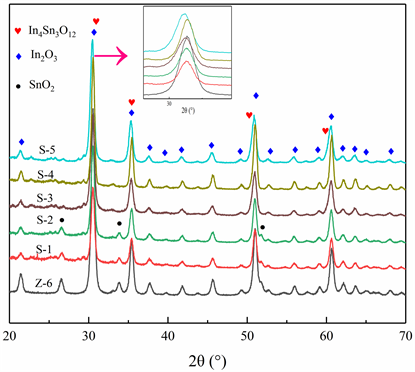
Figure 5. XRD patterns of ITO targets at different sintering temperatures Z-6: ITO Powder; S-1: 1200℃; S-2: 1300℃; S-3: 1400℃; S-4: 1500℃; S-5: 1600℃
图5. 不同烧结温度下ITO靶材的XRD图 Z-6:ITO粉末;S-1:1200℃;S-2:1300℃;S-3:1400℃;S-4:1500℃;S-5:1600℃
且所有温度下靶材的In2O3相的衍射峰相较于标准的In2O3衍射峰向小角度发生偏移现象,温度越高,向小角度方向的偏移越明显,发生该现象的原因是因为Sn4+以置换原子的方式进入In2O3的晶格形成In2O3-Sn固溶体,固溶体会导致ITO发生晶格畸变导致衍射峰相较于标准PDF卡片发生偏移,当烧结温度越高时,SnO2与In2O3的固溶程度越高,衍射峰向小角度的偏移量就会越大。此外,因为立方In2O3相的三强峰在向小角度偏移后与In4Sn3O12的三强峰角度极为接近,都是萤石衍生结构,所以In4Sn3O12相的特征衍射峰在图中无法与In2O3衍射峰进行明显区分。此外,从图可以看出烧结温度越高时ITO靶材的衍射峰变得更窄且尖锐,这表明温度越高时,ITO靶材的结晶性越好。
为进一步证实二次相的出现,如图6所示对1600℃下烧结的ITO靶材抛光后进行酸腐蚀出其晶粒,选择任意的粗晶粒和细晶粒进行线扫描。从图6中可以清楚看到在细晶粒区出现明显的In元素的降低和Sn元素的明显升高现象,这表明粗晶和细晶是两种不同的相。
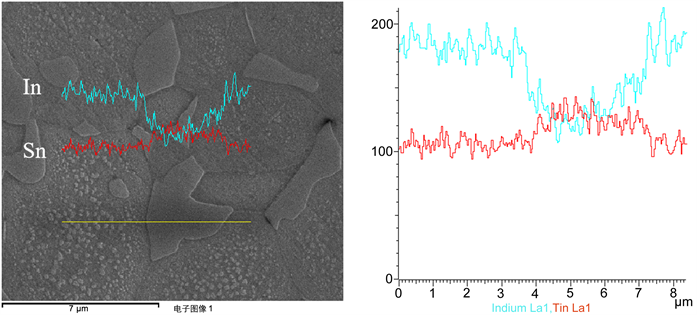
Figure 6. Line scan of ITO target at sintering temperature of 1600℃
图6. 烧结温度为1600℃时ITO靶材的线扫描图
如图7所示,对1600℃下烧结靶材的不同区域进行EDS分析得到靶材内部晶粒的元素含量。点1和点2的位置位于小晶粒的中心,点3的位置位于大晶粒的中心部分,从分析结果可以看到在点1和点2出的Sn元素含量远远高于点3,而In含量则恰恰相反。结合上述XRD、线扫描分析和EDS结果可以断定靶材中有二次相的存在,大晶粒为In2O3-Sn相,三个或多个大晶粒交界处的高Sn含量的小晶粒为In4Sn3O12相。
此外根据Heward W J [11] 等人的研究表明,通过In2O3-SnO2的伪二元相图可以看出,随着烧结温度的升高,SnO2的固溶度随之增加,在1600℃时达到12.2 mol%,换算成质量分数仅为7.01 wt%,远远小于在ITO粉末中的17mol%的固溶度,ITO靶材处在In2O3和In4Sn3O12的两相共存区,所以含10 wt% SnO2的ITO粉末在经高温烧结过后必定会存在一定量的In4Sn3O12相。通过计算可知In4Sn3O12相的理论密度为7.30 g/cm3大于ITO的理论密度7.155 g/cm3,所以,当靶材内In4Sn3O12相含量增加时,使得ITO靶材的致密度增加。
3.3. ITO靶材元素分布
为了进一步了解ITO靶材中各组成相的分布情况,对靶材研磨抛光后酸腐蚀后进行元素的Maping分析。图8和图9分别是1500℃和1600℃下通过EPMA测得In、Sn、O三种元素的分布。
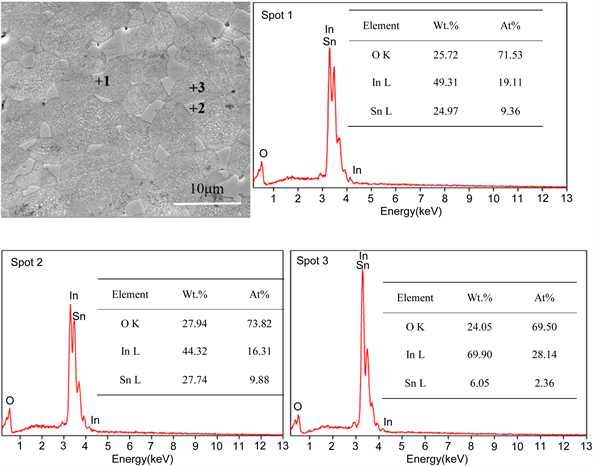
Figure 7. EDS analysis of ITO targets at sintering temperature of 1600℃
图7. 烧结温度为1600℃时ITO靶材的EDS分析
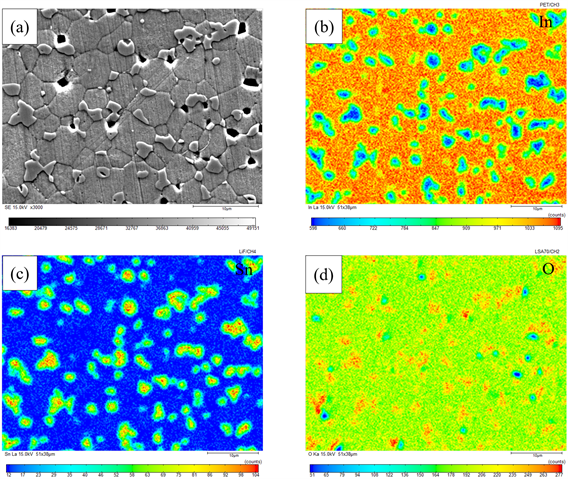
Figure 8. Electron probe analysis of target at sintering temperature of 1500℃
图8. 烧结温度1500℃时靶材的电子探针分析
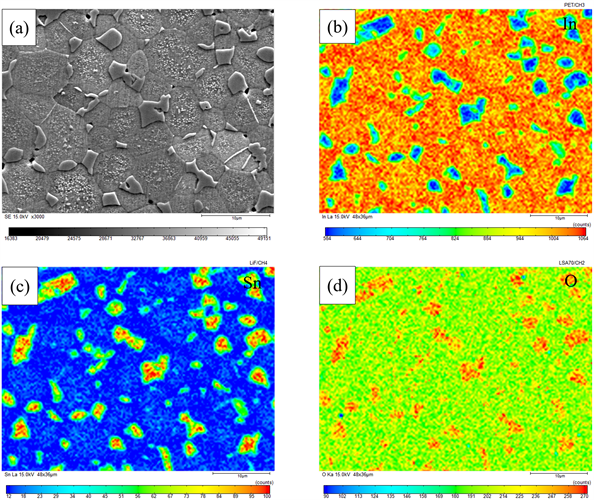
Figure 9. Electron probe analysis of target at sintering temperature of 1600℃
图9. 烧结温度1600℃时靶材的电子探针分析
从图8和图9可以明显看出两种不同烧结温度下靶材由两种尺寸差别较大的晶粒所组成,由上节分析可知大晶粒为主相In2O3-Sn相,小晶粒为In4Sn3O12相,经过计算可知当烧结温度为1500℃时,In4Sn3O12相的平均晶粒尺寸约1.3 μm,In2O3-Sn相的平均晶粒尺寸约4.4 μm,当烧结温度为1600℃时,In4Sn3O12相的平均晶粒尺寸约1.7 μm,In2O3-Sn相的平均晶粒尺寸约5.2 μm,并且大部分In4Sn3O12相的形貌从平直的三角形变为弯曲的多边形,说明烧结温度不仅影响晶粒尺寸,而且影响第二相粒子形貌,这与Mei Fangsheng [12] [13] 等人的研究结果基本一致。Maping扫描结果显示靶材内部元素分布并不均匀,主相中的In元素的含量比二次相中的要高,且主相与二次相的晶粒交界处存在In元素的过渡层。在主相晶粒内部的In元素分布不均匀,出现一部分低In含量的小区域,越靠近晶界In元素的含量越高,这些主相晶粒内部的低In区是由于主相的过饱和固溶体析出所产生的富Sn相,其次,随着烧结温度的增加,粗晶粒中的富Sn颗粒明显增加如图8(b)、图9(b)所示,这说明随着烧结温度的升高,SnO2在In2O3中的溶解度进一步增加,这与XRD衍射峰的结果相吻合。In2O3-Sn相晶粒出现明显的Sn元素富集现象,且沿主相晶粒边缘处出现Sn元素的沿晶界的带状降低区如图8(c)、图9(c)所示。
O元素在小晶粒处出现明显的富集现象,这是和In4Sn3O12相中O元素所占的比例比主相In2O3-Sn中高相吻合。这与侯俊峰 [14] 等人通过TEM微区分析的研究结果基本一致。
3.4. 富Sn析出相分布的规律及其形成机制
图10是不同烧结温度下In2O3-Sn晶粒中富Sn析出相粒子的扫描照片,从图中可以明显看出In2O3-Sn晶粒中间部分富Sn粒子尺寸较大且分布较为稀疏,离晶界距离越近时,富Sn粒子越密集且尺寸越小,在沿晶界处有明显的无析出带出现。随着烧结温度的升高,可以发现富Sn粒子的尺寸和相互之间的距离明显增大,沿晶界的无析出带宽度增加。和图8(b)、图9(b)结合可知,沿晶界处的In元素含量最高,正好对应该无析出带。导致该现象出现的原因是,晶界附近的扩散通道一般由晶格畸变和一些其它的缺陷提供,靠近晶界处的氧化锡会向晶界处移动并形成稳定的In4Sn3O12相,且因为较短的迁移距离使该范围内氧化锡含量快速降低,形成该无析出带。烧结温度越高,扩散进行的速度越快,无析出带宽度越宽越明显。
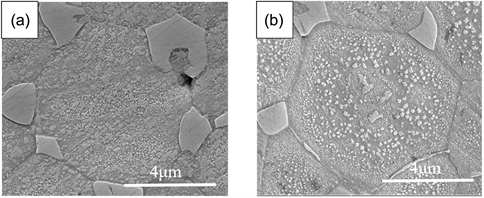
Figure 10. Sn-rich phase precipitated particles in In2O3-Sn grains at different sintering temperatures (a) 1500℃; (b) 1600℃
图10. 不同烧结温度下In2O3-Sn晶粒中富Sn相析出粒子(a) 1500℃;(b) 1600℃
富Sn析出相在In2O3-Sn晶粒中是以均匀形核的方式析出,和在晶界处形成的In4Sn3O12相晶体结构不相同,富Sn析出相的晶体结构是立方结构并且通过XRD并未检测到该相的出现,造成该现象的原因有两个:1) 富Sn析出相粒子的物相结构与ITO靶材的立方In2O3的结构极为接近;2) 该相含量极低通过XRD检测不出。从图10可以看出富Sn粒子在主相中是普遍存在且所占范围不少,这表明富Sn粒子是一种和ITO晶格结构相似度极高的一种析出相。当In2O3-Sn晶粒内的过饱和SnO2相开始析出时会和周边的In2O3-Sn形成新相,此相与多晶交界处的二次相In4Sn3O12相比稳定性不同的原因是In4Sn3O12相和主相一样都具有较高的界面能,相变的驱动力大于晶界处,所以新相是和主相In2O3-Sn具有相同的晶体结构和化学组份的中间相,该相的自由能高于二次相而小于主相是一种亚稳定相。富Sn析出粒子在主相中发生形核后的长大机制是Ostwald机制,其机理是由于毛细作用,小尺寸粒子周围的母相浓度会高于大尺寸粒子,两者间会产生一定的浓度梯度导致SnO2向低浓度区扩散,为大颗粒继续长大提供成分,小颗粒不断溶解并在大颗粒表面析出。因为SnO2过饱和浓度和其生长驱动力的不同,在主相晶粒中间位置析出的富Sn颗粒间距和尺寸较大,而近主相晶界处的析出颗粒间距和尺寸较小。该相的长大过程如图11所示。
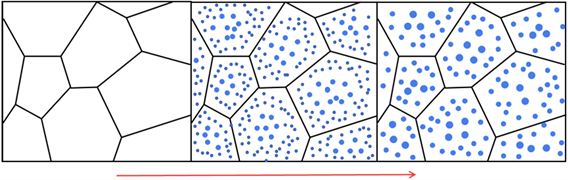
Figure 11. Formation and growth mechanism of Sn-rich particles in the main phase
图11. 主相中富Sn颗粒的形成及长大机制
3.5. ITO靶材烧结致密化机理
ITO属极难完全致密化材料,微小孔隙率会导致后续玻璃镀膜的“中毒”现象。研究证明:ITO靶材烧结遵循Coble固相烧结理论的三个阶段:即烧结初期、烧结中期和烧结后期。如果致密的坯体是由大量细分颗粒形态密堆积的形式存在,考虑到细分粉体本征地具有发达的颗粒表面,与同质量的未细分粉体密堆积系统相比前者具有过剩的表面能必然处于一个高能状态。固相烧结过程中系统过剩的表面能充当着本征热力学驱动力,在该力的作用下颗粒系统烧结成为一个致密的晶体向低能状态过渡。因此烧结的主要驱动力是体系的表面能(表面积)降低,与此同时系统界面能(界面积)的增加是烧结致密化的阻力,故总的致密化的推动力为 [12] :
(1)
这里,和是体系的总自由能、表面能和界面能的变化,γs和γi分别为表面张力和界面张力。As和Ai分别为比表面积和比界面积。对于上述模型,结合致密化其物质迁移的驱动力有两种:其一,颈部弯曲表面引起本征Laplace应力;其二,由于颈部和它连接的两个颗粒在化学组成上存在质的差异,在此基础上建立起化学位梯度。
在烧结初期假设坯体具有理想烧结的密堆积结构,伴随烧结的进行,温度的升高,在有In2O3SnO2直接接触共同参与烧结的区域首先形成了烧结颈。这是因为:ITO靶材烧结为固相烧结,其烧结过程中物质的传输机制以扩散为主。其瓶颈形成的推动力主要是两颗粒间瓶颈形成的化学势△μ [15] 。
随着烧结的进行,相邻的ITO颗粒间形成烧结颈。而此时,在单相颗粒接触区还没有形成烧结颈。温度继续升高,单相颗粒接触区的烧结颈开始形成生长。与In2O3SnO2直接接触的“复相区”不同的是:“单相区”瓶颈形成的推动力不再是两相熔点差异引起的化学势,而是颗粒粒径差异,即烧结颗粒颈部弯曲表面引起本征Laplace应力。同一颗粒内部和“单相区”不同颗粒间的物质传输关系可由下式表示:
(2)
进入烧结中期后,颗粒开始黏结、颈部扩大、晶界面广泛形成,但气孔由不规则形状逐渐变成由三个颗粒包围的圆柱形管道,气孔相互连通形成网络,而颗粒间的界面仍是相互孤立而不形成连续网络,晶粒正常生长。大部分的致密化过程和部分的显微结构发展产生于这一阶段。考虑到烧结中期气孔相互连通而晶界是相互孤立的,所以其物质传输机制不可能靠晶界扩散,而是表面扩散、体积扩散。而表面扩散往往是各种扩散方式中最易发生的,因此,烧结中期物质的传输扩散机制很可能仍以表面扩散为主,其有效扩散系数表示为:
(3)
在未进入烧结中期时,In2O3SnO2直接接触的复相区早已形成了正常的ITO晶粒,由于表面扩散作用使其更容易和周围的相对较小的颗粒形成烧结颈。因此,进入烧结中期后,当其它区域的颗粒完成气孔排除时,这两个区域的大晶粒则在大肆的“吞食”小颗粒。因为两者之间的粒径相差悬殊,即化学位梯度较大,故“吞食”速率较快,其间的气孔来不及排出而滞留在大晶粒内部,在烧结后气孔进一步圆化。
随着烧结过程中气孔变成孤立而界面开始形成连续网络,烧结进入第三阶段即烧结后期。在这一阶段孤立的气孔常位于两晶粒的界面,三晶粒间的界线或多晶粒的结合点处,也可能被包裹在晶粒中,烧结后期致密化速率明显减慢,晶粒生长较迅速。烧结后期气孔变成孤立而晶界相互连通形成网络,所以这时的气孔排除仅能通过晶界或体积扩散实现;晶粒则通过晶界移动生长。
在烧结后期,孔隙的消除与二次晶粒的长大均通过晶界扩散和体积扩散实现,因此致化速率降低。1600℃时In2O与SnO在氧气氛下的分压仅为1.5 Pa和74.6 Pa [16] ,所以蒸发与凝聚机制对烧结过程影响很小。此时晶界上原子排列疏松混乱,是气孔(空位源)通向烧结体外的主要扩散通道,同时也是溶质偏聚极易发生的区域。
这种分布情况下体系的吉布斯自由能为:
(4)
如果G < 0,体系中溶质原子混乱的分布于晶粒内,在过冷却或过饱和条件下,溶质原子充当着“晶核”系统便会出现析晶现象,系统通过形成新的界面使体系的自由能增加。
4. 结论
1) 靶材的致密化程度随着烧结温度的升高而不断提高,在1600℃时相对密度达到99.05%。晶粒尺寸随着温度的升高而变大,断口的孔洞随着温度的升高而减少。
2) XRD分析结果表明从1400℃开始靶材中的SnO2相消失,而二次相In4Sn3O12出现,通过线扫描及EPMA进一步证实靶材中确实存在二次相In4Sn3O12。大小晶粒中元素分布并不均匀,大晶粒内In元素浓度比小晶粒内的浓度高,且在与小晶粒交界处存在一定厚度的In元素浓度过渡层。
3) 本文对ITO靶材的烧结机理进行简要阐述,分析了靶材烧结过程三个阶段的扩散和传质等现象。
NOTES
*通讯作者。