1. 引言
现有研究表明,孔边多裂纹结构的强度与疲劳寿命要比含单一裂纹结构的强度与疲劳寿命小很多 [1] 。虽然孔边应力集中问题已经明确,但是在飞机结构大量存在的多孔结构会使裂纹的萌生以及扩展呈现出加快的现象,其中典型的有1988年由于孔边疲劳裂纹融合而引起的Aloha航空事故 [2] 。类似的事故不断发生促进了研究者们对于含多结构孔设计的研究 [3] ,虽然现已有大量关于多源疲劳损伤问题的研究模型,关于多孔结构的设计及相关疲劳寿命研究仍在进行 [4] ,明确设计方案并完善相应设计标准对保证飞机结构的使用安全、提高飞机相关结构设计水平具有重要意义与实用性。
因此,本文依据现有的飞机结构疲劳损伤相关理论分析方法进行数值模拟 [5] [6] ,从静强度以及疲劳损伤角度进行孔间距的优化设计,为结构设计人员提供相关参考。本文以损伤力学方法为理论基础分析多孔问题,将静力分析与孔边裂纹疲劳扩展分析相结合,对结构疲劳寿命进行评估,分别建立以结构静强度和疲劳寿命为判据的孔间距设计标准,该结论能够帮助设计人员针对不同的设计要求进行相应的结构优化设计,便于提高设计效率。
2. 计算模型
2.1. 双孔(多孔)分析模型
飞机壁板上含通孔的结构比较简单,考虑到应力集中效应,开口一般为圆形、椭圆形或者带圆角的矩形,通过应力分析不难发现圆形开口对结构强度削弱最小,且圆形开口工艺比较简单,所以通孔设计以圆形最为常见,本次研究也以圆形孔作为研究对象,其中包含的尺寸参数有孔直径d、壁板厚度H、壁板尺寸L,如图1所示。
对于实际结构,多孔问题与双孔问题在本质上是一致的,关键在于孔间区域的应力干涉造成的强度问题,而对其影响最大的在于相邻最近的孔,所以本文取双孔模型进行讨论,所得结果也适用于多孔结构。本文双孔模型如图2所示,孔径(d1, d2)和孔间距α(d1, d2)是影响该结构应力分布的重要参数,其中α为无量纲间距系数。
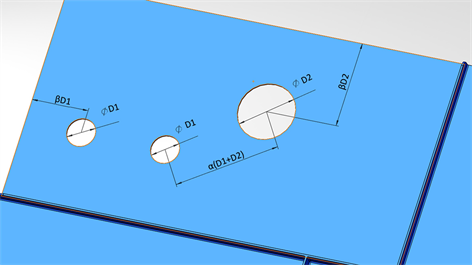
Figure 1. Model of porous wall structure
图1. 多孔壁板结构模型图
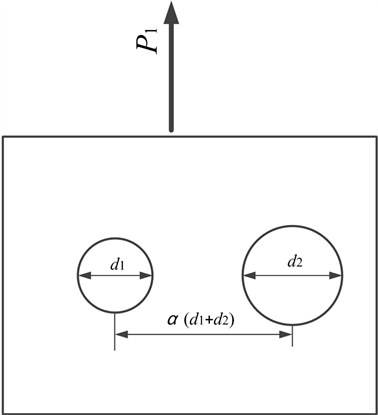
Figure 2. Diagram of the two-hole spacing parameter
图2. 双孔间距参数示意图
2.2. 有限元模型应力分布
本文应用ANSYS 18.0建立双孔的有限元模型,使用的材料参数按照2024铝合金进行选取 [7] ,考虑到该模型属于薄板,可以当作平面应力问题处理,所以单元类型选择SOLID183。为简化计算使用1/2模型并施加对称边界条件,两侧面施加对称边界条件,载荷为均布拉应力,应力分布如图3所示。
通过有限元计算发现,两孔间的区域应力水平较高,这是由于孔边应力集中所造成的应力场重叠,该部分是结构中最危险的区域,应对此处重点分析,裂纹也最容易在此部位萌生。
2.3. 损伤分析的有限元开发
基于损伤力学,在通用有限元软件运行环境中进行二次开发,将上述损伤演化方程及损伤累计
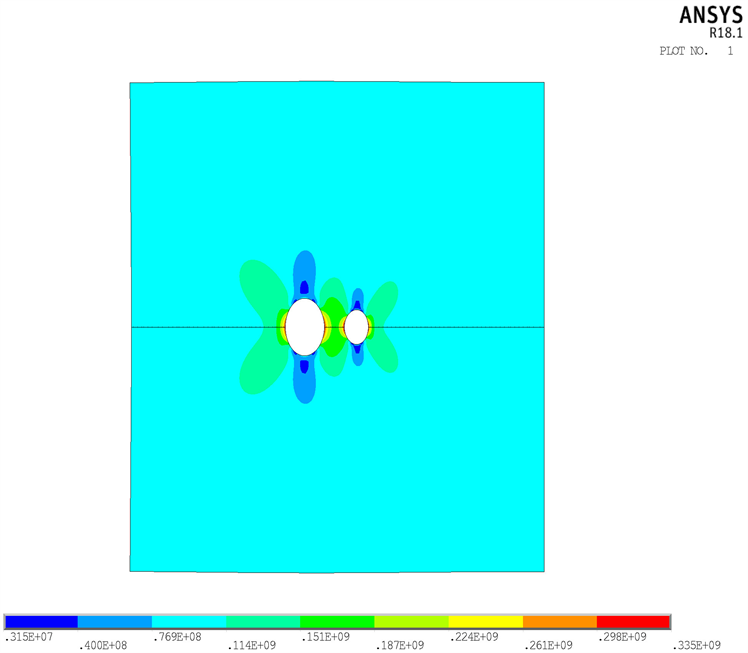
Figure 3. Stress cloud diagram under far field tensile stress
图3. 远场拉应力载荷下的应力分布云图
计算流程形成嵌入有限元计算,从而实现了有限元模型进行材料/结构损伤模拟分析。际结构,多孔问题与双孔问题在本质上是一致的,关键在于孔间区域的应力干涉造成的强度问题,而对其影响最大的在于相邻最近的孔,所以本文取双孔模型进行讨论,所得结果也适用于多孔结构。本文双孔模型如图2所示,孔径(d1, d2)和孔间距α(d1, d2)是影响该结构应力分布的重要参数,其中α为无量纲间距系数。
3. 基于静力分析的双孔间距设计
本节继续采用前文建立的模型,对不同的直径组合进行计算,取不超过单孔应力集中系数(理想状态为3) 10%的范围作为应力标准线,相应的间距系数如图4所示。
从图4中可以发现,间距增加显著降低最大应力水平,并且,对于尺寸相差较大的两减轻孔,间距系数α也需要较大。当D1 = D2时,α可取0.75,而当D2 = 4D1时,α则应取1。另一方面,考虑到间距系数可能会受到圆孔绝对尺寸的影响,接下来将圆孔直径作为自变量,固定间距系数而改变孔的实际尺寸(d1 = 5~10 mm, d2 = 2d1),相应的最大应力集中系数变化如图5所示。
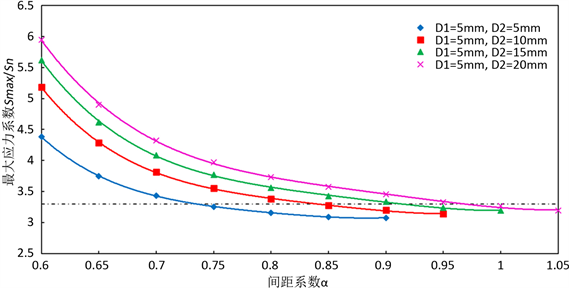
Figure 4. Curve of maximum stress at different apertures spacing
图4. 不同孔径下最大应力与间距曲线图
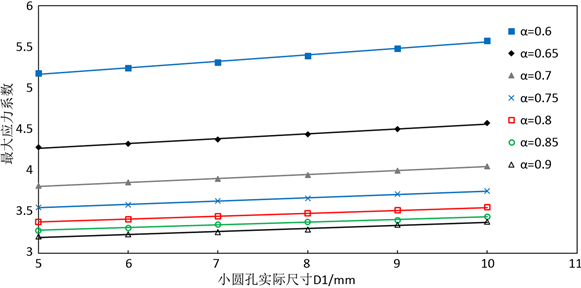
Figure 5. Graph of relationship between the maximum stress level and the actual size (fixed hole ratio)
图5. 最大应力水平与圆孔实际尺寸的关系图(固定双孔比例)
在上述条件下,即两孔尺寸之比为1:2,图5中的有限元结果表明,随着孔的尺寸增大,最大应力是不断变大的;当距离系数大于0.8时,最大应力变化相对较小,特别是在减轻孔间距较大的情况下,孔的绝对尺寸大小对最大应力的影响较小。
4. 结合疲劳寿命的双孔结构分析
结构的静强度分析是结构设计的基础,但结构疲劳设计往往不是静强度设计所能覆盖的,因此,疲劳设计是结构设计中更为重要问题。接下来本文将通过基于ANSYS二次开发的损伤模拟程序,对上述双孔模型进行结构的损伤分析和疲劳寿命预估。
针对双孔结构,经分析可以发现,即使孔间距离较近,但只要两孔的孔边应力集中效应没有互相产生影响,即最大应力水平保持不变,则裂纹萌生的疲劳寿命基本不变。但是,从疲劳裂纹后继扩展的角度分析,一旦出现孔间双裂纹,由于孔间距较小,孔边应力集中影响区域存在重叠,导致双裂纹更快地扩展和汇合,最终表现为结构过早失效破坏。
虽然从静力分析的角度,两孔间距系数α大于0.75即可以满足设计要求,但是从结构疲劳寿命评估上看,尤其是从裂纹后继扩展的角度分析,该间距显然不充分安全。两孔的间距应该保证其各自的应力集中影响区接近完全分离的状态,这样才能避免疲劳裂纹加速扩展导致的结构疲劳寿命过分降低。因此,本节依据裂纹萌生寿命以及裂纹扩展进行双孔间距设计分析。
4.1. 双孔间距对裂纹萌生寿命的影响
对于工程应用而言,肉眼可见裂纹是检测界定结构疲劳失效的常用标准。因此,本节在模型模拟损伤时,取孔边出现长度大于3 mm的裂纹作为判断标准,对应的疲劳寿命为疲劳裂纹萌生寿命。进一步取不同的减轻孔尺寸计算其疲劳寿命,可得到两减轻孔在不同间距系数α下的结构疲劳寿命曲线如图6所示。
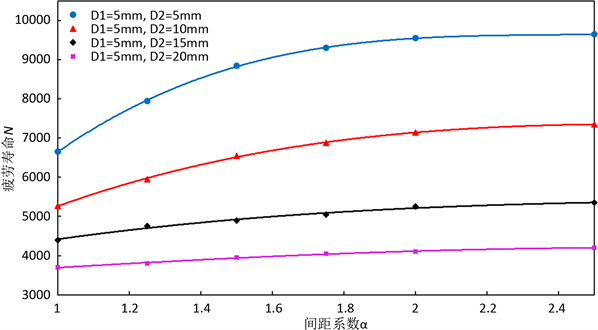
Figure 6. Structural fatigue life affected by the spacing factor
图6. 结构疲劳寿命受间距系数影响
根据图6可知,间距系数α达到2后结构疲劳寿命增长趋缓;且与静力结果类似,两减轻孔尺寸相差越大,为降低应力水平,防止孔边应力集中区域过快趋近,应选取较大的间距系数。同时,应避免减轻孔尺寸过大。当然,鉴于萌生阶段裂纹扩展对孔间距不敏感,故可针对实际设计要求和工程应用的现实,适当减小孔间距。
4.2. 双孔间距对裂纹后继扩展寿命的影响
如前文所述,如果结构设计中的孔间距过小,孔边裂纹萌生后的后继扩展会加速,造成结构快速破坏。在裂纹的后继扩展中,除了有疲劳损伤的原因外,裂纹尖端场应力强度因子K达到临界值,也是结构破坏/加速破坏的重要原因,需要在疲劳分析的同时,结合静强度分析进行结构破坏分析。
本节以模型中所使用的峰值100 MPa的脉动载荷为例,由于该载荷峰值相对较小,双孔中间的裂纹可以持续扩展并始终保持在临界的应力强度因子以下,但当两裂纹扩展至接近贯通时,由于应力水平较高,裂纹会产生快速的扩展并导致双裂纹汇集(多孔情况下与其类似,对应为多裂纹汇集),原先较低的应力强度因子直接大幅度提高并致使结构失效。这种情况相对于单裂纹模型更加危险,结构的寿命也会显著下降。有鉴于此,取不同的间距系数α进行上述分析,得到后继裂纹扩展寿命曲线如图7所示。
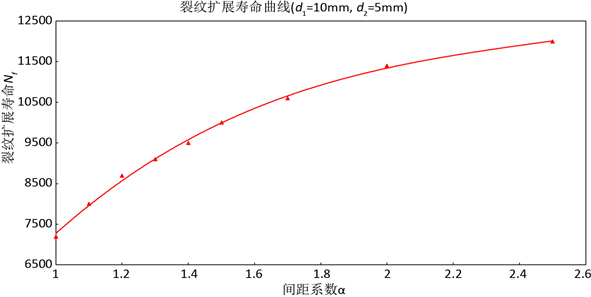
Figure 7. Curve of crack propagation life with spacing
图7. 间距系数对裂纹扩展寿命的影响曲线
由图7可知,裂纹扩展寿命对孔间距要求比较苛刻,孔间距对裂纹扩展寿命的影响比较大。而当间距缩短时,裂纹扩展寿命呈加速下降的趋势,这也说明孔间裂纹的危险性,相比于裂纹萌生寿命的间距系数标准(α > 0.75),如果要考虑裂纹扩展寿命的影响,则显然应取更大的α值。
另外,值得注意的是该结论适合于中低载荷情况下的孔间距设计,当外载荷很高时,裂纹扩展很短的长度就会达到临界应力强度因子,高载荷情况下裂纹扩展寿命受多孔裂纹相互影响的效果则可以忽略,该问题可直接按照单孔分析。因此在高载荷情况下,多孔间距设计也不需要考虑多裂纹汇集加速结构破坏的问题,间距仍可按照α > 2的准则设计即可。
5. 结论
本文取双孔模型作为研究对象,对飞机壁板等结构件中常见的孔结构要素进行设计研究,并结合有限元方法对双孔的孔间应力水平以及孔间裂纹扩展寿命进行模拟计算,经过分析后得到在避免显著提高应力集中效应或降低疲劳寿命的情况下,双孔模型的间距设计要求。需要说明的是,上述分析结果和得到的结论也适合多孔情况。
另外,在不同的工况以及载荷水平下,孔间距的设计要求有所区别,高应力情况下多孔干涉问题的影响更小,设计准则更为划一,即可依据最大应力水平这一准则进行分析,一般情况下取间距系数α为0.75;而中低应力水平下的结构则会存在明显的多孔干涉问题,使得原先足够长的设计寿命大幅度缩短,此时对应的间距最好依据裂纹后继扩展寿命准则进行分析,增大孔间距以避免出现多裂纹过早汇合导致结构失效的现象,结构设计允许的情况下应将间距系数α设计在2以上。
总而言之,本文中的结论为结构中孔间距的设计分别从静强度和疲劳寿命两个角度提供了参考,实际应用起来方便有效,具有良好的工程应用价值。